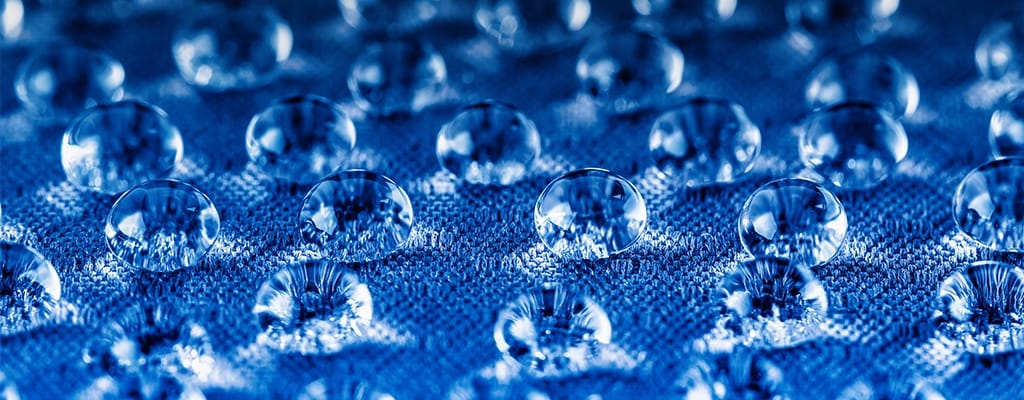
Hydrophobic vs Hydrophilic: PDMS Surface Modification for Microfluidic Chips
It’s not hard to figure out why PDMS has become a preferred material for microfluidic device applications. It’s highly biocompatible, elastic, optically transparent, easy to fabricate and inexpensive.
But despite its many benefits, PDMS has one decidedly repulsive characteristic: hydrophobia. Hydro-phobia. Fear of water?
“Hydrophobic” means that PDMS naturally repels aqueous solutions and that’s a big problem for many biomedical applications. Hydrophobic surfaces:
- Tend to absorb molecules which can lead to inaccurate analytical measurements.
- Inhibit liquid flow through micro channels which can necessitate the use of pumps on microfluidic chips.
- Prevent proper droplet formation.
These are serious issues because for many biomedical microfluidic applications, it is desirable for surfaces to be “hydrophilic,” which means the surface bonds more easily with aqueous solutions. Hydrophilic surfaces attract molecules and have high surface free energy, thus the flow of liquids is favoured.
So, despite its many benefits, it is necessary to treat PDMS surfaces to make most biological assays perform correctly within microfluidic devices.
What is Wettability?
In microfluidics, you will likely hear the term “wettability” used interchangeably to describe hydrophobic and hydrophilic surfaces. Wettability simply describes whether a surface wants to attract or repel liquid. If a surface repels liquid, it is considered to have low surface wettability (hydrophobic). If the surface has an affinity for liquid, it is considered to have high surface wettability (hydrophilic).
Wettability is measured by the angle at which a drop of liquid sits upright on the surface. If you imagine pouring a few drops of olive oil into a stainless steel pan, it quickly spreads out (high surface wettability) and has a low contact angle to the surface of the pan. Now imagine water droplets beading up on a leaf (low surface wettability). Surface wettability is primarily impacted by surface roughness, heterogeneity or solution impurities and there are various ways to correct for these issues.
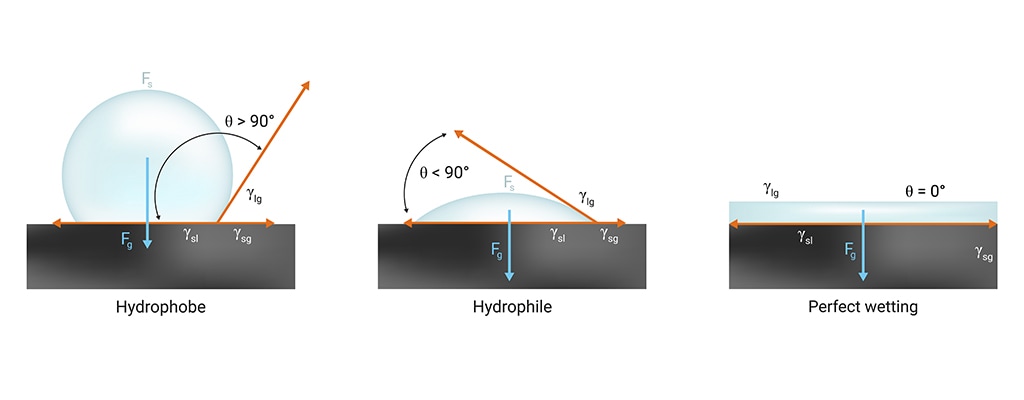
Hydrophilic Surface Coatings for Microfluidics
Bulk PDMS polymer is naturally hydrophobic, yet most biological tests and experiments require a homogenous mixture of aqueous solutions with biological sample. To make this happen effectively, the channels or surfaces within the microfluidic device must be made hydrophilic. Various ways exist to achieve this (we will discuss in a moment) but the benefits of doing so are:
- Improved wetting and spreading of fluids within a device, which can be useful for creating precise flow patterns.
- Coatings can be useful for reducing cross-contamination and absorption/adsorption from the PDMS polymer.
- Better performance of certain types of chemical reactions or separations, such as those that involve highly-polar or highly-charged molecules.
- Creation of stable droplets or emulsions, which can be useful for certain types of chemical reactions or sample handling.
Sometimes Phobias Are a Good Thing… Hydrophobic surfaces are sometimes desirable in microfluidic applications as they can be used to create barriers that control the flow of fluids, optimize flow patterns or prevent cross-contamination.
PDMS Surface Treatment Methods
Surface treatments for PDMS fall into two categories. The surface material can be directly modified or the surface can be coated. The most common methods for making PDMS microfluidic surfaces more hydrophilic (more wettable) include:
- Oxygen Plasma Treatment: This process uses oxygen plasma to etch the surface of the PDMS. Immediately thereafter, the PDMS is permanently bonded to another PDMS or glass substrate. After 15-60 seconds of treatment, the surface becomes hydrophilic . Plasma is the most commonly used technique.
- UV/Ozone Treatment (UVO): UV light and ozone are used to oxidize the surface then immersed in water to retain wettability. It also removes organic contaminants from polymer surfaces.
- Polymer Coating: This involves adding a coating to the surface using a hydrophilic polymer called PVA. This is typically done on non-PDMS surfaces however.
Making It Stick
It's worth noting that these methods may change the mechanical properties of the PDMS and therefore care should be taken to optimize the conditions for specific application. Plasma treatment, in particular, can result in rapid hydrophobic recovery of the PDMS surface so it’s not suitable for all applications. Other techniques exist but have not been widely applied to commercial microfluidic applications. Coatings can be difficult to apply and hold for periods of time, especially in small microfluidic channels. They are also sensitive to pH and temperature variations, which can affect their performance over time.
Surface Coating Methods
Spin Coating
This is a simple and widely used method in which a substrate is coated by spinning it at high speeds while in contact with a liquid coating solution. This method can be used to apply both hydrophobic and hydrophilic coatings to microfluidic channels and surfaces.
Dip Coating
This method involves immersing a substrate into a coating solution and then removing it at a controlled rate, allowing a thin film of coating to form on the surface. One drawback to this method is that it can result in a non-uniform coating.
Spray Coating
This method involves spraying a coating solution onto a substrate, which then forms a thin film of coating on the surface. This method is commonly used to apply hydrophobic coatings to microfluidic channels and surfaces.
Each of these methods has its advantages and disadvantages, and the choice of method will depend on the specific application and the properties of the coating being used.