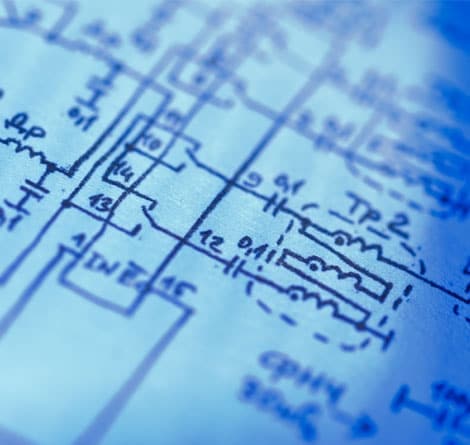
Insights on relays, from our engineers
Our team publishes a wide range of technical documentation and guidelines, explaining how to specify, select, test, and maintain relays in a variety of applications.
Featured Application Note
Technical Documents on Relays
-
Relay Coil Suppression with DC Relays
This application note has been written in response to the numerous application problems resulting from improper relay coil suppression. The typical symptom is random "tack" welding of the normally-open contacts when switching an inductive load or a lamp load with high inrush current.
-
Automotive Applications
Automotive applications can be classified into resistive loads, capacitive loads and inductive loads. The current curve of resistive loads is specified by the load voltage and load resistance. Capacitive loads have a high inrush current and a low steady current. Therefore lamps are counted to the capacitive loads, because the cold filament has a significantly lower resistance, than the hot filament. Inductive loads are characterized by an exponential current increase and a remarkable switch off arc, induced by the demagnetization of the magnetic circuit of the load. Power supply relays (clamp relays) can switch or feed a mixture of different loads.
-
Beware of Zero-Crossover Switching Transformers
A zero-crossover solid-state relay may be the worst possible method of switching on a transformer or a highly inductive load. Evidence1 has come to light that zero-crossover turn-on of such loads can cause a surge current of perhaps 10 to 40 times the steady state current, whereas turn-on at peak voltage results in little or no surge.
-
Coil Suppression Can Reduce Relay Life
This application note deals with problems related to the methods used in de-energizing electromagnetic relay coils, particularly when a solid state switch is used, and how they affect relay life.
-
Coil Voltage and Temperature Compensation
Relay and contactor coils are usually wound using copper wire - and copper wire has a positive temperature coefficient as shown in the formulas and chart following. Most coils are also powered by a relatively fixed voltage. Thus, assuming the voltage remains constant, increasing temperature will result in higher coil resistance and decreased coil current.
-
Contact Arc Phenomenon
Incandescent lamps, inductive loads like motors and solenoids, capacitive loads like electronic ballasts and switching power supplies, etc. can exhibit very high initial surge currents upon energizing. This can be up to 10X the steady state current or more and is especially troublesome should the contact closure randomly occur near the peak of the voltage sine-wave. Welding of contacts due to such excessive surge current is often the result. Relays for such applications usually need to be oversized or specially designed to handle the high inrush current relative to the relatively modest steady state current. This usually results in extra control cost and increased space usage.
-
Contact Load Live Peformance Enhancement
What precisely is an electric arc? How does it ignite and what causes it to extinguish? How does an arc affect the life of relay contacts? These are some of the questions that we will discuss here. We hope to help you better understand how to obtain the longest life possible from relay contacts such as these.
-
DC Relay Coil Power Reduction Options
It is often desirable to reduce total control power consumption and reduce heating. One way to do this is to reduce relay coil power consumption. Following are two methods used to accomplish that for DC coil relays. It is important to note, however, that reduction of coil power by any method reduces the relay’s ability to keep the relay armature seated, hence reducing the relay’s shock and vibration tolerance.
-
Determining Relay Coil Inductance
Relay users often desire to know the inductance of the relay coil they are using so they can determine the energy released by the coil upon deenergization.
-
Mounting Termination and Cleaning of PCB Relays
Incorrect handling and mounting of printed circuit board relays can alter the relay’s operational characteristics and result in premature relay failure. Additionally, recommended conductor widths and PC board cleaning procedures play an important part in assuring that the assembly will yield long, reliable service.
-
Operating DC Relays from AC and vice-versa
A relay coil is copper wire wound many times on and around a bobbin in which an iron core is situated. When a voltage of sufficient magnitude is impressed across the coil, the coil and core develop magnetism which attracts the armature. The armature, in turn, controls contact movement. Depending on the total length of the wire and its unit cross-sectional area, the coil exhibits a certain amount of resistance to the flow of electric current.
-
Proper Coil Drive is Critical to Good Relay and Contactor Performance
Throughout this Application Note, references to “relay(s)” may generally be assumed to apply to “contactor(s)” as well. Similarly, little is specifically mentioned regarding application of “telecommunications type relays”. Generally, the need for proper coil drive applies equally to contactors and telecommunications relays except that increased internal and coil temperature rise due to contact load is seldom an issue in telecommunications applications.
-
Relay Contact Life
Relay contacts are available in a variety of metals and alloys, sizes and styles. There is no such thing as a universal contact. The relay user should select contact materials, ratings, and styles to meet, as precisely as possible, the requirements of a particular application. Failure to do so can result in contact problems and even early contact failure.
-
Temperature Considerations for DC Relays
Relays and temperature are intertwined. When a relay is exposed to various temperatures, its operating characteristics change dependent upon the temperature. The most notable changes occur in the pick-up voltage (VPI) and coil resistance (RC). The coil winding of a relay is produced with copper wire and thus the coil resistance varies with the temperature coefficient of copper.
-
Venting Sealed Relays
Unless specifically advised otherwise by TE Engineering, all sealed relays (that have a venting means provided by the manufacturer) must be vented after PCB assembly and cleaning, but before use electrically, in order for published ratings to remain applicable.