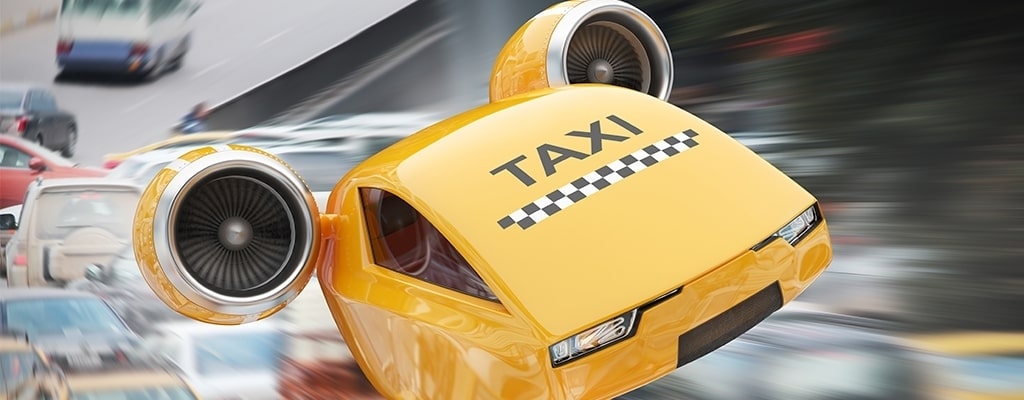
URBAN AIR MOBILITY
Accelerating innovations in Urban Air Mobility (UAM) with high power, high voltage interconnect solutions
This is the first in a series of white papers from TE Connectivity (TE) on solutions for meeting the challenges of urban air mobility (UAM) projects. For over 75 years, our global technology and manufacturing leadership has been empowering customers with a wide range of connectivity and sensing products for aviation, aerospace, automotive, and defense applications. As a go-to innovation partner, TE offers this overview of an evolving portfolio of products that can handle the significant power requirements of electric flight.
Opportunities
The sky is the limit for urban air mobility (UAM) projects, which are inspiring revolutionary innovations in electric flight. However, as with electric and hybrid-electric aircraft in general, electric-powered vertical takeoff and landing (eVTOL) aircraft, rotorcraft, commercial drones, and personal air vehicles (PAVs) employ significant amounts of electrical power to enable vehicle takeoff and maintain flight. As a result, designers face many electrical interconnect challenges when handling high voltages and high kW peak output for electric propulsion motors, inverters, controllers, batteries, infotainment, and sensors. To deploy successful prototypes and products rapidly, designers benefit by understanding these challenges and how to “follow-the-wire” using TE technologies and expertise to solve them
Challenges
At the beginning of a design project, it’s valuable to view interconnects holistically as part of the system rather than a lastminute afterthought. EVERY CONNECTION COUNTS for data and for power. Over the years, specific products have been introduced—and new designs continue to be developed--to handle power challenges encountered in electric flight. Advanced solutions from TE provide capabilities that include:
Preventing partial electrical discharge:
Managing high power is easier on the ground than in the air. That’s because high voltage can ionize air, which can become conductive to produce a corona discharge. The corona effect is responsible for electrical power losses through voids, cavities, and electrical treeing as insulation breaks down. Electrical arcing is the likely result. Occurrences of corona discharge can be minimized by selecting proper insulating materials.
Avoiding arc tracking damage:
With high voltage sources, carbon tracks may form on the surface of polymeric insulators, causing the insulator to lose its dielectric properties and become an electric transmitter instead. Electrical arcing can then occur across the conductive path, resulting in power loss with a high probability of ignition. Once again, proper insulation materials must be used to avoid this problem.
Handling the effects of environment on inception and extinction voltages:
Partial discharges can occur when two parts of a circuit that are not adequately protected from each other are subjected to high voltage differences. Voltage differences become more extreme as altitude, temperature, and frequency increase. Inception voltage is when the corona effect starts; extinction voltage is when it ends. Consequently, electrical systems must be protected to minimize critical voltage differentials encountered within the operating environment
Negating skin effect:
When determining proper shielding and filtering for electromagnetic compatibility (EMC), designers must account for skin effects---the tendency of AC current to flow close to the surface of a conductor. Skin effect is the result of eddy currents induced by the changing magnetic fields of alternating current and, therefore, is a factor in nearly every AC design. Printed circuit board (PCB) traces and other aspects of AC power circuits can be designed to negate skin effect, but expert planning is required
Managing size and weight constraints:
Components used in high power electrical energy storage and management can add weight and volume. High-efficiency relays and contactors are available from TE to handle higher voltage and amperage within a compact footprint, helping meet the demanding size, weight, and power (SWaP) requirements of electric aircraft. TE applies the same approach to minimize SWaP solutions for cables, terminations and connectors.
