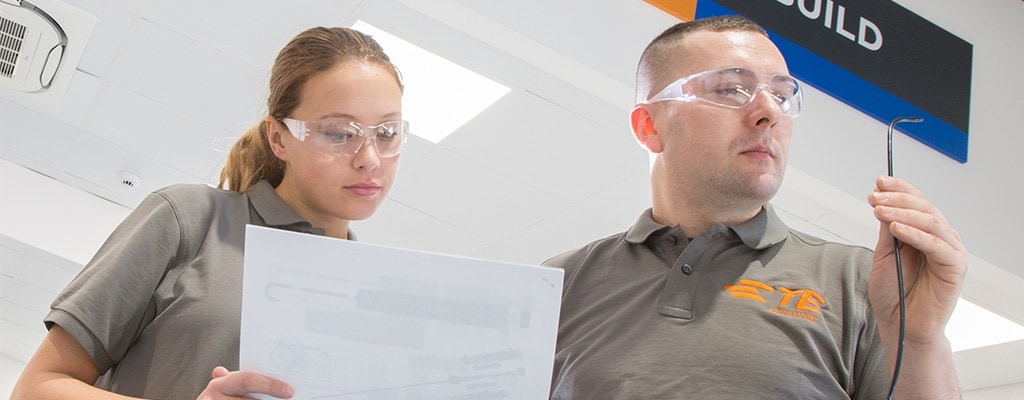
Meet our Experts
Our 330+ medical device development and manufacturing experts provide top-tier engineering and manufacturing expertise to help our customers innovate and manufacture key components and minimally invasive medical device solutions for a wide range of healthcare specialties and procedures. Meet some of them on this page.
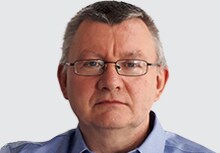
Bernard McDermott
Fellow, Medical
Bernard specializes in the design and development of interventional medical devices and device components at TE. He works closely with customers to provide high performance, cost-effective, novel, and manufacturable solutions from conception to production. A subject-matter expert in structural heart therapies and devices, Bernard also has extensive experience in electrophysiology, cardiovascular, neurovascular, peripheral and endoscopic devices.
Bernard is a member of the advanced technology group, whose key role is to take a long-term view of the future of medical device developments to identify and develop technologies that our customers will need in the coming years. In addition to nearly two decades of experience in medical device innovation and rapid prototyping groups, Bernard also has an extensive experience in other areas, including high-volume electronic device manufacturing and thermal design.
Engineering Speciality
Braided, hypotube or hybrid-based device design
Laser cut hypotube component design
Device simulation
Sensor integration
Design for manufacturing
Novel additive manufacturing processes
Focal applications
Smart devices
Next generation devices and constructions
Novel automated manufacturing processes
Ask Bernard about
Structural heart therapies and current devices
Future trends in interventional therapies
Component and device design
Design for manufacturing
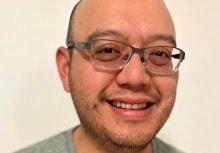
Steve Hsu
Engineering Manager, Polymer Tubing
1) Why did you choose to join TE? What makes you stay here?
I've been with TE for about 8 years. Previously, for most of my career I was in the tech space working on semiconductors. Right before joining TE, I worked for a solar company. I liked the sense of purpose I felt there, and I thought medical would be a good next move, as it would also allow me to have a positive impact on people's lives. TE was a good fit and has been great -- for my career, for myself and for my family.
2) What do you enjoy most about your work?
I especially like working with our customers’ R&D engineers. Often customers come in with a good idea of what they want, but just need some help tweaking it so it’s final. Not only do we have a large array of solutions in our back pocket, but we also have the ability to tweak things to fit their exact needs. This allows us to successfully help them with challenges they were struggling with. It's especially satisfying when we can provide a novel solution they've never seen before.
3) What’s the most interesting project you’ve worked on at TE?
