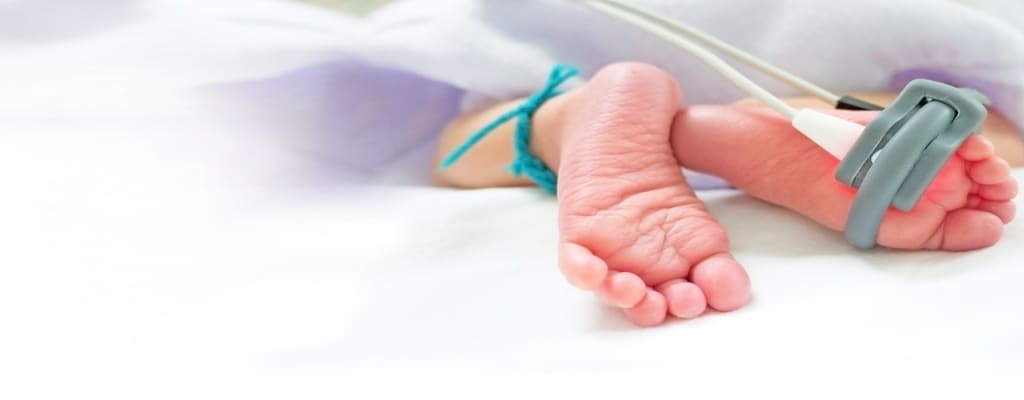
White Paper
Advanced Detection
The unique properties of piezo film as a dynamic strain sensor make it well-suited to the detection of vital signs, whether mounted in direct contact with the skin or mechanically coupled through intervening layers. Some film elements are sensitive enough to detect a human pulse in a device which is carried in the pocket of outer clothing.
When a strip of piezoelectric PVDF polymer film (piezo film) is stretched, it generates an electrical signal (charge or voltage) between upper and lower electrode surfaces, proportional to the amount of elongation. Piezoelectric materials are generally thought of as responding to pressure, but in the case of piezo film, the geometry of the element means that very high stress levels can be achieved in the cross-section of the film when very low force is applied in the longitudinal direction, while the same level of force applied over a larger area to the surface of the film would generate far lower stress. Therefore piezo film demonstrates phenomenal sensitivity to dynamic strain, typically in the region of 10 to 15 mV per microstrain (ppm change in length) for 28 μm thickness PVDF. The phrase “dynamic” strain is used because electrical charge generated by a change in strain leaks away into the electrical circuit connected to the film, and so static conditions of strain cannot actually be detected. This can prove to be a positive advantage in cases where the sensor may be placed under varying levels of pre-load. The film sees only time-varying changes in strain, with a frequency response that may start from as low as 0.1 Hz. Piezo film is also lightweight, thin, and highly flexible, and requires no external power in order to function. This unique combination of properties enables a wide range of medical applications to be addressed where very low-level mechanical signals must be detected. It is obviously a technology of great interest where available power is limited (it can even generate tiny quantities of power in some configurations). It is also extremely durable, capable of withstanding hundreds of millions of flexing cycles, and shock resistant.
Piezo film is lightweight, thin, highly flexible, and requires no external power to function.

Direct Skin Contact
Exploiting the properties of piezo film as a “dynamic strain gauge,” an element can be easily bonded directly onto the skin (e.g., on the inside of the wrist). TE manufactures a general purpose sensor that already has pressure-sensitive adhesive on one side, but the adhesive is not rated for biocompatibility, so for short-term trials, a patch of 3M 9842 (thin polyurethane tape with adhesive coating) was fixed on the skin and the piezo film sensor applied on top. Figure 1 shows a pulse signal, obtained using a charge amplifier with low frequency limit set to 1 Hz and a sensitivity of 1 mV/pC. The output of approximately 130 mV pk-pk corresponds to an open-circuit voltage of around 100 mV pk-pk, that in turn, can be interpreted as a dynamic strain of roughly 8 με. This signal was recorded while the hand was at rest. Flexing or rotating the wrist could generate much higher amplitude signals, especially when a lower frequency limit was selected on the preamplifier. As an example, Figure 2 shows the response of the sensor while an object was gripped then released repeatedly, showing an amplitude of around 3V open-circuit or around 250 με.
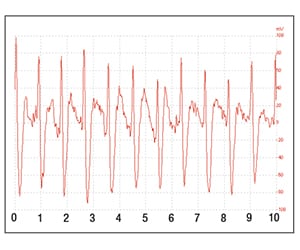
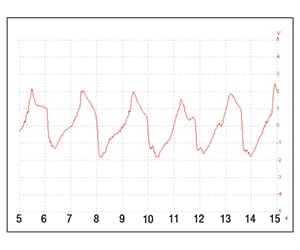
This ability of the film to detect both very tiny physical signals and also gross movement arises from the fact that the piezo response in PVDF film is linear over a very large dynamic range (estimated to be as great as 14 orders of magnitude). In many cases, the smaller signals can be extracted by filtering, as long as the bandwidths of the target signal and the “noise” are sufficiently well separated. Similar self-adhesive sensors have been used to detect muscle and skin movement of the chest, leg, and eyelid during the study of sleep disorder. Also, the response of a muscle (for example, between thumb and forefinger) to a deliberate electrical stimulation can be detected as an indicator of the effectiveness of anesthesia (known as neuro-muscular transmission).

