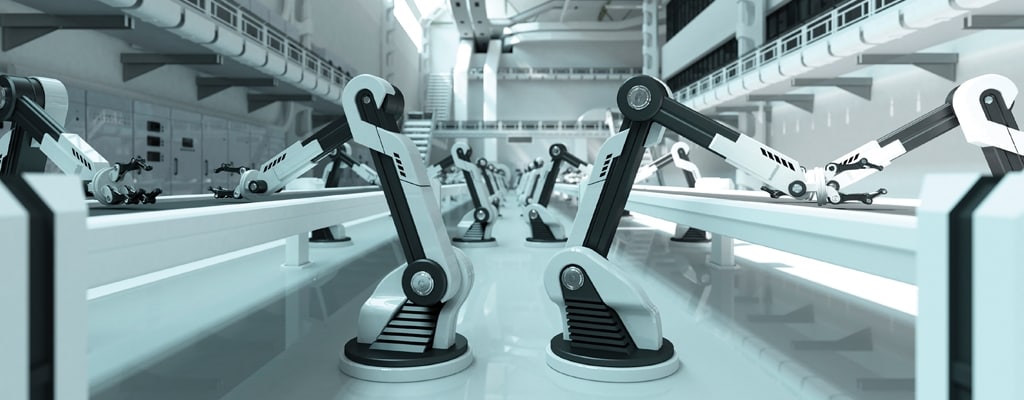
Trend Insight
Accelerating Industrial Internet of Things (IoT)
As Industry 4.0 (I4.0) advances machine-to-machine (M2M) communications, factories can now integrate crucial processes and reduce production cycles. But are these improvements enough to make factories smarter? By: Daniel Walldorf, Project Manager, Innovation Platforms & Ventures
It is 2:00 am, and the machine in Europe is down. The planner accesses the system and finds out that products have to be shipped in the morning. He immediately sees open capacities and a stock of raw material in his factory in the US and triggers a start of production there. Back in Europe, a maintenance technician is informed and he sees immediately machine process data in his office and can locate the problem to a workstation. On the shop floor, from his tablet, the technician accesses the workstation and begins modifying the data-acquisition time for the process data. In minutes, he recognizes and solves the problem. The machine is back up and running again.
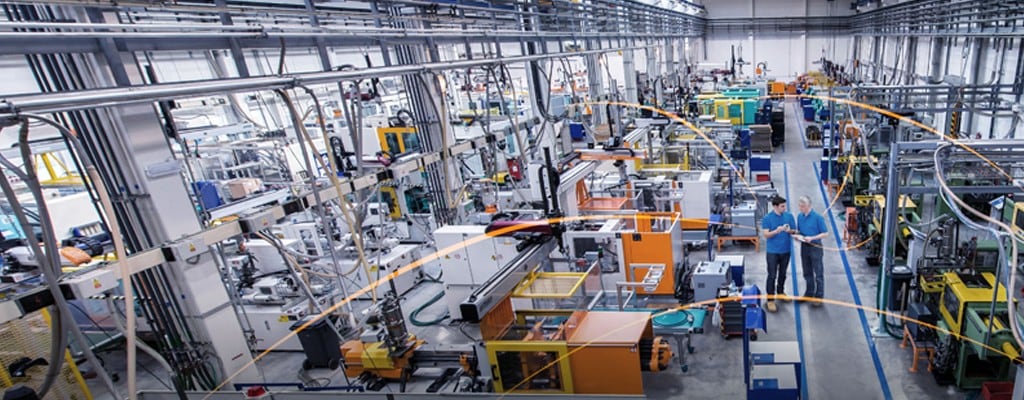
Understanding the Challenge
For most companies, this level of speed is the aspiration, not the reality. What is perhaps most significant is that this case is only about one small part of the capability a smart factory can perform. In the digital factories of tomorrow, everyday operations will include predictive maintenance, flexible machine use-and-upgradability, production and raw material footprints of goods, tracking and tracing of goods in productions with mass customization, and energy efficiency.
+20%
Reduction in process inefficiencies realized.
I4.0
Industrial IoT, combination of information and communication with production processes.
There are many opportunities for generating value. This involves making process data and metadata from machines more available to – and transparent for – planners and technicians, down to the most granular machine level. Looking at current machine infrastructures, there is a large quantity of data that is created but not available. The challenge is that machines have a hierarchic control structure which is – in most aspects – optimized for fast and efficient machine control. The data relevant to this control structure is transferred with very low latency, with the control system requiring cycle times in the range of milliseconds. This increases the stress on the machine control, which must process additional data that is not latency relevant. To resolve this type of challenge, our team approaches the critical issues from three perspectives.
Enabling the Smart Factory
Our Three Perspectives
Devices, Connectivity, Content
- Smart devices: Determining which components will enable data creation, starting with smart relays over additional sensors and connectors that function as smart devices, by collecting – for example – information about energy consumption or monitoring condition.
- Physical connectivity: Positioning more smart devices inside a machine creates additional connections, which generates more data to be transferred and at the same time, reduces the size and cost of nodes; this leads to the need for alternative connectivity solutions including wave-guided data transfer and wireless solutions.
- Connecting the content: Managing a data path for added value data; the connectivity solution will need to manage, aggregate, buffer, and process data as well as open up a secure path to transmit data to the enterprise-level IT system.
At TE, our team is collaborating on new ideas related to these three perspectives. Our goal is to transform the concept of the smart factory into an operational reality. To accomplish this, we are developing smart relays that are capable of recognizing component failure and directly switching over to a replacement. We have manufactured connectors that monitor energy consumption. We have built a new solution for transferring 1 GB/s across only two wires. We have also developed a way to leverage microwaves travelling in plastic fibers to achieve high-speed connectivity through miniaturized, cost-efficient components. Our sensors offer the capacity to communicate wirelessly and synthesize data with a cloud-based interface.
Achieving Results
Before we recommend our innovations to our customers, we rollout our ideas in our own digital factories. This ensures that the solutions are tested to be smart and bring the value that we anticipate. Through these initiatives, we have implemented smart-data aggregators in a model which have enabled us to visualize real-time data for complete production value streams of connectors on factory level. This enabled our production team not only to drive incredible improvements in yield and process time but also to an overall reduction in process inefficiency. In the next steps. this approach will be extended to synchronize material management and rollout the system to more TE factories.
Currently, the industry is changing from traditional factories towards smart and digital factories. In this transitional phase, it is important to find solutions that can be applied to upgrade factories instead of looking only towards Greenfield applications. We believe that in this phase it is especially important to enable fast benefits that justify investment needs for the upgrade, while not losing the focus on doing this with an architecture that will leverage a variety of productivity improvements in future. This means being backwards compatible while opening new opportunities. Smart connectivity achieves this act of balances easily and is therefore our key to smart factories.