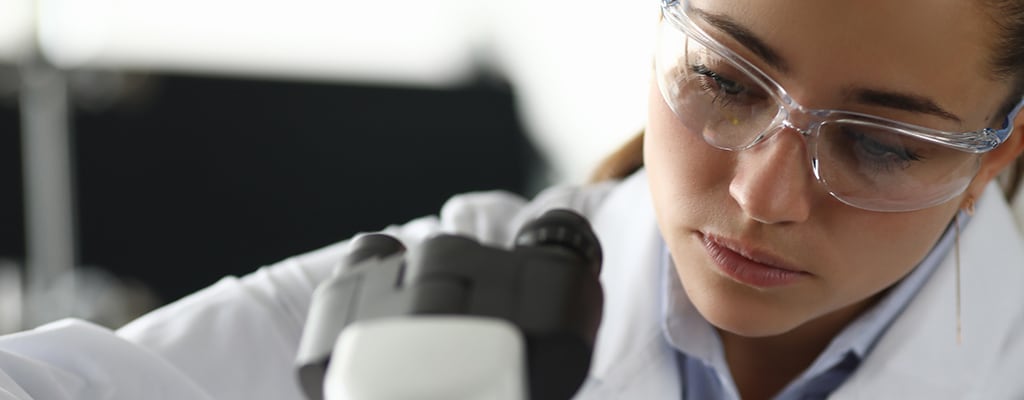
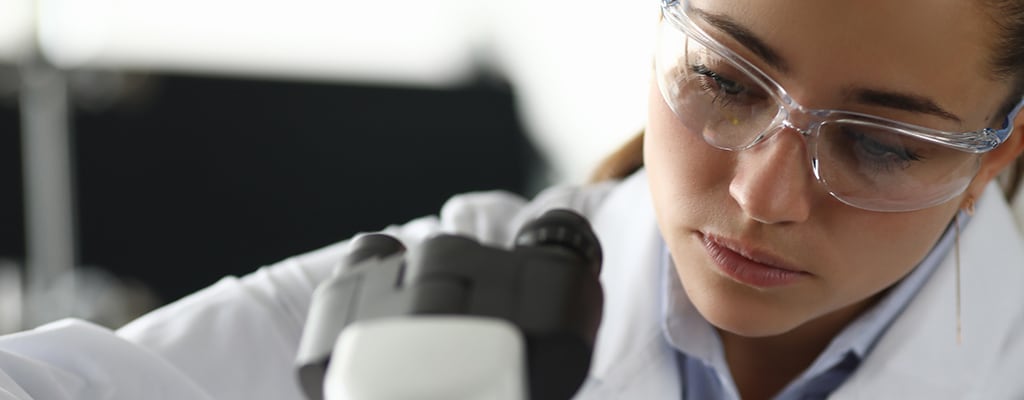
Most conventional polymers...are created from non-renewable petroleum in...[an] energy intensive process...Biomass polymers are derived from recurring plants like forms of sugar or castor oils. We're at the beginning of the biomass journey.
January 23, 2023
The technologies we rely are increasingly manufactured with complex often groundbreaking material compositions that enable engineers to develop innovative solutions to current connectivity concerns. These materials typically possess superior properties to optimize the performance and production of a wide range of applications. As noted by Phil Gilchrist, TE's vice president and chief transformation officer for artificial intelligence and sustainable materials, advanced materials are helping address three technology innovation concerns: the increased expectation of mass customization; alternative design solutions; and processes for testing and validating new materials.
“The world is embracing advanced materials to leave the world way better than we met them,” explains Phil. Today’s biomaterials can be either natural or synthetic and composed of numerous substances, including metals, ceramics, and polymers. Some examples of biomaterials include titanium and stainless steel, which are commonly used in joint replacements. Another is polyethylene, which is used in artificial heart valves.
The creation of new materials is helping to address the increased expectation for mass customization and rapid on-demand production, Gilchrist explained. This is true in the field of biomaterials, where new materials can be designed with specific properties, such as biocompatibility, that make them well suited for a wide range of medical applications. These new materials can be produced quickly and sometimes at a lower cost than traditional materials, enabling engineers to use these in a wider range of customer solutions.