Acceleration Sensor
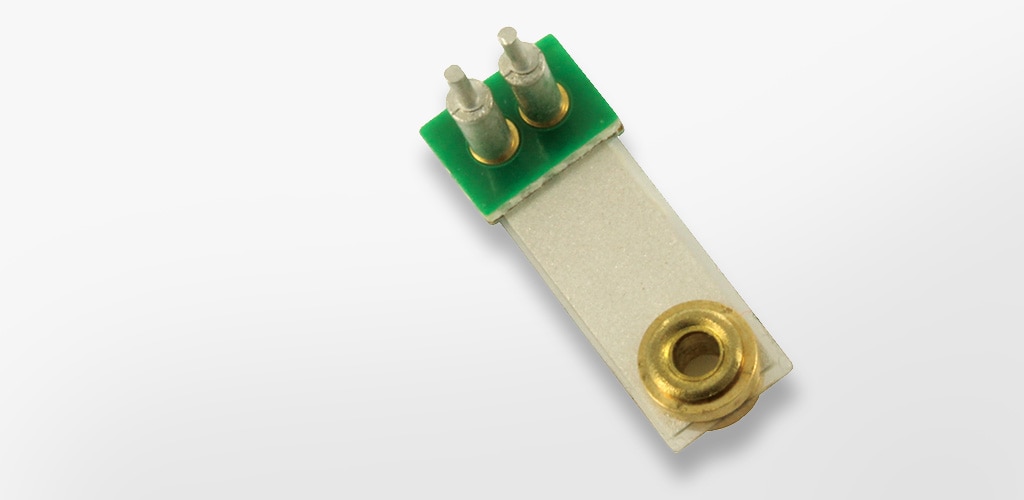
The Minisense 100 is a standard component that employs a mass-loaded cantilever design with rigid PCB material forming the clamp and allows the mounting of the connection pins. The added mass causes the sensor to respond inertially under the influence of acceleration. The film element bends as the mass stands still, leading to extremely high voltage sensitivity (around 1 V/g). A variant of this component detects vital signs when a “smart badge” (equipped with RF telemetry) is worn by a staff member or patient and enables a periodic signal to be transmitted for tracking or location purposes. The badge goes into sleep mode when the sensor detects that the badge has been taken off a live person, but is kept “awake” by muscle tremor, gross bodily movement, or even vibration from the pulse. The standard sensor can reveal detail of heart “sounds” when held against the chest using a light elasticated strap. With a very low frequency limit selected in the electronic interface, it is possible to see breathing rate also (Figure 3). In that waveform, the movement of the chest wall shows up as slow periodic signal with approximately a four second period, while individual heartbeats can be seen at around 1/s (60 bpm). To eliminate the breathing signal and remove some noise, it is possible to apply filters at 1 Hz (lower) and 10 Hz (upper) to obtain realtime signals (Figure 4). Note that the traces in the Figure 4 waveform are all taken from a patient at rest. Naturally, using an accelerometer, bodily movement can easily dominate signals from the heartbeat. In fact, a tiny implementation (active sensor dimensions 1.3 x 3 mm) of just such a cantilever beam acceleration sensor is used within a pacemaker to detect the level of physical activity of the patient, so that the pacing rate can be adjusted accordingly.
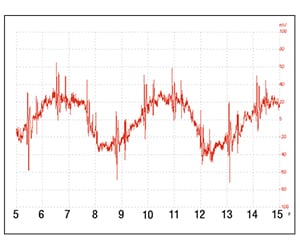
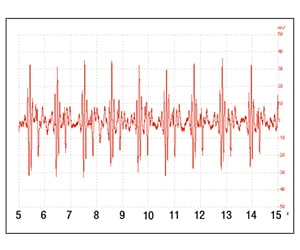

Applications
Several electronic stethoscopes have used piezo film as the active sensing element, due to its robustness, high sensitivity, and broad bandwidth. Here, the sensing element must be held with some “reaction force” against the body – normally using a conventional massive bell design as for a direct acoustic stethoscope. Once the dynamic pressure signal has been converted into an electrical signal, the information content can be enhanced by selective filtering or amplification, played back as an audio signal, analyzed using more complex algorithms to detect specific conditions, transferred over data link to remote base station for further analysis and storage, and so on. Using a compact acoustic sensor means that more than one point can be monitored simultaneously.
Using a compact acoustic sensor means that more than one point can be monitored simultaneously.
Moving further away from direct contact with the body, both piezo film and piezo cable have been used as part of a mattress to detect heartbeat, breathing, and bodily movement of a patient. An array of sensors can be integrated into a mattress coverlet that passively measures patient information as the patient lies or sits upon these collection devices, providing accurate measurements even through clothing, gowns, or sheets. Static “presence” is detected by flexible switches, while piezo film elements convert all dynamic vital signs from the patient into corresponding electrical signals, that can be displayed on a bedside unit with alarm logic. The system can give early warning of heart or respiratory rate abnormalities as well as unauthorized bed exit, all without direct patient contact.

Conclusion
As shown in the variety of applications featured, piezo film presents an excellent alternative to more traditional electronic components for transmitting vital data to patient monitoring systems. As a result of its array of benefits, this technology may be implemented into more life saving medical devices in the future.