The ability to use our solutions in new ways makes things very interesting. Take our reflow products. Typically, adhesive is used in these products as a sealant. One customer asked if we might be able to use the adhesive in a different way. On their suggestion, we were able to use the adhesive not only to seal, but to bond and build up a structure that solved their challenge.
4) What are the biggest challenges customers face?
Going forward, sustainability is a big driver for both TE and our customers. But there is this pull between single-use components to enhance patient safety and the desire to reduce medical waste. Medical devices don't breakdown easily, so we need to find new ways to make reusable products safer. Recently we looked at antibacterials that can be added to polymers. The concept of a circular economy, reusing more and being less wasteful is what our customers are increasingly focused on, especially in Europe.
5) Which personal traits are essential for today’s engineering challenges?
For today's engineers, I think curiosity is key. There must be a desire to learn and a willingness to change one's mind. This means looking at a challenge we've always handled a certain way and asking: 'what can we do differently? So often, we must fail first before finding a new and better solution.
6) What types of engineering changes do you expect to see over the next five years in heat shrink tubing?
There haven't been a lot of major changes in medical tubing in recent years. But exciting things are coming, thanks to the rise of 3D printing technology. Currently, we're working on miniaturization, which could be key in neurovascular applications. We also remain committed to supporting cutting edge minimally invasive procedures by pushing the capabilities of our materials and equipment in novel ways.
7) How does TE approach innovation, in a way that directly translates to the solutions we provide to customers?
The level of knowledge and innovation that exists within TE is tremendous. Our various labs across TE allow us to easily connect with a variety of subject matter experts. I have access to people with PhDs in areas I might only have surface level knowledge in. It can be very inspiring to go outside our smaller teams to get ideas and learn about what's possible.
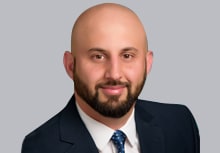
Jamal Rezayee
Staff R&D/Development Engineer, Metals Processing
1) What challenges you in a positive way?
Our customers are always pushing the boundaries of manufacturing, so keeping up with the latest technology in order to meet our customer’s demand is one of the best things about my job. I also relish using new advancements and technologies to adapt to new challenges.
2) How do you think you make a difference?
I have 13 years experience in guidewire design and manufacturing; this experience enables me to quickly understand the customer requirements and get prototypes to our customers quickly and accurately.

Makiya Kimura
Manager, R&D/Development Engineer
Insight. Experience. Creativity. Resilience. These traits define TE engineers. Makiya Kimura has had a love of designing and assembling models since he was a boy. As a TE Medical engineer, he still enjoys working with multiple components to construct a product--only now he's solving customers' problems and often helping build products that change people's lives. Collaboration with customers is key, to understand their challenges and find solutions quickly.
1) What has been your most interesting project to work on at TE?
I had the opportunity to work on two new I/O connectors, which both required a high-degree of design skill. The high pin count (456 pins or 456P) connector is very complex, and the other USB size 38P connector is simple but very small. Our product lines are full of variety, so every new project seems very interesting to me.
2) What do you enjoy most about your work?
I get to learn different types of connector design and development and have many possibilities to develop my career at TE. Here, I am on the cutting edge of technology and enjoy creating new products and seeing them be released to the market. Because of all the ways our products connect to people’s lives, I feel like I am contributing to society in a positive way just by working at TE.
3) What are the biggest challenges customers face?
Material selection for connectors is very challenging and very important because the materials must be able to tolerate sterilization. We use plastic and metal for connectors, so as sterilization requirements increase or become more harsh, being able to understand how materials will react and offer alternative, more durable solutions is crucial for design. Collaborating with customers is key because the customer’s challenge is our challenge as well.
4) Why did you choose to join TE?
I feel like I have been an engineer since boyhood—I always liked making plastic models and radio-controlled model cars. Now, my interest has shifted to connectors and I still enjoy working with multiple components to design and assemble the product model in development. Another aspect of working at TE Medical is that both mechanical design and electrical design skills are needed for connector design--something that interests me greatly as an engineer.