Read – and listen to – an interview with Phil Gilchrist.
What is driving the need to develop advanced materials, such as bactericidal surfaces and biomass derived ingredients such as bioplastic monomers from shrilk?
Well the truth is, we live in a material world. The amount of material that's been consumed by humanity has surpassed 100 billion tons a year. Think about this. Everything that we use in the world is made of something. At TE alone, last year we made something like 147 billion things, representing some 300,000 product lines and all of that's made of material. In fact, I recently read that overall employment of chemists and material scientists is projected to grow by 6% from 21 % to 31%. So material science might just be one of the most important technology of the next decade. There are several factors driving this change. Some are driven by our customers, some are driven by new technical capabilities, and some are driven by new science and the increasing ability of the engineer; our increasing ability to engineer very small things. So let me talk about some of those drivers.
From the customer side, I think the drivers include the need for sustainable materials, materials that have less weight, materials that have higher performance characteristics within a smaller physical space, materials that need to operate in extreme temperatures and harsh environments, materials that need to isolate electrical signals flowing through a physical architectures. There's been an exponential growth in our knowledge of material design, all the way down to the nano and quantum levels. I think the ability to see and manipulate atomic structures of exotic materials like shrilk, which for the audience is a fully degradable bioplastic made from a material called chitosan, which is found in shrimp cells.
AI is a new design aid that helps material scientists find the right permutations of a polymer. It used to be that developing new materials was a painful process of trial and error, as the right permutation of chemistry that met the requirements was “discovered." In the pre-AI days, this meant hundreds of physical formula variants being tweaked and tested. And that could take literally years. AI allows the whole discovery process, the search for the most promising candidate formulations, to be searched for in the digital space. That’s just much faster. In the end, you still need to physically make and test them, of course, but you need to test fewer of them, and the few that you test are more likely to be right. Practically speaking, this could reduce the development time dramatically, by as much as 50%. That's another way of saying you can double your material development capacity by 100%. And that results in a suddenly expansion in the world's capacity for new formulas.
Is sustainability an important concern when developing new materials, and if so, why?
Sustainability is something the whole world is embracing with all the kind of zeal and passion of a kind of new convert. Our customers are beginning to demand products that support a fully sustainable product life cycle. And we do too. At TE Connectivity, we have a consistent and I think, transparent record of the environmental and social reporting. And you can read that online in one of our corporate responsibility reports. Everyone at TE lives in the world, too. We have kids, we have grandkids, and we have a desire to leave the world in a better shape than we found it. We make millions of things a year that the world needs and will continue to need, and that does create greenhouse gases in the process of making them. But we believe in a world where those things can be made sustainably. The world regulatory bodies are also beginning to play a big role in driving sustainable alternatives, driven by the public demanding a more sustainable world. I think it's fair to say that Europe is driving a very focused, some would say aggressive, environmental regulation policy that's beginning to propagate throughout the world, and that will force other regions to eventually adapt.
I think about the future like this. Traditionally, product design has been about finding an optimal solution between three fundamental constraints: performance, manufacturability, and cost. To those three fundamental constraints, at TE, we're adding a fourth one - sustainability. New fundamental design constraints don't happen that often. So that's a big deal.
How different is the function of the mechano bactericidal surfaces? How do these differ from conventional materials?
Well, in conventional products, surface material is really the same material as one nanometer or 1mm or 1m below the surface. The material operates the same if you have a gram or a kilogram of it. Products with antibacterial surfaces or surfaces that change color based on some stimulus, like a gas or excessive heat, are examples of new biomaterials where the surface or materials has an active chemical design that can be programmed to do different things from the bulk of the material based on some stimulus. And that's an extremely interesting development and offers a new design dimension to exploit.
For example, you can imagine antibacterial plastic tubing around your shopping cart handles that continually sanitizes the handling surfaces, or high-speed data cables that crack or heal from some scratch or whatever filling in the gaps themselves when certain catalysts are exposed to the air. Truly, the opportunities, I think, are endless. I like to say that nature, evolution, discovered patent portfolio, with countless applications of smart surfaces and smart materials. To a very large extent, we just need to discover what nature’s already found and adapt and adopt it.
