
Temperature Effects on LVDT's
Learn how temperature can affect the performance and selection of LVDT position sensors.
For over fifty years, the LVDT linear position sensor has remained a reliable tool for linear position feedback for various laboratory, industrial, military and aerospace applications. An inherently reliable device, LVDT position sensors are capable of providing linear displacement measurements from micro inches to two feet with high accuracy while operating over a wide range of temperatures. While the output stability of LVDT linear position sensors is suitable for many applications, it is not immune to variation with temperature. Temperature effects can be significant in certain specific applications such as aircraft, subsea equipment, and turbo-machinery.
Temperature Variations on Output Signal
Temperature variations can affect the output signal from an LVDT in two different ways, including mechanical expansion and changes in LVDT electrical properties. Mechanical expansion causes relative motion between the LVDT core and the LVDT windings. The net effect is a false core motion signal that produces a zero-shift error. Temperature can also affect the electric properties of the LVDT by changing its primary input current or the magnetic properties of the core materials. This produces a scale-factor change or span-shift error.
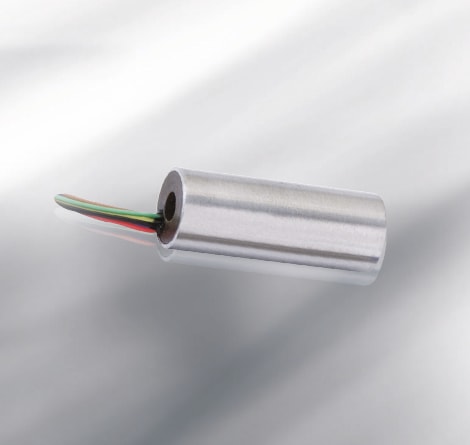
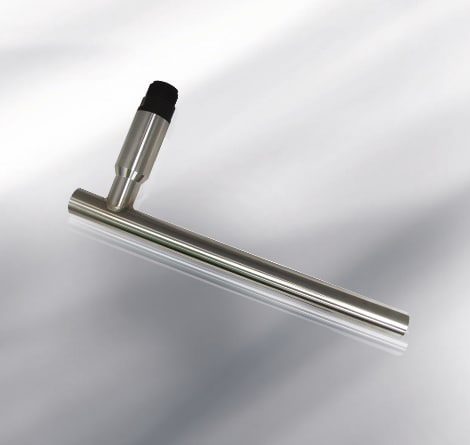
AC vs. DC LVDT Output Signals
The maximum operating temperature of AC-operated LVDT position sensors are 300°F, as electronics can be located remotely from the sensor. A DC-operated LVDT, on the other hand, that contains electronics within the body of the sensor, is limited by the properties of the materials in the electronic signal-conditioning module. DC-LVDTs can operate at temperatures as low as –40° F, if the temperature remains nearly constant.
Ambient Temperature
Ambient temperature variations have a predictable effect on the operation of an AC- and DC-operated LVDT. While signal conditioning can help compensate for the primary current changes for the AC-LVDT, the DC-LVDT cannot use this tactic due to space limitation.
Temperature Effects on LVDT Materials
The effect of temperature variation on the magnetic properties of the LVDT core material is small and has negligible influence on transformer operation over the ordinary operating temperature range. To offset the effects of the thermal coefficient of the expansion of the LVDT materials, LVDTs are constructed to expand symmetrically from the center toward either end. New construction techniques and materials also enable LVDT operation in hostile environments including those with high and low temperature extremes. Custom LVDTs can be designed for operation at continuous temperatures as high as 400° F. The high temperature ratings are achieved by using special construction materials for the linear position sensors that include special high melting point soldering.
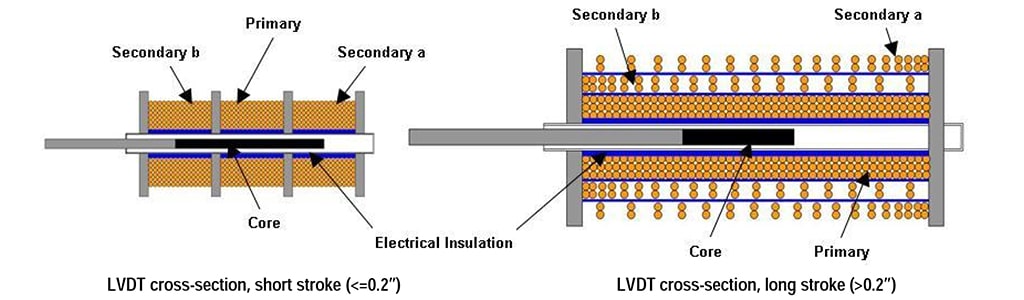
Temperature-Induced Resistance Variation
A rise in transformer temperature produces an increase in the resistance of the copper wire ordinarily used to wind the primary and second coils. The most direct consequence of this resistance increase is an increase in primary impedance.
Primary Current Stabilization
A constant-current excitation source is an obvious, but not always practical solution to temperature effects. If a constant-current power source is not available, primary current may be stabilized somewhat by connecting large external resistance in series with the primary.