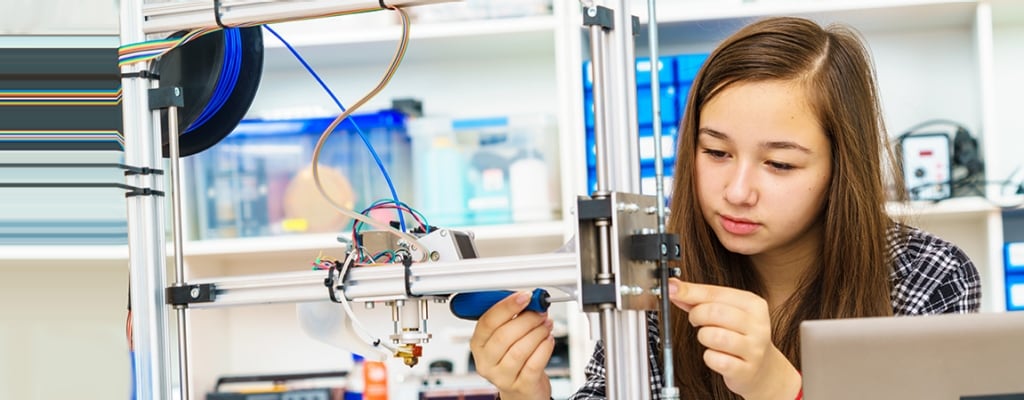
Putting Printers in Plants – Across TE
Recent advancements in 3D-printing materials and hardware are transforming how manufacturers operate and engineers think. As one of the world’s first adopters of 3D printing, we are using this technology to drive cost savings, cut time-to-market, and develop products more efficiently.
Authors:
Mark Savage, Principal Development Engineer, Additive Manufacturing
Robert F. Zubrickie, Manufacturing Engineer, 3D Printing & Prototyping Center
Worldwide, most electronic components are manufactured using traditional processes, typically injection molding, stamping, and plating. While today’s production machinery can perform this labor-intensive process more efficiently than in decades past, the technology lacks the capacity to easily and cost-effectively produce complex forms quickly.
To gain this kind of capacity, particularly when making small quantities of parts, manufacturers – including TE – are experimenting with alternative production approaches such as 3D printing, a technology with the potential to economically produce the complex end-use components required in today’s increasingly smaller, lighter, and integrated electronics.
Also known as additive manufacturing (AM), 3D printing enables manufacturers to add only what is needed – layer by layer, in exact and intricate shapes, with reinforcements built into the design to support the geometry. Although 3D printing has been around for more than 30 years, only over the last decade has its development accelerated.
While there are times when 3D printing is not the best choice, such as when the geometry is simplistic and the design can be machined simply, 3D printing is effective when making prototypes – of connectors, with contacts, as the housing, and even the entire fixture and the cable assembly connected to it.
The result is a lighter, potentially stronger product, made faster, with less waste, with components for complex geometries.
At TE, we introduced 3D printing back in 1987, through AMP, one of our predecessor companies. At the time, we were one of six companies worldwide to test and use this technology in a production environment. Initiated by TE employee and 3D-printing advocate Robert (Bob) Zubrickie, a mechanic by nature who joined AMP in 1979 and now runs TE’s Pennsylvania-based 3D Printing and Prototyping Center, our adoption of 3D printing began with running stereolithography machines (also known as SLA or SL) in two locations – our plants in Harrisburg, Pennsylvania and Charlotte, North Carolina.
At the time, we were using SLA to quickly fabricate prototypes of products, such as connectors. These early designs were made using liquid resin, which enabled us to produce – layer-by-layer – parts with very fine detail. With SLA, we could turn customer drawings into fully functional product, giving customers a three-dimensional object to hold in their hands, so they could see all their intended complex geometries. Though this was an immediate hit with customers, early 3D printing had a crucial drawback: The materials then available could only produce very brittle prototypes. Models broke very easily, and the brittleness often failed to demonstrate a design’s functionality.
Although innovation in 3D-printing technology slowed between the late-1980s and the mid-1990s, our team remained focused on finding a use that gave us a competitive advantage. During this time, as early practitioners gathered for the first international AM symposium, we investigated the opportunities and invested internally in getting to know the machines and the materials. Our efforts quickly established TE as one of a handful of companies thinking strategically about the potential uses of 3D printing in a manufacturing environment. Over the years, through Bob’s team, we experimented with using SLA to make it an easier-to-use technology, introduced our engineers to 3D-printing machines, and worked closely with resin manufacturers to test new materials. This work enabled us to iterate quickly.
Today, our 3D Printing and Prototyping Center in Pennsylvania operates seven different technologies and uses thirty types of materials. In 2017, the center fulfilled more than 700 work orders – with an average turnaround of three days – submitted through our new online work order system: This amounted to several million US dollars in cost savings – over only six months – on production and prototyping projects. Today, we are finding ways to fabricate quality, functional prototypes of electronic components right out of an SLA machine.