What advantages can be gained from using bio mass polymers over other materials?
Most conventional polymers used in this world are created from non-renewable petroleum in a very high temperature, and by that, I mean energy intensive process. Petroleum is, as we know, non-renewable. Biomass polymers are derived from recurring plants like forms of sugar or castor oils. We're at the beginning of the biomass journey. The feedstock these polymers are made from represents about 1% of the global plastics market. It is gaining in popularity, but it's still quite marginal. And it's fair to say that there are significant challenges and disadvantages. A couple of these are cost and the danger of competing with the food chain. So we want to source biomass feedstock that humans don't compete for.
Will these new materials eventually replace the tried and true?
Over time, yes. The validity and the legitimate use of these alternative materials will be proven. That will take a number of years. But there's no real reason that various applications or market spaces would not adopt these. In fact, if we could verify and qualify these products, given their environmental and sustainable benefits, we don't see any issue of the industry rejecting that.
Can these new materials help enable mass customization and rapid on-demand production?
This is a great question and really shows the scope of the the change afoot in the materials space. Leaving aside the drivers I just mentioned, my passion is all of the above. There's even more to talk about because fundamental material change is beginning to happen that will enable new ways to manufacture.
For example, we've been melting plastic resin beads into a high temperature liquid form, injecting them at a high pressure into steel molds, and converting that liquid back to some form of solid for decades. And you can see that from everything from Legos to connectors to car bodies, injection molding has dominated the manufacturing of plastic parts. And that's changing. 3D printing, the ability to build up complex parts by depositing a very thin layer of plastic on another layer of thin plastic, is not new to the world. And I guess we've all seen different examples of it. And you can buy home 3D printers for hundreds of dollars these days. But until recently, 3D printing didn't have the capabilities of injection molded materials for industrial products like ours. Characteristics are things like electrical isolation or resistance to fire, among other things. But the industrial printable materials Rubicon really has been crossed, and there are new materials becoming available that have the industrial strength that we require. These materials are being designed for 3D printing, manufacturing, and they will perform equivalently or even better than traditional injection molded parts.
Why should our customers care? Well, three immediate reasons: speed, speed, and speed. This is the first critical value proposition we need to grasp. The difference is that 3D printed parts can be printed within one hour of the design being completed, whereas in an injection molded part we need to make the steel mold and that takes 2 to 3 months. It's expensive and requires a lot of iterations to get it right. So speed is the game changer. The second critical value proposition is the ability to make new designs that really replicate nature’s use of curves and voids, instead of a highly geometric, industrial, right-angled components we're all used to seeing. And there are no right angles in nature. Again, nature has the patent portfolio and we just need to discover it. In my view, the new industrial design language will allow us to make different, stunning, things. Think about this by analogy. Think about the skyline of a medieval European town against that of modern London, or Tokyo, or New York, or Shanghai, or Bangalore. The material capabilities really expand one's design capability and they change what can be built and imagined. And I think that's revolutionary.
What must engineers consider when using a new material, particularly when developing complex technological architectures?
So fundamentally, an engineer needs to understand what the design constraints are for any product and any application. In data center applications, they require high data performance, operating at 100 Gbps to 200 Gbps. That creates a lot of heat and electrical interference, and the material needs to handle that and an ever-shrinking physical space. All of those things have to be addressed simultaneously. This application space, among others, like automotive and in defense, is why we've launched the performance materials BU to focus on the components like O-rings or gaskets in general. These products may seem modest, but they are heavily impacted by the capabilities of material and mission-critical components. If they fail, the whole system fails. And that may seem hyperbolic, but just remember that in 1986, the Space Challenger shuttle blew up because of a Floridian frost and the material properties of an O-ring in the right rocket booster. Data centers are, of course, less explosive venues, but a failure in these critical components could lead to heat flows to be mismanaged. And that causes the electronics to fail.
What advantages might manufacturers gain?
The bigger one is to create greater sustainability in terms of lower greenhouse gases. This will dominate all of that 100 billion tons I referred to earlier. Faster design to product when we're thinking of 3D printing and solving application problems better, reducing weight and space, thermal management, electrical management.
What must manufacturers address before using a new material?
