Quick-Turn Molding of Functional Elastomeric Seals for Harsh Environment
ABSTRACT
A quick-turn and low-cost process for making functional prototype or high mix low volume (HMLV) sale-able elastomeric seals is demonstrated using 3D printed plastic or polymer molds. We demonstrate that this simple and versatile process is capable of molding different TE production grade silicones and fluorosilicones, producing a variety of complex functional seal designs with fine details and precision that meet our customer requirements.
PROBLEM STATEMENT
Elastomeric seals are essential components that protect the electrical contacts in connectors, sensors and cable assemblies from corrosion due to harsh environmental factors such as moisture, gases, dust, fluids and other chemicals. TE offers a large portfolio of seal designs including facial seals, family seals, cable seals, peripheral seals, and O-rings. The seals need to meet challenging customer requirements for different connectors and electrical components.
The objective of our work has been to develop a versatile, quick-turn and low-cost process that can produce functional prototype and or HMLV saleable seals that can be made in production grade materials ranging from liquid silicone rubber (LSR) to high consistency rubber (HCR) or gum stock fluorosilicones (consistency of clay or putty-like material) to rubbers and other elastomer classes. Further, the quick-turn seals should be able to be qualified to the three key criteria of form, fit and function (i.e. able to meet dimensional, assembly and functional testing requirements). A quick-turn process provides TE engineers with the ability to rapidly qualify seals while comparing different versions of a seal design in different materials with varying properties (e.g. hardness, compression set, tear strength, chemical resistance). TE engineers will now not only be able to provide parts quickly to end-customers but also get faster feedback from product testing.
Here we demonstrate use of 3D printed polymer molds for molding elastomeric seals that can achieve the above-mentioned criteria. The advantage of this process lies in its simplicity and adaptability to work with both liquid and gum stocks. A variety of photo-polymerization based printing technologies, namely stereolithography (SLA), monomer jetting and digital light processing (DLP) as well as different mold materials have been evaluated, and appropriate printer/material combinations identified for printing polymer molds capable of withstanding typical molding conditions (e.g. high temperature and pressure). Outside TE, suppliers continue to develop new polymer mold materials geared towards injection molding of thermoplastics [1].
We have also benchmarked the functional performance of seals made from printed polymer molds vs. metal molds, and the overall process time/cost savings associated with prototyping using polymer molds. Further we highlight the importance of choosing the right polymer mold material and mold processing conditions, the capabilities and limitations of polymer molds.
METHODS AND RESULTS
Printers and Materials
The primary printers used in this study were commercial SLA, DLP and monomer jetting printers and various commercial resin materials for printing molds. Aspects such as differences in print quality/accuracy, mold surface roughness and mold reusability will be described in the discussion section.
Our process is capable of molding commercial grades of silicone and fluorosilicone materials such as high consistency rubbers (HCR) (also known as gum stock or solid silicones) and liquid silicones (e.g. 2 part). The curing temperatures of these grades is typically > 150 ºC. The grades used in this study range from 20 to 70 shore hardness (e.g. shore A 20 or shore A 50) and are suitable for harsh environmental exposure.
Process Description
Polymer Mold Preparation: Multi-cavity molds were designed using seal models. 3D CAD mold models (.stl format) were used for creating slice or layer files for 3D printing. After 3D printing, molds (Figure 1a) were cleaned in organic solvents to remove any excess resin on the surface of the mold, followed by degassing/UV treatment, and then heat treating at an appropriate temperature to ensure that the printed molds were completely cured. We found that it is crucial to heat cure the polymer mold materials at an appropriate temperature, otherwise the silicone may not cure completely in the polymer mold, remaining tacky to touch.
Metal Molds: 4-cavity steel molds were prepared by conventional machining. Steel molds were cleaned using a degreasing solvent and then used for silicone molding.
Molding Process: The 3D printed polymer molds were sprayed with a silicone-based mold release before molding We have extended the use of 3D printed molds to various molding processes such as injection, transfer and compression molding. We have developed expertise around polymer mold design, tuning molding process and using non-conventional approaches, given the limited tool life due to lower strength/thermal conductivity of the polymer mold material. Typically molding with polymer tool would require a higher cycle time, which is acceptable for prototyping purposes. It is critical to choose an appropriate mold material as the polymer molds were subjected to 180 ºC in our process for curing the silicones.
