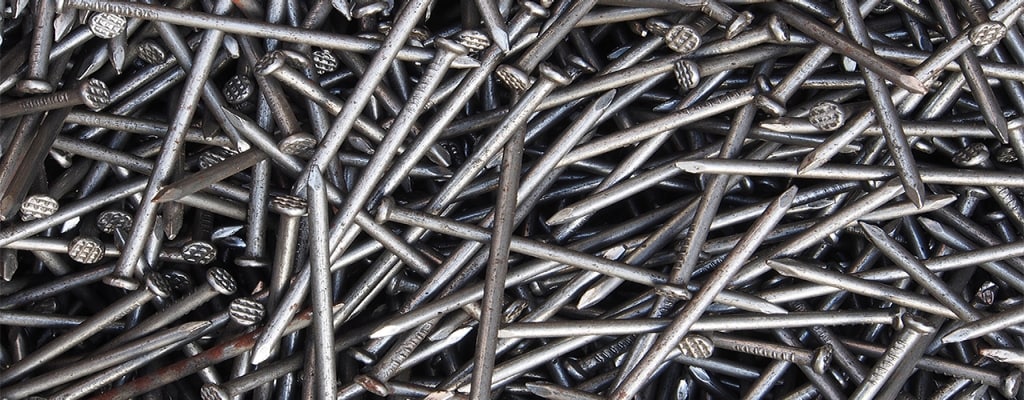
Trend Insight
Fiber Needs an Image Change
"It’s antithetical to think of fiber in rough and ready consumer devices, ...or bumping along in vehicles or thriving in harsh industrial and physical environments. Yet that’s what’s beginning to happen."
Fiber: Rough and Ready?
If you ever search for clip art of “optical fiber,” you will find pictures of hair-thin bundles lit from within like glow sticks. One imagines these carefully held by masked, white-gloved lab technicians and carried with a ceremony that emphasizes their preciousness. Brittleness, delicateness, and fragility leap to the popular mind with the word “fiber.” It’s antithetical to think of fiber in rough and ready consumer devices, flung onto tables, or bumping along in vehicles or thriving in harsh industrial and physical environments. Yet that’s what’s beginning to happen. In addition to being a question of cost, to really penetrate the last feet of delivering bits optically to the consumer, from cloud to chip as it were, fiber needs an image change: it needs to be tough.
For the Last Few Feet
Photons were created 10 seconds after the Big Bang and have remained around ever since. Without digressing into a physics lesson, photons are intrinsically pretty tough and are the fastest thing around. When channeled, they allow vast amounts of data to be squeezed down a single strand of fiber. How much data depends on things like fiber composition, its length and noise, but theoretically data rates in the petabits per second for each optical fiber are possible (single mode). The momentum is clear, all the world’s data will at some point be transmitted through photonic guiding mediums. Most people can imagine the great telecommunication fiber trunks circling the world, transmitting bits at close to the speed of light over thousands of kilometers. But then they hit “the last few feet.” Within the last few feet exist consumer products, self-contained independent systems like automotive vehicle harnesses, switch and router data cards and most homes and business premises. Copper wire has dominated this “last few feet” for good reasons and will remain a good choice for designers. But there are application specific reasons to look at this anew.
LIGHT
Fiber is lightweight, so more wires don't mean added weight.
FLEX
Fiber is more flexible today and tougher today, thanks to bendable polymers.
FEEL
The future of fiber promises stress detection and added security.
Making the Case for Change
Optical Fiber Cabling
Light, Flexible, Strong, and More
Fiber is light. I don’t mean that poetically, I mean in weight. The more things we wish to connect the more wires (and wireless, of course) we need to connect them. Harnesses of copper wire weigh a lot and are hard to route (formally called “cable management”). New bendable polymers mean that fiber is a lot more flexible and tougher than people think. It’s useful for wiring the control and infotainment systems in weight sensitive commercial aircraft where space is at a premium. Also, changes in photons streaming through the fiber can be used to detect stress in structures and physical intrusion; a photonic nervous system that senses change very accurately is in the near feature. Quantum cryptography promises hacker free transmission. But we don’t need to think so exotically.
Optical Chips
The Ultimate Destination
Fiber is making it into the thought processes of the automotive business for some of the same reasons; the more things that need to be connected, the heavier the cables get. There are multiple experiments of signal carrying copper traces in PCBs being replaced with optical lines as an alternative to directly connecting components with robust optical cabling (a much better solution in my mind). It has to be said, though, that one technology replacing another always takes longer than advocates predict. The optical components required to route photons aren’t free. Aircraft and vehicle designers are reluctant to change copper harness infrastructure that has proven its reliability over many years. Caution is rational, given the downsides of failure, but the chances are that you’ve flown in commercial aircraft controlled by optical cabling. Optical chips, of course, in which electrical communication busses are replaced with photonic communication busses, are the ultimate destination.
The Makeover Starts Now
It comes as a shock then when one actually visits a fiber wire manufacturing plant. For all the highest-tech associations connected with fiber, the process starts as a thick block of silicon being heated with intense burners as if being roasted on a spit. Burners melt the silicon and dope it with germanium or other elements. After a period of dope-roasting, the block of glass is taken to a 100+ foot draw tower, reheated and pulled into the long strands we’re all familiar with, clad in a protective coat and rolled around shipping drums. Born in the aftermath of the biggest explosion ever known, existing for 13.8 billion years, channeled in silicon dioxide manufactured in a blacksmith-like process of fire, elemental soot and kneading, the photon is tough! Fiber’s delicate image is holding it back! It will be a leading indicator of penetration in the “last few feet” when we begin to see clip art of an installer’s van, crowded with tools, ladders, fast food wrappers and thoughtlessly thrown drums of fiber.