We need to design and thoroughly validate these materials. And that takes a lot of time. They need to perform as required and they need to be manufacturable, and they need to be at the right cost. So that's a long process of maybe a year or two to get through the internal qualification of that product.
Is it feasible for manufacturers to use new materials in production?
Very realistic. We do it all the time. We introduce new materials often. And to give you some benchmark, currently TE uses about 4,000 different types of polymers. Again, it all comes back to good material science. I think we excel at that and good engineering practices. Customers trust our engineering. Those 247 billion things that we make a year I think testify to that.
What are the limits of materials innovation?
I don't think there's much limit. Our scientific and engineering knowledge and capabilities are expanding dramatically. I'm very optimistic that we can push the innovation curve as far as it needs to go.
What is being done to find new uses for the new materials?
Well at TE, we're one of the only companies that in our space that I'm aware of that has a dedicated team of material science scientists and experts. We're investing in material sciences as a core strength of our company. These teams have aggressive goals that are focused on new polymer design that create some form of competitive edge, whichever market application that we're talking about or addressing. We're also investing in the AI systems and databases that will improve our productivity, as I mentioned earlier.
What must be addressed to ensure new materials can meet requirements without compromising performance?
Our new Performance Materials BU team is focused on finding the right composition of polymers and fillers. The balance of polymer ingredients determines how it performs. So, given that there are so many permutations of a polymer formula, more permutations than there are atoms in the universe. In fact, the team's experience is invaluable in figuring out what that right balance is. At the end of this process, any new material would be fully validated and any product that comes from it would be fully validated.
What distinguishes TE’s approach to partnering with OEMs when developing new materials for customized solutions?
I would answer that is to say our level of investment in materials science, which is really an investment in very smart PhDs and also non PhD scientists. As I've said, as far as I'm aware, we're the only company in our space with a dedicated materials team. This team works with the BU teams that have the detailed application knowledge necessary to ensure that the right problems are being focused on. We are actively embracing AI as a tool to augment the number of polymers that can be developed, and the increasing speed connected with that is in one of our competitive advantages. Launching a performance material BU as a place to expand has been very critical as well.
How do you see materials research evolving over the next 5 years?
I think there is so much value-based creativity being created in smart materials, so many advancements in our understanding of the underlying physics and biology and the engineering of materials. Just so much science is being invested in that I really do see a continued expansion and acceleration of the rate of change in materials. Couple all that with the fact that we really do live in a material world. So based on that, I think the future is very exciting. And if you're looking for an analog, it feels like materials are at that same inflection point similar to the Telecoms world of 25 years ago, as it transitioned from a wireline pay by-the-minute world to a mobile cellular world with free voice over internet. I think everything is going to change.
Did you enjoy this interview? Read the source article.
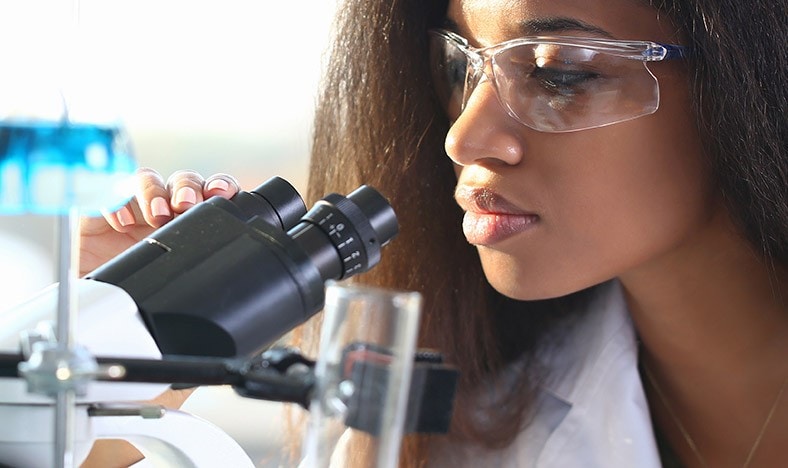
Innovation in materials engineering is enabling an evolution in product manufacturing. Companies that recognize this are developing processes to help them stand out from their competition.
