Development of Autonomous Mobile Transportation System
ABSTRACT
Autonomous mobile robots are playing an important role in flexible material transportation. The mobile robot developed based on the Simultaneous Localization and Mapping (SLAM) is fully capable of map building, pathing finding and its optimization, as well as obstacle avoidance, and is most flexible and agile to automate the factory logistics for digital transformation on automatic warehousing and transportation for materials. We have investigated in the applications of navigation technologies with the mobile robots, and has developed solutions from strategic perspective to automate the water spider processes.
PROBLEM STATEMENT
Conventional material transportation approach is to use the water spider to transport materials from the Material Super Market or Warehouse to the Production Areas. Fig.1 illustrates a general water spider process with operator to push/pull a trailer loaded with boxes of materials at a TE Plant. Normally, the materials are not directly transported to the production lines, but first to a buffer area, as shown in Fig.2. The production lines fetch the materials from the buffer area, and once checked with no sufficient quantity of materials to support production for the next two or more hours, the production line would put a tag at the buffer area to notify the request on materials. Material keepers check the availability of materials at the buffer area once they see/receive the material request, the material keepers would help to apply for materials from the Material Super Market or Warehouse, with water spider allocated to transport the materials. Obviously, the conventional approach is labor intensive and with low efficiency. Besides, there are generally many different types of materials to manage, and it takes a bit effort to find/locate materials, which in further affects the efficiency of the material transportation. What’s worse, the manual water spider might not respond to the request of material transportation timely, which might cause the production lines to wait for materials to arrive, and affects the productiveness of the production lines.
Automation and Digital Transformation would largely help to improve the material transportation efficiency and reduce the response time. Autonomous Mobile Robots that are able to move around autonomously and be enhanced with digital connections to the production lines and MES systems, are excellent alternatives to replace the manual water spiders. There are generally four major different kinds of navigation technologies: Fixed Path Navigation, Laser Target Navigation, Inertial Navigation and SLAM Navigation, as shown in Table 1. The Fixed Path Navigation method, which requires to construct magnetic tapes to be pasted on the floor to guide the mobile robot to follow, has the lowest mobility and flexibility; the Laser Target Navigation, which relies on Laser Target to reflect back laser beam to the robot for precise localization of the robot, is low in compatibility in the environment, and once the Laser Target position is changed or blocked by other obstacles, it would be very difficult to navigate the mobile robot precisely; the Inertial Navigation, which requires to construct the floor by installing magnetic nails or pasting QR codes, has better compatibility to the layout change of the surroundings, but is only reachable to the areas that are constructed with magnetic nails or QR codes; the SLAM Navigation, which is fully capable of updating the map in real time for path finding, obstacle avoidance and autonomous navigation, has the highest compatibility with the environment and flexibility to autonomously move around, and is an optimal Navigation Technology for flexible material transportation in the production areas which has frequent interactions with humans or other mobile devices. Table 1 makes a comparison among different Navigation Technologies. Our direction is to develop SLAM Navigation based Autonomous Mobile Transportation Systems for TE.
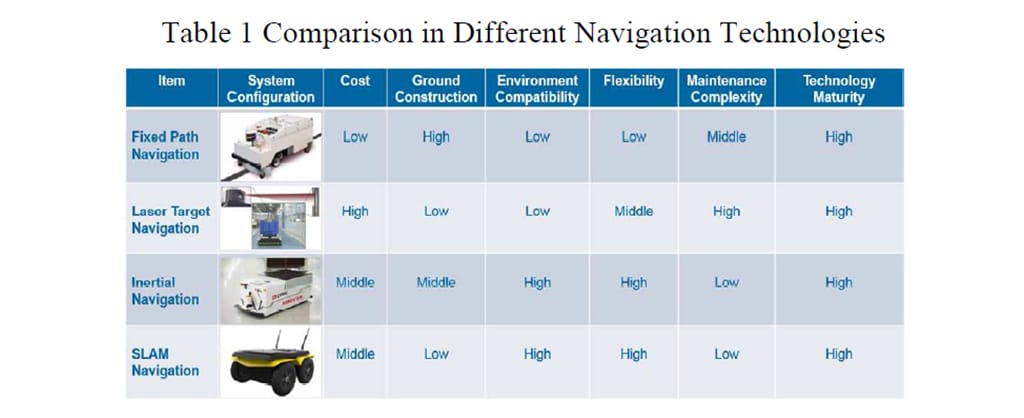
METHODS AND RESULTS
Start-of-Art Navigation Technology on Mobile Robots
Navigation, which is based on the localization and environment perception, is a high-level research topic in robotics. Generally, a global path planner is good in producing an optimized path, but poor in reacting to unknown obstacle. Incontrast, a local / reactive navigation method works well in dynamic and initially unknown environment, but is inefficient especially in complex environment[1]. This research studies both global and local path planning algorithms, and proposes the hybrid navigation method.
Global path planning has been well-studied in academic area and applied in many practical cases. Graph-based algorithm is a commonly used branch among them, such as Dijkstra[2], A*[3] and Voronoi[4] graph, which are usually used in a bounded area. Artificial Potential Field (APF)[5] methods use more information of the environment and are suitable in realtime navigation.
However, trajectories generated by APF are generally not optimal. Markov Decision Process is a probabilistic method in which the decision only relates to the last state and has nothing to do with more previous states. Besides, some other global path planning algorithms [6] are discussed to figure out the path to reach the goal.