After de-molding, the seals were manually deflashed and then post-cured for an additional 10 to 120 min at 180 ºC to ensure complete curing. Depending on the durability of the core features, the molds could be either one-time use or reusable. For comparison, seals were also made from machined metal molds using a standard molding process.
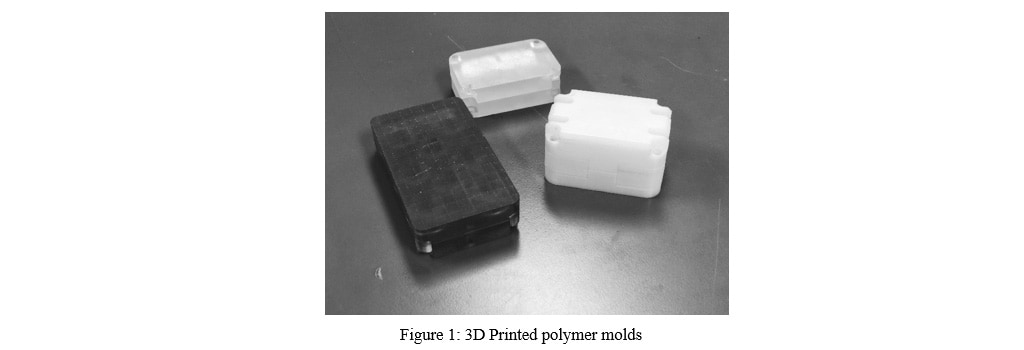
Figure 2a-g shows examples of molded seals produced using different printed polymer mold materials in a variety of shapes, sizes, complexity and silicone material types. Using high resolution polymer molds, we were able to mold small grommet seals (Figure 2b-c) with a complex hole profile (hole diameter 1.01 mm, minimum diameter in the hole profile 0.53 mm, wall thickness between two holes just 0.25 mm). Figure 2e-f shows an example of an automotive seal design with small features (smallest wall thickness of 0.35 mm and small holes with 0.69 mm diameter) that were molded successfully. Figure 2g shows examples of automotive single wire, peripheral and grommet seals.
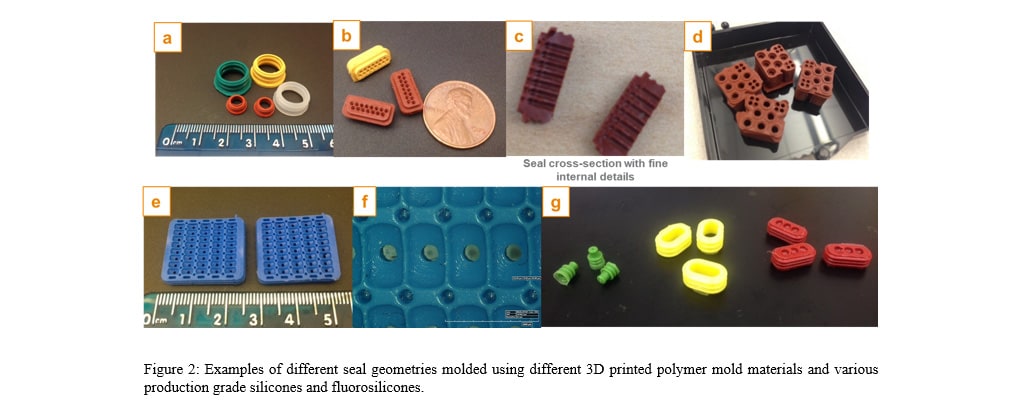
Seal Functional Testing Results
Functional seals (Figure 2a) for an aerospace customer, prepared using a) 3D printed polymer molds, and b) steel molds, were assembled in Aluminum terminals, followed by wire insertion and crimping (see Figure 3). All seals passed the assembly and the dimensional requirements (seal gland diameters were within the allowed tolerance of 0.1 mm). The assembled terminals were pressurized at the wire end and air leak tested under water at 1 bar and 2 bars. Leak testing was done before and after parts were subjected to a) 10 cycles of thermal shock (-65 ºC to 180 ºC) and b) temperature conditioning (180 ºC for 5 days). The requirements for seal design qualification from the customer were to pass all tests at 1 bar without leakage.
