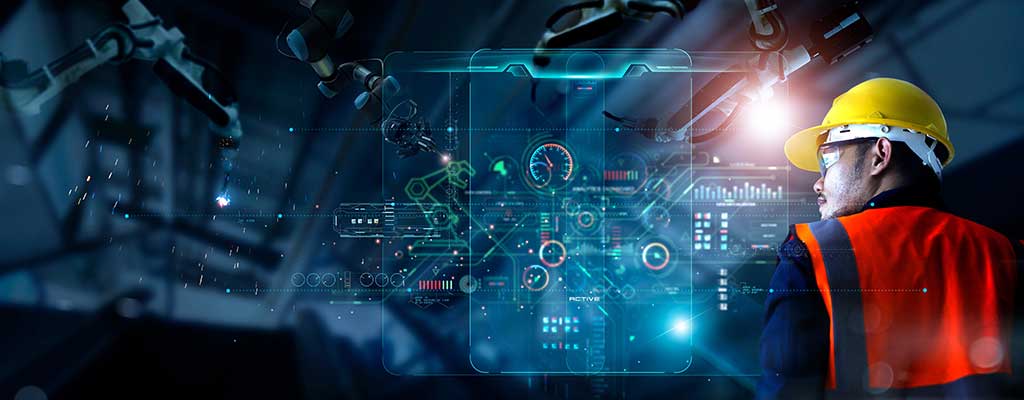
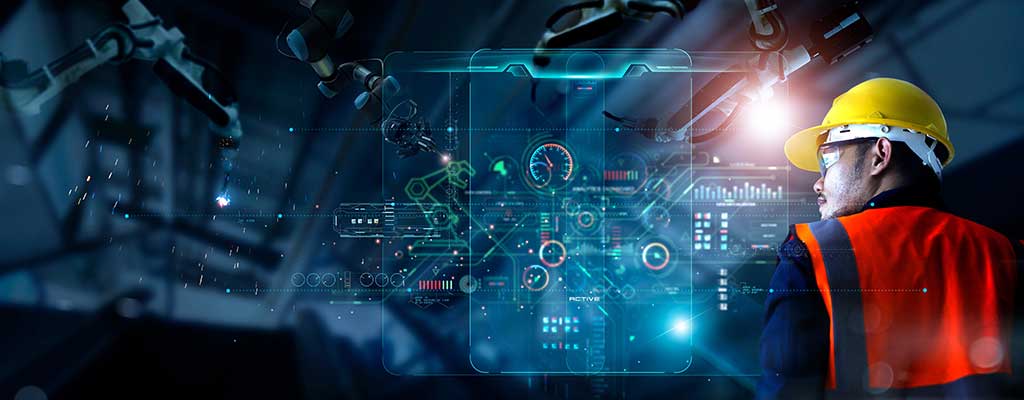
These new technology architectures incorporate redundancy, fail safe, and advanced monitoring tools that enhances robustness and operational durability.
As the technologies of discrete, hybrid, and process automation technologies in manufacturing evolve, manufacturers are achieving unprecedented economies of scale, customization opportunities, and maintenance predictability. However, more needs to be done to realize their full potential. Virtual PLCs provide flexible and decentralized production, which reduces hardware costs and enhances real-time decision making. There is a shift towards sustainable and efficient manufacturing process due to the benefits of modular and adaptable systems. Modern robots, spanning from AGBs to cobots, increase production flexibility and efficiency because of reprogrammable and AI-enhanced capabilities. Learn more in our interview with TE's Anil Kumar Ramsesh, PhD, Engineeering Fellow for Industrial Automation & Electrification, and Ivan Ruiz Stubelj, Manager, Strategic Business Development, Automation Controls.
How do virtual PLCs and other controllers enable manufacturers to develop and then run more flexible and decentralized production processes?
