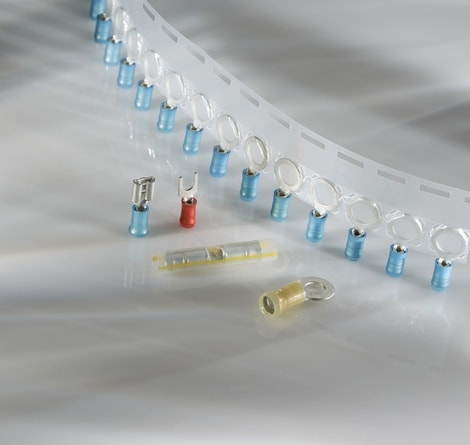
PIDG Terminals and Splices: Durable, Vibration-Resistant, and Field-Proven Reliability
PIDG terminals are engineered for consistent reliability, even in the most demanding circuit environments where high vibration and wire movement are concerns. They feature a nylon or PVC-insulated body along with a metal sleeve that crimps onto the wire insulation for enhanced support. Designed for vibration resistance, the wire barrel allows flexibility in any direction without compromising the wire insulation or conductor. Millions of PIDG terminals and splices remain in use years after installation, demonstrating the rigorous testing and research behind their design and manufacturing. Many PIDG terminals also meet or exceed the requirements of SAE AS7928, Type II, Class 1.
Product Features
PIDG Terminals & Splices
Insulation | Nylon, PVC, PVF2 (Radiation resistant) | Approvals | UL/CSA, Mil Spec |
Features | Highest vibration resistance - wire can bend in any direction without fail |
Crimp Design | "C" Crimp or TetraCrimp |
Wire Size | 0.12 – 6.64 mm2 (26 to 10 AWG) | Voltage Rating | Terminals 300V Splices 600V & (1000V signs) |
Plating | Tin | Temperature Rating | Nylon & PVC: 105°C, PVF2: 150°C |
Materials | Copper alloy | Terminations | All tongue types; Butt splices |
Benefits
- Many PIDG terminals and splices are Military Approved: ASM7928
- Vibration resistant; wire can bend any direction without damage
- Insulation repels hydrocarbons (greases, oils, etc.) and has high dielectric strength.
- Serrations in wire barrel give maximum electrical contact and tensile strength with the conductor
- Funneled wire entry prevents turned back wire strands and permits rapid wire insertion during high speed production
- Insulation sleeves and corresponding tooling are color-coded by wire size for easier identification
The guide is focused on solderless closed barrel termination. It gives practical guidelines through simple and clear illustrations that help the user in achieving a properly crimped terminal or splice every time. The guide illustrates the dos and don’ts of crimping and highlight the advantages of using matched cable, terminal and tooling from the extensive TE Connectivity product range.
Reliable Crimping
The design of the crimping dies and construction of the terminal allow for uniform insulation thickness under crimping pressure, transmitting the pressure evenly to the center of the crimp area. This produces a crimp and terminal that are alike in appearance and performance. PIDG products are available as rings, spades, flanged spaded, slotted rings, splices in several other varieties and sizes.
In electrical assembly, few tasks seem as simple as crimping wires to terminals. A crimping tool compresses the wire barrel securely around the stripped wire strands, creating a strong, uniform connection. This simplicity has made solderless terminals one of the most widely used connectors for over seventy years. Download this white paper to learn more.
Tooling Options
Frequently Asked Questions Tooling
PIDG Terminals & Splices
Q.1 - Can wires be combined in PIDG terminals & splices?
Ans: Yes, they can as long total CMA (Circular Mil Area) and insulation diameter fall within specifi cation.
Q.2 - Are PIDG terminals MIL specified?
Ans: Yes, most of them meet or exceed MIL-T-7928, Type II, class 1 .
Q.3 - Why can PIDG terminals just handle 300V and PLASTI-GRIP terminals 600 V?
Ans: Because the additional copper sleeve is close to the end of the sleeve.
Q.4 - What is the advantage of this copper sleeve?
Ans: It provides circumferential insulation support to the wire and allows the wire to bend in any direction, without fraying the wire’s insulation or breaking the conductor.
Q.5 - Why is there no crimp height given for PIDG terminals?
Ans: It is the geometry of the TE crimping tools which ensures the perfect crimp on PIDG terminals.