Prototype seals were made for various wire sizes and different silicone and fluorosilicone materials were screened by leak testing. A suitable grade of HCR silicone material was shortlisted based on an acceptable leak test performance. Seals from polymer molds for all wire sizes passed the leak test before and after thermal shock conditioning, which is a very encouraging result. Further all polymer mold seals for larger wires (AWG 000, 00, 0A, 1, 2, 3) passed the leak test after the five-day temperature conditioning at 180 ºC. The prototyping process using polymer mold also allowed us to quickly qualify smaller AWG 8 seals with a modified design (thicker wall, 1.99 mm) that passed all the leak tests. Our results show that the prototype seals from the polymer molds are able to pass the functional requirements similar to metal molds.
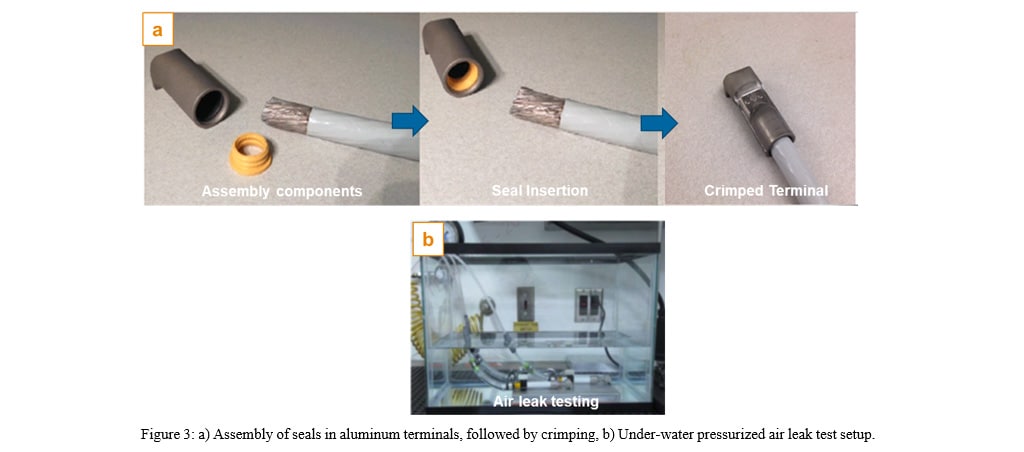
DISCUSSION AND KEY POINTS
3D Printed Polymer Mold Capabilities & Limitations
The molding process using multi-cavity 3D printed polymer molds can produce intricate and complex seal designs applicable to a large portfolio of TE seals. The number of cavities per polymer mold can range from 1 for larger sized seals to > 35 for smaller sized seals. SLA printers typically use a laser, providing highest accuracy and best feature resolution (note that SLA can also print sharp features or corners), closely followed by DLP printers that use light projection technology followed by monomer jetting printers that cure photopolymers using broadband UV light (note that sharp corners print rounded). Over-curing of resin near feature edges due to light penetrating deeper than desired can affect resolution and accuracy of the printer.
Surface roughness of the printed molds varies by printer and material being printed. Surface roughness is inherent to layer by layer printing (e.g. layer thickness 0.05 mm for SLA) and stair stepping effect (surfaces built at an angle) that can be clearly seen in the microscopic image of an SLA mold feature (Figure 4a). The surface topography of the polymer mold surface is clearly replicated on the molded seals (Figure 4b). The molded seal surface roughness from a polymer mold is higher than that of the seals from the metal molds (Figure 4c). Additional roughness may be present in areas where support material is removed from the mold surface. The additional surface roughness may not be acceptable for some sealing applications. Note that is also possible to use hybrid tooling, in which printed polymer molds are combined with metal core pin inserts for applications requiring extremely low surface roughness sealing surfaces.
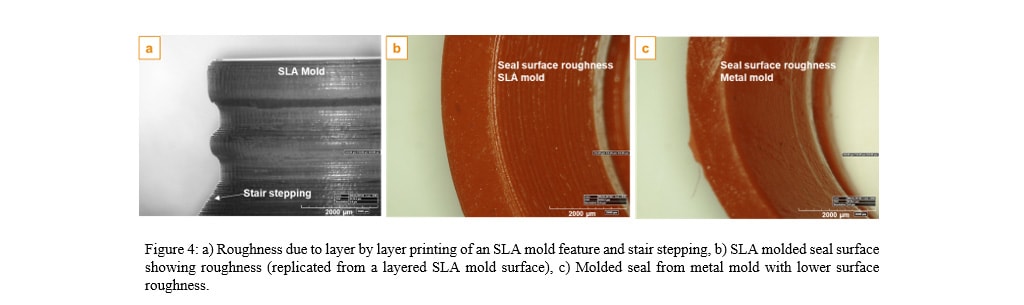
The life of the polymer molds is limited unlike the metal molds. The mechanical properties of the polymer molds drop significantly at the higher temperatures, especially above the heat deflection temperature [2]. The reusability of the molds strongly depends on the minimum core feature size as well as the molding process parameters such as mold temperature, pressure etc. For example, molds with larger core features could be used multiple times before the polymer mold cracks whereas smaller core feature breakage would limit the number of shots per mold. For seals with extremely small geometry (not achievable by printing) and or when large number of parts are needed, it may be desirable to use hybrid tooling (i.e. printed polymer mold with metal core pin inserts), rather than sacrificial or one-time use polymer molds.