Ivan: Virtual PLCs rely on virtual machines or containers to run a virtual controller inside a powerful piece of hardware. And currently they are revolutionizing the manufacturing industry by enabling flexible and decentralized production processes. Unlike traditional PLCs, which often require physical hardware upgrades to perform new functions, virtual PLCs can be adjusted through mere software configurations, enabling motion control, image recognition, and many other functions. Moreover, they can run on various hardware platforms, including industrial PCs, local servers, and, in certain use cases, even cloud-based platforms. This provides manufacturers with a full array of choices to meet their needs.
Being able to run in different hardware configurations, it's a key driver of decentralization and decentralized control. For instance, virtual PLCs can be deployed at the edge of production processes, reducing latency and improving real time decision making while more processing intensive data operations like time series database processes can be deployed on the cloud.
Moreover, these types of units, which are high speed Ethernet native, can operate autonomously or in coordination with other units, enhancing overall production flexibility. Lastly, PLCs in certain cases are even hardware agnostic, and because of this they minimize the need for dedicated hardware units, reducing initial capital investment. This makes it more affordable to upgrade and expand production capabilities to industrial end users.
How are smart industrial production machines similar to and different from conventional manufacturing machinery?
Dr. Anil: Let me start with saying smart industrial production system is a factory of the future. So why do we say that factory of the future? Generally, if you see with the increasing demand of the customer requirement and on the other side, we need to have affordable, effective, efficient manufacturing processes. We also need to maintain the sustainability aspect means; we should have a green and clean factory. And the most important thing is on the safety of the manufacturing. That is one of the critical things. The smart industrial production or factory of the future will help us in achieving these things. If we have a modular and adaptable system and solution which is flexible, convertible, reusable, expandable, and combinable, the benefit becomes the reduction of the Capex. We are putting up a plant. Now I can reuse the components. The cost of investment goes less. If that product line is the end of the product line, we can reuse the system and reconfigure it for the new thing. This will also help in doing it faster, saves time in establishing the new lines, and enables sustainability.
As I mentioned earlier in the traditional system, it is a dedicated manufacturing line for a particular product, and it is designed to do a particular process which may be customized for that product. While the smart manufacturing system is configurable with stations that perform generic performance-like process like punching, cutting, welding - those kind of things - and it is integrated to meet the requirement of a particular product manufacturing. These stations could be reused in the other product lines.
How is robotic automation enabling manufacturers to develop and run more flexible and decentralized production processes?
Ivan: First, what I would like to clarify is that robots are a very broad category that encompasses automated guided vehicles, AGVs, collaborative robots, and cobots to articulated robots. There is a whole universe of different robots, but the key aspect of modern robots is that they can be reprogrammed for various tasks, and this reduces the need for specialized machinery at the automation end user side. This flexibility basically allows manufacturers to quickly switch production lines to accommodate different products or variations with minimal downtime. For instance, cobots, or collaborative robots, can efficiently handle custom orders and small batch production. These robots are being deployed across a wide range of industries, from electronic manufacturing to metalworking, and in these cases, for instance, the operator can quickly train the cobot by mimicking a manual operation such as welding, allowing the robot to execute the task with minimal programming needed.
Lastly, what I would like to clarify is that with the massive adoption at the advent of artificial intelligence, machine learning, and vision recognition technologies, robots can improve performance over time, adapting to new tasks and optimizing production processes. Leveraging this strength, robots can, alongside humans, combine their strength to increase the overall efficiency and safety within production processes.
What are challenges in developing the required technical architectures for using factory robots on the factory floor?
Dr. Anil: No doubt, to design a flexible modular manufacturing system, one should have a broader understanding of multiple domains and benefits - what we get from multiple domains. The second thing is integration of multiple product or systems together interface between the things. It is very important to understand and take it forward.
The second point I say about is the standardization of the hardware, software, communication protocol, etc. We need to plan it. Especially the connectivity solutions become very critical there because now when we want to interchange, the interfaces should be reusable and easy to do. And there should be flawless interface. So that is the most important at the connectivity and communication solution for such system. We at TE Connectivity are working to support our customers.
