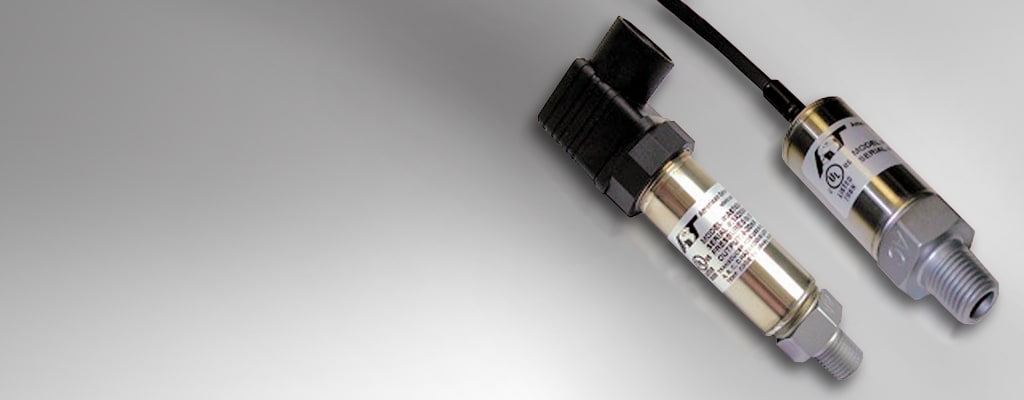
Trend Insight
Sensing Pressure
As system integrators and OEMs strive to increase reliability, safety, and performance while decreasing cost, the need for sensors embedded into manifolds, load holding valves, actuators, and pumps is becoming of paramount importance.
Pressure sensors, second only to temperature sensors in usage, are experiencing growth in hydraulics, water, medical, and many other applications where size and performance are of key importance. As the pressure generated inside systems are increasing to improve efficiency, the size of the system is decreasing. The cost savings of a more compact system is forcing pressure sensor manufacturers to develop a smarter solution. Standalone sensors that offer integral electronics, EMC protection and temperature compensation are acceptable for applications with adequate space, however, they are not suitable for compact and miniature systems.
Embedded sensors can be used in high temperature, vibration, and radiation environments with the electronics isolated from these hostile environments.
Embedded pressure sensors can be designed to provide either a compensated or uncompensated output based on the price and overall performance targeted for the system. Certain people have the capability within their electronics to characterize the uncompensated sensors (learn the performance characteristics of the sensor over pressure and temperature) to optimize use within the application. For uncompensated sensors, the user needs pressure and temperature inputs to read precisely how the sensor is reacting before the data can be used. Uncompensated sensors tend to be lower cost and offer flexibility if someone can characterize within his or her electronics. Compensated sensors are easy to use since these are characterized over pressure and temperature at the factory. An amplifier module is required to get the desired output. Since the sensor is supplied to the user to perform to a specific accuracy over pressure and temperature, the user has less to test or program.
In most cases, the use of remote electronics tends to offer the best options when using embedded sensors. Depending upon the technology and media, embedded sensors can be used in high temperature, vibration, and radiation environments with the electronics isolated from these hostile environments. When using low impedance (i.e., less than 2 kΩ, high-output silicon piezo-resistive strain gages), the user can allow the electronics to be located several feet away from the sensor. The wetted material and clamping configurations for the embedded sensors must be carefully selected to avoid costly failures. Using 316L stainless steel is well suited for applications such as water, oxygen, hydrogen, and many other hostile and critical media. Titanium and nickel alloys are preferred in medical and toxic media such as body fluids, hydrogen sulfide, and bleach. Figure 2 shows typical configurations of pressure embedded sensors for use in hydraulics and medical OEM equipment.
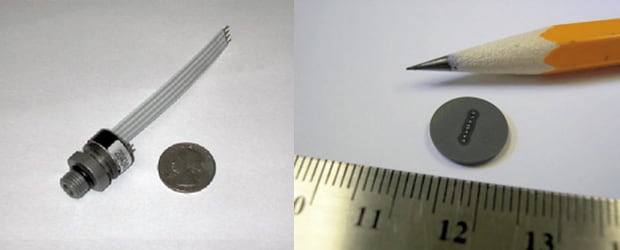
Pressure sensing technologies play a vital part when considering the integration of an embedded device. Reliability and longevity are the two keys factors that dictate system performance over time. In critical processes such as medical, semiconductor and industrial, which involve gases such as hydrogen and oxygen, it is very important that the pressure sensor does not introduce contamination into the process. Figure 3 shows two types of sensor technologies that are popular with embedding; each technology measures pressure in a unqiue way, with different capabilities to contain pressure. The main variation is the potential for contamination within the process.