Cost/Time
Our internal mold printing costs were significantly lower for a printed polymer multi-cavity molds vs. a machined metal mold from an external vendor. For printed molds, the total time needed from the mold design to molded seals was 2 weeks vs. 8-10 weeks for an external vendor.
SUMMARY
In summary, we have developed a unique capability for quick-turn molding of seals in different TE production grade silicones and fluorosilicones using 3D printed polymer molds. The key to this capability is the expertise around polymer mold design, tuning the molding process and using non-conventional approaches, given the limited tool life of the polymer mold material. The rapid turnaround ability from CAD design to producing fully functional seals helps TE engineers to rapidly qualify seals while comparing various seal designs/materials and provide parts quickly to end-customers for faster feedback from product testing. Our quick-turn molding process is a valuable tool that can offer significant cost/time savings for producing fully functional prototype or HMLV seals that meet all customer requirements.
ACKNOWLEDGEMENTS
The authors would like to thank Martin Bayes, John Wasserbauer, and Bob Zubrickie (Corporate Technology), Nicholas Ruffini, Kenneth Dowhower (A D & M) and Galen Martin (Automotive) for their valuable support for this work.
REFERENCES
[1] L. Zonder, N. Sella, “Precision Prototyping: The role of 3D printed molds in the injection molding industry,” Stratasys.
[2] G. A. Mendible, “Applications of transient cooling simulations in injection molding”, Ph.D. Thesis, University of Massachusetts Lowell, 2015.
Quick-Turn Molding of Functional Elastomeric Seals for Harsh Environment
ABSTRACT
A quick-turn and low-cost process for making functional prototype or high mix low volume (HMLV) sale-able elastomeric seals is demonstrated using 3D printed plastic or polymer molds. We demonstrate that this simple and versatile process is capable of molding different TE production grade silicones and fluorosilicones, producing a variety of complex functional seal designs with fine details and precision that meet our customer requirements.
PROBLEM STATEMENT
Elastomeric seals are essential components that protect the electrical contacts in connectors, sensors and cable assemblies from corrosion due to harsh environmental factors such as moisture, gases, dust, fluids and other chemicals. TE offers a large portfolio of seal designs including facial seals, family seals, cable seals, peripheral seals, and O-rings. The seals need to meet challenging customer requirements for different connectors and electrical components.
The objective of our work has been to develop a versatile, quick-turn and low-cost process that can produce functional prototype and or HMLV saleable seals that can be made in production grade materials ranging from liquid silicone rubber (LSR) to high consistency rubber (HCR) or gum stock fluorosilicones (consistency of clay or putty-like material) to rubbers and other elastomer classes. Further, the quick-turn seals should be able to be qualified to the three key criteria of form, fit and function (i.e. able to meet dimensional, assembly and functional testing requirements). A quick-turn process provides TE engineers with the ability to rapidly qualify seals while comparing different versions of a seal design in different materials with varying properties (e.g. hardness, compression set, tear strength, chemical resistance). TE engineers will now not only be able to provide parts quickly to end-customers but also get faster feedback from product testing.
Here we demonstrate use of 3D printed polymer molds for molding elastomeric seals that can achieve the above-mentioned criteria. The advantage of this process lies in its simplicity and adaptability to work with both liquid and gum stocks. A variety of photo-polymerization based printing technologies, namely stereolithography (SLA), monomer jetting and digital light processing (DLP) as well as different mold materials have been evaluated, and appropriate printer/material combinations identified for printing polymer molds capable of withstanding typical molding conditions (e.g. high temperature and pressure). Outside TE, suppliers continue to develop new polymer mold materials geared towards injection molding of thermoplastics [1].
