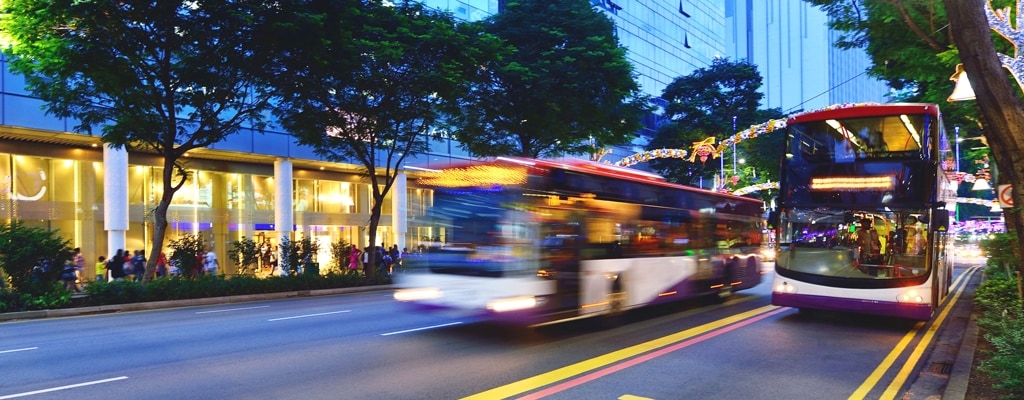
Trend Insight
The Role Ethernet in Autonomous Driving
Learn more about the connectivity requirements to enable commercial and industrial vehicles autonomous driving.
Author
By Mark Brubaker, Data Connectivity Product Manager, TE Connectivity
The autonomous driving trend has long since gone beyond passenger vehicles. Evermore commercial and industrial vehicles are looking into introducing advanced functionalities like driver assistance and automation, infotainment options, 360° camera systems, high speed V2V and V2I communications, and a wide range of essential safety features The new features and technologies will bring many advantages to commercial and industrial vehicles. They increase satisfaction and safety for drivers, while at the same time growing productivity and performance for operators, and lowering the Total Cost of Ownership for vehicle owners. Trucks, busses, and off-highway vehicles equipped with these advanced functionalities will “know” much more about their immediate environment and the route ahead: New features will significantly reduce fuel consumption and environmental impact while making driving safer for everyone.
Advanced Driver Assistance Systems (ADAS) technologies will be made possible by a vehicle-wide set of sensors –camera systems, radars/lidars, and more. They will enable advanced safety features like lane-keeping assistance, blind-spot detection, emergency braking, passenger watch, and drowsiness monitoring. Infotainment functions will not only include entertainment and communication systems for more driver satisfaction and enjoyment but also give access to vital information systems allowing the driver to monitor and pilot the vehicle, like 360° surround view and multimedia audio/video streaming to high-resolution digital displays and dashboards.
All these systems and devices must be interconnected via sophisticated networks for the transmission of high-speed data with low latency throughout the vehicle, enabling all information gathered by the devices to be processed through one or more on-board electronic control units (ECUs), to create a complete model of the vehicle and its environment.
However, there are still challenges to overcome before these new advanced functionalities can come on board. Commercial vehicles operate in harsh conditions, so component robustness is a major prerequisite. Essential terminals and connectors of in-vehicle networks must operate reliably and in real-time even in extreme environments. They must provide severe vibration and mechanical shock resistance, and allow field maintenance in the harsh environments in which commercial vehicles operate. This includes situations involving dust, dirt, and moisture, and even temperature ranges of -40°C to +125°C.
In-vehicle networks
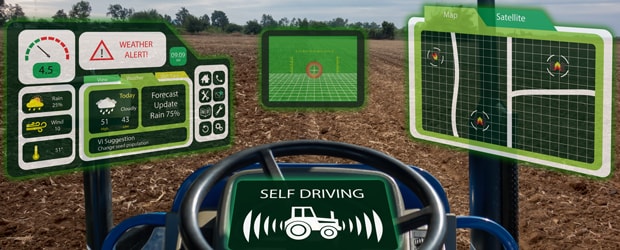
The in-vehicle network is the backbone of the vehicle, the underpinning infrastructure which makes all communication possible: within the vehicle, between vehicles (V2V), between the vehicle and infrastructures like the operator or control center or the manufacturer (V2I), and also, increasingly, communication with everything in the vehicle’s environment (V2X). The network provides reliable real-time data transmission, ensuring full information of the driver about every aspect of the vehicle, at all times, with advanced features like telemetry, cloud computing, and autonomous vehicle architectures.
As vehicles evolve towards being fully autonomous, they require and create exponentially more data than today’s systems, data that is delivered and transmitted by an increasing number of sensors and external antennas. In addition, much of the vehicle’s operational maintenance and updates will have to be performed via over-the-air (OTA) software updates, which requires even more high-speed data transmission.
The Ethernet - More bandwidth
Growing numbers of ECUs sharing real-time data on a much broader level are increasing the demand for more network bandwidth. The most common network architecture used in industrial and commercial vehicles today is CAN networks, SAE J1939. To create more bandwidth in an existing system, more CAN networks can be added. However, as requirements increase, completely new architectures will be needed to satisfy the data communication requirements. Therefore, the automotive industry has been developing new Ethernet standards tailored to meet the harsh requirements in industrial automotive communication networks, using 100BASE-T1 physical layer communication protocols on the basis of the OPEN Alliance.
The Ethernet creates a strong value proposition for automotive communication networks. The technical work done on Ethernet protocols for autonomous driving in passenger cars has already created an avenue for the commercial vehicles space to address their own new trends.
