TE Connectivity (TE) delivers cabled backplane products that provide maximum flexibility and throughput with exceptional signal integrity.
As data center equipment speeds continue to increase, traditional FR4 printed circuit board (PCB) substrates may no longer provide acceptable transmission performance, especially at 25 Gbps and beyond. Core switches and routers need maximum throughput with superior signal integrity, and as these systems achieve greater computational power, the backplanes and the number of daughter cards they support become greater in size, number, and complexity. Many equipment manufacturers are looking for connectivity alternatives to PCB substrates, and high-speed cabled backplane technology has emerged as a primary option. In this paper, we will examine the need for high-speed cabled backplane connectivity, its advantages over PCB-based alternatives, its potential drawbacks, and how TE Connectivity delivers cabled backplane products that provide maximum flexibility and throughput with exceptional signal integrity.
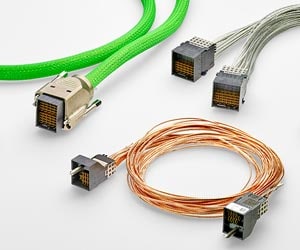
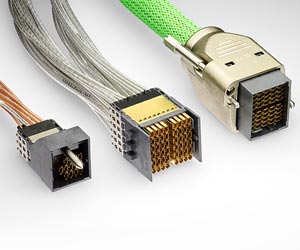
Cabled backplane technology has been in existence for more than 10 years. Recent migration from the 10 Gbps backplane ecosystem to the 25 Gbps and beyond backplane ecosystem is making cabled backplane technology a more attractive solution for today’s system architects. A cabled backplane can solve three issues: it increases performance, enables low-loss communications across long channels, and allows routing flexibility.
Higher Performance
Using high-speed cabled backplanes significantly improves electrical performance at 25 Gbps and beyond. Other than using fiber optic technology, the cabled approach is one of the few alternatives for larger computing and switching systems. Leading PCB fabrication suppliers have developed HDI (high density interconnect) structures to help mitigate trace routing challenges, but it takes 20-30 fabrication process steps to build these very high layer count backplanes, and they are 5-10 times more expensive than traditional PCB substrates.
Low-loss Communications
Loss budgets for an entire channel are becoming tighter so designers need to reduce the insertion loss as much as possible in the physical connection. PCBs have insertion loss associated with them. For example, typical Meg 6 PCBs have a loss of 0.75 dB/in at 12.5 GHz. In contrast, TE’s STRADA Whisper cabled backplane solutions have a loss of 0.11 dB/in. High-speed backplane cable allows designers to maintain insertion loss, return loss, skew, cross-talk and other signal integrity attributes within OEM performance specifications at 25 Gbps and above. The reduced insertion loss achieved by the high- speed cable also can allow signal integrity to be maintained at distances two to four times greater than a conventional PCB backplane design. This technology is critically important as it can enable data channels of three feet or more in full rack systems.
Routing Flexibility
With a cabled system, interconnect manufacturers have the design flexibility to offer the OEM a variety of system configurations. The backplane configuration with daughter cards mounted parallel to each other is one popular approach. In addition, a midplane/orthogonal configuration mounts cards in a 90-degree orientation. Cabling in this manner typically connects the cards in the midplane space, allowing for more efficient thermal management. Improvements in electrical performance and signal integrity are enhanced using cable in these various configurations.
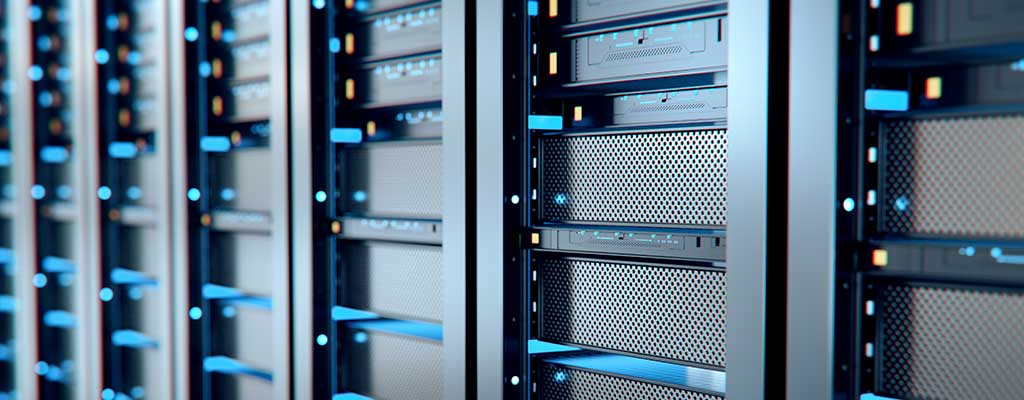
Cabled Backplane Challenges
Despite these advantages, there are potential challenges to using cabled backplane technology. The first is the sheer number of connections that may be required. Larger communications systems typically require the cabled approach because of the greater data lengths involving a larger number of daughter cards, switch cards and so on. Each card will typically connect to all other cards in the system, resulting in many point-to-point connections. Each connection requires a twinax cable with a differential pair configuration, so many mating cabled headers and receptacles may be necessary along the edge of a daughter card.
