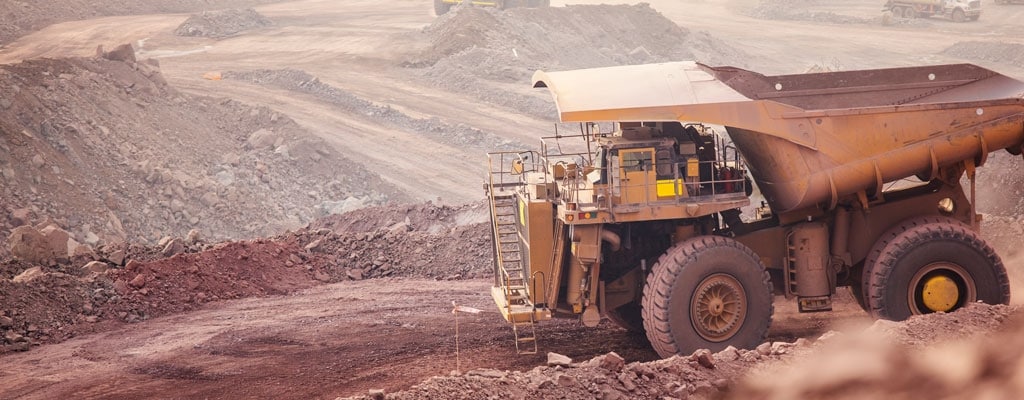
Trend Insight
Engineering Ethernet into Commercial Vehicles
Enabling advanced, data-heavy functionality means getting comfortable with integrating Ethernet into a mixed architecture.
Authors
By Joachim Barth, R&D/Product Development Engineering Manager, and Christian Manko, Data Connectivity Product Manager, TE Connectivity
Off-highway vehicles for agriculture, construction and mining are more connected than ever. As demands for safer, greener, and more productive commercial vehicles keep increasing, features such as advanced driver assistance systems (ADAS), 360-degree camera systems, proximity detection systems, vehicle-to-vehicle (V2V) and vehicle-to-infrastructure (V2X) communication and more are moving from “nice to have” to “need to have.” These functions need a massive amount of data and those data needs will increase exponentially over the coming years as greater functionality is added.
To increase the volume and speed of data transmitted in the vehicle, engineers need to make major changes to their vehicle electrical/electronic (E/E) architecture by either adding more dedicated CAN networks or integrating faster communication protocols like Ethernet, which can currently handle up to 1 GB per second of data.
Designing in Ethernet
Design engineers have options. Instead of replacing the entire existing communications network, most likely a CANbus protocol, they can design in Ethernet, where appropriate, for the functions customers most want—for example, telematics, diagnostics, and ADAS. Engineers must scale the whole system and use dedicated lines for Ethernet where it is needed to enable these advanced, data-heavy functions. Integrating Ethernet into the architecture can be challenging for OEMs, especially as this is a relatively new technology for the heavy-duty vehicle market, but the challenges can be overcome with the right expertise. Working early in the design phase with consultative suppliers who understand the complexity and have Ethernet expertise is key to a smooth design-to-production journey. Suppliers with automotive Ethernet expertise can help OEM designers optimize the topology and choose the right technology upfront to ensure signal integrity under harsh conditions while increasing sensing and computing power for all the latest functions and applications.
Depending on the E/E architecture, as more advanced and automated features are added, designers will need to design in Ethernet switches. Unlike CAN and other previous protocols, the switch is needed to direct the signal with integrity and low latency to its desired destination. It’s important to consider early on where to place the switch, whether the switch should be in a new dedicated electrical control unit (ECU) or in an existing ECU, how many cables, connectors, and sensors will be needed, and where to place them. These considerations apply to every advanced functionality in the vehicle that requires Ethernet.
Generally, parts in agriculture, construction, mining, etc., must meet additional standards for ruggedness, especially if located on the outside of a vehicle, to protect against high vibrations, physical shock, dust, chemicals, and water. Plus, they must withstand temperature ranges of -40 C (-40 F) up to 125C (257 F) and allow field maintenance.
