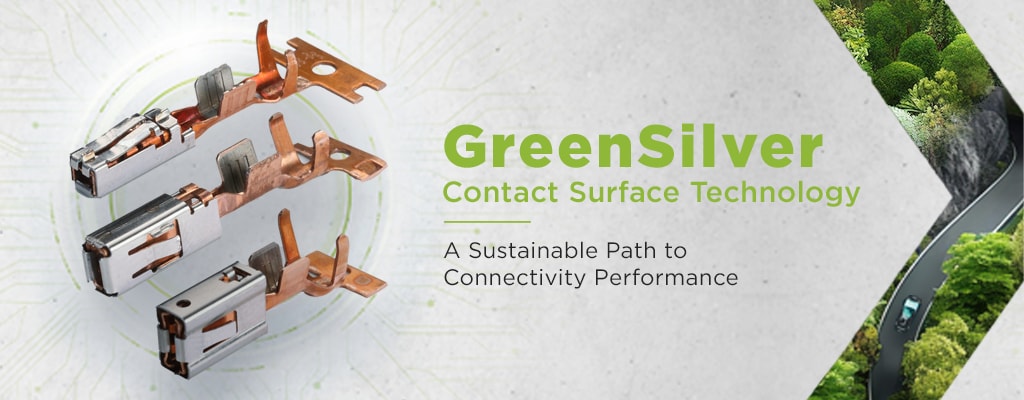
GreenSilver Contact Surface Technology
Removing Barriers to Innovation: Solving automotive connectivity challenges with ‘green’ surface technology
35%
Less Energy Consumption & CO2 Emissions
99%
Less Fresh Water
180°C
Temperature Resistance
Sustainable and Innovative Solution Breakthrough
Exceeding today’s requirements while enabling tomorrow’s innovations. As the demand for higher-performing connectors increases, so does the industry’s need to be freed from outdated surface technology that limits its ability to innovate and meet sustainable goals.
Managing environmental impacts in ways that count, TE Connectivity’s new GreenSilver contact surface technology is an innovative ‘green’ technology helping manufacturers not only meet their sustainability goals but is also designed to enhance connector performance in high voltage applications for EV powertrains enhancing vibration tolerance and heat dissipation as well as being ideal for low-power and signal transmission purposes in miniaturized connectivity.

Best-in-Class High-Performance
TE's GreenSilver contact surface technology will enable the future of automotive trends by supporting highly complex and reliable connections – often in extreme high-vibration and high-temperature environments by achieving the highest