Local path planning deals with obstacle avoidance at a local environment. Model Predictive Control (MPC) [7] is increasingly applied in navigating the autonomous mobile robots due to its robustness and convergence on path planning. The key idea of MPC is to predict the future with customized model to do path planning and then apply initial control corresponding to the chosen trajectory for the mobile robot. Dynamic Window Approach (DWA)[8], which evaluate each trajectory and select the one with highest score, is not only an independent algorithm but also a component of MPC. However, DWA assumes that all obstacles are static, which is not applicable for dynamic obstacle avoidance with relatively high speed. Algorithms like velocity obstacle and collision cones assume that obstacles move with deterministic velocity and acceleration.
Obviously, in most TE plants, there are relatively static layouts on the equipment and production lines with known environments, and also unpredictable moving of operators of devices, which are regarded as the dynamic obstacles, neither the global path planning nor the local path planning approaches would work well for the navigations of the mobile robots. It is necessary to develop a hybrid method with combined local path planner and global path planner to realize the navigation.
Basis of Autonomous Navigation – Map Building
When the autonomous mobile robot is deployed in an unknown environment to autonomously find the way to reach the goal, the robot has to traverse throughout the environment until reaches the goal. While some new goals are added and set, it is unwise to command the robot to traverse every time, which is high in cost of the computation time and storage space.
In addition, the goal is usually a relative position with respect to the mobile robot while navigating throughout the environment. Therefore, it is important to employ an environmental descriptor, for example the map, to record and describe the information of environment to get the robot to know where it is and where exactly to go. There are different variations
for the map, such as the Feature Map, Topology Map, Grip Map and the Appearance-based Method. Feature Map, which describes the environment with key points, lines or planes, contributes to lively visualization.
Topology Map describes the nodes and the connectivity of environment. Appearance-based Method calculates the pose of robots directly. Grid Map takes account of both the simplicity and visualization on representing the environment. Therefore, Grid Map is an optimal choice as environmental descriptor for the navigating the mobile robots. This section studies the approach for Mapping Building of an unknown environment to obtain a Grip Map.
With no prior knowledge of the environment, Simultaneous Localization and Mapping (SLAM), which constructs the map of the unknown environment while tracking the robot pose simultaneously, plays a vital role in map building. In our method, Rao-Blackwellized particle filter is used for SLAM to ensure the robustness and quality of mapping. One of the most common particle filtering algorithms is the Sampling Importance Resampling (SIR) filter. The mapping process with Rao-Blackwellized SIR filter are decomposed into following steps:
- Sampling: the current pose of the robot xt(i) is calculated with last pose of the robot xt-1(i) by the proposal distribution π(xt|z1:t,u0:t)
- Importance Weighting: each particle is formulated on its own weighting, as described by Eq.(1)

- Resampling: to prevent the infinite particles and ensure the convergence of the algorithm, the quantity of particles should be reduced, and the particles of low importance weightings are replaced by those of high for the resampling process.
- Map Estimating: The current map mt(i) is estimated with the historic observations z1:t and poses x1:t.
Therefore, the main idea of Rao-Blackwellized particle filter is to compute a posterior probability over maps and trajectories, as formulated by Eq.(2)
P(x1:t, m|z1:t, u0:t) = P(x1:t, m|x1:t, z1:t)P(x1:t|z1:t,u0:t) (2)
Where, u0:t is the sequential of odometry measurements including initial pose, z1:t is the sequential of observations, x1:t describes the potential trajectories and m represents the map.
A simulation environment is constructed to verify the map building algorithm, as shown in Fig.3. The mobile robot is moving around the free space, the environment is bounded by surrounding walls and the boxes inside illustrate different stations, which could be regarded as obstacles. The blue area shown in Fig.3 is the scanning range of the mobile robot. By commanding the mobile robot to move throughout this simulation environment, the Grid Map is built based on SLAM technologies, as shown in Fig.4.
Path Planning in Known Environment
With the availability of the map for the environment, the initial position of the mobile robot is often set as a Start Point, and the goal is set as the End Point at the map to construct the path to command the robot to follow. Finding an accessible path from the Start Point to the End Point and commanding the robot to the move along the path by considering the dynamics of the robot and surroundings, are called global path planner and local path planner.
In the process of global path planning, Dijkstra’s and A* algorithm are two major ways to search the shortest path, which are featured with breadth-first search and depth-first search respectively. They are briefly described as shown in Table 2.
Brief Description of Dijkstra’s and A* Algorithm
Table 2
Dijkstra’s Algorithm | A* Algorithm |
---|---|
(1) Set the initial distance value to each node: assign 0 to start node and infinity to others (2) Set the start node as current and mark all other nodesunvisited (3) For current node, find the nearest node whose distanceto the visited set is shortest. (4) Mark the nearest node as visited so that it will neverbe checked again (5) If the goal node has been marked visited, then thesearch is finished. Otherwise repeat the step of (3) |
(1) Set the initial node as current node. Calculate the weight for its neighbors by f(n) = g(n) + h(n),where g(n) is the cost of the path from the start nodeand ℎ(n) is the estimated cost from n to the goal (2) Set the node whose weight is smallest as the currentnode and continue the step of (1) (3) Repeat (1) & (2) until the goal is identified as thecurrent node |
No matter which method is chosen, an accessible path could be theoretically generated. However, an accessible path doesn’t mean an executable path. Local path planner builds a bridge between accessible path and executable path. In this research, the dynamic window algorithm is used, and the algorithm includes the following steps:
- Discretely sampling in the robot control space
- Predict what would happen for each potential samples with forward estimation
- Evaluate these candidate trajectories from the point of distance and the coincidence of global path
- Pick the trajectory with highest score
- Rinse and Repeat
For the generation of the executable path, the local path planner shows great advantage in avoiding obstacles. When the mobile robot follows the global path, local observations build local map so that new/unpredicted obstacles are marked on the local map. Then the local path planner would generate a local path to avoid interference with these obstacles. In this case, the robot can avoid both static and dynamic obstacles with low speed.
