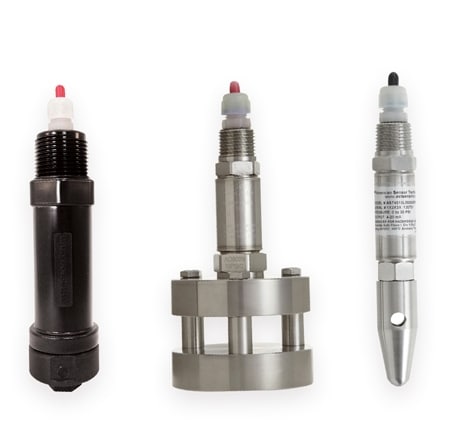
Submersible Pressure Transducers
TE Connectivity’s submersible pressure transducers are designed to measure liquid levels by sensing pressure in applications such as holding tanks, oil or fuel tanks, and irrigation equipment. Our portfolio offers a wide selection of configurable options and include intrinsically safe models that are approved for use in hazardous locations.
Liquid level can be determined using a submersible pressure transducer by taking a continuous pressure measurement from the bottom of the tank or measurement point where the transducer's diaphragm is placed. If the pressure transducer is located at the bottom of the measurement range, such as resting at the bottom of a tank, the pressure is proportional to the height of the liquid directly above it. If the tank is vented to atmosphere, the pressure transducer can also be configured with a vented gauge measurement type, utilizing a vent tube within the cable to correct for barometric pressure changes.
Portfolio Features
Configurable options available
- High strength stainless steel construction
- Certified for Class I Zone 0 Ex ia IIB T4 Ga
- No internal O-rings
- Engraved housings
- Pressure ranges up to 240 psi
- Voltage or 4-20mA output
- Pressure accuracy to +/- 0.1% FSO
- Conduit fittings at electrical connections
- Wide range of media compatibility
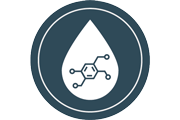
Liquid media compatibility
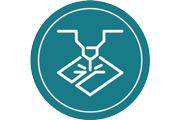
Engraved housings
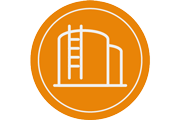
Tank level measurement
Applications
- Groundwater level
- Biofuels
- Gasoline and diesel fuel tanks
- Fertilizer tanks
- Irrigation equipment
- Ballast tanks
- Oil tanks
- Wastewater canals
- Saltwater holding tanks
- Lift stations
- Food tanks
- Earthen and concrete dams
- RV and marine holding tanks

How to Calculate Liquid Level Pressure
Submersible Pressure Transducers
The pressure at the bottom of the tank or body of liquid is related to the height of the liquid. This level pressure is called hydrostatic pressure or head pressure.
Typical units of measure for hydrostatic pressure are inches, feet, or meters of water column. 27.679 inches of water column (WC) is the approximate equivalent of 1 PSI at 100°F.
The volume of water or shape of the tank or vessel will not affect the hydrostatic head pressure; it is the height that affects the pressure. Whether 27.679 inches deep in the middle of a large body of water or a small bucket of water the head pressure is the same.
Modern PLC's and HMI's can calulate the liquid level of a tank by entering the geometry of the tank and the specific gravity of the liquid. Water density at 100°F (37.8°C) = 60.00 pounds per cubic foot. As you can see in this example the pressure exerted by a column of water is dependent only upon the height of the water column and is independent of the affected volume.
Examples:
(Height of the tank (inches) / 27.68" water column) x liquid density = Measurement range in PSI
35 foot tall water well (420 inches)
(420" / 27.68") x 1.00 = 15.17 PSI
35 foot tall diesel tank (420 inches)
(420" / 27.68") x 0.833 = 12.64 PSI

Typical Mechanical Installation
Consideration Factors
There are a variety of factors to consider when thinking about how to install a submersible pressure transducer. This outline drawing shows one installation method for the AST4510 submersible transducer inside a tank using a rigid pipe. The AST4510 offers a standard 1/2" NPT male conduit connection at the base of the cable connection.
In tanks that are turbulent due to an inlet/fill pipe or the use of an agitator, the transducer can have rigid plastic or metal conduit installed over the cable to prevent sensor movement within the tank. It is most common in mobile applications such as ships, train cars, or applications where the tank is transported between locations such as fuel tanks for construction sites, chemical totes for industrial processing, or well site injection chemicals.
