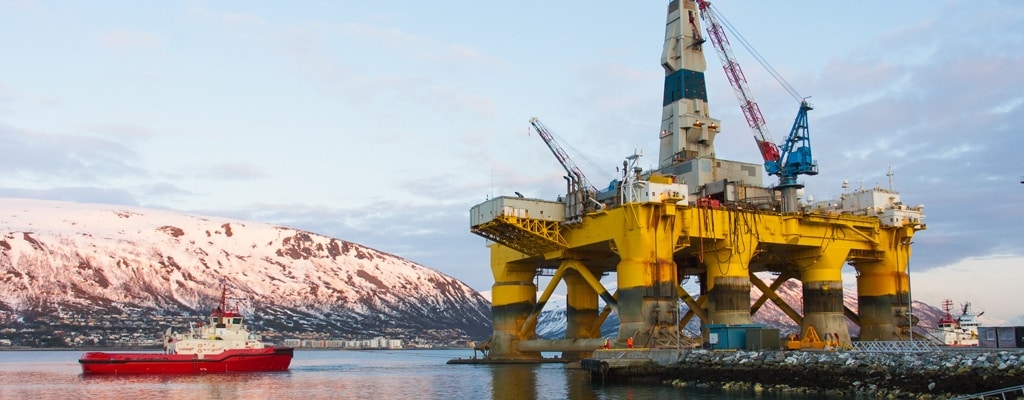
Trend Insight
Reliable Performance for Deepwater ROVs
New technologies in insulation and optical packaging allow umbilical cables to supply more power to ROVs – and support increasingly sophisticated capabilities.
As offshore activity continues to migrate into deeper waters and more remote locations, every aspect of exploration and development faces increasing challenges and levels of complexity. Most headlines on this subject are dominated by platform and riser technology evolution, the trend to next-generation drill ships, and augmenting production capabilities to include subsea processing. All of these involve incredibly complex solutions and will continue to revolutionize the industry; still, their application use and success will continue to rely on remotely operated underwater vehicle (ROV) evolution that can keep pace and deploy those technologies into reality.
33"
Bend radius of TE's several-layered umbilical cable.
2771
Pounds of weight in water – per 1,000 feet – for TE's umbilical cable.
10k
PSI of hydrostatic-pressure resistance for TE's STEEL-LIGHT armoring.
Working in Deepwaters
Consider the basic challenge of physically placing an ROV into the deep water areas necessary to perform its tasks. Where traditional WROV’s operate in waters around 2,500 meters deep, today’s activity is increasingly taking place in depths closer to 4,000 and even 5,000+ meters. One can readily appreciate the increasing size, weight, and powering capacity of umbilical cable needed to support this activity.
Withstanding Harsh Conditions
An umbilical cable for ROVs needs to meet a range of mechanical and environmental requirements not commonly experienced in other applications. At deepwater levels, temperatures are typically between 0 and 3°C. Pressures are also a concern. At 2,000 meters, the pressure of ocean water exceeds 2,900 psi (2000 N/cm2). Add in the long lengths of the cables and the need to withstand twisting and other movements, you can see the tensile loads on the cable are quite challenging.
Packaging the required elements in an umbilical assembly involves protecting them both mechanically and environmentally. At the same time, the design should be no larger or heavier than necessary and should be flexible to accommodate the movement of the ROV. Umbilical cables typically also serve as the main lift cable for ROV. The design challenge is to manage the tradeoffs between achieving a mechanically robust cable and minimizing size and weight.
Understanding Umbilical Cables
Given the complexity of the design and the mission critical need for reliability, only a handful of companies have earned the trust of the global ROV community to produce such cables. Smaller, lighter cables simplify shipboard deployment by reducing the space required for winching equipment and cable storage. Since deepwater umbilical cables are several thousand meters long, a 10% reduction in a cable’s diameter can significantly reduce the required deck space.A high-performance umbilical cable typically contains multiple types of elements to handle power, control, video, and telemetry. Thus you will find a mixture of larger conductor power cables, twisted-pair and multiconductor elements, coaxial cable, and fiber-optic cable in various combinations to meet the specific needs of the application.
