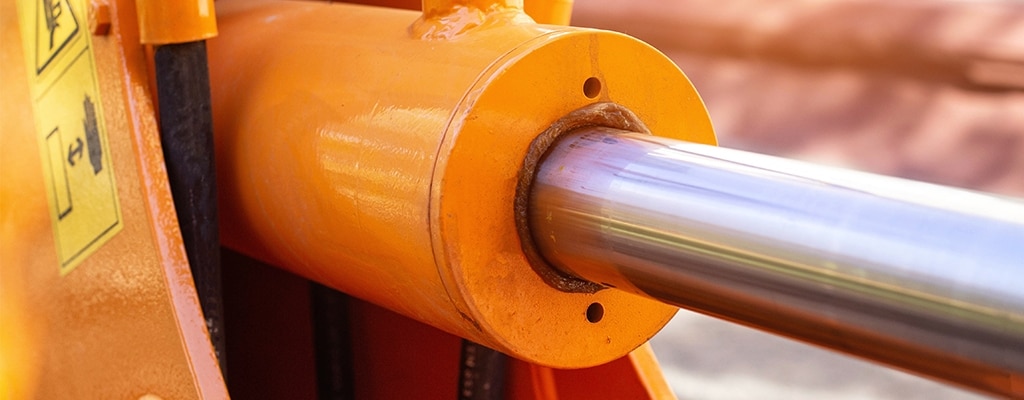
Hydraulic Pressure Sensors
TE Connectivity manufactures pressure sensors, transducers and transmitters for hydraulic pressure measurement applications.
Hydraulic sensor applications typically host various challenges for the mechanical construction of the sensor as well as the external environment. TE Connectivity (TE) manufactures pressure sensors in standard and custom configurations to withstand those challenges using MEMS sensing technology. The sensor is constructed taking a single bar of high strength stainless steel, milling the threads and hex on the outside, then boring the center of the metal for the fluid to flow into. The thick metal diaphragm isolates the liquid or gas to the sensing element. Silicon strain gages are applied to the opposite end of the bored hole to measure the deflection of the metal to produce a linear output signal. Combining this feature with strain gages that offer a high raw output signal, the sensor can be packaged with excellent proof (4X) and burst pressure (10X) capabilities, high cycle life, and long-term stability in standard packages.


Mechanical Packaging
One example is the AST4000 Industrial Pressure Sensor; it is available with 1/4" NPT Male, 7/16-20 UNF (SAE4) and 9/16-18 UNF (SAE6) process connections. TE can integrate a welded stainless steel restrictor plug inside the pressure port in order to reduce the inside diameter orifice size to protect against pressure transient common to hydraulic systems.
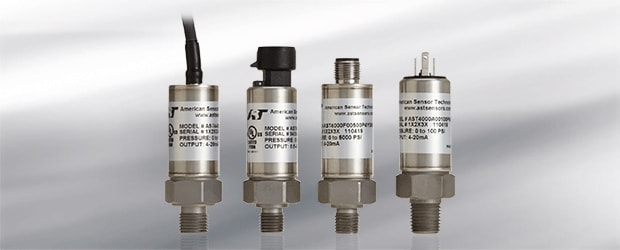
AST4000 pressure transducers
For example, if a fork lift has a full load on the forks and drops the load onto a concrete floor at full speed, the hydraulic system will see a pressure transient exceeding the limits of the pressure sensor. The restrictor plug dampens the pressure spike and protects the diaphragm of the sensor. The TE restrictor plug, also referred to as a snubber, is on the inside of the port rather than an added adapter. This can reduce the overall length and weight of sensors that use external restrictor plugs.
Electrical Packaging
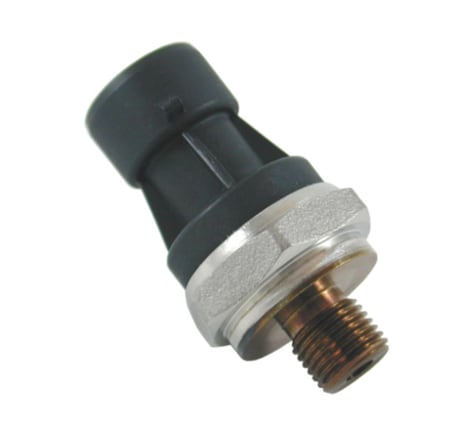
M7100 Pressure Transducer
The product features a welded housing, to shield from electrical interference and protect the electronics of the sensor from application environments and tough installations. The electronics of the pressure sensor also have EMI (Electromagnetic Interference) and RFI (Radio Frequency Interference) protection to the latest CE standards for industrial equipment. This family of hydraulic pressure sensors offers flexibility in the connection type. With a variety of cable lengths, the customer can connect to their electronics with ease. Depending on the output signal, TE will recommend maximum distances to run the cable to limit signal loss. TE also offers a full line of connectors that are integrated into the housing of the pressure sensor including: DEUTSCH DT04, M12x1, PT06A, and DIN. For OEM requirements, TE can also offer a custom cable assembly with specific cable lengths and integral connectors.
Environmental Conditions
A customer can package a standard pressure sensor with the electronics sealed from the outside environment. Known as sealed gauge, the pressure sensor is calibrated to the barometric pressure of the date of calibration. This will prevent moisture and dust from entering the pressure sensor for gauge pressure sensors. Because gauge pressure sensors are referenced to the atmosphere, they typically "breathe" through a vent tube in the cable jacket or through a hole in the connector. Sealing the pressure sensor is common for hydraulic uses because the pressure ranges are high enough that the difference in barometric pressure from location-to-location and day-to-day is insignificant as a percentage of the measurement range. The better trade-off is to protect the sensor from humidity, dust, ice, and high pressure wash-down. In summary, TE pressure sensors and transducers can be built to last through the rugged conditions common to hydraulic systems. By reviewing the application and environment of the sensor, TE can help to provide a solution.