Simulation of Autonomous Navigation
A simulation environment is set up as Fig.3, and the map of the environment has been built up in Section II.B based on SLAM algorithm. The path planning algorithm is tested over the map, with Dijkstra’s algorithm implemented and verified in this part. First of all, the current pose of the robot is configured in the map, and the current pose is set as the Start Point.
The robot would be commanded to follow the path which is planned via global path planner after the goal is set. As shown in Fig.5, the blue path is global path from start to goal while the yellow one is local path that follows the global path. Based on several rounds of tests for verification, it is concluded that Dijkstra’s approach could generate an accessible global path
and local path generated by DWA could be constructed the executable path to align with the global path.
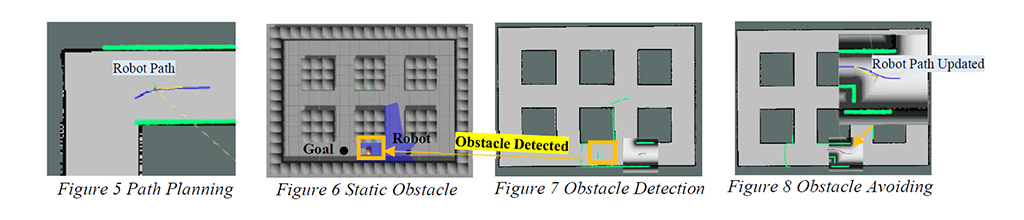
The capability to avoid obstacles is also evaluated here. As shown in Fig.6, an unpredicted obstacle, which is not marked at the map, occurs to be right in front of the robot. The obstacle is in the scanning range of the laser scanner, and is detected by the robot, as shown in Fig.7. In order to test whether the robot would be able avoid interference of the new obstacle and
pass by it, a Goal is configured right after the detected obstacle to check how the robot performs in reaction of the unpredicted obstacle to reach the Goal. By running the local path planner, a local map is generated as shown in Fig.8, with the obstacle updated in the local map, the yellow curve is the local path generated for the avoidance of obstacle. It could be
seen that the robot is not directly moving straight ahead to cause interference with the obstacle, instead it follows an adapted path by moving around the obstacle with no collisions with the obstacle. So here verifies the capability of the robot to passmby the static obstacle, it has also been tested to add some dynamic obstacles that are also able to move around the map at a relatively low speed, can could come across with the robot, the test results also show that the robot is able to update its local map with local path generated to avoid collisions with the dynamic obstacles. The simulation results verify the hybrid approach with combination of global path planner and local path planner on robot path planning and obstacle avoidance.
DISCUSSION AND KEY POINTS
Autonomous Mobile Transportation Vehicle
Key technologies developed and verified in Section II on map building and path planning with SLAM enhance the capability of autonomous navigation for the mobile robot. As compared in Table 1, the SLAM based navigation technology does not require to construct the floor with magnetic tape, magnetic nails or QR code, there is also no need to paste the laser target to the walls or fixed structures. It is fully capable to build the map of an environment automatically, and could handle well to avoid collisions with unpredicted obstacles that are not marked in the map. SLAM based mobile robot is the optimal alternative to be used to develop autonomous mobile transportation system.
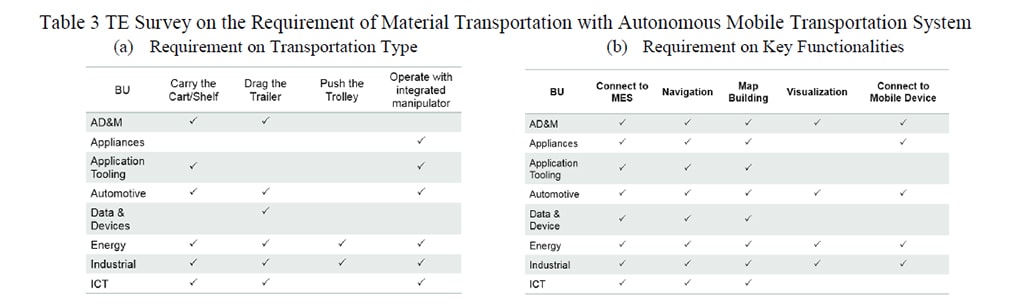
A survey has been conducted across TE business units on detailing the requirements of autonomous mobile transportation for materials. Some high priorities on the material transportation type are to get the mobile robot to carry the cart/shelf, drag the trailer, and to integrate a manipulator to operate the materials, as shown in Table 3(a). Key functionalities with high priorities to implement on the autonomous mobile robot are to connect to MES, navigate autonomously and build the map automatically, as shown in Table 3(b). Among all expectations, the automation of the water spider process with the mobile robot has been rated with high priority by Business Units. As shown in Fig. 9, the Water Spider Process has been the most
critical process for material transportation from the Warehouse / Material Super Market to Production Areas. Here proposes to develop latent type Autonomous Mobile Transportation (AMT) Vehicle based on SLAM navigation technology to carry the shelf for flexible transportation of materials as shown in Fig. 10. The Autonomous Vehicle is able to support a payload for more than 300 kg, and can run at a speed of 0.8 ~ 1 m/s at the plant. It is a highly efficient and effective alternative to replace the manual water spider process.