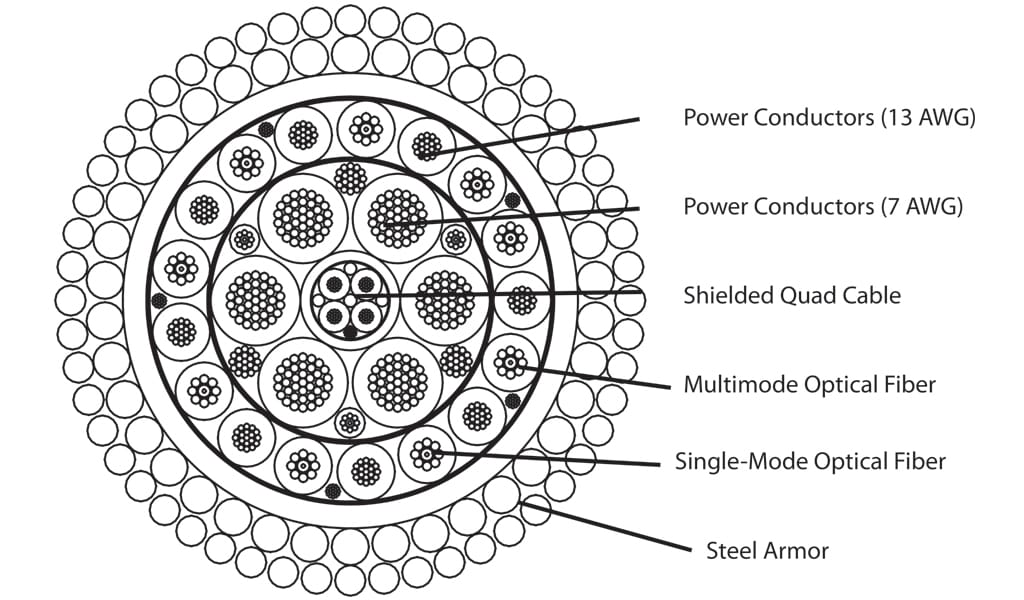
A typical umbilical cable is an armored assembly containing signal conductors, power conductors, and optical fibers.
Defined by Diameter – to Maintain Concentricity
An umbilical cable is typically constructed in several concentric layers. The image above shows a type of construction designed by TE Connectivity (TE) that combines power, multimode, and single-mode fiber-optic cables, and a shielded quad cable in a double-armored cable. As you can see, this is a complex design and it is important that all elements work together in harmony to provide the required power, data, and mechanical criteria. Each layer is defined not by function, but by the diameter of each cable element to maintain concentricity. Some cables, for example, may have power cables near the core’s center, while others have them in outer layers. Maintaining concentricity is important both to clean, efficient winching and to achieving rugged flexibility.
Each layer is wrapped with a tape, typically an aluminum/polymer tape, and voids are typically filled with water-blocking materials. Not called out in the image above are drain wires and fillers. These are added as necessary.
The outer armoring serves as both strength members and core protection; it functions to disengage the cable elements from the overall tensile load placed on the cable. The cable is 1.670 inches (42.42 mm) in diameter. Its weight in water is 2,771 pounds per 1000 feet (4123 kg/km). It has a working load 35,000 pounds (156 kN) and a bend radius of 33 inches (84 cm). The bend radius is most important to the diameter of the sheave. Using the cable at smaller bend radii can increase fatigue resistance and shorten the service life.
Given the challenges of creating robust umbilical cables, designers use advanced simulation tools to analyze the mechanical and electrical performance. It is impractical to build multikilometer prototypes, so expertise in design and simulation are essential.
Current efforts in umbilical innovation are focusing on the cable’s core, looking for ways to pack more functionality into the same or smaller space. The engineers developing our Rochester Cable family of products, for example, are working with thin-wall insulation and fiber-optic packaging as key to next-generation cables.
Enabling Optical Communications
Optical fibers are finding increased use in umbilical cables because of the increased bandwidth they offer over long distances. While fibers have high tensile strength to withstand longitudinal pulling, they can be easily broken or damaged if not protected correctly. As a result, fiber-optic cables typically have their own armoring. While aramid yarn – the same strength members common with other fiber-optic cables – are used, more robust designs also use metallic armoring. The high hydrostatic application pressures can increase attenuation in a fiber.
Our Three Approaches
- Fiber in Steel Tube (FIST), which places the fiber in a solid stainless-steel tube to protect against hydrostatic pressures, high temperature effects and corrosive environments. FIST packaging is a loose-tube design, which can accommodate several fibers loosely held within the tube and encapsulated in gel. Because the fibers ‘float” within the tube, the length of the fiber is slightly longer than the tube to ensure low strain. FIST technology is the simplest and lowest cost approach. It maintains low strain on the fiber by decoupling stress on the tube from that on the fiber. If the cable stretches during installation or use, the excess fiber can accommodate the stretching without being strained. Loose tube designs also are very forgiving of extreme temperature excursions, but are less suited to the most rugged applications, such as extreme depths and extreme cable lengths. FIST also offers high density packaging of multiple fiber in the tube and, of the three options, is the easiest to terminate.
- STEEL-LIGHT armoring, which uses strands of precisely sized plow steel concentrically arranged around the fiber buffer to protect the fiber from breakage.
- ELECTRO-LIGHT armoring, which is similar to STEEL-LIGHT armoring but uses copper in place of steel. The copper can also be used for power to allow composite cables to be designed with a smaller outside diameter.
