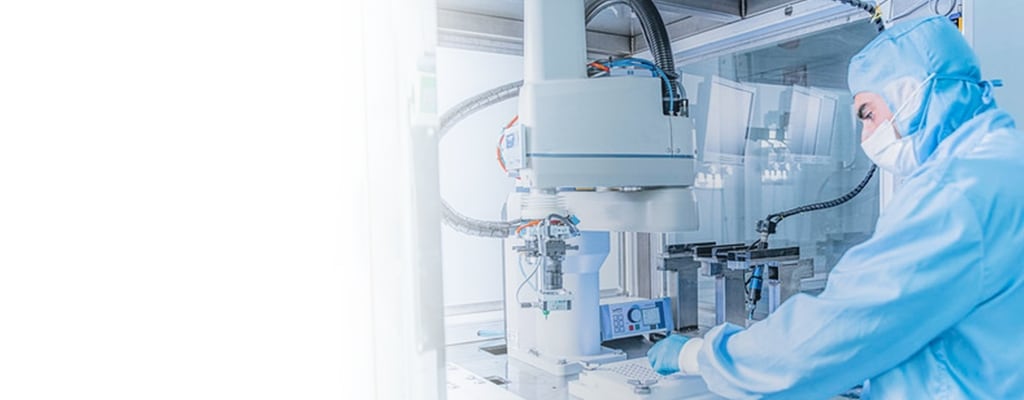
Microfluidic Manufacturing Process Development and Automation
Improving consistency, reliability and lowering microfluidic device production costs through the development of state-of-the-art and emerging micro and nano manufacturing processes.
Most Not all IVD and Life Science devices progress from small to large can be moved into full-scale volume production immediately as market demand dictates. Sometimes the need to scale is immediate, more often it happens in stages. By developing the processes of manufacturing and assembly in tandem with the device itself, TE can help ensure a smooth transition to mass manufacturing at the end of the development lifecycle.
Further TE has expertise in the deployment development of scalable materials, reagents, and processes required to establish new manufacturing production lines. Automated processes can boost efficiency via the inclusion n
of maintenance plan, more traceable electronic documentation, and calibration steps.
When conventional production processes fail to enable manufacturing of your microfluidic device, trust TE Connectivity to provide custom process development and automation for the manufacturing processes of your device.
Transitioning From R&D to Mass Manufacturing
There’s no assurance that a beta prototyped device, resulting from a NPD (New Product Development) phase, will smoothly transition to scaled-up production. Further optimization development and considerations for reagent formulations, fit-for-use materials, regulatoryvalidation requirements, and supply chain security are required to fulfil the scale-up process phase for IVD and Life Science devices. TE works to optimizewell define these parameters and lead your product to a successful production line launch, supply chain management, and QMS.
Core Capabilities:
- Mechatronics and Aautomation Ddesign
- Ultra-Clean Washing of Plastic Components
- Photolithography Technologies (Class 10-100)
- Complex Multi-Plane and Radial Laser Welding
- Radial Laser Welding
- Thin Film Processing: Sputtering, Oxidation Furnaces, etc.
- Blister Filling Techniques
- Plasma dry Eetching:RIE and DRIE
- Microreplication: Hot Embossing, Casting, Micro Milling
- Micro Injection Molding
- Surface Functionalization
- Automated UV Placement
- Track-Etched Membrane Placement and Support
- Membrane Spotting
- Reagent Placement on Device
- Automated Reagent Deposition/Integration
- Bonding Technologies (Solvent, Wire, Ultrasonic, Anodic, Fusion and Adhesive Bonding)
- VOC Evacuation During Bonding
- High Tthroughput Lamination Equipment (Adhesive and Thermal)
- Requirements & Specifications Development
- Concept Development & Evaluation
- Pilot Production Assembly
- DNA / RNA Mitigated Production Facility
- Automated quality control systems
Benefits of Process Automation
Integrating automation into the IVD manufacturing process leads to a wide array of benefits for the IVD device designer and manufacturer. Automation allows for the inclusion of software-based calculation, calibration, and documentation, which in turn leads to improvements in test efficiency, calibration scheduling, regulatory compliance, and instrument/equipment traceability. These benefits lead to less labor, a reducedlower risk of errors (standardization), and fewer calibration tests. Furthermore, automated volumetric measurements simplify production fabrication processes by providing manufacturers with better control over manufacturing equipment and stepsthe production line.