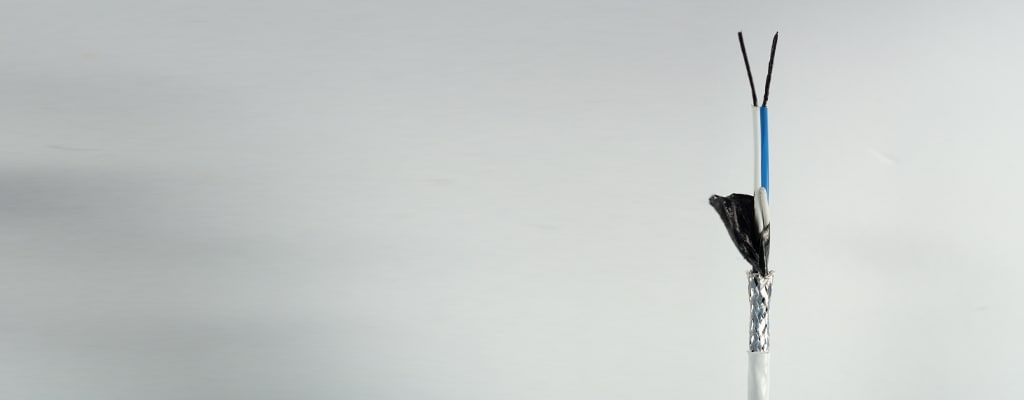
White Paper
Carbon Nanotube Technology may lead to Revolution in Cabling
Handling of CNTs in the form of yarns and tapes means that manufacturing processes for building cables need refinement to optimize throughput and improve yields.
Revolution in Cabling
While carbon nanotube technology (CNT) has generated widespread interest for medical applications, one area that is a focus of research at TE Connectivity (TE) is high-performance electrical cables. TE has been actively developing CNT for wire and cable, including cooperative efforts with universities and industry leaders, and has prototype samples for evaluation. While there is still much progress to be made before CNT cables become main stream, we believe the technology is sufficiently advanced to meet specific niche applications such as satellites.
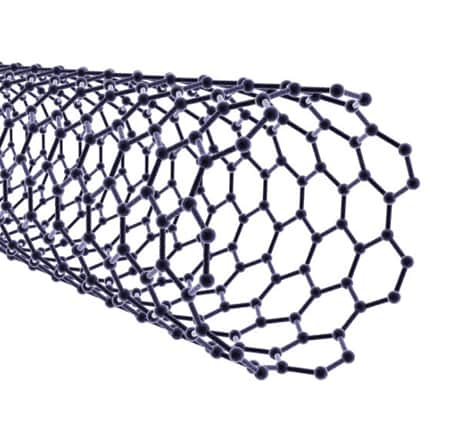
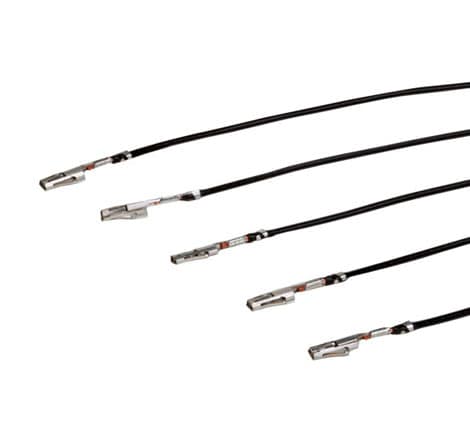
Cables using CNT components have the potential to become a disruptive technology, primarily due to weight savings compared to existing materials. In practical terms, these savings mean weight reductions of tens to thousands of pounds in platforms ranging from satellites to UAVs to manned military aircraft. For example:
- Satellites: Launch costs to put a satellite in orbit can range from $5,000 to $50,000 per pound of payload. Any reduction in weight can significantly influence costs or allow extra weight for additional scientific and engineering equipment or more maneuvering fuel to extend the life of the mission.
- UAVs: Lower weight means longer times aloft. Consider that the large UAV contains about 850 pounds of cable. Using a CNT shield in place of a metallic one could save 300 pounds. An all-CNT cable might save an additional 100 pounds, cutting the overall weight from 850 to 450 pounds.
- Manned aircraft: Weight savings translate into greater fuel efficiency or higher payloads or longer range.
The benefits of CNT cable goes beyond aerospace applications. Weight savings can also be important to ground vehicles and even soldier-worn equipment.