Autonomous Mobile Transportation System
With the availability of the Autonomous Mobile Transportation Vehicles, the key is to integrate the vehicles as part of the Autonomous Transportation System (AMTS) to develop turn-key solutions for TE plants. Fig.9 illustrates the overall process for material transportation. Generally, it takes operator to unpack the material boxes, and to sort the materials at the
warehouse, then transfer the sorted materials to the boxes to be stored at the Material Super Market, manual water spiders are employed to transport the materials from the Material Super Market to the Buffer Area. The production lines fetch the materials from the buffer area.
Considering the fact that almost all TE plants have not yet automate any part of the process
from warehouse to production line, here first proposes to automate the water spider process with the Autonomous Mobile Transportation Vehicle, as shown in Fig.10. Obviously, AMT Vehicle provide end-to-end material transportation automation solutions from the material super market to production line, the AMT Vehicle would be fast in response and efficient in material transportation, which significantly reduces the labor cost and saves the buffer areas that are required from manual water spiders.
To further enlarge the benefit of using AMT Vehicle on its capability to be digitally connected to networks. Here also proposes to transform the material requesting process from manual operation with paper works to a digital process. Since now it is common to see operators/technicians/engineers using the smart phones, here proposes to develop an App to be installed at the mobile terminals for material requesting and communication, as shown in Fig.11. For the sake of security in communications, the Apps and AMT Vehicles, as well as the server will be connected to TE local networks, with only authorized employees allowed to login the App or access the system for material requesting, communications, as well as monitoring.
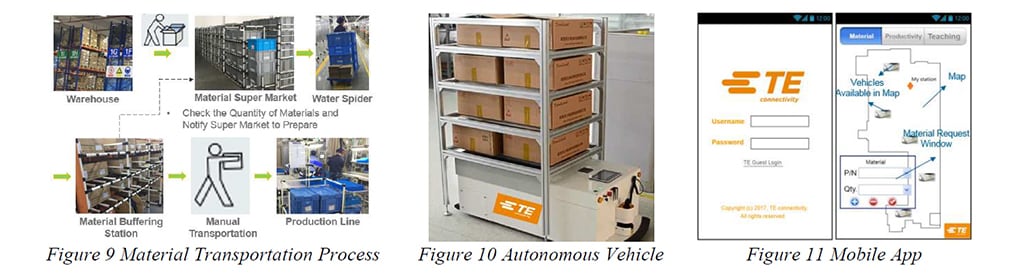
Therefore, the Architecture of the Autonomous Mobile Transportation System is proposed as shown in Fig.12. All AMT Vehicles are managed by the AMTS Central Coordination System for task allocation, path planning and traffic control.
Apps are also connected to the AMTS Central Coordination System, and once the Production Lines request materials via Mobile App, the operator at the Material Super Market would receive the request and prepare the materials in advance, afterwards the AMTS Central Coordination System would assign an AMT Vehicle to come to execute the task for material
transportations. After the AMT Vehicle successfully deliver the materials to productions lines, operators could click confirm to set free for the resource of this AMT Vehicle to be planned by the AMTS Central Coordination System.
ACKNOWLEDGEMENTS
The authors are grateful for the suggestions and instructions from Josef Sinder from Automotive BU, Tim Darr from AMT Harrisburg. The authors also appreciate Automotive Suzhou Team on introducing the requirement to implement material transportation automation for Automotive Suzhou Plant.
REFERENCES
[1] Wang, Lim Chee, Lim Ser Yong, and Marcelo H. Ang. "Hybrid of global path planning and local navigation implemented on a mobile robot in indoor environment." Intelligent Control, 2002. Proceedings of the 2002 IEEE International Symposium on. IEEE, 2002.
[2] Skiena, S. "Dijkstra’s algorithm." Implementing Discrete Mathematics: Combinatorics and Graph Theory with Mathematica, Reading, MA: Addison-Wesley (1990): 225-227.
[3] Duchoň, František, et al. "Path planning with modified A star algorithm for a mobile robot." Procedia Engineering 96 (2014): 59-69.
[4] Garrido, Santiago, et al. "Path planning for mobile robot navigation using voronoi diagram and fast marching." Intelligent Robots and Systems, 2006 IEEE/RSJ International Conference on. IEEE, 2006.
[5] Warren, Charles W. "Global path planning using artificial potential fields."Robotics and Automation, 1989. Proceedings., 1989 IEEE International Conference on. IEEE, 1989.
[6] Hoy, Michael, Alexey S. Matveev, and Andrey V. Savkin. "Algorithms for collision-free navigation of mobile robots in complex cluttered environments: a survey." Robotica 33.03 (2015): 463-497.
[7] Morari, Manfred, et al. "Model predictive control." Preprint (2002).
[8] Fox, Dieter, Wolfram Burgard, and Sebastian Thrun. "The dynamic window approach to collision avoidance." IEEE Robotics & Automation Magazine 4.1 (1997): 23-33.
