During this webinar, Eugene Mayevskiy Principle Engineer will discuss COMFORT NX, TE's newest ergonomic cable design for medical ultrasound imaging.
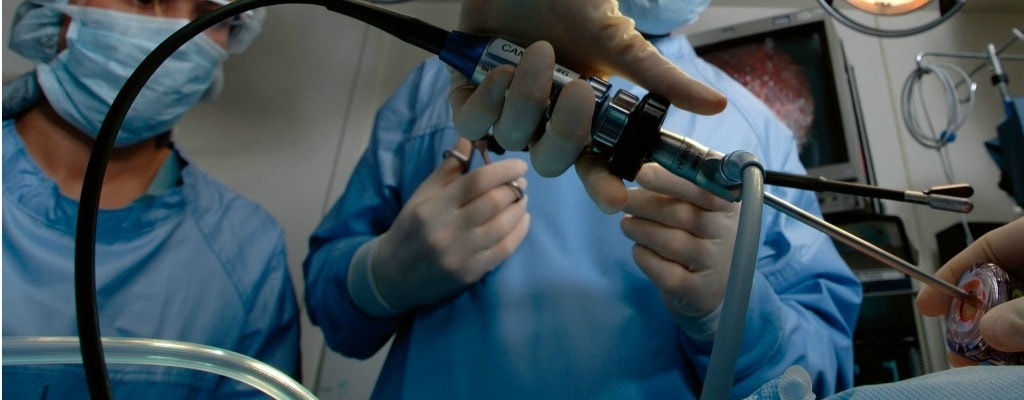
Reusable Surgical Cable Assemblies
With more than 30 years of experience in custom cables, interconnects, and shaft design and manufacturing, TE has the knowledge to help shorten your development time and help reduce development risk for the most demanding imaging and surgical device applications.
Connect to a higher standard of surgery connectivity. TE’s materials experts will guide you in designing a robust cable assembly that withstands the rigor of sterilization while maintaining user-friendly ergonomics for surgical settings. Our worldwide manufacturing capability offers cost-effective, on-demand production. With over 30 years in surgical product development, our proficiency in cables, connectors, tubing, and injection molding, TE has the experience to support you in developing your next generation reusable surgical cable assemblies.
Core Components and Manufacturing Capabilities
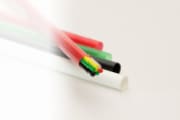
Materials
Whether silicone, PVC, or polyurethane, our experts can support you in selecting the optimal materials to develop your components to meet your specifications for sterilization and biocompatibility. Our extensive in-house manufacturing capabilities provide you with the flexibility to enhance your cable assemblies with re-enforced coverings or lubricious coatings.
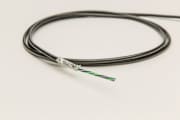
Wires and Cables
TE's design engineers can help you design the complete signal path, from probe tip to system interconnect. From HD quality video or low-loss power cables, we have the capabilities to support your complete electrical and mechanical design. Our product offerings include catheter cables, hybrid cables and micro-coax cables (52AWG) that are designed and developed to withstand high pressures, humidity, and variable temperatures while maintaining signal integrity and avoiding moisture ingress
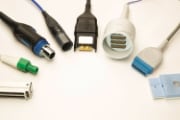
High-Precision Interconnect
Extensive portfolio of miniature high-speed connectors, power-edge card connectors, high-density one-to-many mating interconnects and smart (use-limiting) connectors to meet your exact requirements. Our manufacturing capabilities for high-precision connectors include precision stamping, plating, 3D circuits in plastic, insert and micro-molding.
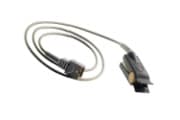
Optical Sensors
Capabilities for both photo optic components and the complete sensor solution.
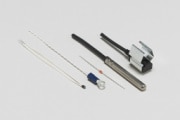
Temperature Sensors
Discrete NTC Thermistor with copper leads and epoxy coated of chip. Copper leads are soldered to the NTC chip. Leads are tin/lead plated. (63/37).
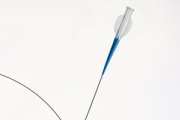
Molding
Capabilities include automated horizontal or vertical molding, over-molding, micro-molding and LIM silicone—all with the ability to withstand severe sterilization processing requirements. Our molding technology is ideal for enclosures, handpieces, and strain/flex relief for surgical devices.
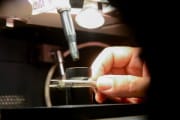
In-house testing
In-house testing for autoclaving, automatic washing, and other required processes.