The long aspect ratio of a single carbon nanotube, only a few nanometers in diameter but several millimeters in length, gives it remarkable properties in the nanoscale: tensile strength greater than steel’s, conductivity greater than copper’s, thermal dissipation greater than diamond’s, and resistance to corrosion and fatigue. Table below gives typical properties of a single carbon nanotube.
Mechanical Strength | CNT | Steel | Aluminum |
---|---|---|---|
Young's Modulus (TPa) | 0.8 to 1.4 | 0.3 | 0.7 |
Tensile Strength (GPa) | 63 | 2 | 0.3 |
Density (g/cm3) | 1.4 | 8 | 2.7 |
CNT Shields
CNTs are grown by thermal processing and arranged into yarns for conductors and into tapes, sheets, and yarns for shields.
Bundling CNT strands into yarns or sheets to achieve practical sizes alters the properties of the material. A single carbon Nanotube has a conductivity thirty percent higher than copper but a yarn composed of a network of CNTs is orders of magnitude less coductive than copper. Figure below shows recent efforts in CNT yarn connductivity improvement since 2007.
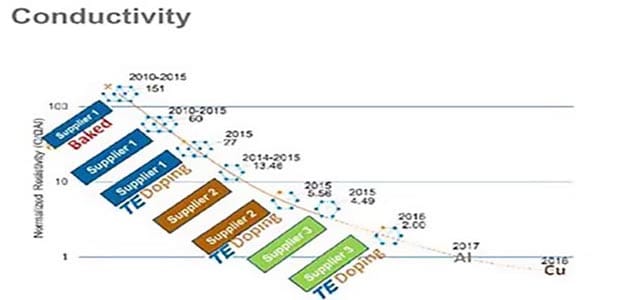
CNT cables are now being actively developed for MIL-STD-1553B and IEEE 1394 applications for aerospace and satellite applications—with a transition from prototypes to production happening in the next few years. Initial IEEE 1394 cables will use CNT shielding, while MIL -STD-1553B cables will likely be the first all-CNT construction.
CNT-based shields combine high shielding effectiveness with significant weight savings. A two-layer CNT tape offers roughly the same shielding as a copper braid at high frequencies—roughly 50 dB at 4 GHz—but weighs less than 2 percent of the braid it replaces.
The high resistivity of CNT shields, however, means poor shielding performance below 100 MHz and an inability to provide protection against lightning strikes. For the double-braided cables common in aerospace applications, replacing one of the braids with CNT allows the remaining braid to handle low-frequency noise and lightning, while the CNT shield handles the higher frequencies. Weight savings are 25 to 30 percent for hybrid shield constructions.
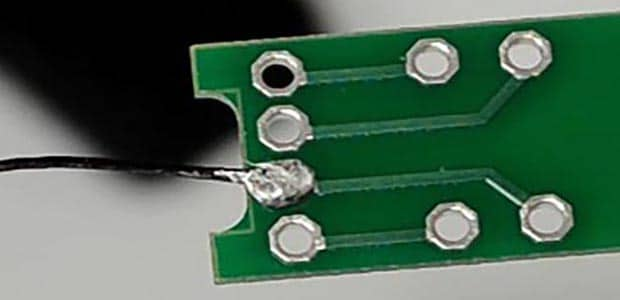
Ready for Prime Time?
As progress is made toward enabling the use of CNT materials in cables, two other issues deserve mention. The first is how to terminate CNT cables. CNT conductors are compatible with existing contacts and can be terminated with standard crimping techniques, albeit with modified crimp tool settings and dies. Testing of the mechanical strength of the crimps suggests that the CNT yarns fail before the crimp fails. Shields can be terminated to backshells with steel bands and other compression techniques. Tapes and yarns are also compatible with soldering,through the use of special alloys.
The second issue is moving from prototypes to production. CNT yarns, sheets, and tapes are available in commercial quantities, but challenges remain in volume production of long parts needed for cable. The production capabilities of CNT suppliers are rapidly increasing but the supply chain today typically has long lead times. Many applications today— such as composite enclosures—use CNTs measured in microns or millimeters. Cables represent a completely different scale from those applications, requiring tens of meters.
As TE works with commercial and university partners to improve the conductivity of macroscopic CNT arrangements, we have also manufactured miles of CNT, wire and cable for testing and evaluation.
TE has built a CNT pilot plant capabale of producting hundreds of miles of wires and cable per year. Handling of CNTs in the form of yarns and tapes means that manufacturing processes for building cables need refinement to optimize throughput and improve yields. TE has devloped the refinements and can supply many different wires and cables in long lengths.
