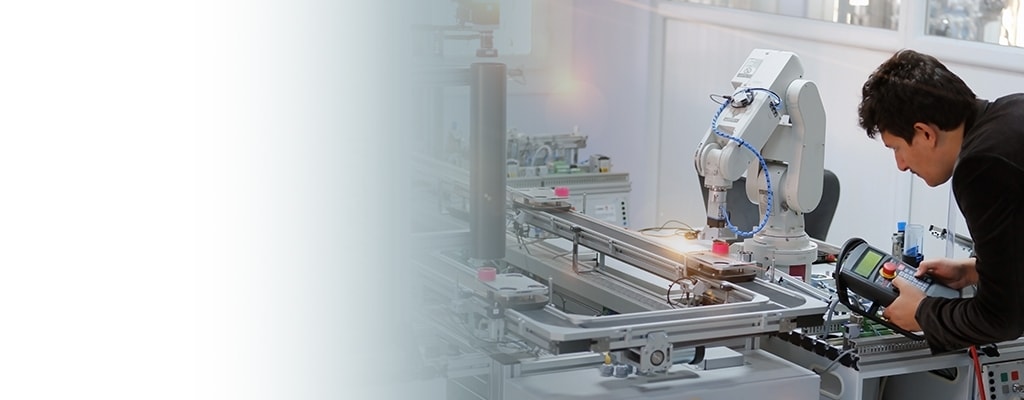
Microfluidic Cartridge Pilot Line Development
Trust TE Connectivity's expertise in microfluidic cartridge pilot line design and setup with the ability to develop novel production processes.
As sales improve and you shift from small-batch to moderate-volume production, We can leverage our present TE pilot lines to reduce your initial CAPEX or create a novel robust pilot line that allows you to meet growing market demand. We can develop your line alongside proprietary platforms or as a complete end-to-end solution. Our facilities are ISO 13485:2016 certified and FDA registered with dedicated ISO 5 and 7 (Class [NS1] 100 and 10,000) cleanrooms to ensure cartridges are sterile, RNase/DNAse free etc. upon manufacturing.
Manufacturing Capabilities and Services
- Microfluidic Pilot Line Production
- Design for Manufacturing and Assembly (DFMA)
- Six Sigma DMAIC [NS1] Process
- Prototype Production
- Photolithography Technology (Class 10–100)
- Thin Film Processing
- Plasma Etching
- Microreplication (Hot Embossing, Casting,Micro-Milling)
- Microinjection Molding
- Surface Treatment
- Automated Reagent Deposition/Integration
- Bonding Technologies (Solvent, Wire, Ultrasonic, Fusion, and Adhesive Bonding)
- High Throughput Lamination Equipment (Adhesive
and Thermal)
- Laser and Sonic Welding and Assembly
- Membrane Placement
- Leak Testing
- Heat Testing and Treatment
- Blister Forming, Filling, and Sealing
- Microfluidic Chip Design
- Clean Room Assembly
- Installation/Operational/Performance Qualification
- Supply Chain Management
- Inventory Management
- Gap Manufacturing
- Process verification and validation
Microfluidic Pilot Lines
Pilot lines present a way to fulfill growing demand for cartridges while simultaneously developing and testing high-volume manufacturing processes. This allows you to bridge the gap from small-batch to high-volume production smoothly while prioritizing reproducibility, accuracy, and throughput.
Whether your device is designed at the macro, micro, or nano scale, TE can use present pilot lines or establish new ones at one of our manufacturing facilities in the USA or Europe. Moreover, we can help you overcome the microfluidic pilot line challenges associated with micro-scale manufacturing (such as the combination of macro and micro features, process step combination, assembly, and QC). Our team helps avoid manufacturing gaps, ensuring that production demand is met and follows you as demand increases.
Areas of Expertise
Clean Rooms for Microfluidic Manufacturing
To ensure that microfluidic cartridges are sterile upon manufacturing, TE utilizes
ISO 7 (Class [NS1] 10,000) clean rooms in accordance with the FDA QSR, ISO 13485, and ISO 14644-1 to establish contamination control and ensure that airborne particulate concentrations are effectively limited and regularly monitored. Packaging and inspections are carried out in the clean room in a static-controlled environment. Clean room operations are carefully managed, with specially trained staff adequately clothed and surfaces and equipment kept clean and sterilized. TE also employs Class [NS2] 10-100 clean rooms for specialized purposes like photolithography and MEMS.