Learn about the trends shaping materials development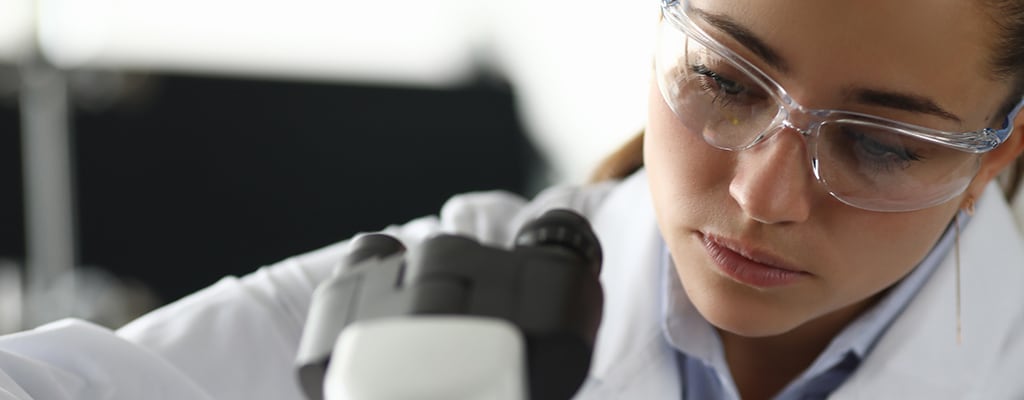
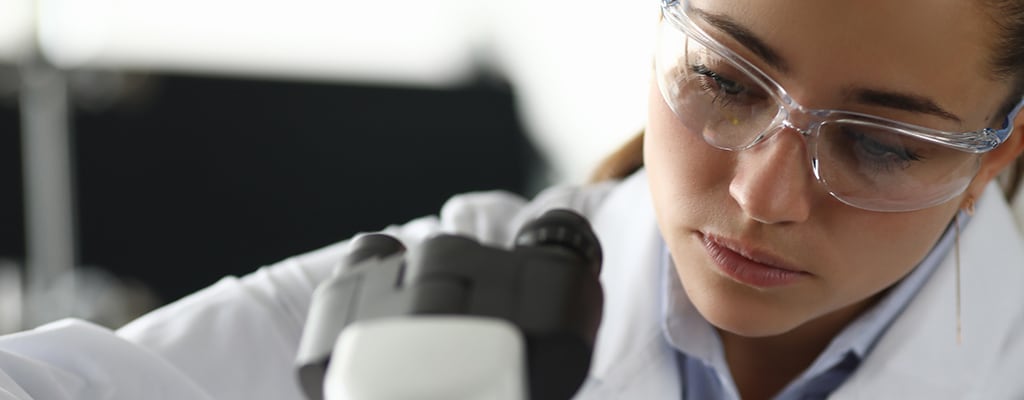
Most conventional polymers...are created from non-renewable petroleum in...[an] energy intensive process...Biomass polymers are derived from recurring plants like forms of sugar or castor oils. We're at the beginning of the biomass journey.
January 23, 2023
The technologies we rely are increasingly manufactured with complex often groundbreaking material compositions that enable engineers to develop innovative solutions to current connectivity concerns. These materials typically possess superior properties to optimize the performance and production of a wide range of applications. As noted by Phil Gilchrist, TE's vice president and chief transformation officer for artificial intelligence and sustainable materials, advanced materials are helping address three technology innovation concerns: the increased expectation of mass customization; alternative design solutions; and processes for testing and validating new materials.
“The world is embracing advanced materials to leave the world way better than we met them,” explains Phil. Today’s biomaterials can be either natural or synthetic and composed of numerous substances, including metals, ceramics, and polymers. Some examples of biomaterials include titanium and stainless steel, which are commonly used in joint replacements. Another is polyethylene, which is used in artificial heart valves.
The creation of new materials is helping to address the increased expectation for mass customization and rapid on-demand production, Gilchrist explained. This is true in the field of biomaterials, where new materials can be designed with specific properties, such as biocompatibility, that make them well suited for a wide range of medical applications. These new materials can be produced quickly and sometimes at a lower cost than traditional materials, enabling engineers to use these in a wider range of customer solutions.