We have also benchmarked the functional performance of seals made from printed polymer molds vs. metal molds, and the overall process time/cost savings associated with prototyping using polymer molds. Further we highlight the importance of choosing the right polymer mold material and mold processing conditions, the capabilities and limitations of polymer molds.
METHODS AND RESULTS
Printers and Materials
The primary printers used in this study were commercial SLA, DLP and monomer jetting printers and various commercial resin materials for printing molds. Aspects such as differences in print quality/accuracy, mold surface roughness and mold reusability will be described in the discussion section.
Our process is capable of molding commercial grades of silicone and fluorosilicone materials such as high consistency rubbers (HCR) (also known as gum stock or solid silicones) and liquid silicones (e.g. 2 part). The curing temperatures of these grades is typically > 150 ºC. The grades used in this study range from 20 to 70 shore hardness (e.g. shore A 20 or shore A 50) and are suitable for harsh environmental exposure.
Process Description
Polymer Mold Preparation: Multi-cavity molds were designed using seal models. 3D CAD mold models (.stl format) were used for creating slice or layer files for 3D printing. After 3D printing, molds (Figure 1a) were cleaned in organic solvents to remove any excess resin on the surface of the mold, followed by degassing/UV treatment, and then heat treating at an appropriate temperature to ensure that the printed molds were completely cured. We found that it is crucial to heat cure the polymer mold materials at an appropriate temperature, otherwise the silicone may not cure completely in the polymer mold, remaining tacky to touch.
Metal Molds: 4-cavity steel molds were prepared by conventional machining. Steel molds were cleaned using a degreasing solvent and then used for silicone molding.
Molding Process: The 3D printed polymer molds were sprayed with a silicone-based mold release before molding We have extended the use of 3D printed molds to various molding processes such as injection, transfer and compression molding. We have developed expertise around polymer mold design, tuning molding process and using non-conventional approaches, given the limited tool life due to lower strength/thermal conductivity of the polymer mold material. Typically molding with polymer tool would require a higher cycle time, which is acceptable for prototyping purposes. It is critical to choose an appropriate mold material as the polymer molds were subjected to 180 ºC in our process for curing the silicones.
After de-molding, the seals were manually deflashed and then post-cured for an additional 10 to 120 min at 180 ºC to ensure complete curing. Depending on the durability of the core features, the molds could be either one-time use or reusable. For comparison, seals were also made from machined metal molds using a standard molding process.
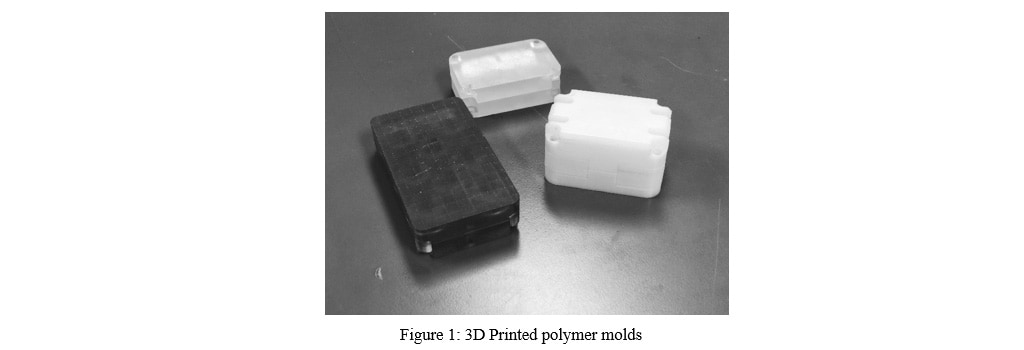
Figure 2a-g shows examples of molded seals produced using different printed polymer mold materials in a variety of shapes, sizes, complexity and silicone material types. Using high resolution polymer molds, we were able to mold small grommet seals (Figure 2b-c) with a complex hole profile (hole diameter 1.01 mm, minimum diameter in the hole profile 0.53 mm, wall thickness between two holes just 0.25 mm). Figure 2e-f shows an example of an automotive seal design with small features (smallest wall thickness of 0.35 mm and small holes with 0.69 mm diameter) that were molded successfully. Figure 2g shows examples of automotive single wire, peripheral and grommet seals.