performance connector system for the engine and body. GreenSilver achieves the pinnacle of performance by producing a finish that provides the superior conductivity of silver, exactly where needed and only there while simultaneously withstanding temperatures of 180°C , very high vibration levels, achieving lower mating forces, an increase in mating cycles, with no cold welding, and thiol-free contacts reducing the overall complexity in the components.

The Future is Green and Bright
TE Connectivity (TE) is leading the charge in advancements towards our CO2 neutrality efforts, achieving an industry breakthrough by introducing an environmentally sustainable solution. The positive environmental impact of the sustainable and streamlined manufacturing process for TE's GreenSilver contact surface technology eliminates hazardous materials associated with electroplating leading to 35% CO2 emissions reduction. Additionally, it uses no water during the dry depositioning process of the contacts, and consumes 35% less overall energy by pinpointing the accuracy of the coatings when applied to specific areas, creating a more efficient process while contributing to increased supply chain optimization.
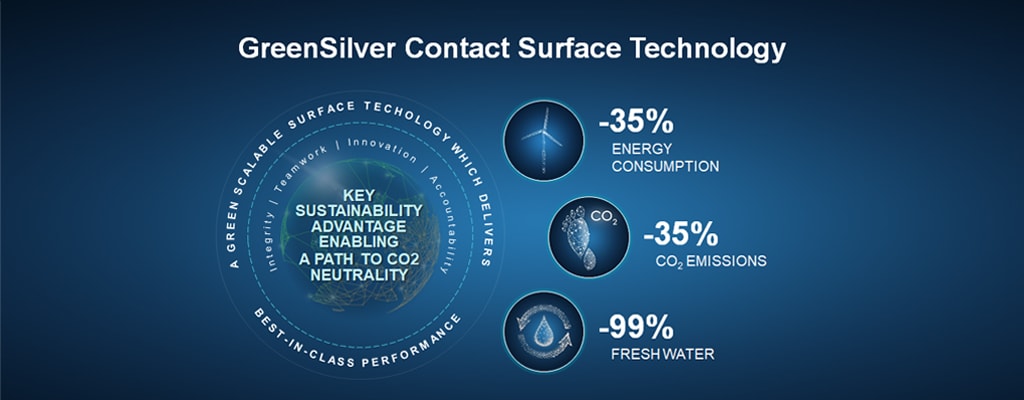
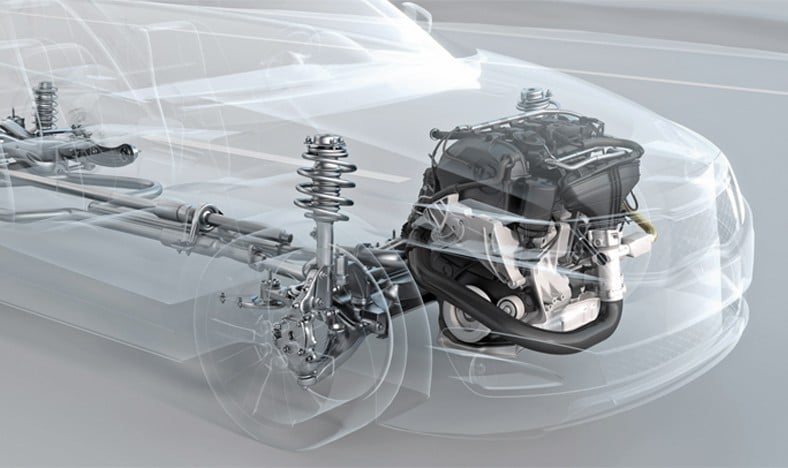
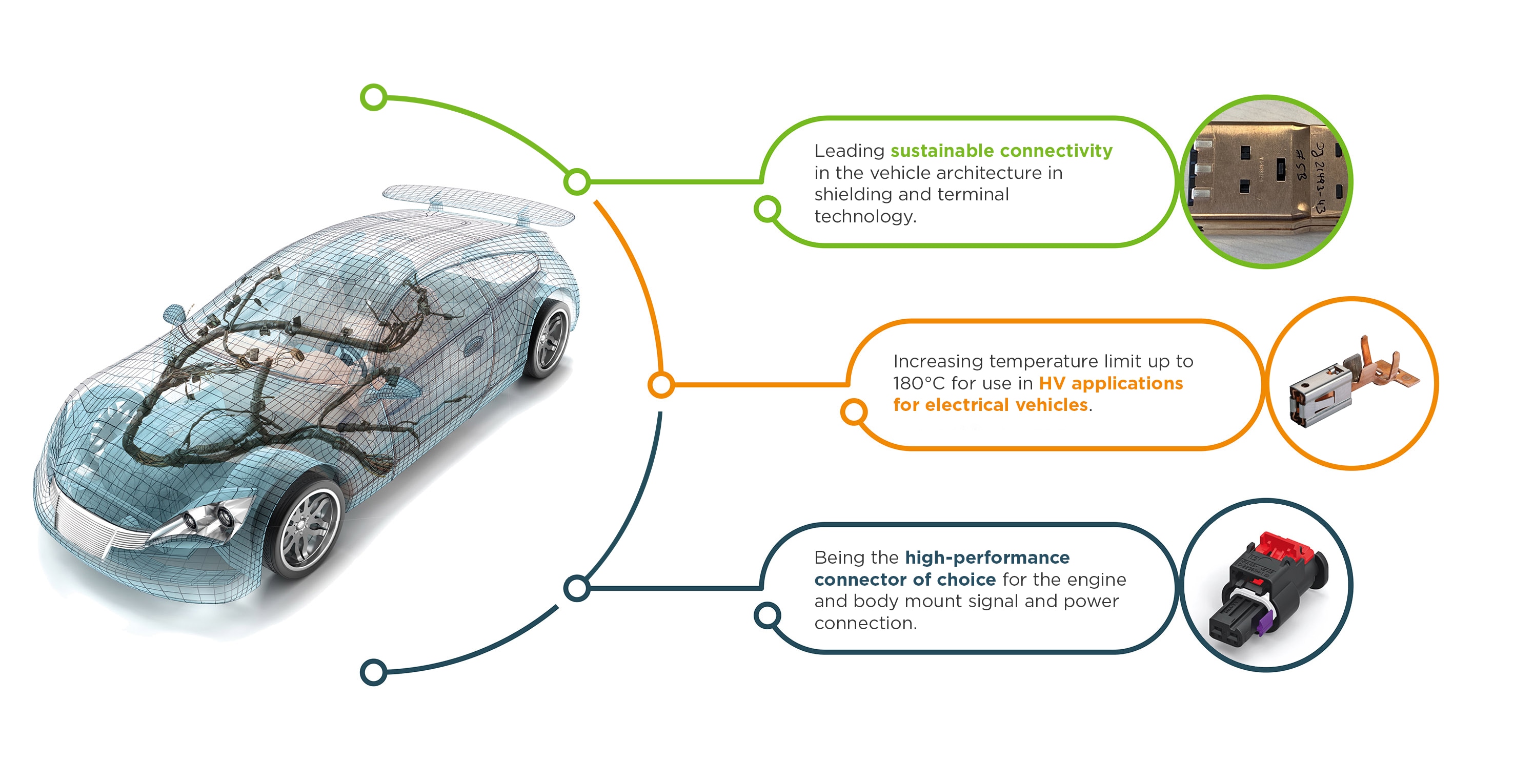