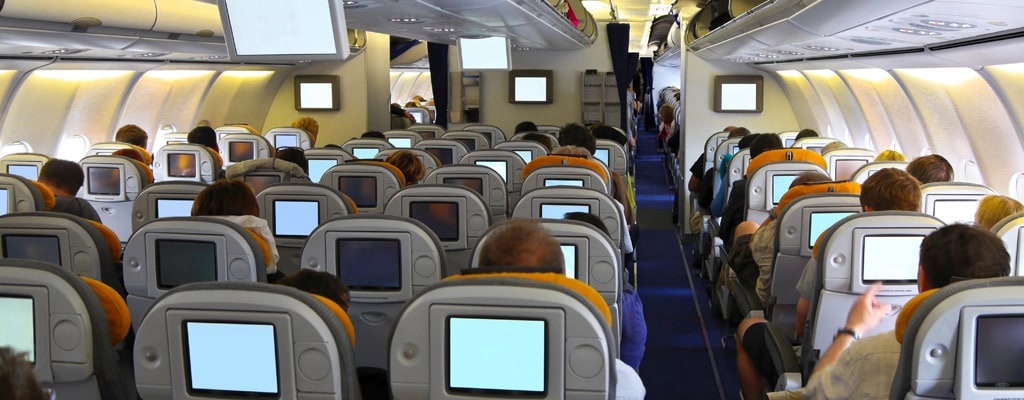
Trend Insight
Transitioning to Electronic Systems
Aircraft-cabin systems must support an increasing number of services, from video on demand to broadband access. But enabling connectivity in these systems still requires communication between boxes. By: Earle Olson, Former Business Development Manager, Aerospace
Aircraft depend increasingly on digital electronics for information and control. The trend toward MEA (more electric aircraft) highlights the transition from mechanical systems to electronically controlled systems. As the electronics content in both aircraft operation and passenger amenities continues to grow, so do the processing loads. Embedded computers are evolving to allow ever-increasing sophistication in flight sensors and radar. Distributed processing – moving the processing power from a centralized location to the point of use – still requires communication between boxes. The bottom line is that modern commercial aircraft do a lot more processing throughout the plane. High-bandwidth computing also requires higher bandwidth in the cables connecting the various boxes. While protocols like IEEE 1394 and USB are finding application, Ethernet has emerged as the de facto favorite, with 1 Gb/s today and 10 Gb/s soon being required to carry the load.
10Gbs
Ethernet required to carry future expected loads of data.
10-µm
Size of dust particle that can seriously degrade the performance of connecting ferrules.
At the same time, embedded computing systems and associated interconnections must meet the drive for lower SWaP, consuming less space, weight, and power. It also satisfies the need for rugged components to withstand the vibration and other hazards common in aircraft. As commercial aircraft offer more services to passengers – from video on demand to Internet access – the interconnection backbone delivering services to each seat must accommodate the higher bandwidth requirements. At the same time, aircraft manufacturers are looking at plug and play solutions that install easily, are robust and reliable, and require little or no maintenance. Given the life span of commercial aircraft, a physical layer that can accommodate future upgrades to electronics is equally desirable.
The Case for Fiber
Increasing data rates require designers to look at fiber optics as a way to deliver high-speed protocols over longer distances. An optical cable has three main benefits:
- Smaller size and weight. While fiber-to-copper comparisons depend on specific cable configurations, consider “generic” baseline cables: a duplex fiber-optic cable offers approximately 25 percent space savings and 50 percent weight savings over a shielded PVC Cat 5e cable.
- EMI immunity. Since optical fibers are inherently immune to electrical noise – neither receiving nor radiating energy – they can be applied without undue concern about EMI control. The potential need to shield copper cables only drives up size and weight.
- Longer transmission distances. While many interconnect distances in aircraft are relatively short, passenger cabins in commercial aircraft can present end-to-end challenges for copper cable.
There remains the perception that optical technology is harder to use and maintain, especially in terminating the fiber with a connector. New technology includes improved fiber cable for commercial and military air – for both fiber cable itself and connectors – that make the cleaning and maintenance easier. ARINC 801 contacts, for example, have removable coupling sleeves, while expanded beam technology protects the fiber core behind “safety glasses” and is defined in ARINC and SAE AS3 standards.
Another myth about fiber optics is a lack of robustness. Occasional lack of success in applying commercial transceivers is seen as evidence of the unsuitability for fiber in high-vibration, wide-temperature-range applications. This ignores the availability of ruggedized transceivers designed for aerospace environments.
Likewise, connector interfaces offer robust performance. There are three main termini used with optical fibers: ceramic ferrules, expanded beam termini, and MT multifiber ferrules. As one indication of robustness, all have been standardized in VITA 66.x specs to provide optical connectivity in VPX embedded computing applications and in ARINC 801 and SAE AS3 industry standards.