Development of Autonomous Mobile Transportation System
ABSTRACT
Autonomous mobile robots are playing an important role in flexible material transportation. The mobile robot developed based on the Simultaneous Localization and Mapping (SLAM) is fully capable of map building, pathing finding and its optimization, as well as obstacle avoidance, and is most flexible and agile to automate the factory logistics for digital transformation on automatic warehousing and transportation for materials. We have investigated in the applications of navigation technologies with the mobile robots, and has developed solutions from strategic perspective to automate the water spider processes.
PROBLEM STATEMENT
Conventional material transportation approach is to use the water spider to transport materials from the Material Super Market or Warehouse to the Production Areas. Fig.1 illustrates a general water spider process with operator to push/pull a trailer loaded with boxes of materials at a TE Plant. Normally, the materials are not directly transported to the production lines, but first to a buffer area, as shown in Fig.2. The production lines fetch the materials from the buffer area, and once checked with no sufficient quantity of materials to support production for the next two or more hours, the production line would put a tag at the buffer area to notify the request on materials. Material keepers check the availability of materials at the buffer area once they see/receive the material request, the material keepers would help to apply for materials from the Material Super Market or Warehouse, with water spider allocated to transport the materials. Obviously, the conventional approach is labor intensive and with low efficiency. Besides, there are generally many different types of materials to manage, and it takes a bit effort to find/locate materials, which in further affects the efficiency of the material transportation. What’s worse, the manual water spider might not respond to the request of material transportation timely, which might cause the production lines to wait for materials to arrive, and affects the productiveness of the production lines.
Automation and Digital Transformation would largely help to improve the material transportation efficiency and reduce the response time. Autonomous Mobile Robots that are able to move around autonomously and be enhanced with digital connections to the production lines and MES systems, are excellent alternatives to replace the manual water spiders. There are generally four major different kinds of navigation technologies: Fixed Path Navigation, Laser Target Navigation, Inertial Navigation and SLAM Navigation, as shown in Table 1. The Fixed Path Navigation method, which requires to construct magnetic tapes to be pasted on the floor to guide the mobile robot to follow, has the lowest mobility and flexibility; the Laser Target Navigation, which relies on Laser Target to reflect back laser beam to the robot for precise localization of the robot, is low in compatibility in the environment, and once the Laser Target position is changed or blocked by other obstacles, it would be very difficult to navigate the mobile robot precisely; the Inertial Navigation, which requires to construct the floor by installing magnetic nails or pasting QR codes, has better compatibility to the layout change of the surroundings, but is only reachable to the areas that are constructed with magnetic nails or QR codes; the SLAM Navigation, which is fully capable of updating the map in real time for path finding, obstacle avoidance and autonomous navigation, has the highest compatibility with the environment and flexibility to autonomously move around, and is an optimal Navigation Technology for flexible material transportation in the production areas which has frequent interactions with humans or other mobile devices. Table 1 makes a comparison among different Navigation Technologies. Our direction is to develop SLAM Navigation based Autonomous Mobile Transportation Systems for TE.
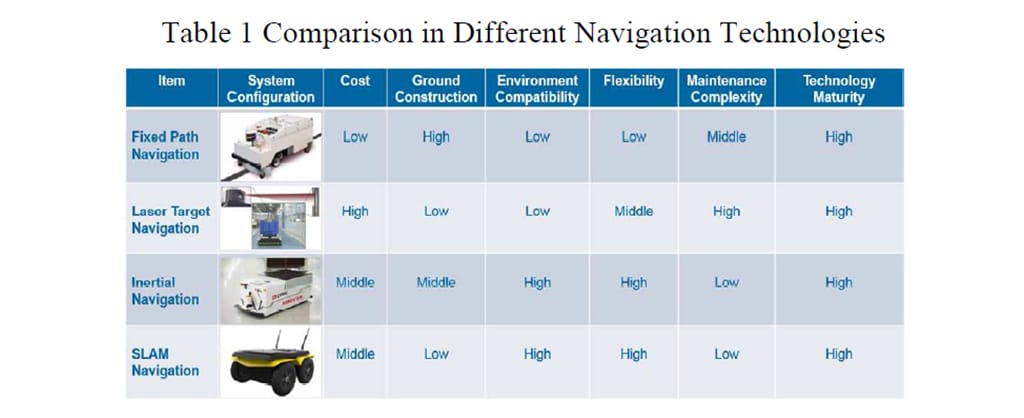
METHODS AND RESULTS
Start-of-Art Navigation Technology on Mobile Robots
Navigation, which is based on the localization and environment perception, is a high-level research topic in robotics. Generally, a global path planner is good in producing an optimized path, but poor in reacting to unknown obstacle. Incontrast, a local / reactive navigation method works well in dynamic and initially unknown environment, but is inefficient especially in complex environment[1]. This research studies both global and local path planning algorithms, and proposes the hybrid navigation method.
Global path planning has been well-studied in academic area and applied in many practical cases. Graph-based algorithm is a commonly used branch among them, such as Dijkstra[2], A*[3] and Voronoi[4] graph, which are usually used in a bounded area. Artificial Potential Field (APF)[5] methods use more information of the environment and are suitable in realtime navigation.
However, trajectories generated by APF are generally not optimal. Markov Decision Process is a probabilistic method in which the decision only relates to the last state and has nothing to do with more previous states. Besides, some other global path planning algorithms [6] are discussed to figure out the path to reach the goal.