From our success and continued investments in 3D-printing technology, a solid practice has evolved from what was once a small group of passionate 3D-printing experts operating in a single location into what today is a quickly expanding global network of engineers and technologists working in an array of industries, embracing AM and looking to apply 3D-printing technology. Our effectiveness in integrating AM across TE is the result of the many employees who participate in our Additive Manufacturing CoE.
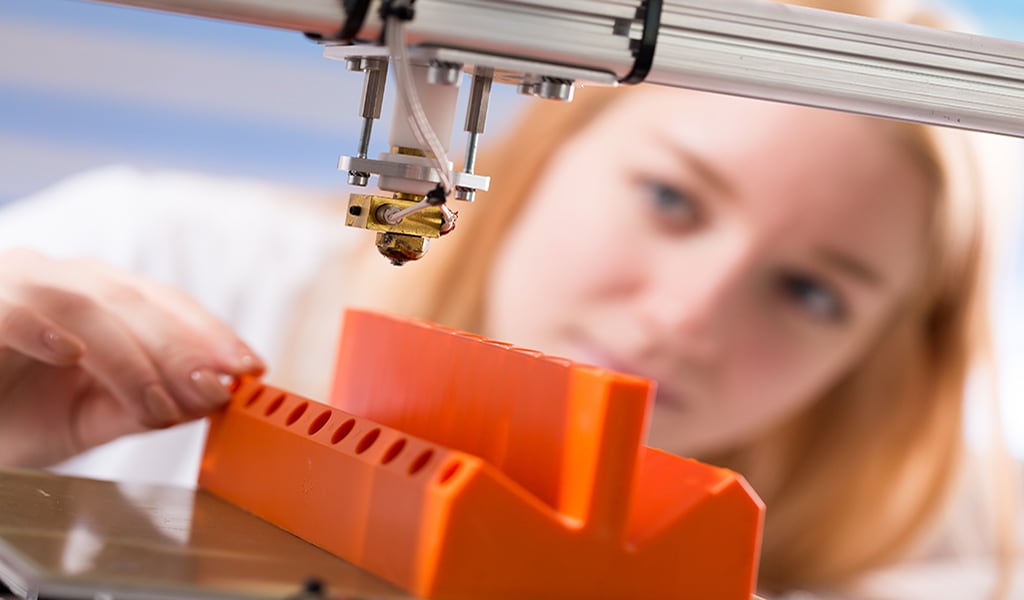
At TE, we have invested in a comprehensive portfolio of 3D-printing technologies. This includes Fused Deposition Modeling (FDM) machines for printing with engineering polymers, and Jetting and SLS machines that use photopolymers. We also have Direct Metal Laser Sintering (DMLS) machines for metals printing as well as Digital Light Processing (DLP) printers using photopolymers with strengths analogous to engineering polymers.
Through the CoE, we share best practices and help production teams understand how 3D-printing can help them more efficiently reduce material waste and manufacturing costs. For example, our teams are now 3D printing low-volumes of grippers and jigs, allowing us to produce tooling cheaper in-house than to invest in costly retooling of production machinery. And recently, our AM CoE launched a 3D-printer loan program that is helping us put this technology into our plants worldwide.
Through this program, any TE plant can borrow a 3D-printer to test and run at the site. This exposure helps our production teams learn about 3D-printing technology first-hand and enables them to use the 3D printers as a cost-saving and time-saving tool for their daily work. The program is helping us expand our use of 3D-printing technology in our USA, Asian, and European locations.
From this, they are learning how to choose the 3D-printer best suited to their job and how to avoid many of the problems commonly experienced in running 3D-printers that lead to avoidable shutdowns.
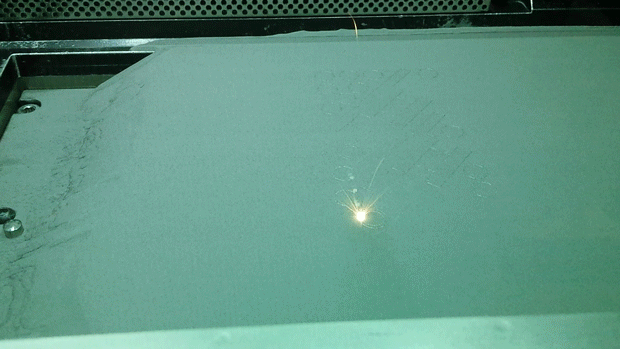
Committed to Investing in Innovation
Today, thirty years after 3D printing first captured the attention of manufacturers, the technology is still only in its preliminary stages. We are close to a time when 3D printing will enable manufacturers to achieve new efficiencies across the production environment. The tipping point will come as more engineers and manufacturers embrace a 3D printing-first approach. At TE, our continued investments in 3D-printing technology are strengthening our capacity to think big and move fast in ways that can help our customers achieve crucial advantages to win in their markets – today and tomorrow.