What is driving market adoption and demand? What could limit this?
Dr. Anil: The flexibility, what Ivan was mentioning, and adaptability, and reconfigurability is the one which is driving. The second thing is productivity. It could be faster, quicker and creating an environment of safety and taking it forward. The challenge I see here is in today's market demand, where variants of the product is more and there are multiple variants of the product that come in. Manufacturing different variants would be always a challenge if you have a traditional line. But if you have a robotic thing we could configure for different variant, the same system, and we can use it and make the production economically feasible, adaptable to various requirements.
How reliable are these technological architectures, especially in improving the operational durability required for always on production?
Ivan: These new technology architectures incorporate redundancy, fail safe, and advanced monitoring tools that enhances robustness and operational durability. Predictive maintenance and remote management techniques further ensure smoother and longer lasting operations by addressing a couple of issues proactively. It's also worth noting that new technologies like virtualization are playing a crucial role in improving reliability and reducing costs.
Virtualization allows to simulate environment, for instance, in digital twins, in which manufacturers can test new configurations without disrupting actual production lines, minimizing risk and physical resource use Virtual platforms, on the other hand, allow for rapid prototyping and scalable testing, enabling thorough evaluation of various scenarios quickly and inexpensively. This process also supports collaboration among geographically dispersed teams, leveraging AI and machine learning to optimize configurations and ultimately predict performance. Overall, iterative development, predictive maintenance, and virtualization collectively are enhancing reliability of early stage manufacturing technologies and ensuring that they meet the demands of always on production while keeping the costs low.
How is modularity changing traditional thinking about machine operation on the factory floor?
Dr. Anil: Let me take an example and start here. There are certain few common things between the traditional and modular manufacturing system, like the material what we use generally, the raw materials like steel, aluminum plastic. Presence remains largely the same, of course, with some exceptions like new composites or new alloys, and those kinds of things. But when we want to process that way, we process. That is the mechanical engineering aspect of physics and chemistry related to that, still need to be handled in the same way as we do it in the traditional thing. But we can do it in a better way using this modular system and approach the entire process of the entire value chain. We can do it in a different way to get the benefit, but with the advancement with it sensing technology, data collection, data archival, and analysis and enabling. This enables modular and smart manufacturing units leading to better safety and efficient operation. Like the example Ivan was mentioning about digital twin. Today we don't need to establish a pilot plant to do the analysis of the flow. It could be done virtually using the digital twin on a machine, and we could configure it unfairly. You can get a better accuracy, maybe around 90% or 80%, 85% plus accurate real-life information you can get, and you can run and take it forward.
This helps in a way of thinking or how we design. It is in a different way. That is one thing. For instance, the preventive maintenance of the plant. Earlier, we never had that opportunity to do that because of lack of technology. Today, yes, we can do that. And to do that we need to think, can we do that? Someone should know. And they should be able to enable it and take it forward and do that. While designing, we need to have a broader thinking how it could be used, what it could be. And as I mentioned, digital twin would help us for easy and fast changeover of the production lines and early estimation. If there is something that is going wrong, we can hardly predict it and take it forward. That is the benefit of putting the modular system over the traditional system. But to do this, we need to have a larger understanding of what it is that enables to do all this and the best we can do it.
What is enabling the transition toward interoperability, specifically in the design of machines and components?
Dr. Anil: Let me take an example of connectivity solution. That's our domain. I would like to explain it. If I have multiple protocols and if I have multiple connection connectors, mechanical connectors, to connect the thing, it would be quite challenging. I can't do it faster. At TE Connectivity, we are working on the solutions that could make our customer easy to connect and configure it. One of the things that we talk about is single payer Ethernet. Probably Ivan would speak more about that. Where the communication and power are on the single line. And that helps plug and play in the mechanical connection. That helps in plug and play for different modules or different stations. That's how we are trying to help our customers.