Read – and listen to – an interview with Phil Gilchrist.
What is driving the need to develop advanced materials, such as bactericidal surfaces and biomass derived ingredients such as bioplastic monomers from shrilk?
Well the truth is, we live in a material world. The amount of material that's been consumed by humanity has surpassed 100 billion tons a year. Think about this. Everything that we use in the world is made of something. At TE alone, last year we made something like 147 billion things, representing some 300,000 product lines and all of that's made of material. In fact, I recently read that overall employment of chemists and material scientists is projected to grow by 6% from 21 % to 31%. So material science might just be one of the most important technology of the next decade. There are several factors driving this change. Some are driven by our customers, some are driven by new technical capabilities, and some are driven by new science and the increasing ability of the engineer; our increasing ability to engineer very small things. So let me talk about some of those drivers.
From the customer side, I think the drivers include the need for sustainable materials, materials that have less weight, materials that have higher performance characteristics within a smaller physical space, materials that need to operate in extreme temperatures and harsh environments, materials that need to isolate electrical signals flowing through a physical architectures. There's been an exponential growth in our knowledge of material design, all the way down to the nano and quantum levels. I think the ability to see and manipulate atomic structures of exotic materials like shrilk, which for the audience is a fully degradable bioplastic made from a material called chitosan, which is found in shrimp cells.
AI is a new design aid that helps material scientists find the right permutations of a polymer. It used to be that developing new materials was a painful process of trial and error, as the right permutation of chemistry that met the requirements was “discovered." In the pre-AI days, this meant hundreds of physical formula variants being tweaked and tested. And that could take literally years. AI allows the whole discovery process, the search for the most promising candidate formulations, to be searched for in the digital space. That’s just much faster. In the end, you still need to physically make and test them, of course, but you need to test fewer of them, and the few that you test are more likely to be right. Practically speaking, this could reduce the development time dramatically, by as much as 50%. That's another way of saying you can double your material development capacity by 100%. And that results in a suddenly expansion in the world's capacity for new formulas.
Is sustainability an important concern when developing new materials, and if so, why?
Sustainability is something the whole world is embracing with all the kind of zeal and passion of a kind of new convert. Our customers are beginning to demand products that support a fully sustainable product life cycle. And we do too. At TE Connectivity, we have a consistent and I think, transparent record of the environmental and social reporting. And you can read that online in one of our corporate responsibility reports. Everyone at TE lives in the world, too. We have kids, we have grandkids, and we have a desire to leave the world in a better shape than we found it. We make millions of things a year that the world needs and will continue to need, and that does create greenhouse gases in the process of making them. But we believe in a world where those things can be made sustainably. The world regulatory bodies are also beginning to play a big role in driving sustainable alternatives, driven by the public demanding a more sustainable world. I think it's fair to say that Europe is driving a very focused, some would say aggressive, environmental regulation policy that's beginning to propagate throughout the world, and that will force other regions to eventually adapt.
I think about the future like this. Traditionally, product design has been about finding an optimal solution between three fundamental constraints: performance, manufacturability, and cost. To those three fundamental constraints, at TE, we're adding a fourth one - sustainability. New fundamental design constraints don't happen that often. So that's a big deal.
How different is the function of the mechano bactericidal surfaces? How do these differ from conventional materials?
Well, in conventional products, surface material is really the same material as one nanometer or 1mm or 1m below the surface. The material operates the same if you have a gram or a kilogram of it. Products with antibacterial surfaces or surfaces that change color based on some stimulus, like a gas or excessive heat, are examples of new biomaterials where the surface or materials has an active chemical design that can be programmed to do different things from the bulk of the material based on some stimulus. And that's an extremely interesting development and offers a new design dimension to exploit.
For example, you can imagine antibacterial plastic tubing around your shopping cart handles that continually sanitizes the handling surfaces, or high-speed data cables that crack or heal from some scratch or whatever filling in the gaps themselves when certain catalysts are exposed to the air. Truly, the opportunities, I think, are endless. I like to say that nature, evolution, discovered patent portfolio, with countless applications of smart surfaces and smart materials. To a very large extent, we just need to discover what nature’s already found and adapt and adopt it.