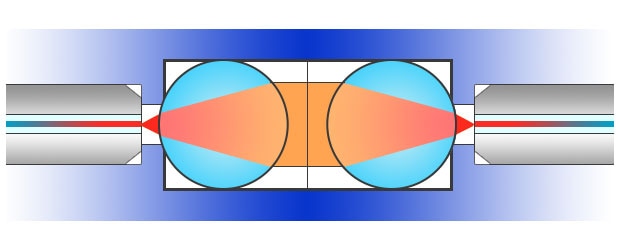
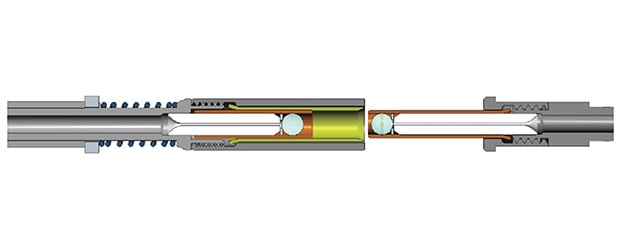
Furthermore, because the ferrule end-face is enclosed and protected behind the lens, the fiber will never require cleaning. Only the exposed outer lens surface can be contaminated, but is easily cleaned. Because the beam size is substantially expanded across the mechanical interface, the signal will not deteriorate by airborne contamination – for example, a 10-µm dust particle – that can seriously degrade the performance of connecting ferrules. The higher insertion loss of an EB connector is often outweighed by the life-long reliable and consistent EB performance.
The original EB connectors were purpose-built using a hermaphroditic interface or an insert for standard military connectors. More recently, the expanded beam concept has been adapted to a size 16 contact that can be used in a D38999 Series III or EN4165/ARINC 809 connector cavity accepting size 16 AS39029 contacts. With the wide range of inserts available for military (and commercial) connectors, it becomes easy to mix and match electrical signals, power, and optical – and even use both EB and PC termini in the same connector.
The Case for Copper
Despite the seemingly overwhelming advantages of optical fibers, copper cables aren’t going away anytime soon. Advanced cross-linked jacket and insulation materials reduce the size and weight of copper cables, while advances in modulation techniques and cable construction allow the cables to support high-speed data over distances up to 100 meters.
As I/O speeds increase, issues of signal integrity and power budgeting create new challenges. Simply put, high-speed signals are harder to manage than low-speed signals. The higher the interconnection speed, the more difficult it is to manage return loss, insertion loss, crosstalk, and similar factors that can degrade signals. While an ideal cabling system would have no intermediate connections between boxes, the real-world need for production breaks and modularity necessitates connectors in the path.
To address this gap in fast copper connectivity, TE Connectivity (TE) has recently introduced three families of CeeLok products capable of 10 Gb/s performance, each of which offers specific advantages to designers in performance and size.
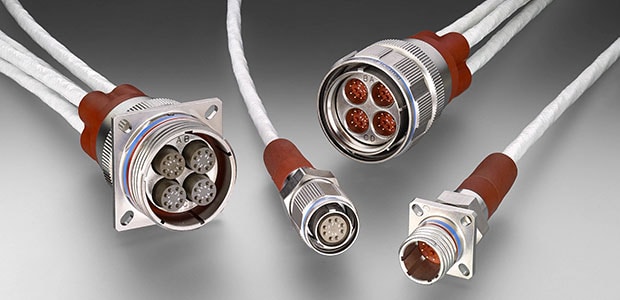
TE CeeLok FAS-X connectors use an innovative method to maintain shield continuity through the connector. As a result, the connectors can be concatenated multiple times without degrading performance. The connector is somewhat larger than the other two discussed here, but has the highest signal integrity, while still offering field reparability. The connectors support a single 10G Ethernet channel in a size 11 shell or four channels in a size 25 shell.
CeeLok FAS-T connectors are smaller – an eight-position connector in a size 8 shell. The connector’s T-shaped contact pattern provides noise cancellation and decoupling to minimize crosstalk and increase signal integrity. The backshell is integrated into the plug body to help provide low profile, low cost, low weight strain relief and EMI protection. The connector is field terminable and repairable.
CeeLok FAS-T Nano connectors use the same T-shaped contact pattern in a nanominiature size – plugs are only 0.3 inch in diameter, with a choice of push-on or threaded coupling. Unlike the larger CeeLok FAS-T connectors, the nano version is factory wired rather than field terminable. The connectors are based on the well-established NANONICS nanominiature connectors, but with an insert designed for high speeds.
Summary
Copper and fiber will coexist in most applications. Each brings specific advantages, from the comfortable familiarity of copper to the high-bandwidth capabilities of fiber over longer distances. As systems are challenged to offer users a seamless experience in handling data, video, infrared imaging and other bandwidth-hungry processes, both optical and copper connectivity must ensure that the end-to-end solution can accommodate production breaks in the path. The good news is that both technologies continue to evolve and give designers new options in meeting ever-increasing data loads