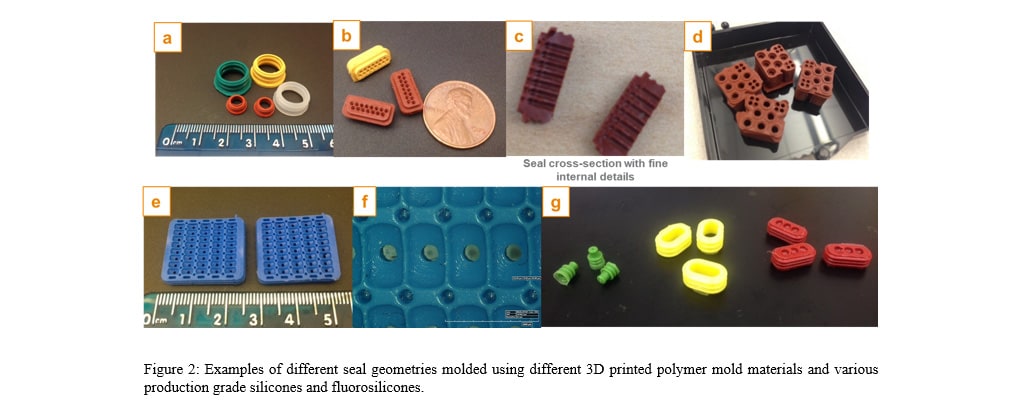
Seal Functional Testing Results
Functional seals (Figure 2a) for an aerospace customer, prepared using a) 3D printed polymer molds, and b) steel molds, were assembled in Aluminum terminals, followed by wire insertion and crimping (see Figure 3). All seals passed the assembly and the dimensional requirements (seal gland diameters were within the allowed tolerance of 0.1 mm). The assembled terminals were pressurized at the wire end and air leak tested under water at 1 bar and 2 bars. Leak testing was done before and after parts were subjected to a) 10 cycles of thermal shock (-65 ºC to 180 ºC) and b) temperature conditioning (180 ºC for 5 days). The requirements for seal design qualification from the customer were to pass all tests at 1 bar without leakage.
Prototype seals were made for various wire sizes and different silicone and fluorosilicone materials were screened by leak testing. A suitable grade of HCR silicone material was shortlisted based on an acceptable leak test performance. Seals from polymer molds for all wire sizes passed the leak test before and after thermal shock conditioning, which is a very encouraging result. Further all polymer mold seals for larger wires (AWG 000, 00, 0A, 1, 2, 3) passed the leak test after the five-day temperature conditioning at 180 ºC. The prototyping process using polymer mold also allowed us to quickly qualify smaller AWG 8 seals with a modified design (thicker wall, 1.99 mm) that passed all the leak tests. Our results show that the prototype seals from the polymer molds are able to pass the functional requirements similar to metal molds.
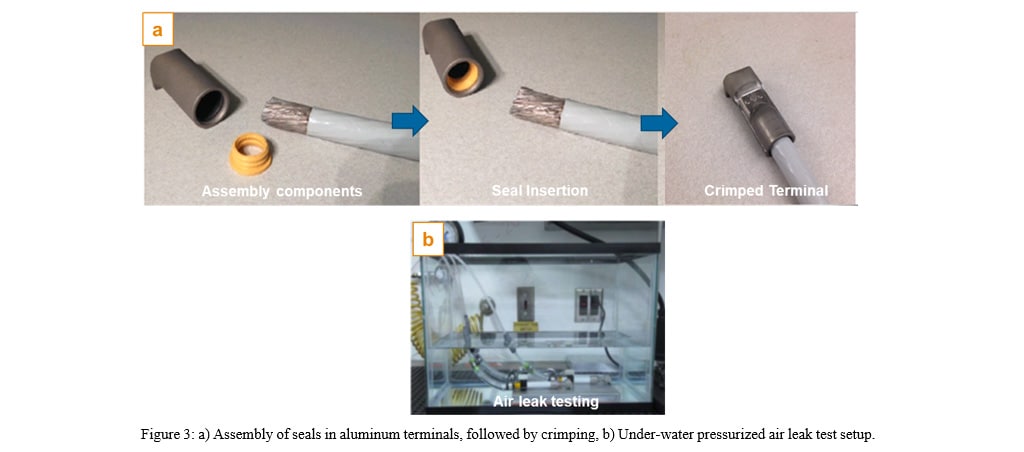
DISCUSSION AND KEY POINTS
3D Printed Polymer Mold Capabilities & Limitations
The molding process using multi-cavity 3D printed polymer molds can produce intricate and complex seal designs applicable to a large portfolio of TE seals. The number of cavities per polymer mold can range from 1 for larger sized seals to > 35 for smaller sized seals. SLA printers typically use a laser, providing highest accuracy and best feature resolution (note that SLA can also print sharp features or corners), closely followed by DLP printers that use light projection technology followed by monomer jetting printers that cure photopolymers using broadband UV light (note that sharp corners print rounded). Over-curing of resin near feature edges due to light penetrating deeper than desired can affect resolution and accuracy of the printer.