How is TE helping manufacturers develop technical architectures to convey data and power in a decentralized system?
Ivan: Anil mentioned a lot of relevant points. At TE we believe that industrial automation is facing a pivotal moment as numerous advancements are converging to redefine the automation landscape. Innovations in miniaturization, artificial intelligence, and increased processing power, among other factors, are poised to drive significant transformation in automation throughout the coming years. These are at the forefront of this evolution, working on a broad array of technologies, including interface connectors, board signal connectors, switching, isolation, and passive components, among many others. These efforts aim to enable and support the next wave of automation, fostering more efficient, intelligent, and integrated industrial ecosystems.
But among all these technologies, the line those threads through the fabric of industrial automation is single pair Ethernet. Single pair Ethernet, or ESP, brings cost effective, efficient, and robust data and power transmission solutions over the same cable. It’s simple cabling reduces weight and space requirements, supporting longer runs and providing sufficient bandwidth for various applications. Some examples: SP’s ability to deliver both data and power over a single pair of wires simplifies installation and maintenance, which is crucial to power IoT devices like sensors and actuators.
One thing that I would like to highlight is that this type of technologies is designed for industrial environments. SP enhances reliability with improved electromagnetic interference immunity, and it facilitates unified network architectures, simplifying management and scalability, supporting advanced technologies like edge computing and real time analytics. By enabling smart manufacturing and industry 4.0 principles, SP ensures efficient resource utilization and as Anil was mentioning, predictive maintenance, making it essential for the next generation of industrial automation.
What other types of elements, such as the power grid, are affecting broader use of factory robotics?
Dr. Anil: In traditional manufacturing units generally, we used to have AC motors, depending on the capacity and the size of the plant and the product we manufacture. But today, when you look at this modular thing, since things are modularized, largely DC motors have been used. If you look, there are multiple power conversions that happen. AC to DC at grid level and then DC to DC internal. There is a lot of opportunity to have optimization on that power network. Whether we want to run it in entire thing on a DC bus or want to run it on completely on the AC bus, there is a lot of flexibility and opportunity to adapt whatever is suitable, which is efficient and easier to do that.
Over and above all this, there is an opportunity for getting this energy source from sustainable things like solar, wind, or fuel cells. Green and clean energy. Largely these sources have a DC power source. I see that there is a lot of opportunity for getting into a DC power network. That would be more efficient and effective in a new modular robotic system. Maybe at lower voltages, it would be safer to operate and much easier to adapt it. I see for these things, TE has a lot of opportunity to develop components. It could be connectors, filters like Ivan was mentioning about passives and EMI, EMC filters, and those kind of things. And we are getting ready there to support our customers.
What can we expect to see or see more of over the next five years when it comes to innovation in factory automation?
Ivan: Over the next five years, we believe that significant advancements in automation, both factory hybrid and process, will take place. This will be driven by artificial intelligence, sustainability, and the industrial Internet of Things. For instance, the integration of more IIoT devices or industrial Internet of Things devices will enable more connected and intelligent manufacturing environments, facilitating seamless data exchange and improving coordination between machines. This will support the growth of smart factories, where decentralized and flexible production processes can be quickly reconfigured to meet changing demands. Virtualization and digital twins will further revolutionize manufacturing because they will allow extensive simulation and testing of new configurations at a very affordable cost. And of course, they will minimize risks and costs associated with physical prototypes. This will enable rapid prototyping and further knowledge. Finally, sustainability will also be a big focus with automation technologies improving energy efficiency, as Anil was mentioning, and reducing waste. Overall, the next five years will see factory automation become more intelligent, flexible, efficient, and having less climate impact in our world.
Dr. Anil: Just to add upon that to what Ivan was mentioning, it would also be safer operations. It will enable safety becomes critical and it also enables safety.