Need help with your Aerospace project?
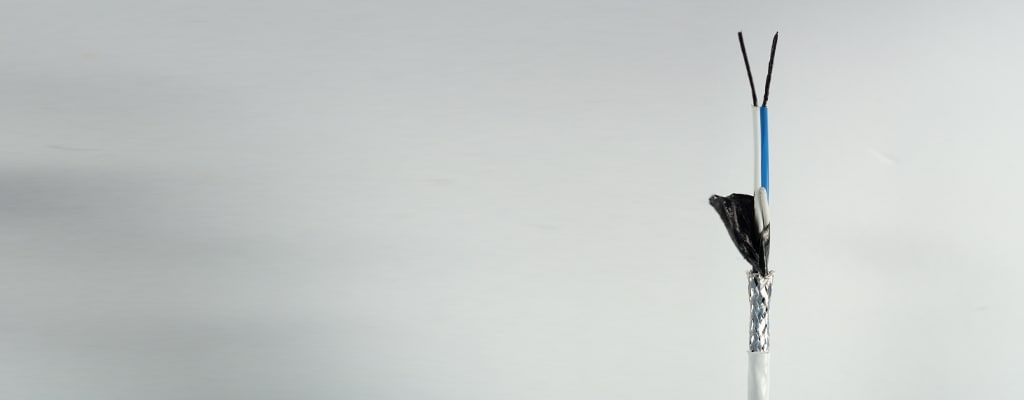
White Paper
Carbon Nanotube Technology may lead to Revolution in Cabling
Handling of CNTs in the form of yarns and tapes means that manufacturing processes for building cables need refinement to optimize throughput and improve yields.
Revolution in Cabling
While carbon nanotube technology (CNT) has generated widespread interest for medical applications, one area that is a focus of research at TE Connectivity (TE) is high-performance electrical cables. TE has been actively developing CNT for wire and cable, including cooperative efforts with universities and industry leaders, and has prototype samples for evaluation. While there is still much progress to be made before CNT cables become main stream, we believe the technology is sufficiently advanced to meet specific niche applications such as satellites.
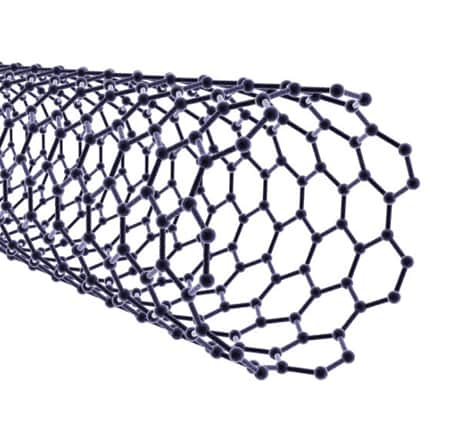
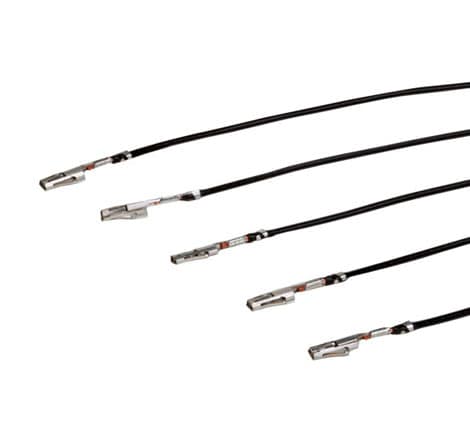
Cables using CNT components have the potential to become a disruptive technology, primarily due to weight savings compared to existing materials. In practical terms, these savings mean weight reductions of tens to thousands of pounds in platforms ranging from satellites to UAVs to manned military aircraft. For example:
- Satellites: Launch costs to put a satellite in orbit can range from $5,000 to $50,000 per pound of payload. Any reduction in weight can significantly influence costs or allow extra weight for additional scientific and engineering equipment or more maneuvering fuel to extend the life of the mission.
- UAVs: Lower weight means longer times aloft. Consider that the large UAV contains about 850 pounds of cable. Using a CNT shield in place of a metallic one could save 300 pounds. An all-CNT cable might save an additional 100 pounds, cutting the overall weight from 850 to 450 pounds.
- Manned aircraft: Weight savings translate into greater fuel efficiency or higher payloads or longer range.
The benefits of CNT cable goes beyond aerospace applications. Weight savings can also be important to ground vehicles and even soldier-worn equipment.
