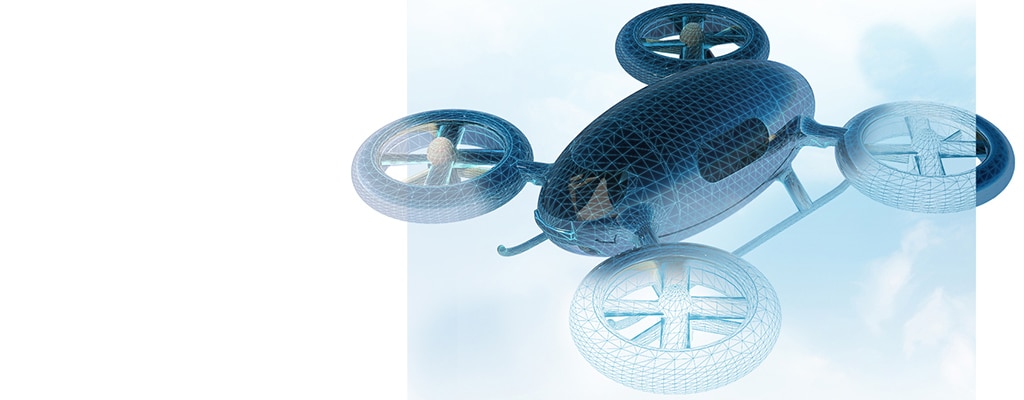
Trend Insight
Reducing Avionics System Weight to Help evTOL Take Off
Lighter advanced interconnects and cabling can contribute significantly to weight reductions in AAM and eVTOL avionics systems without compromising performance.
Advanced-air-mobility (AAM) and electric-powered vertical-takeoff-and-landing (eVTOL) aircraft promise a quieter, environmentally cleaner alternative to hydrocarbon-fueled cars and conventional rotorcraft. Minimizing gross takeoff weight (Wgto), which includes reducing the weight of avionic systems and related interconnects and cabling, is critical to making Urban Air Mobility (UAM) a reality. Lighter, advanced interconnects and cabling can make a significant contribution to weight reductions in UAM aircraft, despite being only a fraction of the total electrical/electronic-component weight.
The Effects of Weight on Aircraft Design
Today’s civilian aircraft carry more electronics than ever. Designers must fit screens, sensors, data hubs, switches, SSD arrays, computers, in-flight-entertainment (IFE) servers and other electronics throughout the airframe and cabin, which requires a tremendous amount of wiring.
Conventional aircraft:
In just one example, the total weight of all wiring and connectors in a wide-body commercial jet is calculated to be 1,814 kg/4,000 lbs.1 Hauling that mass consumes nearly 60,000 gallons of jet fuel annually. Based on the average cost of jet fuel in the U.S. at the time of publication ($6.61/gallon in Nov. 2022), the annual cost for that amount of fuel is $396,600. The annual CO₂ emissions from burning that much fuel amounts to 2,785,200 kg (1,266,000 lbs) — the equivalent of automobile emissions from 124 passenger vehicles.2
In conventional aircraft, weight is optimized for long range and endurance. Approximately one-third of takeoff mass is lost during fuel burn at takeoff, and the plane continues to lose weight as fuel is consumed during the remainder of the flight.3
UAM and eVTOL aircraft:
The effect of weight on UAM and eVTOL aircraft is much different. Vehicle weights remain constant in battery-powered crafts and nearly constant in hybrid UAMs. As a result, UAM designs can be optimized based on payload capacity, the number of passengers, range and safety considerations. Vehicle weight does factor into the power required to hover and in determining motor size and battery requirements for the aircraft.4 Reducing the weight of each component without compromising performance of the aircraft is essential.
Avionics Systems Contribution to Vehicle Weight
The relationships between weight and other design variables have a cascading effect. For example, reducing the weight of the integrated avionics system reduces the overall mass of the UAM aircraft, which reduces disk loading (DL). That, in turn, reduces the power needed to maintain rotor speed, which reduces battery size and ultimately reduces the vehicle’s overall weight even more.