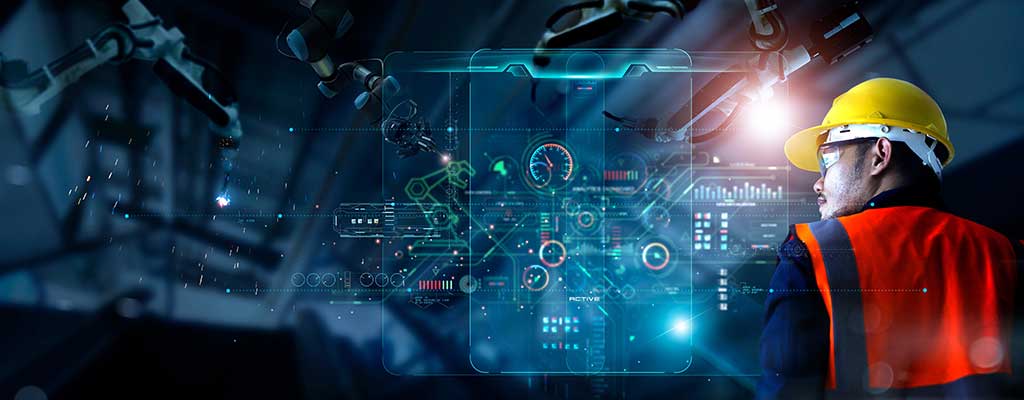
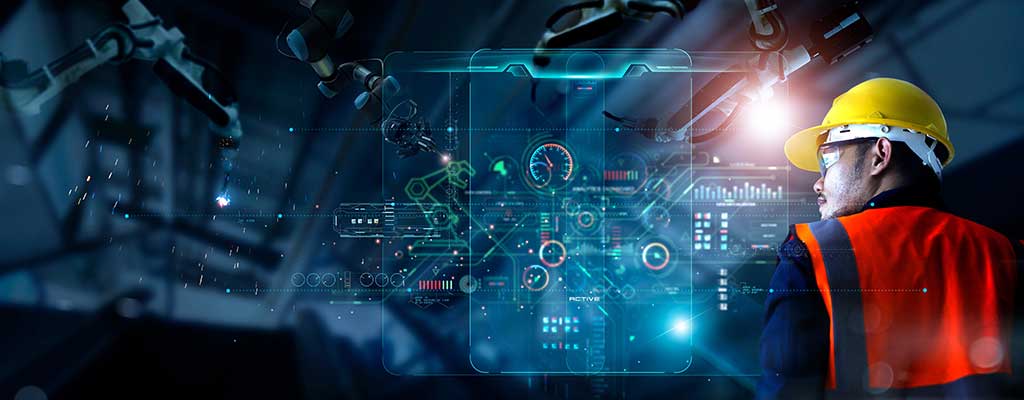
These new technology architectures incorporate redundancy, fail safe, and advanced monitoring tools that enhances robustness and operational durability.
As the technologies of discrete, hybrid, and process automation technologies in manufacturing evolve, manufacturers are achieving unprecedented economies of scale, customization opportunities, and maintenance predictability. However, more needs to be done to realize their full potential. Virtual PLCs provide flexible and decentralized production, which reduces hardware costs and enhances real-time decision making. There is a shift towards sustainable and efficient manufacturing process due to the benefits of modular and adaptable systems. Modern robots, spanning from AGBs to cobots, increase production flexibility and efficiency because of reprogrammable and AI-enhanced capabilities. Learn more in our interview with TE's Anil Kumar Ramsesh, PhD, Engineeering Fellow for Industrial Automation & Electrification, and Ivan Ruiz Stubelj, Manager, Strategic Business Development, Automation Controls.
How do virtual PLCs and other controllers enable manufacturers to develop and then run more flexible and decentralized production processes?