Local path planning deals with obstacle avoidance at a local environment. Model Predictive Control (MPC) [7] is increasingly applied in navigating the autonomous mobile robots due to its robustness and convergence on path planning. The key idea of MPC is to predict the future with customized model to do path planning and then apply initial control corresponding to the chosen trajectory for the mobile robot. Dynamic Window Approach (DWA)[8], which evaluate each trajectory and select the one with highest score, is not only an independent algorithm but also a component of MPC. However, DWA assumes that all obstacles are static, which is not applicable for dynamic obstacle avoidance with relatively high speed. Algorithms like velocity obstacle and collision cones assume that obstacles move with deterministic velocity and acceleration.
Obviously, in most TE plants, there are relatively static layouts on the equipment and production lines with known environments, and also unpredictable moving of operators of devices, which are regarded as the dynamic obstacles, neither the global path planning nor the local path planning approaches would work well for the navigations of the mobile robots. It is necessary to develop a hybrid method with combined local path planner and global path planner to realize the navigation.
Basis of Autonomous Navigation – Map Building
When the autonomous mobile robot is deployed in an unknown environment to autonomously find the way to reach the goal, the robot has to traverse throughout the environment until reaches the goal. While some new goals are added and set, it is unwise to command the robot to traverse every time, which is high in cost of the computation time and storage space.
In addition, the goal is usually a relative position with respect to the mobile robot while navigating throughout the environment. Therefore, it is important to employ an environmental descriptor, for example the map, to record and describe the information of environment to get the robot to know where it is and where exactly to go. There are different variations
for the map, such as the Feature Map, Topology Map, Grip Map and the Appearance-based Method. Feature Map, which describes the environment with key points, lines or planes, contributes to lively visualization.
Topology Map describes the nodes and the connectivity of environment. Appearance-based Method calculates the pose of robots directly. Grid Map takes account of both the simplicity and visualization on representing the environment. Therefore, Grid Map is an optimal choice as environmental descriptor for the navigating the mobile robots. This section studies the approach for Mapping Building of an unknown environment to obtain a Grip Map.
With no prior knowledge of the environment, Simultaneous Localization and Mapping (SLAM), which constructs the map of the unknown environment while tracking the robot pose simultaneously, plays a vital role in map building. In our method, Rao-Blackwellized particle filter is used for SLAM to ensure the robustness and quality of mapping. One of the most common particle filtering algorithms is the Sampling Importance Resampling (SIR) filter. The mapping process with Rao-Blackwellized SIR filter are decomposed into following steps:
- Sampling: the current pose of the robot xt(i) is calculated with last pose of the robot xt-1(i) by the proposal distribution π(xt|z1:t,u0:t)
- Importance Weighting: each particle is formulated on its own weighting, as described by Eq.(1)

- Resampling: to prevent the infinite particles and ensure the convergence of the algorithm, the quantity of particles should be reduced, and the particles of low importance weightings are replaced by those of high for the resampling process.
- Map Estimating: The current map mt(i) is estimated with the historic observations z1:t and poses x1:t.
Therefore, the main idea of Rao-Blackwellized particle filter is to compute a posterior probability over maps and trajectories, as formulated by Eq.(2)
P(x1:t, m|z1:t, u0:t) = P(x1:t, m|x1:t, z1:t)P(x1:t|z1:t,u0:t) (2)
Where, u0:t is the sequential of odometry measurements including initial pose, z1:t is the sequential of observations, x1:t describes the potential trajectories and m represents the map.
A simulation environment is constructed to verify the map building algorithm, as shown in Fig.3. The mobile robot is moving around the free space, the environment is bounded by surrounding walls and the boxes inside illustrate different stations, which could be regarded as obstacles. The blue area shown in Fig.3 is the scanning range of the mobile robot. By commanding the mobile robot to move throughout this simulation environment, the Grid Map is built based on SLAM technologies, as shown in Fig.4.
Path Planning in Known Environment
With the availability of the map for the environment, the initial position of the mobile robot is often set as a Start Point, and the goal is set as the End Point at the map to construct the path to command the robot to follow. Finding an accessible path from the Start Point to the End Point and commanding the robot to the move along the path by considering the dynamics of the robot and surroundings, are called global path planner and local path planner.
In the process of global path planning, Dijkstra’s and A* algorithm are two major ways to search the shortest path, which are featured with breadth-first search and depth-first search respectively. They are briefly described as shown in Table 2.
Brief Description of Dijkstra’s and A* Algorithm
Table 2
Dijkstra’s Algorithm | A* Algorithm |
---|---|
(1) Set the initial distance value to each node: assign 0 to start node and infinity to others (2) Set the start node as current and mark all other nodesunvisited (3) For current node, find the nearest node whose distanceto the visited set is shortest. (4) Mark the nearest node as visited so that it will neverbe checked again (5) If the goal node has been marked visited, then thesearch is finished. Otherwise repeat the step of (3) |
(1) Set the initial node as current node. Calculate the weight for its neighbors by f(n) = g(n) + h(n),where g(n) is the cost of the path from the start nodeand ℎ(n) is the estimated cost from n to the goal (2) Set the node whose weight is smallest as the currentnode and continue the step of (1) (3) Repeat (1) & (2) until the goal is identified as thecurrent node |
No matter which method is chosen, an accessible path could be theoretically generated. However, an accessible path doesn’t mean an executable path. Local path planner builds a bridge between accessible path and executable path. In this research, the dynamic window algorithm is used, and the algorithm includes the following steps:
- Discretely sampling in the robot control space
- Predict what would happen for each potential samples with forward estimation
- Evaluate these candidate trajectories from the point of distance and the coincidence of global path
- Pick the trajectory with highest score
- Rinse and Repeat
For the generation of the executable path, the local path planner shows great advantage in avoiding obstacles. When the mobile robot follows the global path, local observations build local map so that new/unpredicted obstacles are marked on the local map. Then the local path planner would generate a local path to avoid interference with these obstacles. In this case, the robot can avoid both static and dynamic obstacles with low speed.
