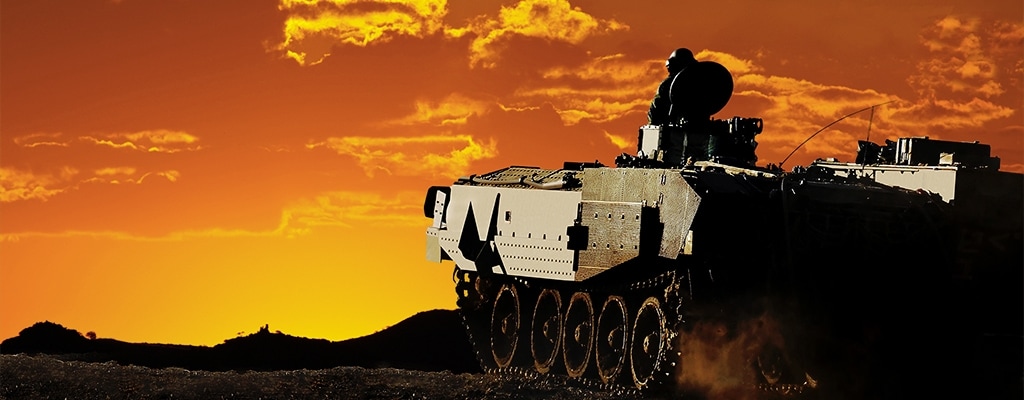
Product Insights
Built for Reliability and Repeatability
MIL-DTL-38999 connectors are corrosion-resistant with material and plating options that have a very high salt spray rating. A rugged design for harsh environments, D38999s are built to reliably transfer power, signals, and data.
To understand D38999 connectors, it’s helpful to first understand what these do. These mil spec connectors are used to attach cables to one another or to electric boxes in a wide variety of harsh environment applications, including space propulsion systems, satellites, industrial equipment, offshore and subsea production technology, as well as in military vehicles, ships, planes, and handheld and communications equipment. Our D38999 connector provides reliability in technology that must operate without unexpected failure, such as in aircraft and other transportation systems.
The main carbonite of a D38999 is aluminum, which has evolved to include stainless steel, bronze, and composite shells. Stainless steel is used for higher temperatures and vibration elements such as engines. Bronze is resistant to high slat corrosion and used in applications such as marine, while composite is used to reduce aircraft weight. The inserts are made of thermal plastics that can be configured in a variety of contact arrangements. The polymers that make up the insert assembly are an excellent dielectric material, the seals are made of silicone-based rubber, and the contacts are made of copper alloy with gold plating.
This assembly helps ensures optimal electrical performance and robust sealing capabilities. Alternative mil-spec materials are composite shell connectors, which provide the same performance as the aluminum shell connectors. In use since the product first came on the market in the 1970s, D38999 connectors have the durability of 500 to 1500 mating cycles. While there are numerous applications that only mate the connectors a few times of the life of the product – which can be 20 to 30 years – these connectors and their robust features are durable with reasonably high mating cycle capabilities.
Our D38999 connector provides reliability in technology that must operate without unexpected failure.
The Advantage of Reliability
When selecting D38999s, it’s crucial to think about the applications. This includes military ground vehicles that often require a quick turnaround when coming in for service. Operators more concerned with keeping equipment running within budget might choose a lower-priced option that not manufactured for conditions involving extreme mechanical use as well as high temperatures, vibrations, and corrosive fluids. In such cases, sacrificing reliability for cost could have significant consequences.
At TE Connectivity (TE), our design heritage with DEUTSCH 38999 connectors goes back to being involved in writing the original specs. Built in accordance with military standards, qualified to MIL-DTL-38999, and ranging in size from 9 to 25, our D38999 connectors are machined for precision – in the shells, contacts, and inserts.
This precision makes our machined parts and our molded design rugged, for reliable performance under rapid temperature fluctuations, atmospheric and altitude humidity changes, shock and vibration, and exposure to chemicals, such as jet fuel. It also gives installers the assurance that they can install the product as intended.
Our Philosophy of Repeatability
Our design philosophy is grounded around repeatability. When TE acquired DEUTSCH in the early 2010s, our manufacturing process enabled us to improve D38999 repeatability through automation and process control. At TE, our manufacturing approach focuses on repeatability at scale, which enables us to provide each customer with the same level of product quality. In our D38999 connectors, our DEUTSCH inserts are manufactured with contact retention feature – called fingers, which grab onto the copper contacts – made of molded thermal plastic. For the product to perform reliably, production of the fingers need to be reliably repeatable. Using molded plastic fingers helps reduce risk during assembly.
There is a common industry variation on our D38999 connector design, which instead of molded plastic uses copper clips sandwiched between layers of inserts that hold the contacts. With this variation, inserting metal clips into the product can lower repeatability and add complexity in production. And considering that many popular D38999 connectors are often equipped with dozens of contacts – even as many as 128 contacts, using a design with inserted metal clips could also affect the ease and accuracy of field installation.
The advantage of our molded plastic design, as we see it, comes down to our manufacturing process. By streamlining assembly to focus on efficiency and repeatability, we can achieve a level of consistent reliability in parts manufactured, which is particularly important when making products in succession.
Select Applications for TE's DEUTSCH Legacy Connectors
Understanding EN3645
What is EN3645? The EN (European Norm) 3645 is the European version of the D38999 , with some slight adjustments. The EN3645 and the D38999 have equal requirements, and these are sometimes interchanged. Because we have facilities worldwide, we can service our customers faster by being near their locations.
EN3645s are also qualified according to JN specifications for Eurofighter applications, such as JN1153 for composite connectors and JN1034 for aluminum connectors. These are also qualified according to VG95319 German specifications.