What advantages can be gained from using bio mass polymers over other materials?
Most conventional polymers used in this world are created from non-renewable petroleum in a very high temperature, and by that, I mean energy intensive process. Petroleum is, as we know, non-renewable. Biomass polymers are derived from recurring plants like forms of sugar or castor oils. We're at the beginning of the biomass journey. The feedstock these polymers are made from represents about 1% of the global plastics market. It is gaining in popularity, but it's still quite marginal. And it's fair to say that there are significant challenges and disadvantages. A couple of these are cost and the danger of competing with the food chain. So we want to source biomass feedstock that humans don't compete for.
Will these new materials eventually replace the tried and true?
Over time, yes. The validity and the legitimate use of these alternative materials will be proven. That will take a number of years. But there's no real reason that various applications or market spaces would not adopt these. In fact, if we could verify and qualify these products, given their environmental and sustainable benefits, we don't see any issue of the industry rejecting that.
Can these new materials help enable mass customization and rapid on-demand production?
This is a great question and really shows the scope of the the change afoot in the materials space. Leaving aside the drivers I just mentioned, my passion is all of the above. There's even more to talk about because fundamental material change is beginning to happen that will enable new ways to manufacture.
For example, we've been melting plastic resin beads into a high temperature liquid form, injecting them at a high pressure into steel molds, and converting that liquid back to some form of solid for decades. And you can see that from everything from Legos to connectors to car bodies, injection molding has dominated the manufacturing of plastic parts. And that's changing. 3D printing, the ability to build up complex parts by depositing a very thin layer of plastic on another layer of thin plastic, is not new to the world. And I guess we've all seen different examples of it. And you can buy home 3D printers for hundreds of dollars these days. But until recently, 3D printing didn't have the capabilities of injection molded materials for industrial products like ours. Characteristics are things like electrical isolation or resistance to fire, among other things. But the industrial printable materials Rubicon really has been crossed, and there are new materials becoming available that have the industrial strength that we require. These materials are being designed for 3D printing, manufacturing, and they will perform equivalently or even better than traditional injection molded parts.
Why should our customers care? Well, three immediate reasons: speed, speed, and speed. This is the first critical value proposition we need to grasp. The difference is that 3D printed parts can be printed within one hour of the design being completed, whereas in an injection molded part we need to make the steel mold and that takes 2 to 3 months. It's expensive and requires a lot of iterations to get it right. So speed is the game changer. The second critical value proposition is the ability to make new designs that really replicate nature’s use of curves and voids, instead of a highly geometric, industrial, right-angled components we're all used to seeing. And there are no right angles in nature. Again, nature has the patent portfolio and we just need to discover it. In my view, the new industrial design language will allow us to make different, stunning, things. Think about this by analogy. Think about the skyline of a medieval European town against that of modern London, or Tokyo, or New York, or Shanghai, or Bangalore. The material capabilities really expand one's design capability and they change what can be built and imagined. And I think that's revolutionary.
What must engineers consider when using a new material, particularly when developing complex technological architectures?
So fundamentally, an engineer needs to understand what the design constraints are for any product and any application. In data center applications, they require high data performance, operating at 100 Gbps to 200 Gbps. That creates a lot of heat and electrical interference, and the material needs to handle that and an ever-shrinking physical space. All of those things have to be addressed simultaneously. This application space, among others, like automotive and in defense, is why we've launched the performance materials BU to focus on the components like O-rings or gaskets in general. These products may seem modest, but they are heavily impacted by the capabilities of material and mission-critical components. If they fail, the whole system fails. And that may seem hyperbolic, but just remember that in 1986, the Space Challenger shuttle blew up because of a Floridian frost and the material properties of an O-ring in the right rocket booster. Data centers are, of course, less explosive venues, but a failure in these critical components could lead to heat flows to be mismanaged. And that causes the electronics to fail.
What advantages might manufacturers gain?
The bigger one is to create greater sustainability in terms of lower greenhouse gases. This will dominate all of that 100 billion tons I referred to earlier. Faster design to product when we're thinking of 3D printing and solving application problems better, reducing weight and space, thermal management, electrical management.
What must manufacturers address before using a new material?
