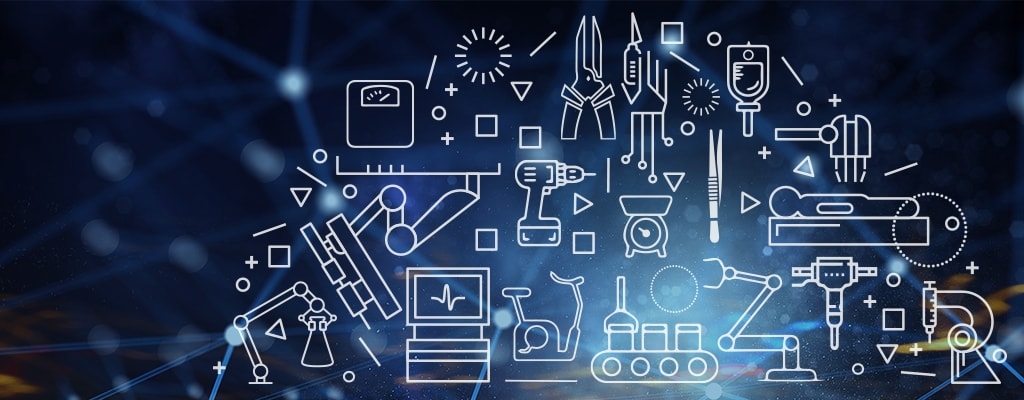
White Paper
Optimizing Compact Load Cell Design For Performance
Learn more about the need for higher performance and compact designs in force sensing.
Automation has become an integral part of our daily functions. This trend not only drives greater sensor content processing requirements, but also calls for higher performance, more compact sizing, and design maximized for volume production.

Force Sensing
The element of force is one of the most fundamental parameters of interest in process control and process monitoring. A force sensor, also called a load cell, converts the force to an electrical signal in mV, amplified or digital output format.
Force sensor applications are highly prevalent. They are used in various applications including, but not limited to:
- In an infusion pump, two force sensors detect the force generated by medicine fluid pressure and correlate the differential signal to the flow rate of medicine.
- A force sensor in an insulin pump detects occlusion by sensing force generated by medicine fluid pressure and correlate the differential signal to the flow rate of medicine.
- Many load cells are used in industrial and medical robots, to precisely control torque in joints and force on the tool.
- Load cells are also used in hospital beds to weigh the patients.
- Orthopedic instruments also utilize load cells in devices such as drills to monitor the torque or force.
- Sports equipment, such as exercise bicycles, interates load cells into the spindles for power metering.
- Home appliances like microwave ovens use load cells for timing controls in various cooking functions.






The most fundamental characteristics for load cells are sensitivity, stability, repeatability, and precision. Furthermore, the ability to withstand great overload without damage through normal usage and handling, including accidental drops and other unforeseen pressures, is important. With the exception of metrology applications where only sensor precision, stability and repeatability are the predominant factors, the majority of applications in OEM and consumer markets require balancing the execution of load cell features against production costs and the ability to scale to volume production thresholds.

Force Sensing
The FX29 button compressive load cell from TE Connectivity (TE), shown in Figure 1, is a prime example of both high performance and exceptional value while maintaining an excellent compact size. The core sensing element is a semiconductor micromachined silicon piezoresistive gauge. Each load cell has four MEMs dies strategically positioned as illustrated in Figure 2. The gauges are paired for closely matched thermal and electrical operating characteristics, form a Wheatstone bridge with two legs of gauges in tension and the other two legs of gauges in compression as the substrate the gauges are attached to deforms in response to a stimulation such as force or torque. The bridge produces voltage differential output proportional to the force applied in the case of FX29.
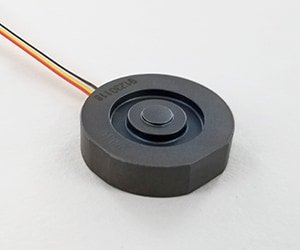
(DIA. 19.7MM X H 5.5MM)
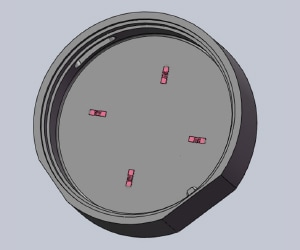
Compared to bonded foil strain gauges (BFSG), a technology utilized by many manufacturers, the semiconductor gauge is 75 times more sensitive allowing stiffer load bearing structure and smaller strain level but still produces 10 times the output.
With the stiffer structure, typically with 0.02mm or less deflection as in shown in simulation as Figure 3, the FX29 load cells are unlikely to have fatigue failure which results from repeated force cycles. The high stiffness of the structure also enhances its robustness towards withstanding forces of shock and vibration. The load cell’s overload capability is typically 2.5 times the nominal force range, as opposed to 1.5 times for BSFG sensors. Other elements of the design and production confirm the FX29 load cell is engineered to function optimally.
The MEMs gauges (Figure 4) are bonded to the stainless substrate by glass, an inorganic material, in a high temperature process called “microfused technology”. Organic bonding material, typical in BFSG but also a destructive cause of sensor drift over time, is entirely eliminated. Moreover, the microfused process relieves the residue stresses in the mechanical parts, ensuring long-term stability.
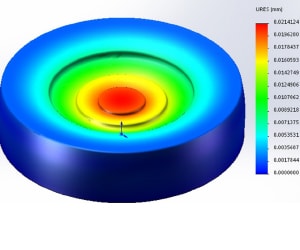
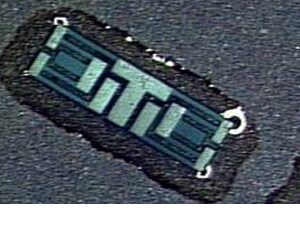
The microfused manufacturing process has already been fine-tuned for mass quantity production by the scale of millions. This is exemplified by the fact that the majority of automotive anti-lock braking system (ABS) sensors are manufactured with this technology; as such, its robustness and price-to-performance ratio are apparent.
The FX29 load cell body is a two-piece construction made by metal injection mold and stamping, designed for high volume and low-cost production. Additionally, the one-size-fits-all output (Figure 5) is another feature of the FX29. The standard offerings are mV/V, amplified voltage and digital I2C outputs in one compact package, eliminating any need for add-on, external electronics modules.
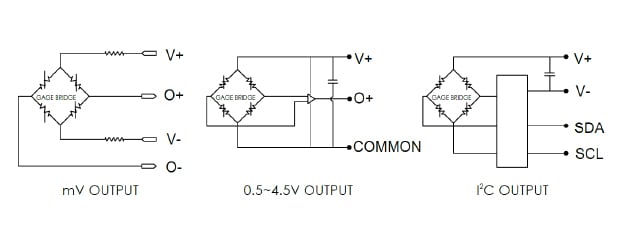

Summary
In summary, the compact FX29 load cell raises the bar for robustness and exceptional price-to-performance, it is enabled by proven volume production technology, universally suited for a variety of force sensing applications.

About The Author
Hai Mei is based in Boston area, and, currently Senior Application Engineering Manager at
TE Connectivity, Sensor Solutions. Hai has 30 years of work experience in instrumentation
industry in various capacities such as product design and application engineering, strategic
sourcing and supplier development. Hai holds 7 US patents and has developed many pressure
and force sensing products. Hai received MS degree in mechanical engineering from University
of Rhode Island and BS degree in engineering mechanics from Shanghai JiaoTong University.

Microfused is a trademark.