The long aspect ratio of a single carbon nanotube, only a few nanometers in diameter but several millimeters in length, gives it remarkable properties in the nanoscale: tensile strength greater than steel’s, conductivity greater than copper’s, thermal dissipation greater than diamond’s, and resistance to corrosion and fatigue. Table below gives typical properties of a single carbon nanotube.
Mechanical Strength | CNT | Steel | Aluminum |
---|---|---|---|
Young's Modulus (TPa) | 0.8 to 1.4 | 0.3 | 0.7 |
Tensile Strength (GPa) | 63 | 2 | 0.3 |
Density (g/cm3) | 1.4 | 8 | 2.7 |
CNT Shields
CNTs are grown by thermal processing and arranged into yarns for conductors and into tapes, sheets, and yarns for shields.
Bundling CNT strands into yarns or sheets to achieve practical sizes alters the properties of the material. A single carbon Nanotube has a conductivity thirty percent higher than copper but a yarn composed of a network of CNTs is orders of magnitude less coductive than copper. Figure below shows recent efforts in CNT yarn connductivity improvement since 2007.
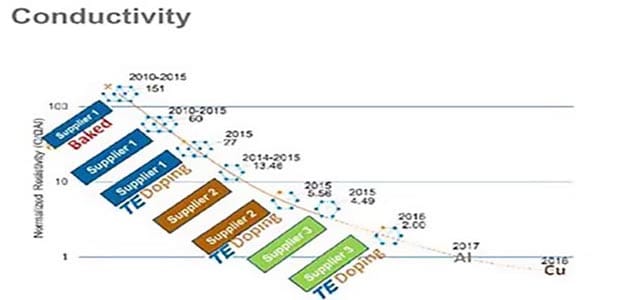
CNT cables are now being actively developed for MIL-STD-1553B and IEEE 1394 applications for aerospace and satellite applications—with a transition from prototypes to production happening in the next few years. Initial IEEE 1394 cables will use CNT shielding, while MIL -STD-1553B cables will likely be the first all-CNT construction.
CNT-based shields combine high shielding effectiveness with significant weight savings. A two-layer CNT tape offers roughly the same shielding as a copper braid at high frequencies—roughly 50 dB at 4 GHz—but weighs less than 2 percent of the braid it replaces.
The high resistivity of CNT shields, however, means poor shielding performance below 100 MHz and an inability to provide protection against lightning strikes. For the double-braided cables common in aerospace applications, replacing one of the braids with CNT allows the remaining braid to handle low-frequency noise and lightning, while the CNT shield handles the higher frequencies. Weight savings are 25 to 30 percent for hybrid shield constructions.
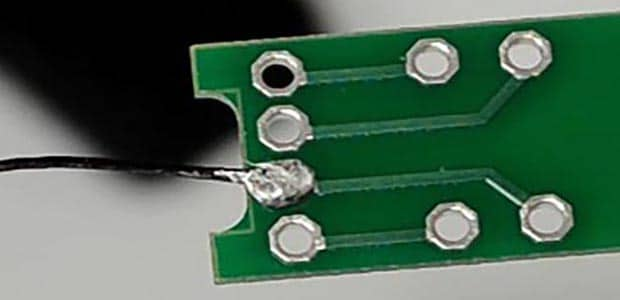
Ready for Prime Time?
As progress is made toward enabling the use of CNT materials in cables, two other issues deserve mention. The first is how to terminate CNT cables. CNT conductors are compatible with existing contacts and can be terminated with standard crimping techniques, albeit with modified crimp tool settings and dies. Testing of the mechanical strength of the crimps suggests that the CNT yarns fail before the crimp fails. Shields can be terminated to backshells with steel bands and other compression techniques. Tapes and yarns are also compatible with soldering,through the use of special alloys.
The second issue is moving from prototypes to production. CNT yarns, sheets, and tapes are available in commercial quantities, but challenges remain in volume production of long parts needed for cable. The production capabilities of CNT suppliers are rapidly increasing but the supply chain today typically has long lead times. Many applications today— such as composite enclosures—use CNTs measured in microns or millimeters. Cables represent a completely different scale from those applications, requiring tens of meters.
As TE works with commercial and university partners to improve the conductivity of macroscopic CNT arrangements, we have also manufactured miles of CNT, wire and cable for testing and evaluation.
TE has built a CNT pilot plant capabale of producting hundreds of miles of wires and cable per year. Handling of CNTs in the form of yarns and tapes means that manufacturing processes for building cables need refinement to optimize throughput and improve yields. TE has devloped the refinements and can supply many different wires and cables in long lengths.