Ivan: Virtual PLCs rely on virtual machines or containers to run a virtual controller inside a powerful piece of hardware. And currently they are revolutionizing the manufacturing industry by enabling flexible and decentralized production processes. Unlike traditional PLCs, which often require physical hardware upgrades to perform new functions, virtual PLCs can be adjusted through mere software configurations, enabling motion control, image recognition, and many other functions. Moreover, they can run on various hardware platforms, including industrial PCs, local servers, and, in certain use cases, even cloud-based platforms. This provides manufacturers with a full array of choices to meet their needs.
Being able to run in different hardware configurations, it's a key driver of decentralization and decentralized control. For instance, virtual PLCs can be deployed at the edge of production processes, reducing latency and improving real time decision making while more processing intensive data operations like time series database processes can be deployed on the cloud.
Moreover, these types of units, which are high speed Ethernet native, can operate autonomously or in coordination with other units, enhancing overall production flexibility. Lastly, PLCs in certain cases are even hardware agnostic, and because of this they minimize the need for dedicated hardware units, reducing initial capital investment. This makes it more affordable to upgrade and expand production capabilities to industrial end users.
How are smart industrial production machines similar to and different from conventional manufacturing machinery?
Dr. Anil: Let me start with saying smart industrial production system is a factory of the future. So why do we say that factory of the future? Generally, if you see with the increasing demand of the customer requirement and on the other side, we need to have affordable, effective, efficient manufacturing processes. We also need to maintain the sustainability aspect means; we should have a green and clean factory. And the most important thing is on the safety of the manufacturing. That is one of the critical things. The smart industrial production or factory of the future will help us in achieving these things. If we have a modular and adaptable system and solution which is flexible, convertible, reusable, expandable, and combinable, the benefit becomes the reduction of the Capex. We are putting up a plant. Now I can reuse the components. The cost of investment goes less. If that product line is the end of the product line, we can reuse the system and reconfigure it for the new thing. This will also help in doing it faster, saves time in establishing the new lines, and enables sustainability.
As I mentioned earlier in the traditional system, it is a dedicated manufacturing line for a particular product, and it is designed to do a particular process which may be customized for that product. While the smart manufacturing system is configurable with stations that perform generic performance-like process like punching, cutting, welding - those kind of things - and it is integrated to meet the requirement of a particular product manufacturing. These stations could be reused in the other product lines.
How is robotic automation enabling manufacturers to develop and run more flexible and decentralized production processes?
Ivan: First, what I would like to clarify is that robots are a very broad category that encompasses automated guided vehicles, AGVs, collaborative robots, and cobots to articulated robots. There is a whole universe of different robots, but the key aspect of modern robots is that they can be reprogrammed for various tasks, and this reduces the need for specialized machinery at the automation end user side. This flexibility basically allows manufacturers to quickly switch production lines to accommodate different products or variations with minimal downtime. For instance, cobots, or collaborative robots, can efficiently handle custom orders and small batch production. These robots are being deployed across a wide range of industries, from electronic manufacturing to metalworking, and in these cases, for instance, the operator can quickly train the cobot by mimicking a manual operation such as welding, allowing the robot to execute the task with minimal programming needed.
Lastly, what I would like to clarify is that with the massive adoption at the advent of artificial intelligence, machine learning, and vision recognition technologies, robots can improve performance over time, adapting to new tasks and optimizing production processes. Leveraging this strength, robots can, alongside humans, combine their strength to increase the overall efficiency and safety within production processes.
What are challenges in developing the required technical architectures for using factory robots on the factory floor?
Dr. Anil: No doubt, to design a flexible modular manufacturing system, one should have a broader understanding of multiple domains and benefits - what we get from multiple domains. The second thing is integration of multiple product or systems together interface between the things. It is very important to understand and take it forward.
The second point I say about is the standardization of the hardware, software, communication protocol, etc. We need to plan it. Especially the connectivity solutions become very critical there because now when we want to interchange, the interfaces should be reusable and easy to do. And there should be flawless interface. So that is the most important at the connectivity and communication solution for such system. We at TE Connectivity are working to support our customers.
