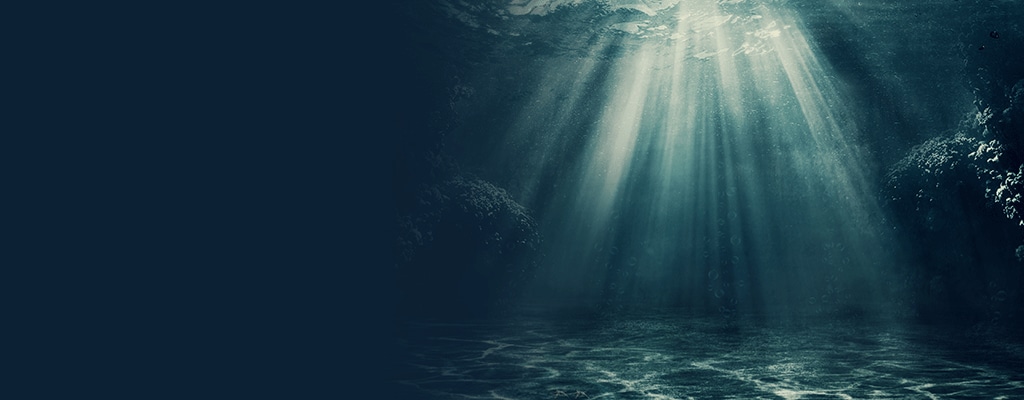
Trend Insight
Sensors in contact with seawater
Learn about the causes of corrosion for sensors in seawater applications and how to design solutions around the challenges.
Seawater attacks metals at varying water depths, resulting in corrosion accelerated by the varying levels of oxygen, temperature, pH, salinity, biological activity, electrical conductivity and velocity flow rates present in seawater at different depths. Sensors, including pressure and linear position sensors, are widely used for control and safety functions at various sea depth levels for applications in offshore platforms, desalination systems, mooring cables, sea floor well heads as well as oil and gas gathering systems. During operation, sensors can be submerged in seawater at varying depths based on tides - from shallow waters at a few tenths of feet to meters below surface and in deep waters below 1000 feet. To operate in these environments, sensors must be constructed from corrosion resistance materials so that units can provide continuous information under the hostile conditions of the seawater. As demand for sensors to be in contact with seawater and seafog increases for applications such as loading systems, sub sea mooring cables, control valves, chokes, desalination plants and platform stability, selecting the correct sensor materials depends upon the proper selection of alloys suitable for the application and service environment. Whether corrosion comes from varying depth levels, galvanic effects or biological attack, matching the proper materials for service application is the top priority for good sensor performance over a long period of time. Material selection is often affected by system reliability requirements, availability, cost and manufacturability.
Seawater Characteristics Leading to Corrosion
Containing high levels of salts, dissolved oxygen, carbon dioxide and micro-organism life, seawater environments are highly corrosive. The corrosion rate can depend upon a combination of global location, temperature and micro-organism activity. Additional sources of corrosion can come from stagnant or polluted conditions that often promote sulfate-reducing bacteria (SRB) that can affect sensor materials’ performance. The major constituents of seawater containing -ions are chloride, sulfate, bromine and bicarbonate, while +ions are sodium, magnesium, calcium and potassium. Seawater increases localized corrosion of stainless steels and other active passive materials as a result of dissolved chlorides and other salts. This type of corrosion can be in the form of pitting, crevice or intergranular.
Corrosion by Micro-Organisms in Seawater
Microbially Induced Corrosion (MIC) is a very serious problem that effects sensor operation based on different service conditions and materials used in sensor construction, especially low grade austenitic stainless steels. MIC is normally found on welded joints and leads to failure of the weld if not checked and treated in time. MIC is a corrosion process involving the degradation of the material. In oxygen-rich environments, aerobic bacteria are active; anaerobic bacteria can be found in low oxygen. The bacteria can be described as slime forming, acid producing, iron oxidizing, sulfate reducing, iron and nitrate reducing. There are hundreds of individual species of bacteria that form MIC. The colonies of MIC bacteria typically form local clusters on a sensor with the location identified as a rough spot, inclusion site, corrosion site or cut on the material surface. These colonies, feeding on oxygen, iron and manganese, produce a sticky paste. This sticky paste invites a host of other biological and non-biological species that, in turn, start to attack the sensor surface leading to crevices, oxygen and ion concentration cells to form, that results in corrosion.