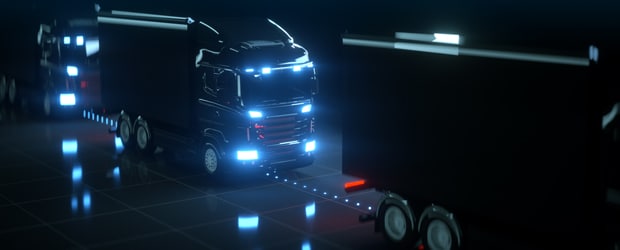
Ethernet is much faster than CAN. The 100 BASE-T1 and 1000 BASE-T1 Ethernet protocols can transmit 1 GB/s via UTP (Unshielded Twisted Pair), compared to only 500 kB with CAN and 1 MB/s with CAN-FD. Ethernet allows for a significant increase in the number of devices that can be supported in the network while enabling much higher speeds.
From a mere electrical standpoint, there is not much difference between Ethernet for passenger cars and Ethernet for industrial and commercial vehicles. However, application-wise, there are two key performance needs Ethernet must comply with within the harsher environments of commercial vehicles.
Mechanical resilience and higher vibration require larger component parts and larger pins. The larger the component, the more features can be put in to ensure high reliability in extreme environments. Larger components are also required for better serviceability. The service teams of commercial vehicles do not want to handle smaller and sometimes more fragile parts. These requirements compete with the need for more miniaturization and the integration of ever more devices, at ever-increasing high-speed performance.
TE Ethernet Solutions
To ensure high corrosion, temperature, dirt and vibration robustness as well as high speed performance, we have been developing completely new, advanced data connectivity systems for the Ethernet in industrial and commercial vehicles. For this application, we bring long expertise in automotive protocols and requirements for autonomous driving to new products that meet Ethernet protocol needs for increased bandwidth and increased speed, while maintaining a high level of reliability, especially in the harsh environment of the industrial vehicle space, where vehicles have to operate many miles and years in demanding operating environments without failure, or, if they fail, with fast and easy repair protocols. We have a range of product that supports Ethernet protocols while leveraging important connector families in the commercial industry.
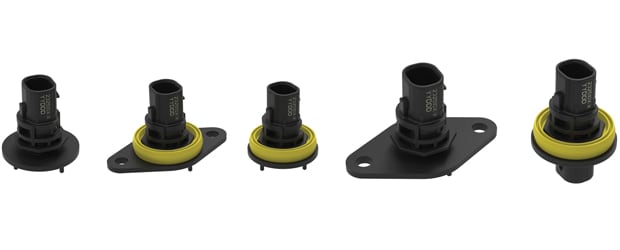
Sealed MCON Ethernet Connectors
Our new portfolio of Ethernet connectors provides robust full duplex, wire-to-wire connections for multifunction displays, telematics, telemetry units, infotainment modules and media access controllers and are ruggedized and sealed for operation and field maintenance in heavy duty environments. To secure contact retention these connectors feature built-in secondary locking and modular applicability for multiple panel thickness.
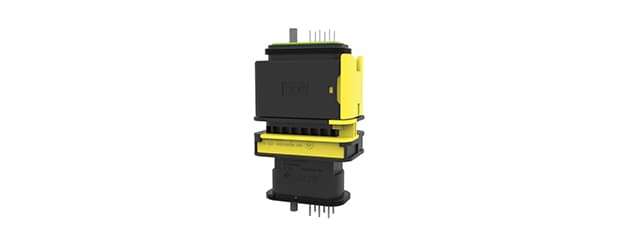
Heavy Duty Sealed Connector Series with MATEnet Inserts
The rugged, heavy-duty thermoplastic connector is combined with our MATEnet interconnection system for 1 GB/s+ automotive Ethernet applications according to IEEE 100BASE-T1 and 1000BASE-T1 Standards. MATEnet interconnection system contributes to modern E/E architectures and has been designed to specifically address today’s requirements of vehicle connectivity while already laying the foundations for future growth. MATEnet was specifically developed for IEEE Automotive Ethernet networks and set a standard for unshielded cabling. It relies on automotive-grade, miniaturized, robust and proven interconnection technology and has successfully passed severe testing and validation. Our Heavy Duty Sealed Connector Series with MATEnet Inserts can be used wire-to-wire and wire-to-device and features the flexibility to implement multiple hybrid interfaces and scalability, by using unshielded or shielded twisted pairs.
To Learn More About our Solutions for Connected Vehicles
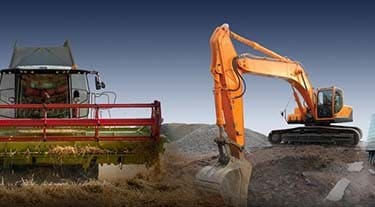
Connected Vehicles
Harsh Environment Requirements
Learn why the components, their placement, and the impact of environmental conditions must be considered at the early stage of your vehicle design to ensure high-speed data transmission.
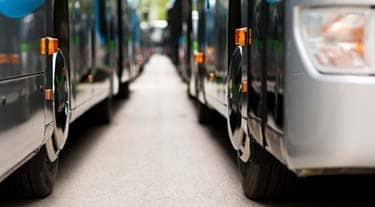
Data Connectivity
Heavy-Duty Vehicles Solutions
Discover why design engineers must consider incorporating Ethernet systems in their industrial and commercial vehicles and machinery to meet future customers' needs.
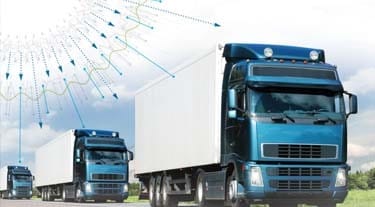
Ethernet Connectivity
Heavy-Duty Vehicles Requirements
Discover the considerations we took to design our Ethernet connectors for heavy-duty vehicles.
Originally published in Markt & Technik