Surface roughness of the printed molds varies by printer and material being printed. Surface roughness is inherent to layer by layer printing (e.g. layer thickness 0.05 mm for SLA) and stair stepping effect (surfaces built at an angle) that can be clearly seen in the microscopic image of an SLA mold feature (Figure 4a). The surface topography of the polymer mold surface is clearly replicated on the molded seals (Figure 4b). The molded seal surface roughness from a polymer mold is higher than that of the seals from the metal molds (Figure 4c). Additional roughness may be present in areas where support material is removed from the mold surface. The additional surface roughness may not be acceptable for some sealing applications. Note that is also possible to use hybrid tooling, in which printed polymer molds are combined with metal core pin inserts for applications requiring extremely low surface roughness sealing surfaces.
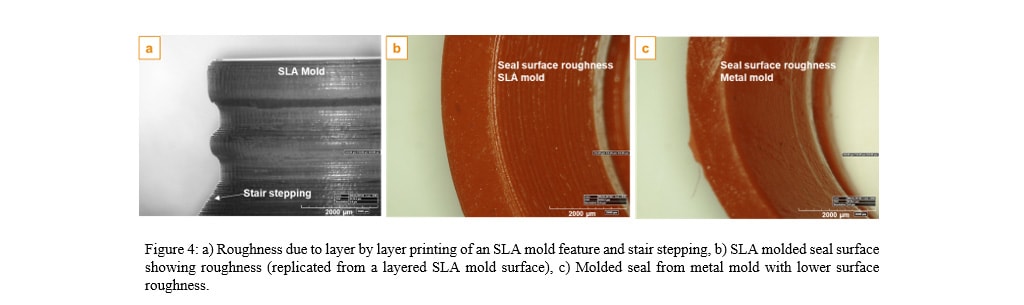
The life of the polymer molds is limited unlike the metal molds. The mechanical properties of the polymer molds drop significantly at the higher temperatures, especially above the heat deflection temperature [2]. The reusability of the molds strongly depends on the minimum core feature size as well as the molding process parameters such as mold temperature, pressure etc. For example, molds with larger core features could be used multiple times before the polymer mold cracks whereas smaller core feature breakage would limit the number of shots per mold. For seals with extremely small geometry (not achievable by printing) and or when large number of parts are needed, it may be desirable to use hybrid tooling (i.e. printed polymer mold with metal core pin inserts), rather than sacrificial or one-time use polymer molds.
Cost/Time
Our internal mold printing costs were significantly lower for a printed polymer multi-cavity molds vs. a machined metal mold from an external vendor. For printed molds, the total time needed from the mold design to molded seals was 2 weeks vs. 8-10 weeks for an external vendor.
SUMMARY
In summary, we have developed a unique capability for quick-turn molding of seals in different TE production grade silicones and fluorosilicones using 3D printed polymer molds. The key to this capability is the expertise around polymer mold design, tuning the molding process and using non-conventional approaches, given the limited tool life of the polymer mold material. The rapid turnaround ability from CAD design to producing fully functional seals helps TE engineers to rapidly qualify seals while comparing various seal designs/materials and provide parts quickly to end-customers for faster feedback from product testing. Our quick-turn molding process is a valuable tool that can offer significant cost/time savings for producing fully functional prototype or HMLV seals that meet all customer requirements.
ACKNOWLEDGEMENTS
The authors would like to thank Martin Bayes, John Wasserbauer, and Bob Zubrickie (Corporate Technology), Nicholas Ruffini, Kenneth Dowhower (A D & M) and Galen Martin (Automotive) for their valuable support for this work.
REFERENCES
[1] L. Zonder, N. Sella, “Precision Prototyping: The role of 3D printed molds in the injection molding industry,” Stratasys.
[2] G. A. Mendible, “Applications of transient cooling simulations in injection molding”, Ph.D. Thesis, University of Massachusetts Lowell, 2015.