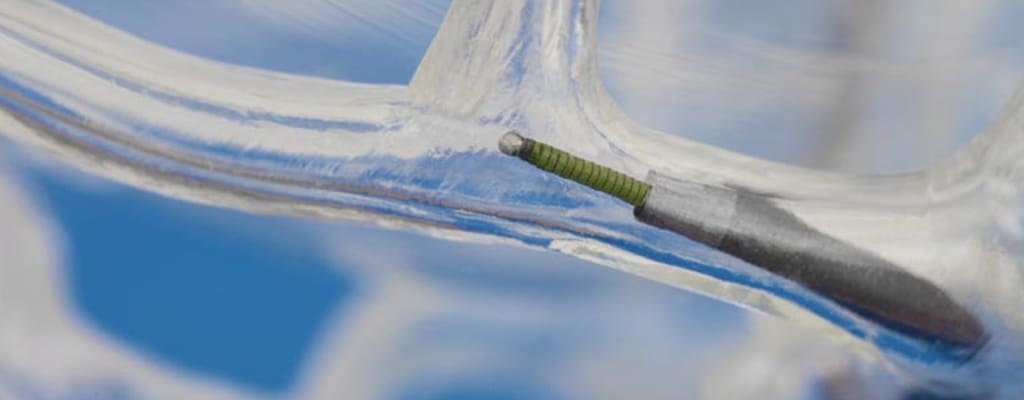
A fresh perspective in guidewire design
Learn how TE works with our customers from concept to commercialization, and support our design process with a complete range of in-house development and testing capabilities.
As the industry's 2nd largest contract manufacturer for guidewires, more than 3 million guidewire products and assemblies are provided by TE each year. In conjunction with our deep expertise in guidewire manufacturing, our design team provide innovative guidewire solutions from simple vascular guidewires to complex applications. Working with our client from concept to commercialization, we support our design process with a complete range of in-house development and testing capabilities. Our design team relish complex guidewire challenges, from custom pre-shaped guidewires for TAVI and Mitral Valve applications to low profile neurovascular wires. Complex guidewire applications call for an optimized balance in performance, summarized below.
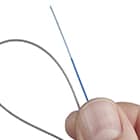
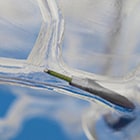
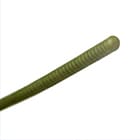
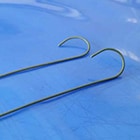
Optimized balance
Complex guidewire applications call for an optimized balance in performance, summarized here
Trade Offs | Technical Solutions | |
---|---|---|
Distal Tip Tip stiffness v track End finish v cost |
Access, Support or Delivery; Soft to medium tip stiffness; Conventional or standard tip end finish & cost | Coil & corewire tip design, shapeability, radiopacity Laser, Plasma welding; molding; atraumatic |
Main Body Stiffness - balance of track, kink resistance, pushability, torqueability |
Normal to standard stiffness; purpose and level of rail support necessary | Corewire profile & material; Coil & material (heat treat); Mulit-material; Variable stiffness customization Transition; Customize torque control & direction |
Lubricity Cost v Deliverability |
Marginal moderate, high level of lubricity necessary for delivery v cost | Hydrophilic; Hydrophobic; Silicone; Parylene |