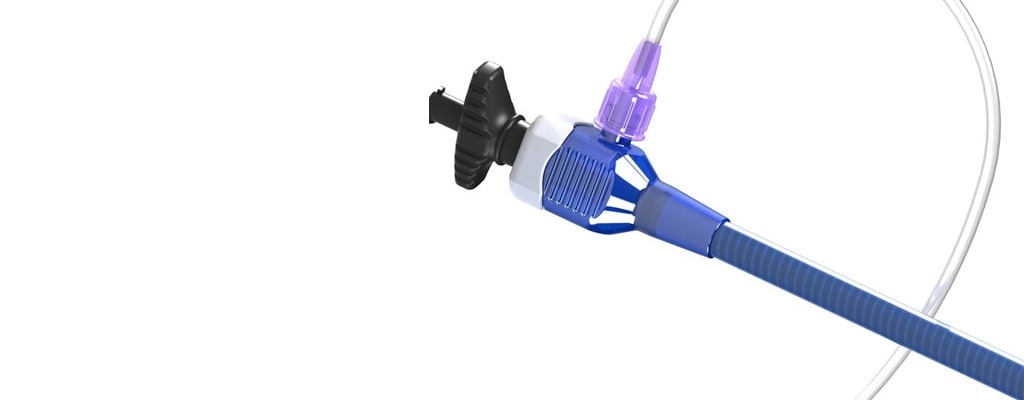
Essential sheath design considerations
Learn about the essential design considerations when designing customized sheaths intended for large bore applications.
TE is a leading outsourcing partner for minimally invasive access & delivery devices including specialty sheaths used in Structural Heart, Electrophysiology and Endovascular applications. We manufacture content for 2 of every 3 TAVRs globally, serving key market leaders. As experts in the design of customized sheaths for large bore applications these are some of the essential design considerations we have learned. Firstly, specify access requirements - radial, femoral, contralateral, expandable, apical or dual combination. Understanding how and where the sheath will be used clinically provides the first design insights to create a product and performance specification. Key design characteristics to keep in mind are how your device will guide through tortuous anatomy. Optimizing for pushability, torque, kink resistance, trackability and distal tip design requirements should all be considered at this point.
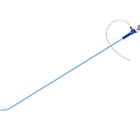

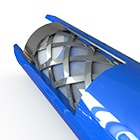
Next, What is being delivered? Understanding what is being delivered, whether it be a mechanical, biological or hybrid implant, defines how to optimize sheath performance for flow rate and perfusion. The sheath design should be optimized to minimize vessel trauma while considering the ID and OD profile for implant delivery. Sheath performance can be enhanced by combining custom material selections, creating unique designs to balance flex & kink, forming an atraumatic distal tip, and lowering insertion forces using lubricious coatings. Thirdly, consider ergonomics and ease of use for physician. How will the physician control the device, advance, position & then deploy the implant to the precise target location. Introducing proximal directional control using a handle will allow for a more precise delivery to these sites. During the prototyping phase, an engineer should consider an ergonomic hub and handle design with enhanced distal features such as marker bands & fillers to increase visibility while using fluoroscopy.
Finally, designing for manufacturability (DFM) ensures the best manufacturing processes and disciplines are being leveraged during the design process and the sheath can be made consistently, at volume, maintaining tight tolerances. If you want more insight on designing a sheath, email our team of design experts that are the most knowledgeable in their field and collaborate for your specific technical focus!