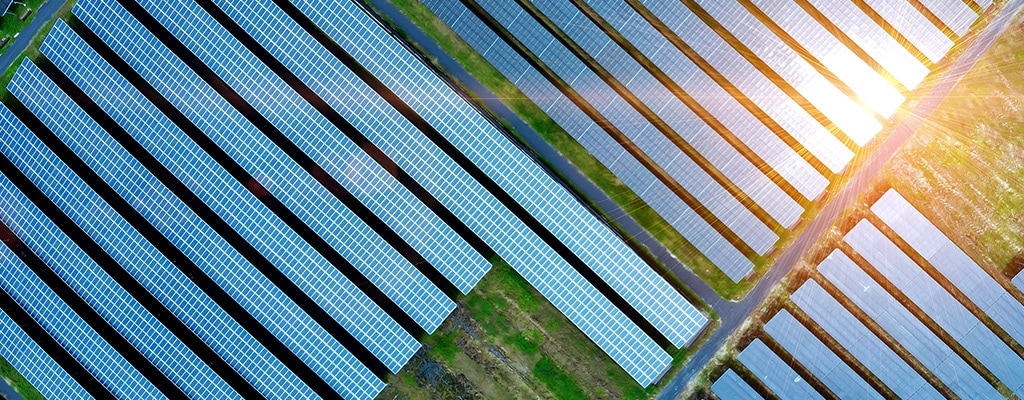
Case Study
Powering Efficiency Through Innovation
A large solar Engineering Procurement and Construction company (EPC) has been tasked with making sure to control the costs associated with the installation, operation and maintenance of the solar plant – on a site prone to flooding.
Accelerating a Solar Farm Installation
TE's new Customizable Trunk Solution helps a 140-Megawatt solar farm in the Midwest USA to simplify and accelerate electrical connection installations – a welcome improvement against the backdrop of particularly challenging site conditions.
The Challenge
One of the US's largest power generation companies contracted a global engineering, procurement and construction (EPC) company to build a 140 Megawatt solar farm on time, keeping labor time and cost under control – and ensuring a maximum voltage drop of 1.5%.The on-site installation involved more than 250 workers over a period of more than a year.
The solar farm construction site, located in rural Arkansas, is prone to flooding, routine thunder and lightning storms, seasonal tornadoes and extended heat waves. In addition, the COVID-19 pandemic created additional delays that threatened to put the entire installation several months behind schedule.
To overcome these challenges, the EPC selected TE's Solar Customizable Trunk Solution (CTS), that uses a centralized trunk-bus architecture, providing a significantly more simple overall wiring architecture compared to the traditional approach.
140MW
To be Produced by this Solar Farm
350 K
Solar Modules to Install
1.5%
Maximum Voltage Drop to Achieve
THE SOLUTION
The CTS system greatly eases the installation, thanks in part to Gel Solar Insulation Piercing Connectors ,which do not require any cable insulation cutback or stripping, saving important labor time. The Powergel-filled clamshell covering the IPC protects the connections from moisture ingress for their service lifetime.
Using this system, on-site technicians report that they require an average of only two minutes to install two IPCs. This includes cleaning the cable, testing it for continuity, setting the IPCs by hand tightening, using a cordless impact wrench to tighten the shear bolt connectors to the specification, applying the gel box enclosure, testing the continuity at the jumper connector, and cutting the end string to length.
In addition, to prevent the threat of frequent standing water, the wiring and the cabling are installed within above-ground cable hangers running East-West and North-South.
We are able to install 10 IPCs and terminate a Trunk Bus Disconnect (TBD) to close a circuit in less than 20 minutes, so it’s been an extreme time saver.
- Site Project Manager
THE OUTCOME
Thanks to the CTS system, the time and labor required to install the electrical portion of this solar farm were greatly reduced.
Another important benefit of the system is that it reduces the number of connections, which helps to minimize current leakage and the voltage drop across any entire solar farm. For this particular project, the CTS architecture is expected to help the solar farm meet its target 1.5% maximum voltage drop for the entire DC-collector distribution network.