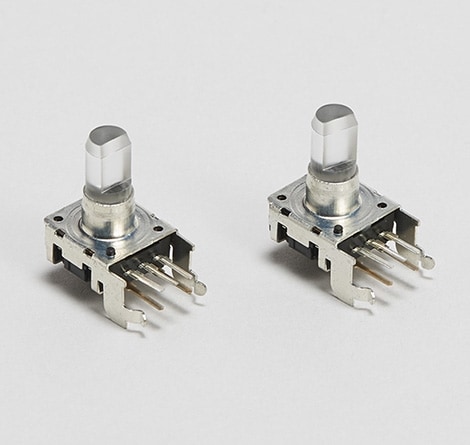
Control and monitor mechanical systems
A rotary encoder is an electromechanical device that measures the number of rotations, the rotational angle, and rotational position. A rotary encoder detects speed and position by converting rotational mechanical displacements into analog or digital output signals which are then processed. Our portfolio of rotary encoders comprises mechanical incremental encoders, which are used as digital potentiometers.
Rotary encoders are commonly used in applications that require control of or monitoring of mechanical systems. These applications include motor feedback, in which rotary encoders control the direction and speed of electric motors and can control multiple axes of motion; cut-to-length applications; filling applications for use in bottle-filling machine factories; conveyors, which are used in a multitude of industries, especially manufacturing; lift industry applications; photographic lenses; ball screw positioning for things like machine tool placement, industrial lifting jacks, and printer carriage positioning; and robotics applications where rotary encoders are used for precise positioning of robotic joints.
What are Rotary Encoders?
There are two primary kinds of rotary encoders: absolute and incremental. Both types of encoders are used to measure the angular position in a variety of industries and applications, such as machine tools, automation, packing, printing, and label and marking equipment.
Understanding Absolute Encoders
Product Overview
In an absolute encoder, the angle position is retained, whether the encoder is powered or not. Even if a movement is made without power, then reapplied, the encoder maintains its original position. Absolute encoders can be single turn or multi-turn. Not only is it required to know the position over one turn of the shaft, but the total number of turns made. Multi-turn encoders are useful for applications that require complex or lengthy positioning measurements. Single-turn encoders are better suited to short travel applications that have a required position measure within a single encoder turn. Advantages of absolute encoders include non-volatility, i.e., the true position is not lost unless power is lost; a continuous position ready is not necessary, battery back or gear function is not needed, high resolution, and no traditional optical disk is needed.
Understanding Incremental Encoders
Product Overview
An incremental encoder is an electromechanical and operates by turning the angular position of the shaft into digital or pulse signals using an optical disk. A specific number of pulses are created per revolution, with each pulse serving as an incremental correspondence to the solution. An incremental encoder can measure the change in position, but it cannot measure the absolute position. Advantages of incremental encoders include lower cost than absolute encoders, they are simpler to use than absolute encoders, and they have high noise resistance.
Because absolute and incremental encoders take similar measures, these components can be used in the same applications. These applications include automated assembly lines, cut to length applications, jacks for railroad cars, packaging machines, and printing applications.
Encoders are used in many industries and in a range of applications, including the following: Automation, cranes and construction, drink technology, factory applications, heavy-duty application, industrial applications, machine building, motorsport, robotics, and quality control.