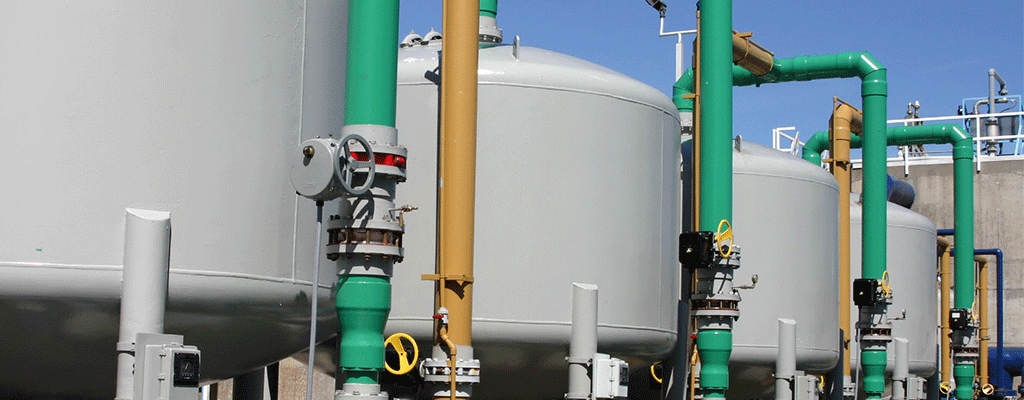
Tank Level Measurement with Pressure Transmitters
Gauge and differential pressure transducers can be installed externally to a tank for liquid or gas level measurement.
Gauge and differential pressure transmitters are reliable, cost effective instruments to measure the hydrostatic level of liquids, such as water or fuel, in vented or sealed tanks. The tank level pressure transmitters should be mounted to the bottom. Typically, the transmitter will be threaded into the outlet line of the tank, a side bung, or flange. Since transmitters provide a linear output signal, e.g., 4 to 20mA signal from zero pressure to the full-scale pressure, the level can be monitored based on the liquid density and the height of the tank. The actual shape of the tank is only needed when a customer uses the liquid level to calculate volume.
EXAMPLE
Density of water at 4°C = 1
Height of tank = 35 feet = 420 inches
27.68 inches of water column = 1 PSI
(420 inches / 27.68 inches of water column) x density of 1 = 15.17 PSI
Here, the height of the tank is converted into a measurement range. Since the pressure cannot exceed the height of the tank while considering the density of the liquid, the user can measure the maximum amount of signal for the specified range.
VENTED TANK
Gauge versus Differential
The only difference between a gauge and differential pressure transmitter in this example is that the differential pressure transmitter will have P2 vent to the atmosphere, where the gauge pressure transmitter will typically have a tube within the cable to allow for changes to barometric pressure. The vent tube of the gauge pressure transmitter should be protected from humidity, especially if there are wide temperature changes between the liquid and atmosphere. This is typically accomplished by venting the sensor inside a control box that is protected with desiccant or by applying a desiccant filter to the end of the vent tube.

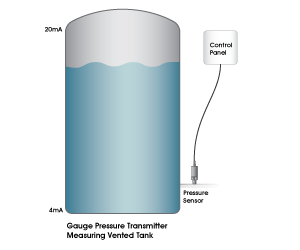
SEALED TANKS
Sealed tanks, such as LNG storage tanks, are required to be sealed from the atmosphere. Under this condition, a differential pressure transmitter should be used to calculate the difference in pressure between the top and the bottom of the tank. P1 of the differential would be installed at the bottom of the tank. A pipe connected to P2 would be connected to the top of the tank. When full, the differential pressure will be the maximum output signal. As the tank level is reduced, P2 will increase and the differential pressure will decrease along with the output signal.
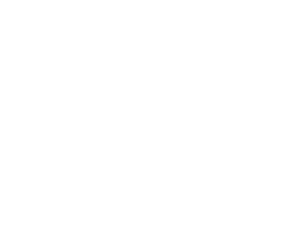
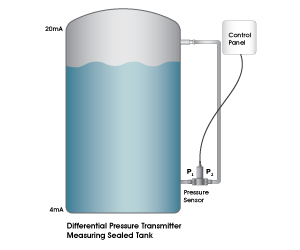
OUTPUT SIGNAL SELECTION
The selection of the output signal is always application specific. 4 to 20mA output signals are most common in monitoring applications that require long distance transmissions. The current can be read at the controller without signal loss for hundreds of feet. The downside is that the sensor will require more power and more importantly, current. For either battery powered or solar powered applications, voltage output signals are suitable. Typically, the solar panel will be located close the pressure sensor, so there is no signal loss caused by the resistance in cable.