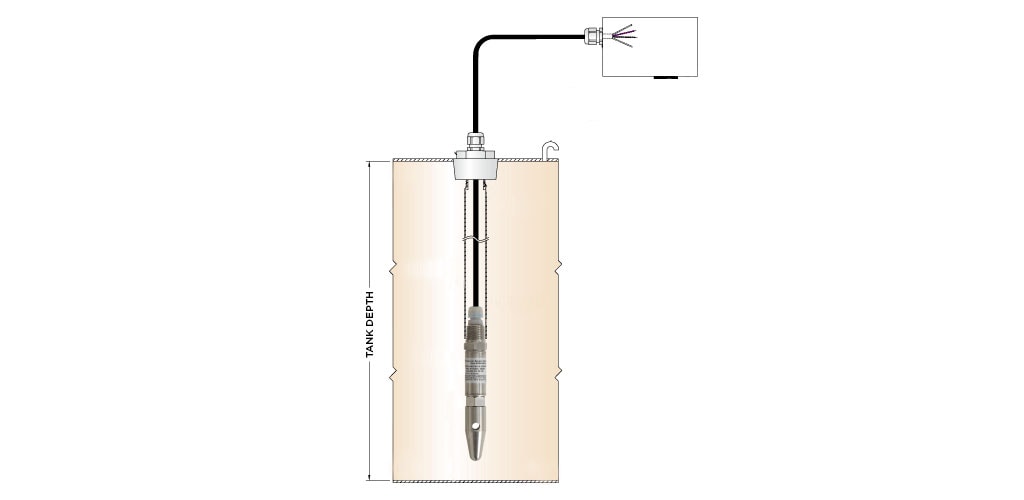
The conduit over the cable is then mounted to a bung at the top of the tank. A popular option is a fitting which threads onto a 1.5" female NPT bung and has a 1/2" female NPT thread to mate the rigid conduit. (Other bung sizes are available for different applications). The cable then exits the tank and is held in place by a cord grip which runs to the control box. The same cable grip can be used at the junction box, ensuring that the vent tube is clear.
Depending on the hazardous location requirements, this can be in the non-hazardous area with connection to the intrinsically safe barrier.