5) Which personal traits are essential for today’s engineering challenges?
As design requirements become more complex, the latest tools such as CAD systems and CAE tools help engineers design and build to specifications. However, it is important for engineers to consider the simplest solutions even in complex designs and systems. If some failure happens during development, which it often does in new product development, we have to be able to solve the problems quickly and the best way to do that is to start with the simplest solutions. Overall, the most important trait is to not give up—there is surely an answer somewhere and it’s our job to find it or to create it.
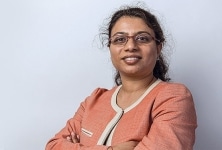
Richa Anand
Global Account Manager
1) Why did you become a product manager?
I come from a technical background and besides solving technical problems, I became very interested in providing solutions to customers from a business perspective by putting together the entire puzzle. As a product manager, I take great pride not only in the product offerings I represent, but also growing the business by effectively partnering with our customers.
2) What made you want to work for TE Medical?
There are many reasons. At TE Medical, we are building custom solutions for our customers who are in the very important business of saving lives. Everyone at TE is passionate about putting the customer at the center of everything that we do. Plus, TE’s Wilsonville, Oregon location, near Portland, is also a wonderful place to live.
3) What are some recent projects you have been working on?
I am working with a few key strategic customers and markets. We are pushing the boundaries in technology by offering customers complete assembly level solutions - not just sub-components. These have been some very exciting projects that I can't wait to see come to life.
4) What do you feel sets TE apart from the competition?
I believe that what sets TE apart is the simple fact that TE has been doing this for years but that we are constantly striving for innovation. We are looking to understand and develop the latest and greatest technologies for our customers. TE offers not only sub-components but has the engineering talent to work with our customers in providing complete solutions. Whether we start from a very basic design concept or we work to develop full assemblies. Our passion for an extraordinary customer experience drives so much of what we do.
5) In your global role, what are some things you are seeing?
I'm fascinated by what I see happening in Asia. Asia Pacific is growing and expanding with the demands and requirements on technology being different than in the US and Europe. Leadership in technology and development work continues to be dominated by the US and Europe. In my role, I love to work with my teams around the world to understand what is happening in the different markets and how we must adapt to address the customers' needs.
6) What’s a memorable story about TE you would like to share?
Well, so many stories come to mind. Here is an example of one: We were at an impasse with a customer where we were informed that we had won an opportunity, but the customer was not willing to issue the PO until they received specific data from TE. Because the customer was located in Europe and was available only at a particular hour, due to time sensitivity, some lead engineers from TE decided to take the call with the customer at 1:00 AM their local time to discuss and allay the customer’s concerns so that we can all move forward. And, guess what? The progress was made where both companies, TE and its customer, could partner together to move forward. Again, it's about delivering an unparalleled experience for our customers.
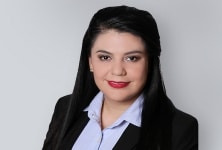
Sheila Garza
Sr. Manager, Supply Chain
1) Tell us about ECE (Extraordinary Customer Experience).
ECE is not only a program, it's our commitment to a culture that all TE employees are encouraged to live by. ECE relies on the fact that we should treat everyone as we would like to be treated. TE's ECE program gives us guidelines and motivates us to exceed expectations of both our internal and external customers. Every detail can make the difference. We work hard to deliver ECE in innovation, quality, delivery and service and support with our customers in every interaction.
2) Do you hear about many ECE success stories?
We have had great ECE stories since the launch of our ECE Program. My favorite ones are those where an opportunity becomes a success story. There are many things that our internal and external customers need, and our challenge is to not only meet customers' needs but to exceed their expectations. By doing so consistently, will be able to continue to improve our partnerships and strengthen our relationships to help ensure a solid future.
3) What are some challenges your customers face?