What is driving market adoption and demand? What could limit this?
Dr. Anil: The flexibility, what Ivan was mentioning, and adaptability, and reconfigurability is the one which is driving. The second thing is productivity. It could be faster, quicker and creating an environment of safety and taking it forward. The challenge I see here is in today's market demand, where variants of the product is more and there are multiple variants of the product that come in. Manufacturing different variants would be always a challenge if you have a traditional line. But if you have a robotic thing we could configure for different variant, the same system, and we can use it and make the production economically feasible, adaptable to various requirements.
How reliable are these technological architectures, especially in improving the operational durability required for always on production?
Ivan: These new technology architectures incorporate redundancy, fail safe, and advanced monitoring tools that enhances robustness and operational durability. Predictive maintenance and remote management techniques further ensure smoother and longer lasting operations by addressing a couple of issues proactively. It's also worth noting that new technologies like virtualization are playing a crucial role in improving reliability and reducing costs.
Virtualization allows to simulate environment, for instance, in digital twins, in which manufacturers can test new configurations without disrupting actual production lines, minimizing risk and physical resource use Virtual platforms, on the other hand, allow for rapid prototyping and scalable testing, enabling thorough evaluation of various scenarios quickly and inexpensively. This process also supports collaboration among geographically dispersed teams, leveraging AI and machine learning to optimize configurations and ultimately predict performance. Overall, iterative development, predictive maintenance, and virtualization collectively are enhancing reliability of early stage manufacturing technologies and ensuring that they meet the demands of always on production while keeping the costs low.
How is modularity changing traditional thinking about machine operation on the factory floor?
Dr. Anil: Let me take an example and start here. There are certain few common things between the traditional and modular manufacturing system, like the material what we use generally, the raw materials like steel, aluminum plastic. Presence remains largely the same, of course, with some exceptions like new composites or new alloys, and those kinds of things. But when we want to process that way, we process. That is the mechanical engineering aspect of physics and chemistry related to that, still need to be handled in the same way as we do it in the traditional thing. But we can do it in a better way using this modular system and approach the entire process of the entire value chain. We can do it in a different way to get the benefit, but with the advancement with it sensing technology, data collection, data archival, and analysis and enabling. This enables modular and smart manufacturing units leading to better safety and efficient operation. Like the example Ivan was mentioning about digital twin. Today we don't need to establish a pilot plant to do the analysis of the flow. It could be done virtually using the digital twin on a machine, and we could configure it unfairly. You can get a better accuracy, maybe around 90% or 80%, 85% plus accurate real-life information you can get, and you can run and take it forward.
This helps in a way of thinking or how we design. It is in a different way. That is one thing. For instance, the preventive maintenance of the plant. Earlier, we never had that opportunity to do that because of lack of technology. Today, yes, we can do that. And to do that we need to think, can we do that? Someone should know. And they should be able to enable it and take it forward and do that. While designing, we need to have a broader thinking how it could be used, what it could be. And as I mentioned, digital twin would help us for easy and fast changeover of the production lines and early estimation. If there is something that is going wrong, we can hardly predict it and take it forward. That is the benefit of putting the modular system over the traditional system. But to do this, we need to have a larger understanding of what it is that enables to do all this and the best we can do it.
What is enabling the transition toward interoperability, specifically in the design of machines and components?
Dr. Anil: Let me take an example of connectivity solution. That's our domain. I would like to explain it. If I have multiple protocols and if I have multiple connection connectors, mechanical connectors, to connect the thing, it would be quite challenging. I can't do it faster. At TE Connectivity, we are working on the solutions that could make our customer easy to connect and configure it. One of the things that we talk about is single payer Ethernet. Probably Ivan would speak more about that. Where the communication and power are on the single line. And that helps plug and play in the mechanical connection. That helps in plug and play for different modules or different stations. That's how we are trying to help our customers.
