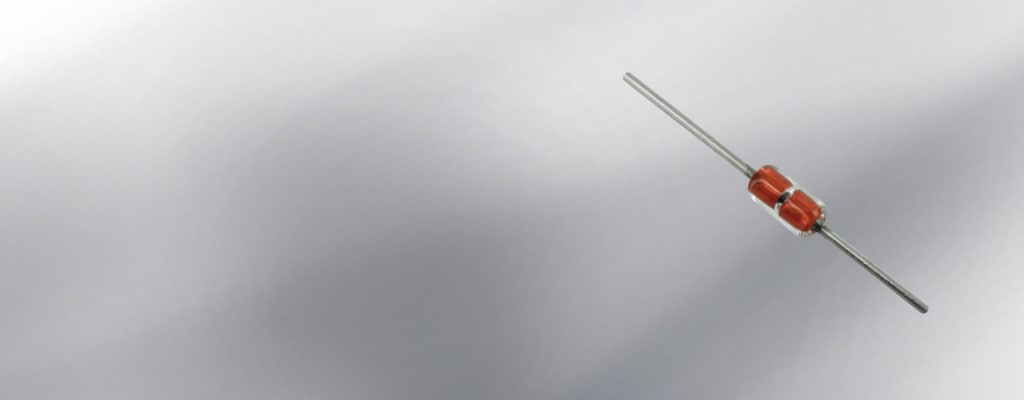
NTC Ceramic Sensor Processing
Learn about the processing techniques for manufacturing NTC ceramic temperature sensors.
TE Connectivity (TE) employs advanced ceramic processing techniques and proprietary formulations for the manufacture of high-stability electro-ceramic thermistor materials. These materials are introduced into a range of high performance NTC thermistor components and probe assemblies for select applications.
There are two factors that are of key importance to customers who rely on thermistor NTC sensors for critical applications.
- The sensor must behave in the specified manner
- The thermistor should continue to provide the same electrical characteristics throughout its operating life as when it was first manufactured.
Based on these key deliverables, TE has invested significant engineering resources into the research and development of high stability electroceramic materials that can be utilized for the most demanding applications.
Powder Processing
Proprietary techniques used in powder processing produces a consistent particle size which is suitable for high densification processes employed later in the ceramics production process. The key focus during powder processing is improving the flow ability of granules by adjusting granule size distribution and increasing the bulk density. Also, improving deformability of granules can be achieved by adjusting the binder system and the careful selection of suitable organic additives.
Ceramic Processing
The spray-dried powder is compacted using a variety of different technologies to provide a geometry suitable for NTC chip wafer production. During the final stage of ceramic processing the electroceramic materials are densified using state-of-the-art fabrication techniques. High pressure is applied during the ceramic fabrication process for a specified amount of time in order to improve the mechanical properties of the ceramic.
The temperature, pressure and process time are all precisely controlled to achieve the desired mechanical and electrical properties. The high densification process allows voids to collapse under the high pressure conditions. The surface of the voids fuse together to effectively eliminate porosity and achieve near 100% theoretical density.
Key Advantages of Densification Technology for NTC ceramics
- Densification of electroceramic bodies to ~100% of theoretical density
- Reduction of internal porosity in ceramic body
- Improves the physical properties of the ceramic components for electrode application
- Electrical performance is greatly enhanced with high resistance stability
- Repeatability and tolerance distribution is greatly improved
- Delivers advanced electroceramic materials with fine grained microstructure
The impact on ceramic densification can be seen when a polished cross-section of the ceramic is compared to two different competitor NTC products. The densification of the electroceramic can be visually compared and the difference is significant. The electroceramic NTC material from TE can be seen to achieve close to 100% density with no porosity noted from high magnification photographs (scale 100 µm).
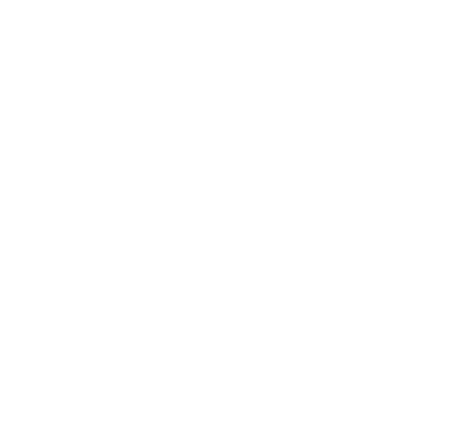
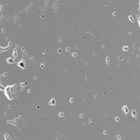
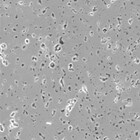
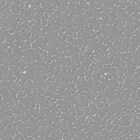
STABILITY TESTING
DO-35 10KΩ NTC Beta3977: High Temp Storage Conditions and Thermal Shock Testing
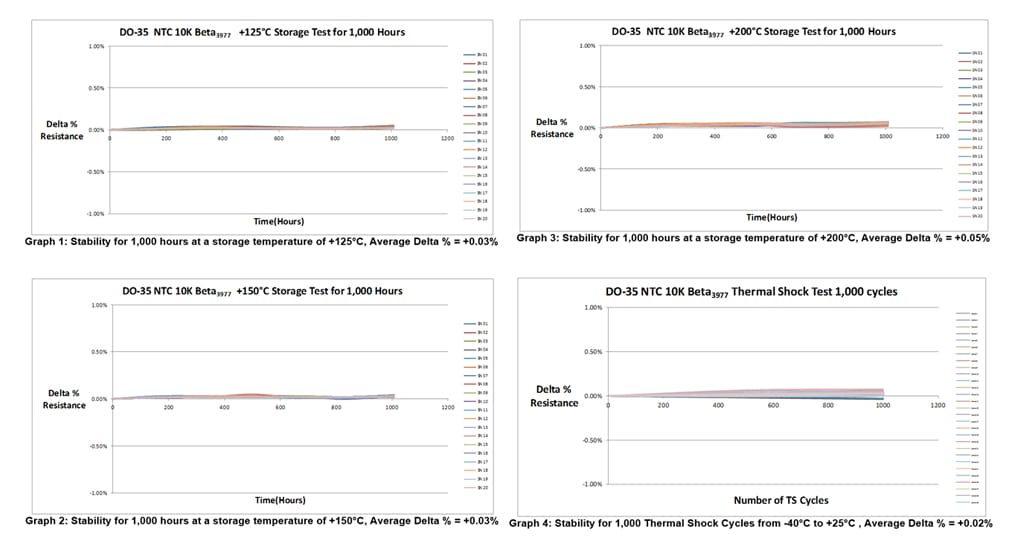