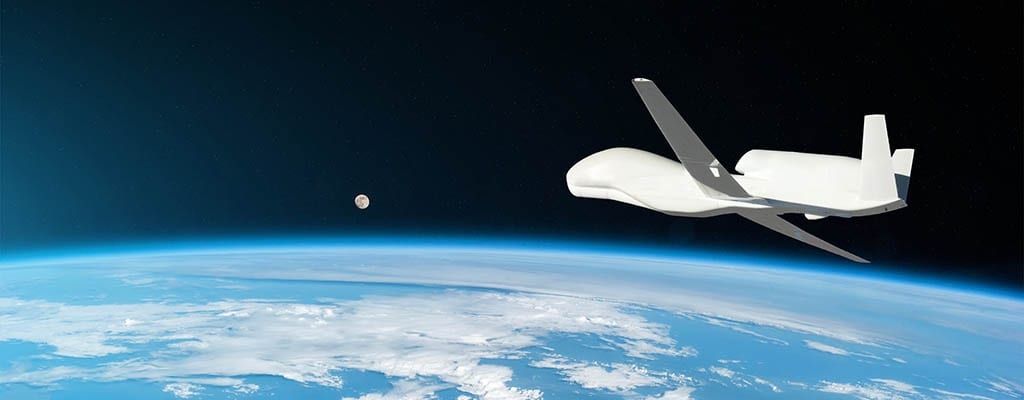
Trend Insight
Connector Technology for Unmanned Aerial Vehicles
Unmanned aerial vehicles play an important role in modern battle spaces. Learn how connector technology is integral to supporting a successful UAV mission.
Unmanned aerial vehicles (UAV) play an increasingly common and integral role in modern battle spaces. With their increased use, however, comes a need for specialized connector technology that can address their specific performance and mission requirements, often while withstanding harsh environments.
How Does UAV Communication Work?
UAVs, such as drone technology and other remotely piloted aircrafts, are linked to their controllers through radio waves or satellite communication. This lets pilots control the movement of their UAVs via remote control, while allowing unmanned aerial vehicle systems to collect and transmit visuals and other data back to their controllers. For these surveillance and reconnaissance missions to be successful, unmanned aerial vehicles must be able to always maintain connection with their controllers, no matter the distance.
What Are Connectors Used for in Drones?
The role of connectors in drones and other unmanned aircrafts is to help ensure that data, power, and signal are all reliably transmitted, even in extreme conditions. This makes connectors critical to the successful communication between UAVs and their pilots.
Connector Solutions for Unmanned Aerial Vehicle Technology
Connector technology for unmanned aerial vehicles must meet certain requirements to operate at the level of performance necessary for a successful mission. This means considering size, weight, and power consumption, using high performance materials, testing for shock and vibration, and ensuring all connectors are fluid resistant.
Size, Weight, and Power Consumption (SWaP):
Each new generation of unmanned aerial vehicle technology is required to perform with less size, weight, and power consumption. Reducing SWaP is vital to longer mission deployments, greater fuel efficiency, and the ability to add additional surveillance and combat capabilities. As components get smaller and lighter, more bandwidth is required to ensure these systems can handle complex high-speed communication requirements, as well as the need for greater functionality.
Materials:
Connector materials must be able to perform in extreme conditions, while being light enough to meet SWaP requirements.
- High strength aluminum alloy helps reduce weight in shelling and coupling rings.
- Conductive black zinc nickel finishes make connectors suitable for most unmanned aerial vehicles.
- Thermoplastic insulators also help contribute to a lighter finished product.
- High-performance gold-plated crimp contacts are less susceptible to corrosion and can withstand harsh environments.
- Fluorinated silicone holds up well in extreme environmental conditions and is resistant to substances like fuel, oil, and solvents, making it ideal for interfaces and wire seals.
All connector materials must also be Restriction of Hazardous Substances (RoHS) and Registration, Evaluation, Authorization and Restriction of Chemicals (REACH) compliant.
Shock and Vibration:
- Connectors aimed at autonomous solutions require rigorous testing for shock and vibration. Because the vibrations encountered in battle tend to be unpredictable, it’s important that connectors undergo random vibration testing to ensure they’re prepared to meet any challenge they may encounter.
- These tests simulate vibrations using a shaker, which shows under what conditions a connector may begin to fail. Sinusoidal vibration testing (finding frequencies at which a device resonates) and random-on-random testing (a complex random test that uses both random broadband and narrow-band signals) are also useful tests to get a better idea of the durability and performance of a connector.
Fluid Resistance:
All connectors aimed at autonomous solutions must show no damage from repeated exposure to fuels, oils, and cleaning fluids.
TE Connectivity DEUTSCH Connectors
TE Connectivity (TE) and its DEUTSCH connectors have pushed the boundaries of technology and innovation for more than 40 years. Today, that means consistently driving the market forward with new products that match the ever-increasing demands of lower weight, smaller size, and better performance in unmanned aerial vehicles. All DEUTSCH connectors are thermal cycle tested and environmentally sealed to IP67 when mated.
All DEUTSCH connectors also offer:
- Compact design/minimum space envelope
- Interfacial and wire sealing
- Boot termination feature
- Printed circuit board PCB) option
- Universal option available (not UAV composite)
- Standard crimp tooling
- Suitable for blind mating
- Visual indication of keyway orientation of connector
- Scoop-proof interface
- Shell-to-shell grounding (not UAV composite)
- Positive locking coupling mechanism
- No need for backshells or boot termination
- In-line and two-hole mounting styles (not UAV composite)
- Surface finishing options
- Keyway options
Key Takeaways
- Connectors are crucial for supporting communication between unmanned aerial vehicle systems and their pilots.
- For connectors to perform at the level needed for a successful mission, they must be built with considerations for SWaP, shock and vibration, environmental durability, and fluid resistance.
- TE’s DEUTSCH connectors are built with these considerations in mind and designed for applications within the aerospace, defense, and transportation markets.
Your Unmanned Aerial Vehicles Challenges, Solved