How is TE helping manufacturers develop technical architectures to convey data and power in a decentralized system?
Ivan: Anil mentioned a lot of relevant points. At TE we believe that industrial automation is facing a pivotal moment as numerous advancements are converging to redefine the automation landscape. Innovations in miniaturization, artificial intelligence, and increased processing power, among other factors, are poised to drive significant transformation in automation throughout the coming years. These are at the forefront of this evolution, working on a broad array of technologies, including interface connectors, board signal connectors, switching, isolation, and passive components, among many others. These efforts aim to enable and support the next wave of automation, fostering more efficient, intelligent, and integrated industrial ecosystems.
But among all these technologies, the line those threads through the fabric of industrial automation is single pair Ethernet. Single pair Ethernet, or ESP, brings cost effective, efficient, and robust data and power transmission solutions over the same cable. It’s simple cabling reduces weight and space requirements, supporting longer runs and providing sufficient bandwidth for various applications. Some examples: SP’s ability to deliver both data and power over a single pair of wires simplifies installation and maintenance, which is crucial to power IoT devices like sensors and actuators.
One thing that I would like to highlight is that this type of technologies is designed for industrial environments. SP enhances reliability with improved electromagnetic interference immunity, and it facilitates unified network architectures, simplifying management and scalability, supporting advanced technologies like edge computing and real time analytics. By enabling smart manufacturing and industry 4.0 principles, SP ensures efficient resource utilization and as Anil was mentioning, predictive maintenance, making it essential for the next generation of industrial automation.
What other types of elements, such as the power grid, are affecting broader use of factory robotics?
Dr. Anil: In traditional manufacturing units generally, we used to have AC motors, depending on the capacity and the size of the plant and the product we manufacture. But today, when you look at this modular thing, since things are modularized, largely DC motors have been used. If you look, there are multiple power conversions that happen. AC to DC at grid level and then DC to DC internal. There is a lot of opportunity to have optimization on that power network. Whether we want to run it in entire thing on a DC bus or want to run it on completely on the AC bus, there is a lot of flexibility and opportunity to adapt whatever is suitable, which is efficient and easier to do that.
Over and above all this, there is an opportunity for getting this energy source from sustainable things like solar, wind, or fuel cells. Green and clean energy. Largely these sources have a DC power source. I see that there is a lot of opportunity for getting into a DC power network. That would be more efficient and effective in a new modular robotic system. Maybe at lower voltages, it would be safer to operate and much easier to adapt it. I see for these things, TE has a lot of opportunity to develop components. It could be connectors, filters like Ivan was mentioning about passives and EMI, EMC filters, and those kind of things. And we are getting ready there to support our customers.
What can we expect to see or see more of over the next five years when it comes to innovation in factory automation?
Ivan: Over the next five years, we believe that significant advancements in automation, both factory hybrid and process, will take place. This will be driven by artificial intelligence, sustainability, and the industrial Internet of Things. For instance, the integration of more IIoT devices or industrial Internet of Things devices will enable more connected and intelligent manufacturing environments, facilitating seamless data exchange and improving coordination between machines. This will support the growth of smart factories, where decentralized and flexible production processes can be quickly reconfigured to meet changing demands. Virtualization and digital twins will further revolutionize manufacturing because they will allow extensive simulation and testing of new configurations at a very affordable cost. And of course, they will minimize risks and costs associated with physical prototypes. This will enable rapid prototyping and further knowledge. Finally, sustainability will also be a big focus with automation technologies improving energy efficiency, as Anil was mentioning, and reducing waste. Overall, the next five years will see factory automation become more intelligent, flexible, efficient, and having less climate impact in our world.
Dr. Anil: Just to add upon that to what Ivan was mentioning, it would also be safer operations. It will enable safety becomes critical and it also enables safety.