Using cabled backplanes also requires the use of complicated pin mapping schemes to understand how each of the cables is routed from board to board. This requires close collaboration between the OEM and the interconnect solution manufacturer. With the possibility of thousands of point-to-point connections required in some systems, it is easy to imagine the complexity of the cable routing. Cable routing can sometimes require challenging wire management involving multiple wire lengths and bends, and this could impact electrical and mechanical performance. Performance integrity before and after product verification testing must be ensured at the cable assembly level as well as the system level.
Another challenge is the considerable amount of cable required. Some systems could include thousands of differential pair channels, so it’s possible that thousands of feet of twinax cable would be a requirement. All that cable adds weight to a system when compared to a conventional backplane solution. This becomes a concern not only in packaging and transportation but is an important consideration in shock and vibration and other validation testing. Damage to these systems can be difficult to detect, especially after shipment from the manufacturer. Repair after installation can be one of the most challenging aspects of the cabled backplane system.
Additionally, it is important to maintain termination of the cable to the connector while still maintaining an appropriate characteristic impedance (typically 85-100 ohms) in order to ensure signal integrity at 25 Gbps speeds and higher. Wire termination techniques commonly used are welding (laser, ultrasonic, or resistance welding) or soldering. Manufacturing processes must be precise and monitored continuously to maintain quality and performance objectives.
Generally, the major challenge in deciding whether to use a cabled backplane comes down to cost. If a PCB will meet the channel budget, then typically cabled backplane is not necessary. However, if architecture flexibility is the main driver in the system design, then cabled backplane can be the best option available. Developing system sizes and channel lengths are allowing cabled backplane to become cost-competitive in the market.
Why Partner with TE
The demand for a cabled backplane will only increase as equipment data rates go from 25 Gbps NRZ and 56 Gbps PAM-4 to 56 Gbps NRZ and 112 Gbps PAM-4. New signal integrity requirements will likely make cabled backplane a necessity in large systems for the core networking and high-performance computing markets in particular. As PCBs become cost-prohibitive at higher data rates, TE’s cabled STRADA Whisper connectors provide a flexible solution.
TE’s STRADA Whisper connector has extremely low cable insertion loss (0.11 dB/in versus PCB loss of 0.75 dB/in at 12.5 GHz) which allows signal integrity to be maintained at distances 2-4 times greater than a conventional PCB backplane design. Reduced insertion loss achieved by the high-speed cable improves the channel margin and allows for more creative system architecture design possibilities
Cabled STRADA Whisper connectors continue to offer the same mechanical robustness and best-in-class electrical and signal integrity performance of TE’s STRADA Whisper product family. They can support 25-56 Gbps PAM-4, with future expansion to 56 Gbps NRZ and 112 Gbps PAM-4.
TE is the right design partner to help mitigate the challenges associated with cabled backplane architecture. When it comes to the complexity of pair mapping, TE’s engineering expertise can help design the most optimal assignments, and TE’s extensive testing assures the assembly is just as reliable as a PCB fabrication supplier. TE has molding, prototyping and development methods to mount, load, form and route cables to accommodate most system sizes or routing needs. Multiple solutions to any single problem can be presented to define the best custom architecture for any customer need. Our manufacturing process includes extensive electrical and visual quality checks with extremely tight tolerances which drive precision to deliver the best possible quality product.
TE offers three main solutions of cabled STRADA Whisper connectors: point-to-point cable, value-add assemblies, and a full backplane/ midplane design. TE’s use of its own MADISON CABLE product, with in-house design coupled with advanced cable engineering capabilities, allows TE to keep the cost of its cabled STRADA Whisper product as low as possible.
The march toward higher data rates in communications equipment is continuing to grow. Conventional PCB connectivity has signal integrity limitations at speeds of 25 Gbps and higher, requiring the use of more expensive substrates that can add significantly to the overall cost of a system. Cabled interconnects from TE help address signal integrity performance and promote design flexibility, taking next-generation systems solidly into the future of 56 Gbps NRZ and 112 Gbps PAM-4 capability.