SRB bacteria can be very corrosive and aggressive when environmental conditions are right for its growth, enabling it to convert sulfate to harmful sulfide. To grow, SRB relies on Acid Producing Bacteria (APB), the main initiator of MIC. APB consumes oxygen and produces low molecular weight, organic acid and alcohol. It is this organic acid that SRB eats and starts the process of producing hydrogen sulfide. The sulfide, acting as a cathode to steel, attacks the steel surface of a sensor in an electrochemical corrosion process and starts to consume anodic iron. This results in the pitting and creation of crusty tops or flakes on the surface of the sensor material. The process accelerates as seawater temperature ranges between 25° and 41°C, subject to location around the world. Titanium and nickel-based superalloys offer much better protection for sensors against localized corrosion. In some cases, Alloy 400 and Alloy K materials have been used successfully in shallow warm waters, particularly in the Middle East and Africa.
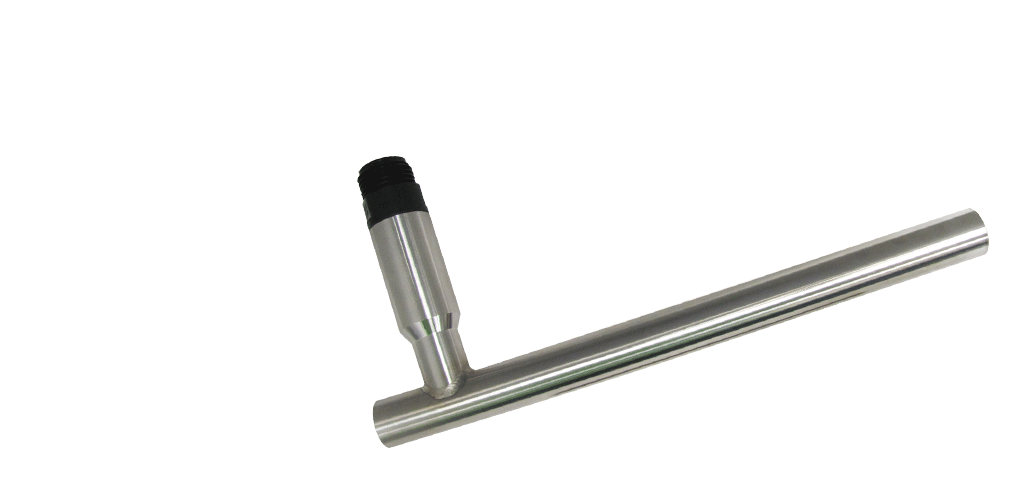
Many common stainless steels, such as 304 and 316, should not be used for sensors that will be in direct contact with seawater. Duplex steels with higher alloy content and Pitting Resistance Equivalent factor (PREN) value greater than 40 have be used as an alternative to stainless steel; however, this alloy does not guarantee long reliable sensor life in new deep sea and Arctic applications. For PREN calculations, the key elements - chromium (Cr), molybdenum (Mo) and nitrogen (N) - are used as the weighted factor, with its multiplier to determine the overall value. The common formula used is: PREN = %Cr + (3.3 x %Mo) + (16 x %N).
PREN = %Cr + (3.3 x %Mo) + (16 x %N)
Nickel-based Super Alloys
Alloy 625 and Alloy C276 are two primary alloys within the nickel superalloy family that offer excellent protection against corrosion due to higher content of nickel, chromium and molybdenum. These two materials form the choice of materials for sensors as well as all other critical components when it comes to reliability and trouble-free operation for many years. In comparison to stainless steels and duplex steels, these alloys cost more; however; they offer total immunity against localized corrosion as well as oxidizing and reducing media.