Managing thermal issues:
Dissipating heat, especially in composite structures can present challenges. When wires and relays are exposed to higher temperatures, pick-up voltage (VPI) and coil resistance (RC) are affected. To ensure stability, it is important to determine the steadystate characteristics for the temperature and voltage combination of a DC relay’s operating conditions. This is also true for AC applications, although their VPI exhibits less variation over temperature than with DC relays
Handling power management:
High-frequency switching enables rapid bus transfer in the event of power loss. There are valuable differences between hybrid electromechanical and solid-state power switching technologies that TE experts can evaluate for a given application.
Higher demand for reliability:
The number of take-off and landings will increase significantly in UAM applications. This puts additional stresses on the electrical interconnect system. TE strives to understand these new reliability levels and provide the appropriate product recommendations.
SOLUTIONS
Today’s UAM projects benefit from the cross-discipline development of power management solutions introduced by TE for automotive, aerospace, energy, and rail sectors. TE is working with industry standards groups—such as the Society of Automotive Engineers (SAE)—that are starting to deal with the challenges imposed by higher power and voltage levels. And TE experts are directly involved in Voice of Customer (VOC) initiatives to provide insights into solving aircraft power problems at the sub-system and component level. For designers, a "follow-the-wire" methodology uncovers critical factors in selecting the appropriate high-power and voltage solutions. TE supplies these needs with well-known families of power-management products:
KILOVAC high voltage relays and contactors:
Since 1964, the small, lightweight relays and contactors of the KILOVAC product line have been extensively used in aerospace, space, and military applications. Providing an excellent size to power ratio, KILOVAC high voltage relays and contactors offer voltage ratings up to 70kV DC and current ratings up to 1,000 Amps. Hermetically sealed for harsh environments, KILOVAC products function across a wide temperature range and feature outstanding shock and vibration performance with low and stable resistance over the life of the contact.
Hartman relays, contactors, and switching devices:
The Hartman product line is widely used in switching electrical power throughout airliners and other highly sophisticated aerospace applications requiring very specialized components. Hartman AC and DC contactors use lightweight, environmentally (gasket) sealed designs that meet applicable MIL-PRF-6106 requirements and/or specific customer specifications. AC contactors are rated up to 500 amps and lightweight highperformance DC contactors, up to 1,000 Amps. Hermetically sealed enclosures are available for the most severe environmental conditions. Multiple main contact configurations and auxiliary contact configurations are available. Additionally, Hartman modular power distribution units or backplane-type panels can be customized for fixed-wing aircraft and rotorcraft applications.
Raychem high performance power feeders and environmental sealing protection products:
Developed over 60 years ago by electrical engineer Paul Cook, the cross-linking polymer used in Raychem heat-shrink tubing and other products endures repeated heating and cooling cycles while retaining its original size and protective properties
AMP high-performance backplane power termination; STRATO-THERM and COPALUM terminals:
STRATO-THERM terminals, splices, and spare wire caps are designed for high-temperature applications up to 1200°F (649°C). COPALUM Lite sealed terminals and splices are up to 60 percent lighter than conventional copper terminals, which helps reduce aircraft weight.
DEUTSCH industry-standard connectors for power and voltage:
For over 70 years, DEUTSCH products have reliably performed in demanding aerospace, defense, industrial commercial transport, and motorsport applications. Today, TE’s DEUTSCH product line includes wires, contacts, and connectors, including military-spec components such as the MIL-DTL-38999 DEUTSCH Connector series
AMP high-performance backplane power termination; STRATO-THERM and COPALUM terminals:
STRATO-THERM terminals, splices, and spare wire caps are designed for high-temperature applications up to 1200°F (649°C). COPALUM Lite sealed terminals and splices are up to 60 percent lighter than conventional copper terminals, which helps reduce aircraft weight.
IMPLEMENTATION
With the broad portfolio of TE products, UAM designers can find reliable advanced technologies to achieve the optimum balance between performance, cost, and time to market. With a heritage in automotive, energy, and aerospace applications, TE offers innovative solutions to help meet the most demanding requirements. Tap our expertise in designing, customizing, manufacturing, and implementing all the components along the wire of the connected aircraft: sensors, monitors, circuit breakers, wiring, assemblies, and more. See how our high-performing solutions help UAM projects take off faster. For high-voltage TE relays, contactors, and related technologies, see our Virtual Developer’s Kit on Power Management for Alternative Energy.