TE Connectivity (TE) delivers cabled backplane products that provide maximum flexibility and throughput with exceptional signal integrity.
As data center equipment speeds continue to increase, traditional FR4 printed circuit board (PCB) substrates may no longer provide acceptable transmission performance, especially at 25 Gbps and beyond. Core switches and routers need maximum throughput with superior signal integrity, and as these systems achieve greater computational power, the backplanes and the number of daughter cards they support become greater in size, number, and complexity. Many equipment manufacturers are looking for connectivity alternatives to PCB substrates, and high-speed cabled backplane technology has emerged as a primary option. In this paper, we will examine the need for high-speed cabled backplane connectivity, its advantages over PCB-based alternatives, its potential drawbacks, and how TE Connectivity delivers cabled backplane products that provide maximum flexibility and throughput with exceptional signal integrity.
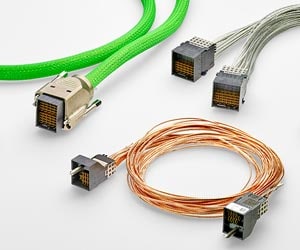
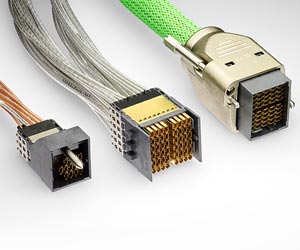
Cabled backplane technology has been in existence for more than 10 years. Recent migration from the 10 Gbps backplane ecosystem to the 25 Gbps and beyond backplane ecosystem is making cabled backplane technology a more attractive solution for today’s system architects. A cabled backplane can solve three issues: it increases performance, enables low-loss communications across long channels, and allows routing flexibility.
Higher Performance
Using high-speed cabled backplanes significantly improves electrical performance at 25 Gbps and beyond. Other than using fiber optic technology, the cabled approach is one of the few alternatives for larger computing and switching systems. Leading PCB fabrication suppliers have developed HDI (high density interconnect) structures to help mitigate trace routing challenges, but it takes 20-30 fabrication process steps to build these very high layer count backplanes, and they are 5-10 times more expensive than traditional PCB substrates.
Low-loss Communications
Loss budgets for an entire channel are becoming tighter so designers need to reduce the insertion loss as much as possible in the physical connection. PCBs have insertion loss associated with them. For example, typical Meg 6 PCBs have a loss of 0.75 dB/in at 12.5 GHz. In contrast, TE’s STRADA Whisper cabled backplane solutions have a loss of 0.11 dB/in. High-speed backplane cable allows designers to maintain insertion loss, return loss, skew, cross-talk and other signal integrity attributes within OEM performance specifications at 25 Gbps and above. The reduced insertion loss achieved by the high- speed cable also can allow signal integrity to be maintained at distances two to four times greater than a conventional PCB backplane design. This technology is critically important as it can enable data channels of three feet or more in full rack systems.
Routing Flexibility
With a cabled system, interconnect manufacturers have the design flexibility to offer the OEM a variety of system configurations. The backplane configuration with daughter cards mounted parallel to each other is one popular approach. In addition, a midplane/orthogonal configuration mounts cards in a 90-degree orientation. Cabling in this manner typically connects the cards in the midplane space, allowing for more efficient thermal management. Improvements in electrical performance and signal integrity are enhanced using cable in these various configurations.
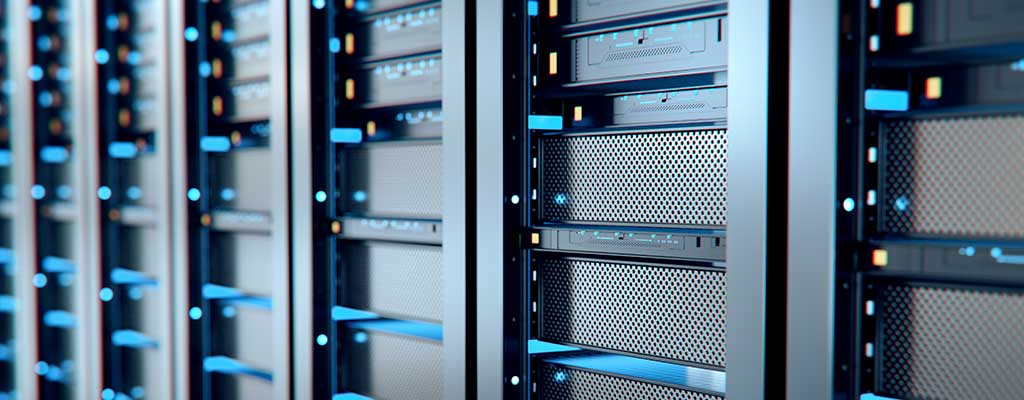
Cabled Backplane Challenges
Despite these advantages, there are potential challenges to using cabled backplane technology. The first is the sheer number of connections that may be required. Larger communications systems typically require the cabled approach because of the greater data lengths involving a larger number of daughter cards, switch cards and so on. Each card will typically connect to all other cards in the system, resulting in many point-to-point connections. Each connection requires a twinax cable with a differential pair configuration, so many mating cabled headers and receptacles may be necessary along the edge of a daughter card.