We need to design and thoroughly validate these materials. And that takes a lot of time. They need to perform as required and they need to be manufacturable, and they need to be at the right cost. So that's a long process of maybe a year or two to get through the internal qualification of that product.
Is it feasible for manufacturers to use new materials in production?
Very realistic. We do it all the time. We introduce new materials often. And to give you some benchmark, currently TE uses about 4,000 different types of polymers. Again, it all comes back to good material science. I think we excel at that and good engineering practices. Customers trust our engineering. Those 247 billion things that we make a year I think testify to that.
What are the limits of materials innovation?
I don't think there's much limit. Our scientific and engineering knowledge and capabilities are expanding dramatically. I'm very optimistic that we can push the innovation curve as far as it needs to go.
What is being done to find new uses for the new materials?
Well at TE, we're one of the only companies that in our space that I'm aware of that has a dedicated team of material science scientists and experts. We're investing in material sciences as a core strength of our company. These teams have aggressive goals that are focused on new polymer design that create some form of competitive edge, whichever market application that we're talking about or addressing. We're also investing in the AI systems and databases that will improve our productivity, as I mentioned earlier.
What must be addressed to ensure new materials can meet requirements without compromising performance?
Our new Performance Materials BU team is focused on finding the right composition of polymers and fillers. The balance of polymer ingredients determines how it performs. So, given that there are so many permutations of a polymer formula, more permutations than there are atoms in the universe. In fact, the team's experience is invaluable in figuring out what that right balance is. At the end of this process, any new material would be fully validated and any product that comes from it would be fully validated.
What distinguishes TE’s approach to partnering with OEMs when developing new materials for customized solutions?
I would answer that is to say our level of investment in materials science, which is really an investment in very smart PhDs and also non PhD scientists. As I've said, as far as I'm aware, we're the only company in our space with a dedicated materials team. This team works with the BU teams that have the detailed application knowledge necessary to ensure that the right problems are being focused on. We are actively embracing AI as a tool to augment the number of polymers that can be developed, and the increasing speed connected with that is in one of our competitive advantages. Launching a performance material BU as a place to expand has been very critical as well.
How do you see materials research evolving over the next 5 years?
I think there is so much value-based creativity being created in smart materials, so many advancements in our understanding of the underlying physics and biology and the engineering of materials. Just so much science is being invested in that I really do see a continued expansion and acceleration of the rate of change in materials. Couple all that with the fact that we really do live in a material world. So based on that, I think the future is very exciting. And if you're looking for an analog, it feels like materials are at that same inflection point similar to the Telecoms world of 25 years ago, as it transitioned from a wireline pay by-the-minute world to a mobile cellular world with free voice over internet. I think everything is going to change.
Did you enjoy this interview? Read the source article.
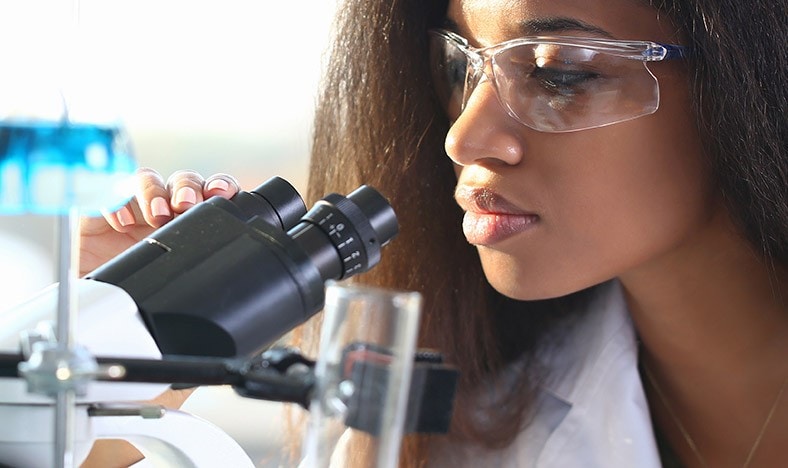
Innovation in materials engineering is enabling an evolution in product manufacturing. Companies that recognize this are developing processes to help them stand out from their competition.
Learn about the trends shaping materials development