OEMs needing to upgrade the components, systems, and networks in their vehicles can feel confident knowing that many high-speed data applications can be designed using connector technology originally developed for and proven in the automotive industry. For example, we added robust housings and upgraded the design of our automotive MCON terminals to create a new sealed Ethernet connector enetSEAL+ that meets the 100BASE-T1 specification. The connector transmits data at up to 100 MB per second.
We also added a rugged, heavy-duty thermoplastic Ethernet connector (Heavy Duty Sealed Connector Series with MATEnet Inserts) to our heavy-duty sealed connector series that can transmit data at rates up to 1 GB per second. Because it is compatible with our MATEnet interconnection system, it offers designers flexibility and scalability—OEMs can use unshielded or shielded twisted pair cables and design in multiple hybrid interfaces.
The point is to choose solutions like these that adapt to virtually any harsh environment/heavy-duty vehicle application meant to enhance safety, productivity, or infotainment, including telematics, onboard diagnostics, multifunction displays, onboard cameras, radar and lidar, and more.
Engineering Challenges
Using Ethernet for E/E architecture is a huge step! The CANbus protocol has been used in vehicles for over 30 years.
Using Ethernet for E/E architecture is a huge step because it is much faster and more complex. When designing a mixed architecture using Ethernet only where appropriate, the faster Ethernet network will still need to be able to “talk” to the slower CAN network, so engineers must design in a gateway that translates faster messages so CAN is able to receive and understand them.
Most connector systems already using Ethernet are first-generation 100 MB speed. The second generation is ten times faster at 1 GB, requiring higher frequency transceivers in the ECUs that need to be qualified for the different kinds of architectures and topologies inside a vehicle. Without much experience with this protocol, engineers are still learning how the mechanical surroundings in a heavy-duty vehicle will influence the electrical performance of the communications.
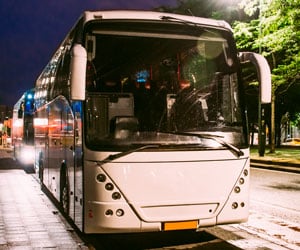
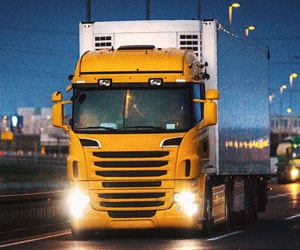
Ethernet operates at higher frequencies and thus is more sensitive when placed near other electronics or metallic parts. Tolerances have to be lower and designers need to account for potential EMI, mechanical disturbances, quality issues on the cable, and more. On a component level, when designing the physical layer, the connectors and cables must fulfill requirements for their dedicated line and function as well as for the whole system. With every part, designers must make sure there are no harmful emissions that disturb other nearby systems and that other nearby systems’ emissions will not disturb that part.
Placement is key to avoid interference from antennas or other components emitting strong electromagnetic fields. Choosing where to use shielded and unshielded components and systems is also important. Every aspect of the physical layer needs to be controlled regarding balance and EMI.
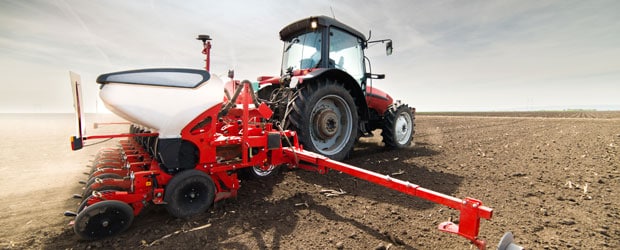
In addition to electromagnetic and mechanical disturbances, it’s vital to understand how different job sites (such as a farm, construction site, or mine) and product applications can affect the electrical performance of the vehicle’s communications system. Factors like extreme temperature, high mechanical loads, chemical exposure, and excessive dust can have negative effects on cables and connectors that are needed for Ethernet data links and, therefore, must be considered early in the design.