Our customers’ biggest challenge is that they need partners that are committed to excellence because their products are used to save lives. Our goal to deliver on that challenge is not only to deliver products with high quality standards, but to make our connection solutions more innovative on a daily basis. At TE Medical and with our customers, we foster open collaboration and innovation so we can help deliver excellent products to the market.
4) What do you like best about working for TE?
I enjoy working at TE because this is a company that fosters inclusion and diversity. I love the TE brand because it stands for innovation and growth. We offer advanced connectivity in catheter systems, sensors technology, and many other applications that will make our products more innovative for our customers.
5) What inspires you?
My family is my big inspiration. I am proud to be part of TE Medical and support our customers who manufacture life-saving medical devices that can make a tremendous positive impact in the lives of our loved ones. My family inspires me to continue looking for daily improvements; they inspire me to help my team to be better leaders as ambassadors of the Extraordinary Customer Experience. At the same time, my commitment is to keep learning and be open to innovate with our internal and external customers.
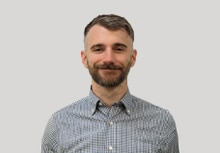
Troy Brown
Advanced Development Engineer
1) Why did you choose to join TE? What makes you stay here?
I work for the Advanced Development Engineering Group, specializing in medical connectors and cable assemblies. It's an area that comes with unique learning opportunities. Reusable interconnects are used in harsh environments, including constant flexing and steam sterilization. Understanding materials and testing is critical in my job. We must be able to determine that a cable is going to last a specific number of cycles under certain conditions. I love the engineering challenge of performing the testing and statistical analysis needed to validate the types of solutions we work on.
2) What do you enjoy most about your work?
I like the challenge of trying to understand a problem completely. Not just looking at one little section of an assembly set, but the whole picture. Asking, 'What are the upstream and downstream impacts of a change?' Coming up with a solution, then trying and testing, and improving that solution. It could involve building it by hand in the lab, working with technicians, whatever it takes. Ultimately, seeing a solution in production, and then being used in a clinical setting is rewarding.
3) What has been your most interesting project to work on at TE?
There are so many interesting projects, but one that comes to mind is working on the development of an automated fine wire termination system. One of our technicians showed me what he was doing with a soldering iron. The result was not what I expected. But we agreed it was worth looking into. We worked the project for almost two years, from initial test to making it reliable. In the end, we created a special piece of equipment and solder paste—all from an unacceptable result that sparked my curiosity to improve on the process we were using at the time.
4) What are the biggest challenges customers face?
The medical industry is unique in that there’s a desire for novel treatments. This, in turn, creates demand for novel medical devices. Sometimes existing knowledge can be leveraged to develop new devices, but often they need to be built from the ground up. With new devices, OEMs want to move fast, but they may lack knowledge in certain areas of manufacturing. This is where TE Medical comes in, which is to help support OEMs with refining specifications, tweak designs and perform testing.
5) What personal traits are essential for today’s engineering challenges?
The ability to communicate is very important in engineering. The bottom line, no one is going to let you work on something if you can't sell yourself on your ability to solve a problem. Natural curiosity and a desire to understand a challenge is also critical. That means going the extra mile, not only to figure out a solution but also to understand exactly why something doesn't work.
6) What types of engineering changes do you expect to see over the next five years?
Product development cycles will continue to shrink over the next several years. To do our very best for customers, we will have to find ways to do things faster. Faster response to customer concerns, faster testing, faster production, faster everything—all while maintaining the level of reliability and quality required in the medical industry. This is where our PROPELUS™ Prototype Center can help accelerate component prototypes. Ultimately, companies will be looking to get their products out the door and through clinicals as quickly as possible.
7) How does TE approach innovation, in a way that directly translates to the solutions we provide to customers?
The amount of expertise we have at TE directly supports our ability to innovate. We have many resources at our disposal, including labs throughout the country. When working for a smaller company, you often send things out to an external lab to get answers. Doing this adds both time and money to projects. By having our experts in-house, we can find out right away whether we're headed in the right direction or if a project even makes sense from a technical standpoint. It's a huge benefit.