Simulation of Autonomous Navigation
A simulation environment is set up as Fig.3, and the map of the environment has been built up in Section II.B based on SLAM algorithm. The path planning algorithm is tested over the map, with Dijkstra’s algorithm implemented and verified in this part. First of all, the current pose of the robot is configured in the map, and the current pose is set as the Start Point.
The robot would be commanded to follow the path which is planned via global path planner after the goal is set. As shown in Fig.5, the blue path is global path from start to goal while the yellow one is local path that follows the global path. Based on several rounds of tests for verification, it is concluded that Dijkstra’s approach could generate an accessible global path
and local path generated by DWA could be constructed the executable path to align with the global path.
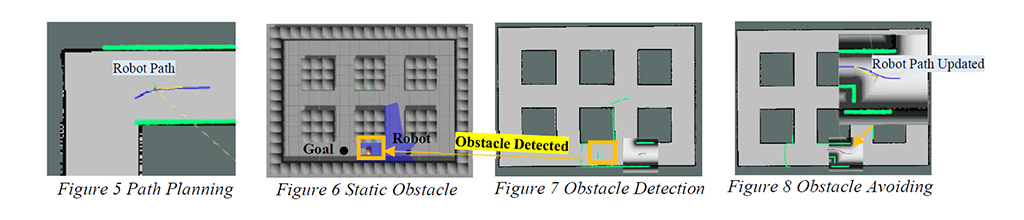
The capability to avoid obstacles is also evaluated here. As shown in Fig.6, an unpredicted obstacle, which is not marked at the map, occurs to be right in front of the robot. The obstacle is in the scanning range of the laser scanner, and is detected by the robot, as shown in Fig.7. In order to test whether the robot would be able avoid interference of the new obstacle and
pass by it, a Goal is configured right after the detected obstacle to check how the robot performs in reaction of the unpredicted obstacle to reach the Goal. By running the local path planner, a local map is generated as shown in Fig.8, with the obstacle updated in the local map, the yellow curve is the local path generated for the avoidance of obstacle. It could be
seen that the robot is not directly moving straight ahead to cause interference with the obstacle, instead it follows an adapted path by moving around the obstacle with no collisions with the obstacle. So here verifies the capability of the robot to passmby the static obstacle, it has also been tested to add some dynamic obstacles that are also able to move around the map at a relatively low speed, can could come across with the robot, the test results also show that the robot is able to update its local map with local path generated to avoid collisions with the dynamic obstacles. The simulation results verify the hybrid approach with combination of global path planner and local path planner on robot path planning and obstacle avoidance.
DISCUSSION AND KEY POINTS
Autonomous Mobile Transportation Vehicle
Key technologies developed and verified in Section II on map building and path planning with SLAM enhance the capability of autonomous navigation for the mobile robot. As compared in Table 1, the SLAM based navigation technology does not require to construct the floor with magnetic tape, magnetic nails or QR code, there is also no need to paste the laser target to the walls or fixed structures. It is fully capable to build the map of an environment automatically, and could handle well to avoid collisions with unpredicted obstacles that are not marked in the map. SLAM based mobile robot is the optimal alternative to be used to develop autonomous mobile transportation system.
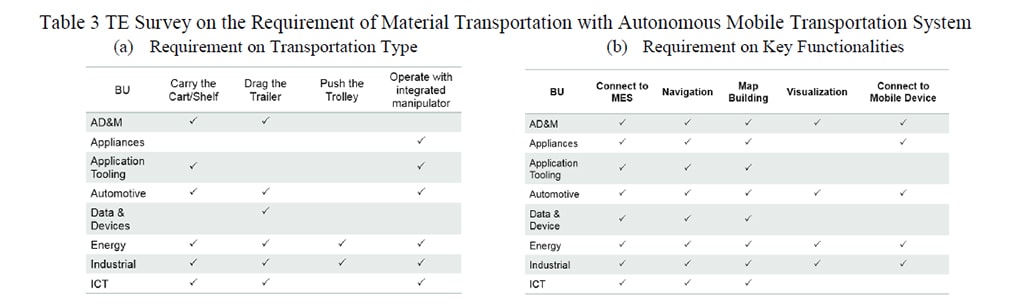
A survey has been conducted across TE business units on detailing the requirements of autonomous mobile transportation for materials. Some high priorities on the material transportation type are to get the mobile robot to carry the cart/shelf, drag the trailer, and to integrate a manipulator to operate the materials, as shown in Table 3(a). Key functionalities with high priorities to implement on the autonomous mobile robot are to connect to MES, navigate autonomously and build the map automatically, as shown in Table 3(b). Among all expectations, the automation of the water spider process with the mobile robot has been rated with high priority by Business Units. As shown in Fig. 9, the Water Spider Process has been the most
critical process for material transportation from the Warehouse / Material Super Market to Production Areas. Here proposes to develop latent type Autonomous Mobile Transportation (AMT) Vehicle based on SLAM navigation technology to carry the shelf for flexible transportation of materials as shown in Fig. 10. The Autonomous Vehicle is able to support a payload for more than 300 kg, and can run at a speed of 0.8 ~ 1 m/s at the plant. It is a highly efficient and effective alternative to replace the manual water spider process.