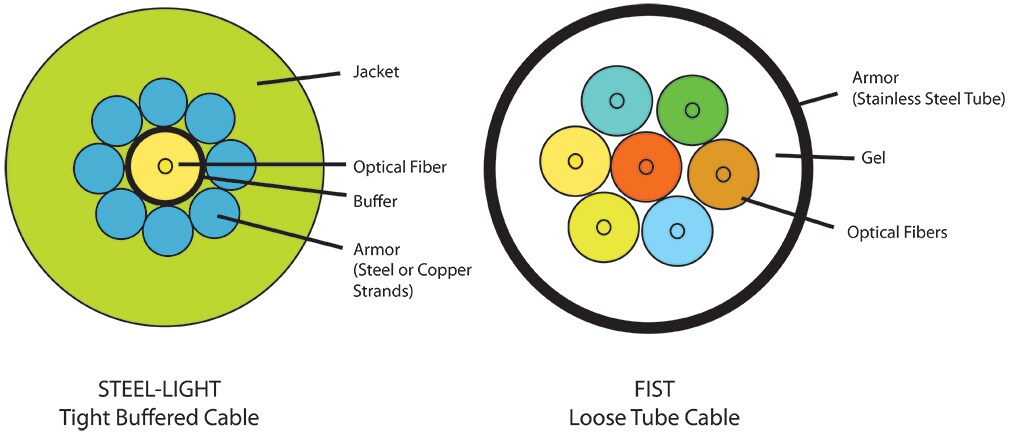
Innovative optical packaging makes application of fiber optics easier.
STEEL-LIGHT and ELECTRO-LIGHT fiber elements are both tight buffered approaches to packaging. Tight buffering, while requiring more careful manufacturing, provides better performance in highly dynamic applications and is the most rugged choice. STEEL-LIGHT armoring is the most rugged, designed to withstand hydrostatic pressures of 10,000 psi. Both STEEL-LIGHT and ELECTRO-LIGHT fibers have very small diameters, allowing them to be fit into interstices in the cable design. With some of newer small-diameter umbilical cables using thin-wall copper conductors, such spaces may not be available. FIST may be a better choice to minimize cable diameter in such cases. Picking the correct one of these three options means you will have solved many of your telemetry issues. It is a matter of weighing the tradeoffs required in ruggedness for a given application against cost, convenience, and cable size. Umbilical cable suppliers have the experience to guide you in the best choice for your applications.
More Power in the Core
As the capabilities of the ROV increase, the power needs of the ROV also increase. There are two ways to increase the power-handling capabilities in the core of the umbilical cable. First, you can use conductors of larger cross section. This will, however, increase the diameter of the cable. The second approach is to use thin-wall insulation in place of standard-wall cable. At TE, we use cross-linked polyethylene (XLPE) as an insulation on power conductors. Thin-wall insulation can achieve cable diameters that are in the range of 30% smaller than comparable standard-wall products. While conventional wisdom dictates that thicker insulation be used as power handling increases, new materials and new processing methods have overturned such wisdom.
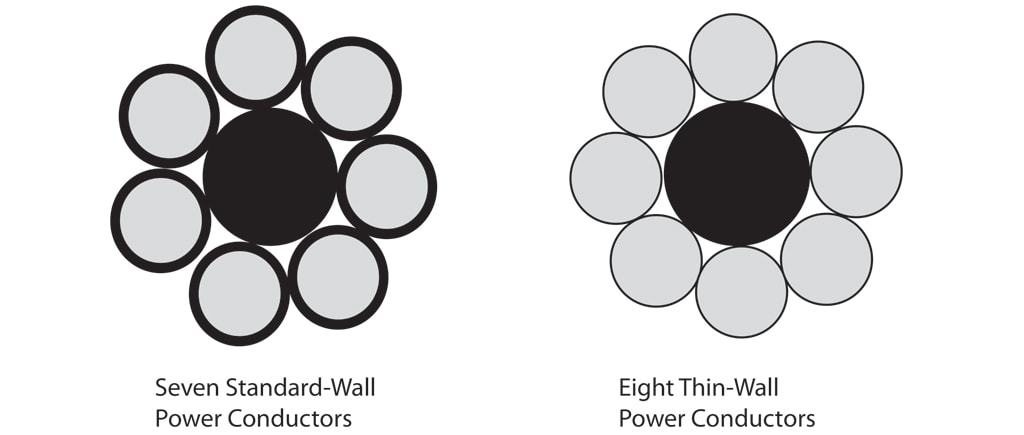
Thin-wall insulation technology allows more power and functionality to be packed into the same space.
Umbilical Runs Deep
Thin-wall technology is well established in the military and aerospace industry, which offers many of the same demands for rugged performance as deepwater applications. Thin-wall insulation has excellent abrasion resistance, excellent thermal stability over a wide temperature range, and electrical properties required for power-carrying applications. Thin-wall insulation technology allows more power and functionality to be packed into the same space.
With thin-wall-insulated wires, it becomes possible to add additional conductors – and thereby provide more power to the ROV – to the umbilical without increasing its size. Thei images above show an example in which eight thin-wall conductors fit into the same space as seven standard-wall conductors.
As the need increases for deepwater ROVs to support research and oil and gas exploration and production, umbilical cables are supporting the needs for robust performance. New technologies in insulation and optical packaging allow umbilical cables to supply more power to the ROV and to support the increasingly sophisticated capabilities. This translates into more capable deepwater devices with a wider range connected by a compact cable delivering more power and more data-handling capabilities.
Contributing Authors
- Mark Casselton, Product Manager, Marine and Offshore Cables
- Sage Wadke, Global Director, Marketing and Business Development, Aerospace, Defense, and Marine