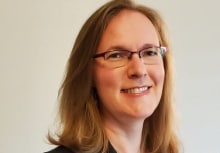
Marie Ottum
Sr. Principal Engineer, Advanced Development
1) Why did you choose to join TE? What makes you stay here?
I've been with TE for over 10 years now after coming across a position in the Advanced Development group in the medical business. I really liked the idea of being able to work on something that would improve people's lives. Previously, I'd been in consumer electronics and was wanting something more meaningful. I was also excited to be involved in building the next generation of medical products and taking advantage of all the labs, tools and resources that TE has to offer.
2) What do you enjoy most about your work?
There are so many opportunities to connect with subject matter experts of various discipline at TE, including a fantastic internal engineering conference we have every year, TEchCON. In addition to technical knowledge, I've enhanced my non-technical skills such as communication through involvement in our employee resource groups. As part of TE’s employee resource groups, I've held leadership positions that exposed me to functions and business units I otherwise never would have been a part of. I also love the customer interaction we get as contract manufacturers. Working with so many different customers and teams is fun and motivating.
3) What has been your most interesting project to work on at TE?
I like complex projects that require me to step back and see the big picture, how things interface with one another and how we need to set our requirements based on those complexities. I find smart catheter products especially interesting because there are so many elements coming together including mechanical catheter shafts, sensors and electronics. In one of my favorite projects, I worked with a customer on a single-use endoscope that helped TE gain new capabilities that had been previously outsourced.
4) What are the biggest challenges customers face?
Today's customers face many challenges. Of course, sustainability is huge including the need for new materials and processes that will allow us all to be less wasteful. But if we focus on our medical customers specifically, there is an aging population that requires more and more procedures and treatment options. Smart catheters and robotic solutions will be key in addressing this need, driving a shift to more minimally invasive catheter-based approaches. By integrating electronics and sensors into these products, medical device OEMs will also be able to capture data that will help providers offer more personalized patient care.
5) What traits are essential for today’s engineering challenges?
Inherently, engineers must be curious. Not only do they need to develop their own ideas, but they must also be able to collaborate as part of a team. Today, I think we have some unique challenges post COVID related to that. There's a lot more hybrid work, making us less physically connected. As a result, being able to read other people and understand the impact our words and actions have is more important than ever.
6) What types of engineering changes do you expect to see over the next five years?
Today's engineers are using more AI-based simulation tools. So, harnessing data and using it to guide our designs using AI to enable new materials and processes will be one of the biggest opportunities in the next five years. That includes using generative design tools to speed up the design process. Additive manufacturing will also continue expanding as more customers start to use it in production.
7) How does TE approach innovation, in a way that directly translates to the solutions we provide to customers?
Innovation is key moving forward. One way we do this is by using more simulation. Whether it's cut patterns on hypotubes, tooling for extrusions, understanding how materials reflow to make a finished catheter shaft, or getting the electrical properties right, simulation increases the confidence in our products even further. We pair that simulation with targeted prototyping at our design centers, such as our PROPELUS™ Prototype Center, where customers can see their ideas developed, quickly.
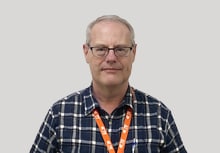
Charlie Holtan
Development Engineer
1) Why did you choose to join TE? What keeps you here?
As a development engineer specializing in ultrasound, imaging and mapping catheters, I work with directly with medical device OEMs. When I first started here 24 years ago, I knew I wanted a customer facing job. I also wanted to make sure I chose a company backed by engineers that would help me learn and grow. TE has delivered on both fronts. I really like the team I work with, the access I get to manufacturing sites and production operators helps me deliver better solutions. Strong internal TE relationships is one of many reasons why TE is a great place to work.
2) What do you enjoy most about your work?
