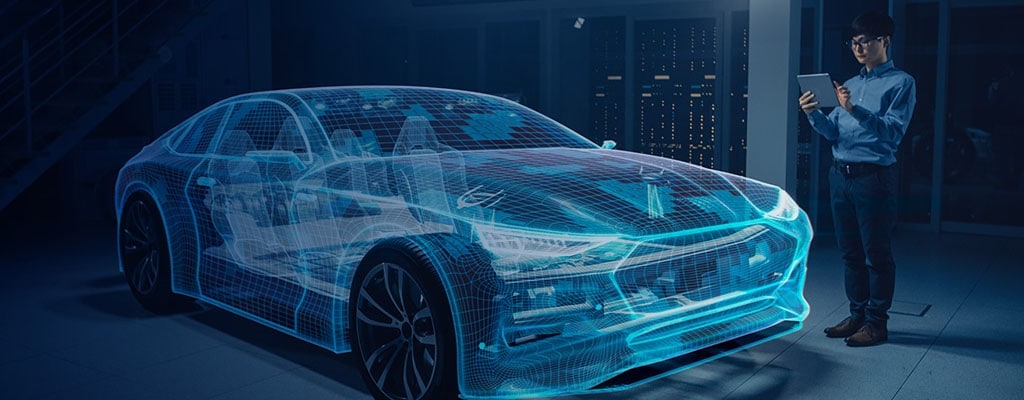
Trend Insight
Rugged for Extreme Temperatures
Interconnections are offering new levels of weight savings for autosport applications. By: Paul Webb, Sales and Marketing Manager, Autosport
In Formula 1 racing and other autosports, weight reduction is critical to competitive advantage. A few grams saved here and a few more saved there can add up to significant savings overall. We are also seeing a move toward high-density packaging of electronics parts. As the electronic content of cars increases, the natural drive is to miniaturize the package to gain maximum efficiency in the use of space. The wiring harnesses and interconnection systems offer opportunities for weight and size reduction. The first requirement for connectors and cable is a rugged design that can withstand extreme temperatures, vibration, and exposure to fluids in general and brake cleaner in particular.
Evolution of Connectors
The evolution of TE Connectivity’s (TE) DEUTSCH AS Series connectors demonstrates the miniaturization of connectors. Smaller connectors typically weigh less, so attention was paid to developing higher density connectors. Stainless steel shells gave way to lightweight aluminum, with even lighter composite available. Features like coupling rings became smaller. As connectors shrink, attention must also be focussed on usability issues, such as redesigning knurls to make it easy for a gloved technician to quickly and accurately connect and disconnect the connectors. Composite-shell connectors offer an attractive method for reducing weight. When the industry first looked at composite connectors, they did not live up to expectations for rugged performance in the autosport market. In particular, the composites did not withstand exposure to brake cleaner. As a result, designers moved away from their use. Composites are evolving. They have improved dramatically, with the next generation soon to meet the needs of auto racing fully. Composites deserve a fresh evaluation of their capabilities to save weight and meet the mechanical and environmental needs of autosports.
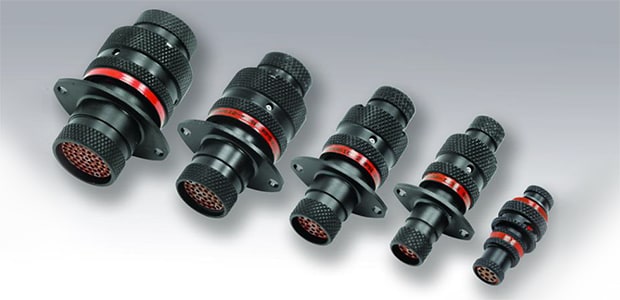
Traditionally, composites have reduced connector weight by around 40 percent. By optimizing the reinforcing material and introducing foam into polymer matrices, an additional 10 to 20 percent savings can be reached. Not only the fiber material but also the length of the reinforcing fibers play a significant role in determining the strength of the finished part. Higher strength materials can mean reduced wall thickness and hence lower weight. Introducing foaming agents or microspheres into a polymer composite – although made more difficult as the reinforcing fiber volume increases – is now possible. High-performance thin-wall cables are already the standard for auto racing. A typical cable, such as TE’s SPEC 55 cable, uses a cross-linked ETFE insulation and jacket offering temperature ranges to 150°C or 200°C and excellent resistance to fluids. The thin-wall construction allows weight reduction without compromising performance. While both the commercial auto industry and the military are starting to use aluminum wire and cable for weight savings, they do not yet find widespread use in autosports.