Using cabled backplanes also requires the use of complicated pin mapping schemes to understand how each of the cables is routed from board to board. This requires close collaboration between the OEM and the interconnect solution manufacturer. With the possibility of thousands of point-to-point connections required in some systems, it is easy to imagine the complexity of the cable routing. Cable routing can sometimes require challenging wire management involving multiple wire lengths and bends, and this could impact electrical and mechanical performance. Performance integrity before and after product verification testing must be ensured at the cable assembly level as well as the system level.
Another challenge is the considerable amount of cable required. Some systems could include thousands of differential pair channels, so it’s possible that thousands of feet of twinax cable would be a requirement. All that cable adds weight to a system when compared to a conventional backplane solution. This becomes a concern not only in packaging and transportation but is an important consideration in shock and vibration and other validation testing. Damage to these systems can be difficult to detect, especially after shipment from the manufacturer. Repair after installation can be one of the most challenging aspects of the cabled backplane system.
Additionally, it is important to maintain termination of the cable to the connector while still maintaining an appropriate characteristic impedance (typically 85-100 ohms) in order to ensure signal integrity at 25 Gbps speeds and higher. Wire termination techniques commonly used are welding (laser, ultrasonic, or resistance welding) or soldering. Manufacturing processes must be precise and monitored continuously to maintain quality and performance objectives.
Generally, the major challenge in deciding whether to use a cabled backplane comes down to cost. If a PCB will meet the channel budget, then typically cabled backplane is not necessary. However, if architecture flexibility is the main driver in the system design, then cabled backplane can be the best option available. Developing system sizes and channel lengths are allowing cabled backplane to become cost-competitive in the market.
Why Partner with TE
The demand for a cabled backplane will only increase as equipment data rates go from 25 Gbps NRZ and 56 Gbps PAM-4 to 56 Gbps NRZ and 112 Gbps PAM-4. New signal integrity requirements will likely make cabled backplane a necessity in large systems for the core networking and high-performance computing markets in particular. As PCBs become cost-prohibitive at higher data rates, TE’s cabled STRADA Whisper connectors provide a flexible solution.
TE’s STRADA Whisper connector has extremely low cable insertion loss (0.11 dB/in versus PCB loss of 0.75 dB/in at 12.5 GHz) which allows signal integrity to be maintained at distances 2-4 times greater than a conventional PCB backplane design. Reduced insertion loss achieved by the high-speed cable improves the channel margin and allows for more creative system architecture design possibilities
Cabled STRADA Whisper connectors continue to offer the same mechanical robustness and best-in-class electrical and signal integrity performance of TE’s STRADA Whisper product family. They can support 25-56 Gbps PAM-4, with future expansion to 56 Gbps NRZ and 112 Gbps PAM-4.
TE is the right design partner to help mitigate the challenges associated with cabled backplane architecture. When it comes to the complexity of pair mapping, TE’s engineering expertise can help design the most optimal assignments, and TE’s extensive testing assures the assembly is just as reliable as a PCB fabrication supplier. TE has molding, prototyping and development methods to mount, load, form and route cables to accommodate most system sizes or routing needs. Multiple solutions to any single problem can be presented to define the best custom architecture for any customer need. Our manufacturing process includes extensive electrical and visual quality checks with extremely tight tolerances which drive precision to deliver the best possible quality product.
TE offers three main solutions of cabled STRADA Whisper connectors: point-to-point cable, value-add assemblies, and a full backplane/ midplane design. TE’s use of its own MADISON CABLE product, with in-house design coupled with advanced cable engineering capabilities, allows TE to keep the cost of its cabled STRADA Whisper product as low as possible.
The march toward higher data rates in communications equipment is continuing to grow. Conventional PCB connectivity has signal integrity limitations at speeds of 25 Gbps and higher, requiring the use of more expensive substrates that can add significantly to the overall cost of a system. Cabled interconnects from TE help address signal integrity performance and promote design flexibility, taking next-generation systems solidly into the future of 56 Gbps NRZ and 112 Gbps PAM-4 capability.