Autonomous Mobile Transportation System
With the availability of the Autonomous Mobile Transportation Vehicles, the key is to integrate the vehicles as part of the Autonomous Transportation System (AMTS) to develop turn-key solutions for TE plants. Fig.9 illustrates the overall process for material transportation. Generally, it takes operator to unpack the material boxes, and to sort the materials at the
warehouse, then transfer the sorted materials to the boxes to be stored at the Material Super Market, manual water spiders are employed to transport the materials from the Material Super Market to the Buffer Area. The production lines fetch the materials from the buffer area.
Considering the fact that almost all TE plants have not yet automate any part of the process
from warehouse to production line, here first proposes to automate the water spider process with the Autonomous Mobile Transportation Vehicle, as shown in Fig.10. Obviously, AMT Vehicle provide end-to-end material transportation automation solutions from the material super market to production line, the AMT Vehicle would be fast in response and efficient in material transportation, which significantly reduces the labor cost and saves the buffer areas that are required from manual water spiders.
To further enlarge the benefit of using AMT Vehicle on its capability to be digitally connected to networks. Here also proposes to transform the material requesting process from manual operation with paper works to a digital process. Since now it is common to see operators/technicians/engineers using the smart phones, here proposes to develop an App to be installed at the mobile terminals for material requesting and communication, as shown in Fig.11. For the sake of security in communications, the Apps and AMT Vehicles, as well as the server will be connected to TE local networks, with only authorized employees allowed to login the App or access the system for material requesting, communications, as well as monitoring.
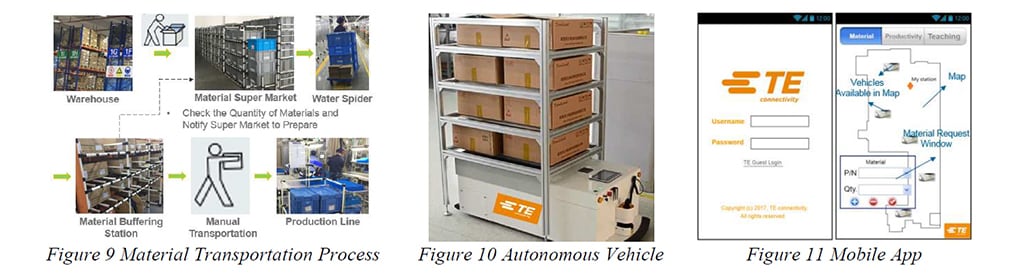
Therefore, the Architecture of the Autonomous Mobile Transportation System is proposed as shown in Fig.12. All AMT Vehicles are managed by the AMTS Central Coordination System for task allocation, path planning and traffic control.
Apps are also connected to the AMTS Central Coordination System, and once the Production Lines request materials via Mobile App, the operator at the Material Super Market would receive the request and prepare the materials in advance, afterwards the AMTS Central Coordination System would assign an AMT Vehicle to come to execute the task for material
transportations. After the AMT Vehicle successfully deliver the materials to productions lines, operators could click confirm to set free for the resource of this AMT Vehicle to be planned by the AMTS Central Coordination System.
ACKNOWLEDGEMENTS
The authors are grateful for the suggestions and instructions from Josef Sinder from Automotive BU, Tim Darr from AMT Harrisburg. The authors also appreciate Automotive Suzhou Team on introducing the requirement to implement material transportation automation for Automotive Suzhou Plant.
REFERENCES
[1] Wang, Lim Chee, Lim Ser Yong, and Marcelo H. Ang. "Hybrid of global path planning and local navigation implemented on a mobile robot in indoor environment." Intelligent Control, 2002. Proceedings of the 2002 IEEE International Symposium on. IEEE, 2002.
[2] Skiena, S. "Dijkstra’s algorithm." Implementing Discrete Mathematics: Combinatorics and Graph Theory with Mathematica, Reading, MA: Addison-Wesley (1990): 225-227.
[3] Duchoň, František, et al. "Path planning with modified A star algorithm for a mobile robot." Procedia Engineering 96 (2014): 59-69.
[4] Garrido, Santiago, et al. "Path planning for mobile robot navigation using voronoi diagram and fast marching." Intelligent Robots and Systems, 2006 IEEE/RSJ International Conference on. IEEE, 2006.
[5] Warren, Charles W. "Global path planning using artificial potential fields."Robotics and Automation, 1989. Proceedings., 1989 IEEE International Conference on. IEEE, 1989.
[6] Hoy, Michael, Alexey S. Matveev, and Andrey V. Savkin. "Algorithms for collision-free navigation of mobile robots in complex cluttered environments: a survey." Robotica 33.03 (2015): 463-497.
[7] Morari, Manfred, et al. "Model predictive control." Preprint (2002).
[8] Fox, Dieter, Wolfram Burgard, and Sebastian Thrun. "The dynamic window approach to collision avoidance." IEEE Robotics & Automation Magazine 4.1 (1997): 23-33.