Depending on the type and passenger capacity of a UAM aircraft, its electrical and electronic components contribute 27% to 68% of non-passenger, non-structural system weight (Figure 1).5
Figure 1: Sources of system weights (in pounds) in various UAM aircraft
UAM Type |
Quadrotor | Side-by-side | Tiltwing |
Number of Passengers | 1 | 6 | 15 |
Total System Weight | 161 | 438 | 938 |
Automatic Flight Control | 40 | 40 | 40 |
Instruments | 10 | 10 | 10 |
Mission Equipment | 40 | 40 | 40 |
Electrical* | 20 | 70 | 160 |
Percent system weight contributed by electrical/electronic components | 68% | 37% | 27% |
*Electrical system weight is estimated to be 10 lbs plus 10 lbs/person. | |||
Source: Johnson, W., Silva C., and Solis, E., “Concept Vehicles for VTOL Air Taxi Operations,” AHS Technical Conference on Aeromechanics Design for Transformative Vertical Flight, San Francisco, CA, January 2018. Adopted from Table 7, System weights, p. 7. |
Advanced Interconnect Technologies Reduce Vehicle Weight
An advanced Controller Area Network (CAN) bus, Single-Pair Ethernet (SPE) and advanced modular-rack-principle interconnect technologies can reduce the weight of integrated avionics systems. These can boost an eVTOL flight performance in terms of disk loading (DL) while enhancing system robustness and bandwidth.
Serial Communications:
In the 1980s, Robert Bosch GmbH developed the CAN protocol for automotive applications. The standard has since been adapted for aircraft. CAN bus offers a low-weight, economical and easy-to-implement alternative to twisted-pair cabling for basic avionic functions in eVTOL vehicles.
The classic CAN frame format accommodates short messages with up to an 8-byte data payload and is available in different versions. The maximum bit rate of “high speed” CAN bus (ISO 11898) is 1 Mbit/s. The CAN Flexible Data (CAN FD) protocol, a relatively new format, allows bigger data payloads (64 bytes) and faster bit rates, 8Mbit/s, for up to 800% faster throughput.
In conventional aircraft applications, CAN bus is used:
- In radio system control panels in flight deck to radio system Line-Replaceable-Units (LRUs) and engine control interfaces;
- For LCD flight instrument displays in glass cockpits;
- To feed control systems and inertial measurement units (IMUs) with altitude, velocity, position, motor parameters and other data critical to unmanned aerial vehicles (UAVs) and drones.
For eVTOL applications, CAN bus can be used to provide fly-by-wire electronic control of flaps, trim, engine controls and autopilot systems in place of bulky, direct mechanical linkages between the flight controls and the flight surface. Further weight reductions can be achieved by transition to fiber optic cabling for CAN bus networks. Comparing FO cable assemblies vs. twisted pair CAN bus copper cable assemblies, it is often possible to replace several shielded twisted pair cables by a single multiple FO cable. That can result in a 90+% cable weight reduction, depending on the AWG being replaced. In addition, there are potential benefits from the EMI immunity of FO cable, which can be a consideration on eVTOL platforms involving DC-AC invertors.
Ethernet Communications:
ARINC Specification 664 calls for quadrax (four-wire) cable or fiber-optic cable. Copper quadraxial cable using MIL-DTL-389994 circular connectors supports up to 100 Mbs.
A recent development is the issuance of a Single-Pair Ethernet (SPE) standard under ARINC 854 specifications for the Cabin Equipment Network Bus. Compatible connectors and cables are described under ARINC 800 Part Two and Part Three specifications, respectively.
Echoing the history of CAN bus, ARINC 854 was based on the 100Base-T1 (IEEE 802.3bw) standard developed in the automotive world. Compatible connectors are available based on DEUTSCH 369 series connectors, a family of rectangular connectors that provide a robust solution in a small envelope.
The weight savings of an SPE solution are significant. SPE cable is up to 73% lighter than a comparable four-wire copper cabling system. The smaller dimensions of cables with 26 AWG wire also improve space utilization. For example, switching from a quadraxial cable with four 24 AWG wires to an SPE cable with two 26 AWG wires shrinks the cable’s diameter by approximately 15%. SPE links can be certified for 100 Mbs operation at 15 m (49 ft) lengths. Future provisions will enable 40 m (131 ft) lengths and speeds up to 1,000 Mbs.
Similar weight saving potential exists in moving from SPE twisted shielded cabling to fiber optic cabling, similar to the CAN bus case already discussed.