I like solving problems and making things easier for both our customers and our internal teams. I really enjoy working with our colleagues here in the R&D lab and the manufacturing groups, as well as our customers. It's great being involved with so many groups and at the different levels. It's these relationships that enable me to provide the best possible technical solutions for our customers.
3) What has been your most interesting project to work on at TE?
When we first started getting inquiries about imaging catheters, a research group working on a grant project reached out. They wanted TE to create the catheter cable assemblies and a generic system interconnect cable for different types of ICE catheters. I had a chance to work directly with the doctors doing the testing and the engineers and scientists from the universities. We prototyped five or six different solutions. As the main person putting it all together for them, I had a lot of fun.
4) What are the biggest challenges customers face?
Unlike the early days of ultrasound technology, cost was secondary to performance, today's customers face significant budget concerns. That, combined with regulatory challenges creates a very competitive environment. One way TE provides added value for these customers is by offering a broad array of solutions that includes cable assemblies, connectors, and other capabilities, which enables customers to reduce the number of vendors they work with.
5) Which personal traits are essential for today’s engineering challenges?
Increased outsourcing and globalization in the industry is changing how engineering is performed. The number one trait needed in engineering today is the ability to communicate effectively. This includes connecting with people in different countries with different cultures and at different levels of seniority. Adaptability is also a key trait. When it comes to things like systems, documentation requirements and manufacturing locations, change is constant, and engineers need to be able to adapt quickly.
6) What types of engineering changes do you expect to see over the next five years?
We will see many of the engineers that pioneered medical components and devices begin to retire. It's important that they share their knowledge with the younger group coming up to fill their place. Covid has also changed how and where we work, especially around remote work. As a result, teams are more spread out and international collaboration has increased. I think we will see more and more engineers “working in multiple sites.”
7) How does TE approach innovation, in a way that directly translates to the solutions we provide to customers?
TE does a great job with taking technology that's developed in in one industry and sharing it across the different business units. In addition, at an individual site level, there's a lot of emphasis on platforming. By creating a standard technology that can be used across a variety of medical device applications, we maximize the value that we bring to our customers..

Katie Devin
Product Manager, Metal Shafts, Hypotubes & Needles
1) Tell us about ECE (Extraordinary Customer Experience).
ECE is not only a program, it's our commitment to a culture that all TE employees are encouraged to live by. ECE relies on the fact that we should treat everyone as we would like to be treated. TE's ECE program gives us guidelines and motivates us to exceed expectations of both our internal and external customers. Every detail can make the difference. We work hard to deliver ECE in innovation, quality, delivery and service and support with our customers in every interaction.
2) Do you hear about many ECE success stories?
We have had great ECE stories since the launch of our ECE Program. My favorite ones are those where an opportunity becomes a success story. There are many things that our internal and external customers need, and our challenge is to not only meet customers' needs but to exceed their expectations. By doing so consistently, will be able to continue to improve our partnerships and strengthen our relationships to help ensure a solid future.
3) What are some challenges your customers face?
Our customers’ biggest challenge is that they need partners that are committed to excellence because their products are used to save lives. Our goal to deliver on that challenge is not only to deliver products with high quality standards, but to make our connection solutions more innovative on a daily basis. At TE Medical and with our customers, we foster open collaboration and innovation so we can help deliver excellent products to the market.
4) What do you like best about working for TE?
I enjoy working at TE because this is a company that fosters inclusion and diversity. I love the TE brand because it stands for innovation and growth. We offer advanced connectivity in catheter systems, sensors technology, and many other applications that will make our products more innovative for our customers.
5) What inspires you?
My family is my big inspiration. I am proud to be part of TE Medical and support our customers who manufacture life-saving medical devices that can make a tremendous positive impact in the lives of our loved ones. My family inspires me to continue looking for daily improvements; they inspire me to help my team to be better leaders as ambassadors of the Extraordinary Customer Experience. At the same time, my commitment is to keep learning and be open to innovate with our internal and external customers.