The tremendous size of many off-highway vehicles can also create challenges for signal integrity for Ethernet applications, having to maintain it through up to 40-m (131.2 ft.) links, while withstanding harsh conditions due to the off-highway environment. Because 40-m cables are used in industrial/commercial transportation, not in automotive, all ECUs and products used in the physical layer—cables, connectors, and transceivers—need to be adapted to the 40-m standard. The Ethernet standard specifies for up to four in-line connections. The quality of the communication link depends on how long each segment is (between one connector and another) and where it is routed through the vehicle.
Therefore significant testing is imperative. All components (ECUs, cables, connectors, transceivers, etc.) and systems need to be validated and qualified for use in commercial vehicles. It’s important to test configurations in different ways to see which way works best and is most stable. The entire vehicle should then be placed in an EMI chamber and tested in different ways as well— testing configurations inside the truck and simulating different conditions and different combinations of conditions that the vehicle may encounter.
Common Mistakes
Designers cannot approach Ethernet the same way as other communication protocols. Designing Ethernet into heavy-duty vehicles takes much more thought and effort than with other networks because of the complexity already described here. We have seen designers try to use interfaces common to office environments and consumer goods, like RJ45 or USB. These connectors were not developed for use in harsh environments and should not be utilized.
RJ45
Common to office environments
USB
Common to consumer goods
In general, a common mistake to avoid is underestimating the effects mechanical influences have on the communication link. This also includes temperature, humidity, and other environmental conditions that can affect material properties and therefore affect the communication links. Currently, there are only two standards for Ethernet in automotive, which are differentiated by speed—100 MB and 1 GB (1,000 MB). Every component on the physical layer—the transceivers, connectors, and cables—and the routing must be examined closely and tested to make sure they will be stable and perform in all conditions at all times.
Industry Trends
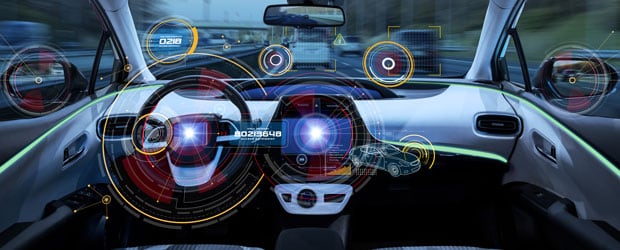
Meet the future's requirements, today. Buyers across agricultural, construction, and mining industries are looking for functionality that enables greater productivity, safety, and sustainability. Engineering Ethernet into these vehicles and machinery is a must not only for today’s demands but also to meet data-heavy connectivity demands of the near and long-term future, as today’s technologies are a stepping stone to greater, and eventually full, autonomy.
To Learn More About our Solutions for Connected Vehicles
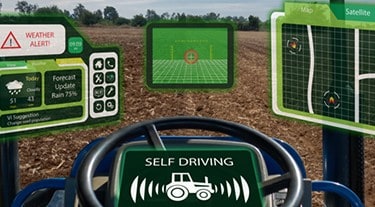
Autonomous Driving
Ethernet Solutions
Learn more about the connectivity requirements to enable commercial and industrial vehicles autonomous driving.
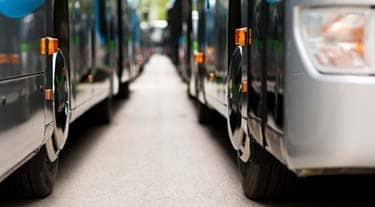
Data Connectivity
Heavy-Duty Vehicles Solutions
Discover why design engineers must consider incorporating Ethernet systems in their industrial and commercial vehicles and machinery to meet future customers' needs.
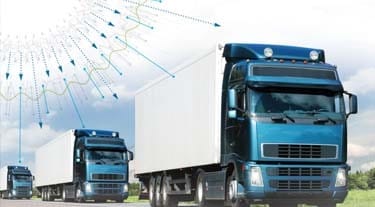
Ethernet Connectivity
Heavy-Duty Vehicles Requirements
Discover the considerations we took to design our Ethernet connectors for heavy-duty vehicles.
Originally published on oemoffhighway.com