369 series connectors employ standard Mil-Spec AS39029 contacts. These miniaturized contacts are particularly robust against vibration. The connector shell is constructed from rugged composite materials that are as strong as steel but 40% lighter.
Modular Racks:
Most of today’s collision-avoidance, IFE, air-to-ground-communications and other avionics systems employ electronics packaged in an Aeronautics Radio INC (ARINC) 600 standard metal enclosure that holds up to 12 Modular Concept Units (MCU) in a centralized “box.” However, a big box has significant limitations, which inspired the development of ARINC 800 series standards in response to the general trend toward embedded computing on miniaturized printed circuit boards (PCBs) deployed locally. The family of ARINC 800 standards includes:
- ARINC 836 defines modular, standardized rack-style enclosures, cabling, connectors and grounding methods for aircraft cabins
- ARINC 836A establishes a mini modular rack principle (MiniMRP) for avionics packaging
- ARINC 836A MiniMRP offers a compact form factor utilizing interconnects that can reduce package size by 40% and weight by 60% as compared to a standard metal enclosure for UAM aircraft
Modeling Effects of Weight Reductions
Implementing a two-wire CAN bus and SPE solution with MiniMRP for UAM connectivity reduces weight by only a small fraction of UAM total mass. However, the reduced size still makes a big contribution to flight performance.
In UAM design, there is a complex relationship between empty weight (eW), takeoff power (T), and disk loading (DL). An increase in DL corresponds with an increase in eW.6 And increasing DL has been shown to correspond parabolically to an increase in maximum T.7
Compared to a four-wire solution for AFDX, a two-wire CAN bus/SPE connector/fiber-optic solution with weight-optimized connectors can potentially reduce avionics cabling and interconnect weight by 50%.
For smaller UAM aircraft, the effect of small weight reductions can be substantial. Reducing avionics system weight from 20 kg (44 lbs) to 10 kg (22 lbs) in a eVTOL aircraft with a 2,000 lb Wgto can cut DL significantly, which has a positive ripple effect that affects rotor, motor and battery size and mass, while contributing to a more compact avionics bay without sacrificing the robustness of the electronics.
Key Takeaways
- AAM and eVTOL aircraft promise a quieter, environmentally cleaner alternative to hydrocarbon-fueled cars and conventional rotorcraft for travel within urban environments.
- Minimizing gross takeoff weight is critical to making urban air mobility a reality.
- While only a fraction of the total electrical/electronic-component weight, advanced interconnects and cabling can make a significant contribution to weight reductions in eVTOL aircraft.
- Advanced CAN bus, Single-Pair Ethernet and advanced modular-rack-principle interconnect technologies can reduce avionics weight to boost UAM flight performance.
References
- Source of wiring weight in Boeing 747 (4,000 pounds): Weber, Austin. “Wire Processing: The Future of Wire.” Assembly, March 30, 2011. Accessed April 20, 2020.
- Graves, R., Advancing Aircraft Connectivity with a Single Pair Ethernet Solution, TE Connectivity, Harrisburg, PA, April 2020, pp. 2-3.
- “Table 6-1: Large Commercial Aircraft – Incremental Fuel Burn.” Economic Values for FAA Investment & Regulatory Decisions Guide - Subsection 6.3.1: Incremental Fuel Burn. Federal Aviation Administration: Regulations & Policies: Policy & Guidance: Benefit-Cost Analysis, September 23, 2016. Accessed April 20, 2020.
- Bacchini, A. and Cestino, E., Electric VTOL Configurations Comparison, Aerospace 2019, 6, 26, February 2019, pp. 7-13. doi:10.3390/aerospace6030026.
- Johnson, W., Silva C., and Solis, E., Concept Vehicles for VTOL Air Taxi Operations, AHS Technical Conference on Aeromechanics Design for Transformative Vertical Flight, San Francisco, CA, January 2018.
- Gatti, M., Preliminary Design Analysis Methodology for Electric Multirotor, Conference Paper in IFAC Proceedings Volumes, November 2013, p. 7. dio: 10.3182/20131120-3-FR-4045.00038
- Excalibur: The Cutting Edge in Tiltrotor Technology, 2011 AHS Design Proposal, Alfred Gessow Rotorcraft Center, Department of Aerospace Engineering, University of Maryland, College Park, Maryland, p. 20.
Find Out How TE Can Support Your Next Urban Air Mobility Challenge?