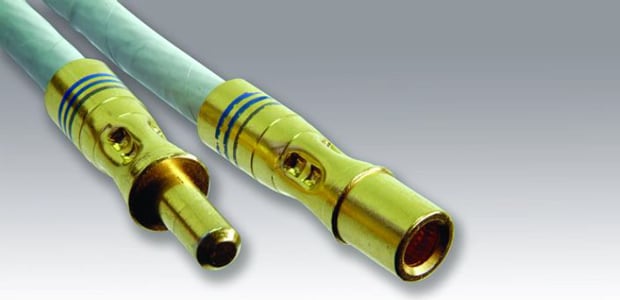
Aluminum wire is seen as hard to work with. Its bend radius is not as tight as copper’s and there are concerns over reliably terminating it due to cold creep. Yet contacts that counteract cold creep to form a reliable, gastight connection are available. Aluminum has only 60 percent the conductivity of copper so a larger conductor is needed to achieve the same current-carrying capacity. Even accounting for this, aluminum will be about half the weight.
Electrical Noise
Addressing EMI: Three Approaches
While shielding has been used sparingly in race cars, newer technology is creating new levels of electrical noise that must be dealt with. High-current energy recovery systems, for example, are a source of electromagnetic interference (EMI).
1
Separation
Increasing separation between the EMI source and susceptible wires and electronics. With the limited space in a car, this approach is impractical in most cases.
2
Shielding
Since shielding adds weight, it is often used on an as-needed basis instead of standardizing on shielded cables. This can be done with a copper overbraid slipped over the cable and terminated to a connector’s backshell. The braid forms a low-impedance path to ground to EMI. TE recently introduced a lightweight braid system that offers weight savings of up to 50 percent over traditional braid.
3
Fiber Optics
This is inherently immune to EMI. In addition, fiber-optic cables are significantly lighter than copper cables. Both glass and plastic optical fibers are candidates for application in autosports. Glass fibers have the advantages of higher bandwidth and higher operating temperature range—with some specialty fibers as high as 700°C. Disadvantages are that they are harder to work with. While glass-fiber cables are robust and available in ruggedized versions, some care must be taken in routing them and observing bend radii. Cable construction can overcome many of these drawbacks to allow glass-fiber cable to withstand the rigors of building, maintaining, and racing a car. Plastic optical fibers are less expensive both in the cable itself and in associated electronic transceivers. Widely used today in commercial auto networks, they are also more forgiving of mechanical abuse and tight bending. The main drawback is temperature range, with standard POF cable limited to 85°C and high-temperatures versions ranging to 125°C.
Integrated Solutions
If composite connectors deserve a new look, so do composite enclosures as a viable alternative to aluminum for housing electronic control units and other systems. The initial attraction of composite enclosures is weight savings—a carbon-filled polyphenylene sulfide composite enclosure can be 40 percent lighter than an aluminum one. Composite materials are strong and can be tailored to provide exceptional impact resistance, tensile strength, bending resistance and so forth. They may be sturdier than aluminum counterparts because they are not easily dented or deformed. Replacing metal enclosures with composites gives you all the mechanical and electrical benefits of metal, but with the added bonuses of lower weight, corrosion resistance, and lower costs.
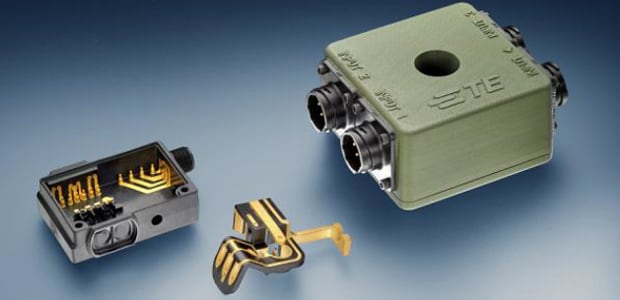
New capabilities and new material formulations give you more options. Fillers, ranging from traditional carbon fiber to microspheres and carbon nanotubes, allow custom tailoring of the enclosure to help achieve the best balance of weight versus electrical, mechanical, and environmental performance. Advanced molding permits standoffs, integrated connector shells, partitions, and other three-dimensional features to be created. Selective metallization allows circuit traces, shielding, and even embedded antennas to be cost-effectively integrated into the enclosure. Three-dimensional molding and selective metallization provide additional weight savings beyond the basic advantages of composites.
Conclusion
Interconnection technology continues to advance, offering new levels of weight savings for autosport applications. More importantly, what is old is new again. Technologies that were thought deficient in one respect or another have evolved. Do not rely on yesterday’s conventional wisdom. Composite connectors and enclosures, fiber optics, braid shielding, and aluminum wire all deserve fresh evaluation. A benefit of working TE is that we take a systems-level approach to interconnections. A couple of grams added here can save kilograms elsewhere. It is the final product that wins the race, not the individual components.