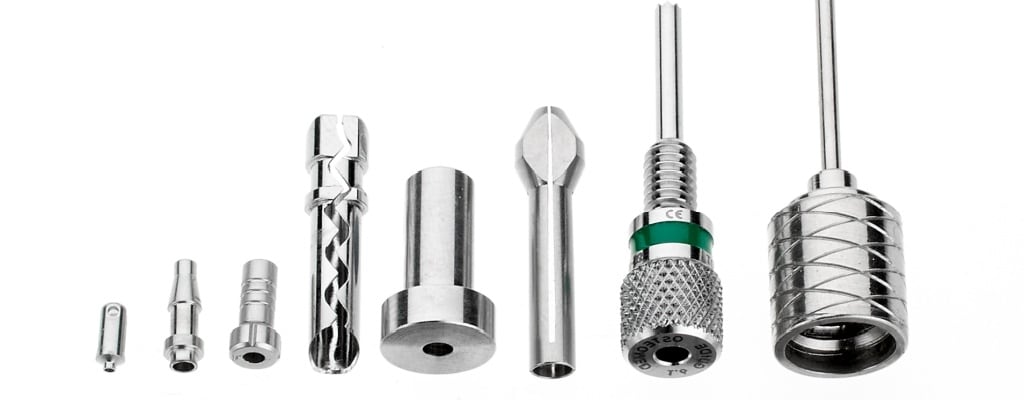
Medical Machining
Components in today’s medical devices must be manufactured within rigorous specs and cost parameters. The machining process requires deep technical expertise to successfully design, produce, and manage production runs on highly specialized equipment. TE has a broad range of machining capabilities engineered for production control and efficiency.
Advancements in machining technologies make highly precise, micro-scale component production possible. TE features in-house machining processes that cover a comprehensive array of customer manufacturing needs:
CNC Swiss-type machines
Complex parts with additional features, such as cross holes or milled flats, require rotating tools for single-machine production. TE uses slow-feed Swiss-type lathes with rotating tooling to create these small, short parts. Although some conventional CNC lathes can produce rotating tool operations, the unique design of TE’s Swiss lathes produce this work with greater accuracy.
Our Swiss lathes are able to support bushings incredibly close to the cutting tool, which maximizes rigidity and minimizes deflection. If further support is necessary, a second sub spindle can be deployed for additional rigidity and stability to the section during machining.
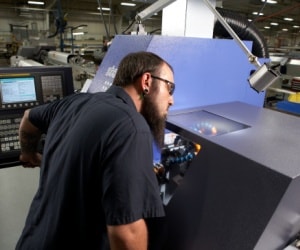
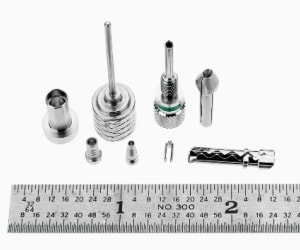
CNC Electrical Discharge Machining (EDM)
Thin-walled, delicate parts with tight tolerances are very difficult to produce using traditional machining methods. TE uses EDM to perform delicate, burr-free cuts on any electrically conductive material, including alloys or hard materials, eliminating the need to soften or heat-treat. Our advanced contactless process helps eliminate damage risks on intricate contours, cavities, and complex feature geometries. Parts produced with repeatable accuracy on our CNC EDM machines achieve extra-fine surface finishes and near perfect perpendicularity. Materials suitable for EDM include stainless steel, Nitinol, titanium, Hastelloy®, Inconel®, and Kovar®.
TE leverages proprietary fixtures in our production process to make cuts of extremely small diameters (down to Ø0.001″ [0.0254 mm]) and to very short lengths (<0.005″ [0.127 mm]). Precision can be held to ±0.001″ (0.0254 mm) for most Wire EDM and Sinker EDM applications. Tolerances of ±0.002″ (0.0508 mm) are achievable for Sinker EDM applications with more complex geometries.
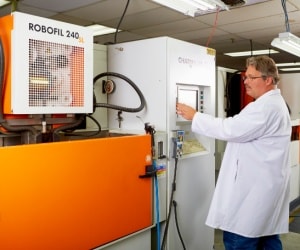
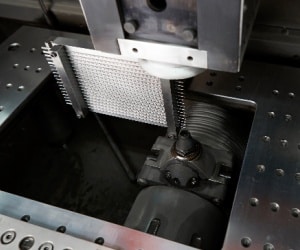
Multi-axis milling
Transforming solid stock material into complex small parts requires machining from many angles to accommodate corners, radii, holes, grooves, contours, and profiles. The multi-axis milling process at TE creates intricate parts in a single operation for improved efficiency and reduced risk of variation between features. Parts produced through multi-axis milling have tight feature tolerances, both individually and in relationship to each other. TE offers both horizontal and vertical milling solutions, with 3-, 4-, and 5-axis capability. Vertical multi-axis milling allows machining from any angle within the part and can generate complex contours into the part surface. Horizontal multi-axis milling is well-suited to high-volume production runs as multiple parts can be run concurrently.
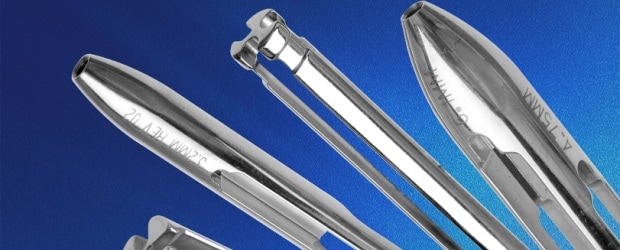