In this example, it is expected that the junction box is properly vented to atmosphere on the bottom to prevent water ingress. In this application, the sensor was installed above the base of the bottom of the tank. Sludge and silt tend to line the bottom of the tank, so a height of 100 millimeters was calculated to ensure the process connection does not clog over time. The diaphragm of the transducer is close to the top of the process connection hex, so the customer can calculate the offset from the tank being empty. Another option would be a flush diaphragm submersible pressure transducer, like the AST4520.

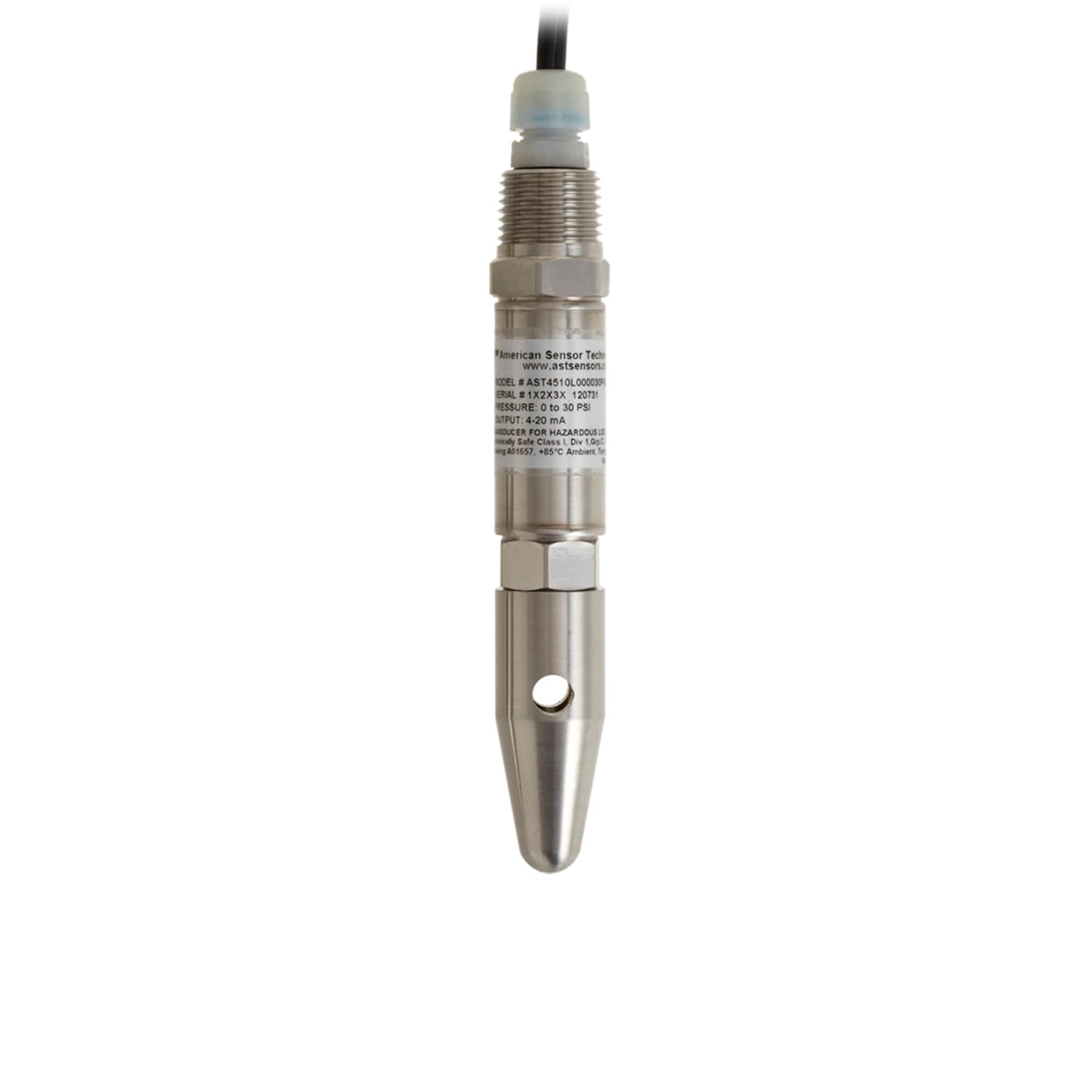
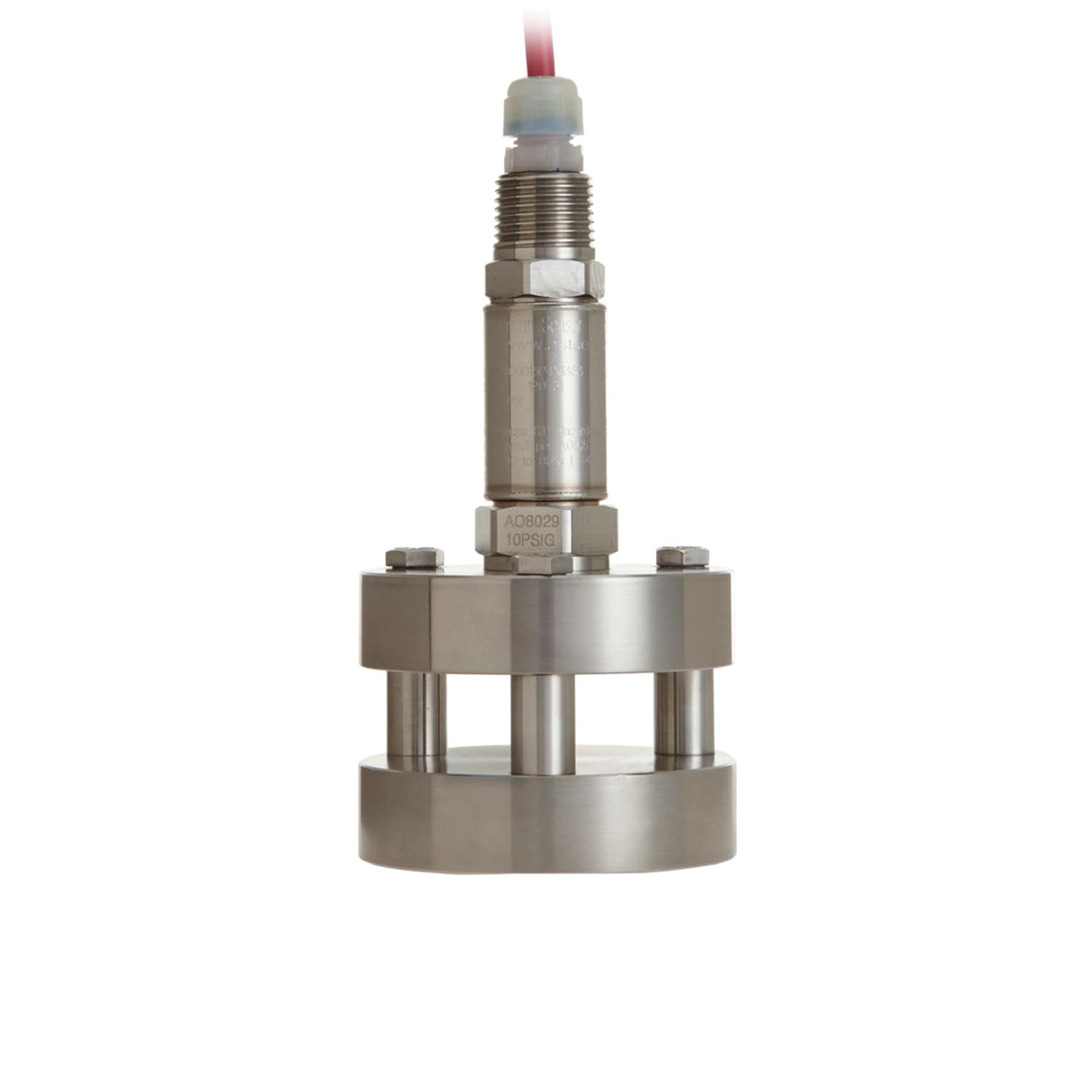
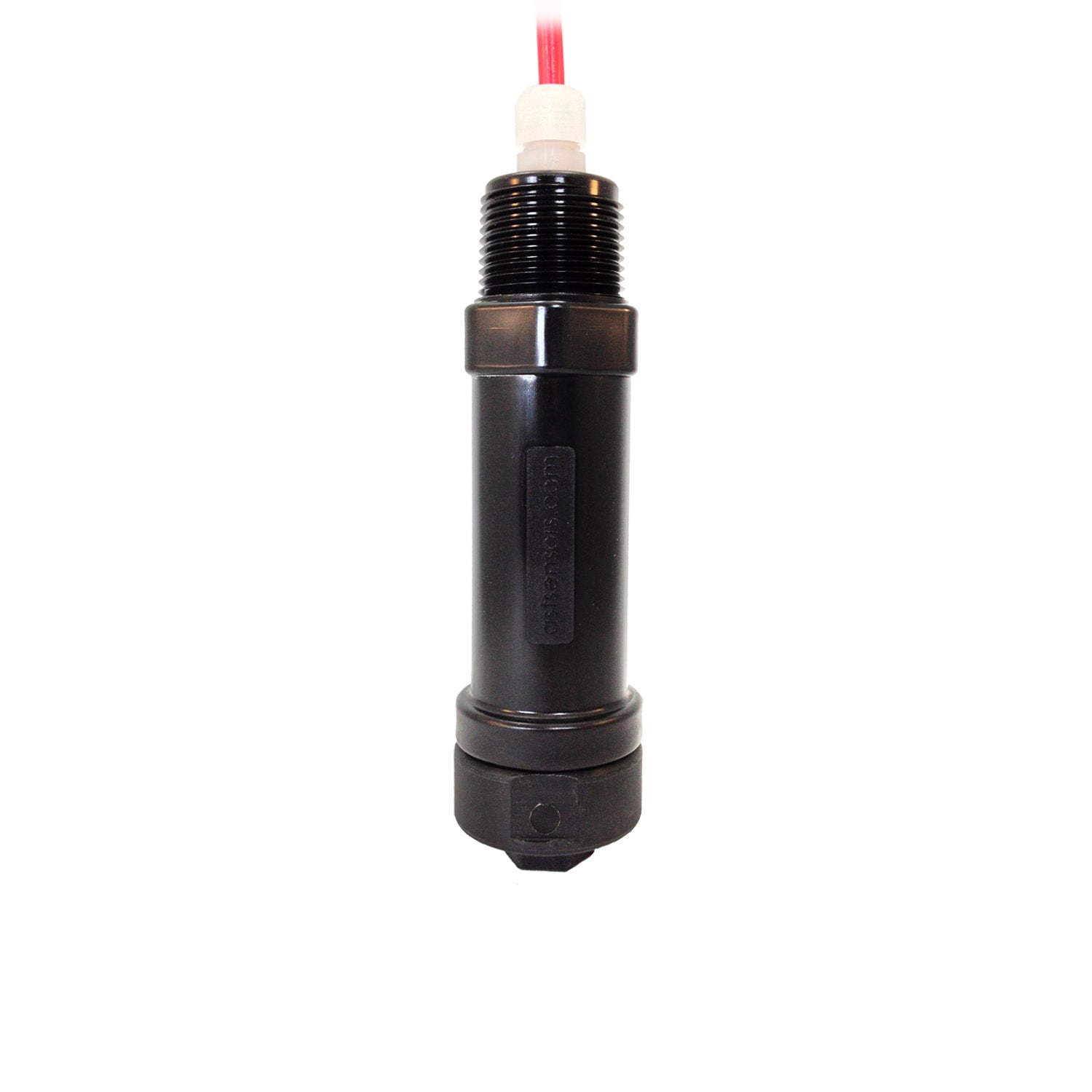
Other applications will have the submersible pressure transducer installed directly into an intrinsically safe radio device at the top of the tank. This reduces the cost of the transducer, because less cable is required and can reduce the time required for installation. With shorter cable lengths, TE can also offer a voltage output signal with low current consumption if the system is battery operated. Less current consumption means longer battery life and less maintenance.
Submersible pressure transducers are cost effective, offer excellent compatibility with liquids, do not have issues regarding reflection or foaming, and can offer low current consumption for battery powered applications. Fresh water, diesel fuel tanks and chemical totes all use submersible pressure transducers for level monitoring.