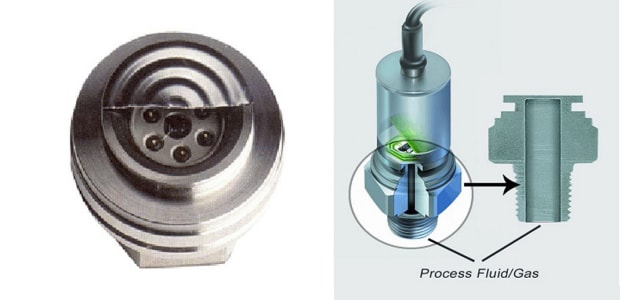
As valves and actuators are being used in critical applications such as nuclear, hydraulics, and automation, embedded position sensors are growing in importance and usage for position feedback. The linear position measurement can be from a few millimeters to meters long. Sensing valve seating is becoming a key area due to safety in the nuclear and hydraulics industry. Similar to the pressure sensing technology, choosing the correct technology for position sensors plays a vital part of the system performance and reliability. For years, position sensors had relied on either contacting or non-contacting technology. In contacting technologies, such as a linear potentiometer, a slider attaches to a moving member, which makes direct contact with resistive device. The potentiometer, acting as a voltage divider, provides an output that can go from 0 to 100% of the applied voltage as the slider travels from one end of the device to the other. These devices tend to be lower cost, however, they are not suitable for high vibration and need to be protected from dust and liquids. Non-contacting technologies, such as optical, variable reluctance, eddy current, magneto restrictive, and linear variable differential transformer (LVDT) have been successfully employed. These devices offer much better performance and reliability in comparison to potentiometers. Optical sensors based on laser interferometer, wavelength, and intensity modulation are only used in lab type conditions and are suitable for harsh media. Variable reluctance type sensors are excellent choices for wide media and temperature, however these are highly non-linear and only operate over a short sensing range. Eddy current devices tend to operate at higher frequencies and require the signal processing electronics in close proximity to the sensor. This limits the device's capability to operate over a wide range of temperatures and radiation. Magneto restrictive sensors while offering excellent performance are also limited to operating temperature due to the close proximity of the signal processing electronics.
For years, LVDTs have been used in commercial and military aircraft applications such as wing flaps, fuel pumps, and landing gear where reliability is critical. These devices employ low frequency (3- to 5-kHz) magnetic circuits and do not generate any radio frequency (RF) noise in comparison to the Eddy current or other high frequency operated linear sensors. The low frequency operation allows these sensors to be separated from the electronics by several feet. Since the LVDT device utilizes a magnetic coupling from the primary to secondary coils and no physical connections, these sensors can be hermetically sealed against water, dust, and ice. By using modern application specific integrated circuit (ASIC) based electronics, the length of the sensor can be reduced significantly in size while maintaining maximum performance. The ASIC allows digital signal processing with full compensation over a wide range of temperatures. This technology has opened the market for linear non-contacting sensors to be used in tight-space envelopes such as valve seating and subsea chokes in cylinder sensing. Figure 4 shows two non-contacting position sensors that can be embedded in valves and transmissions.
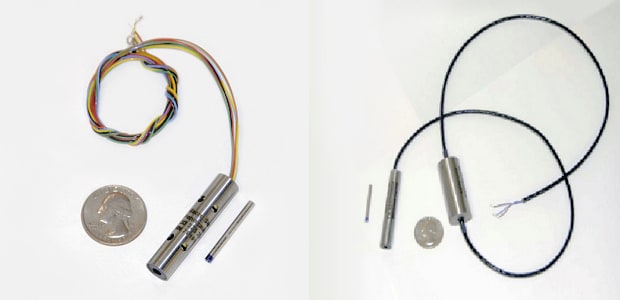