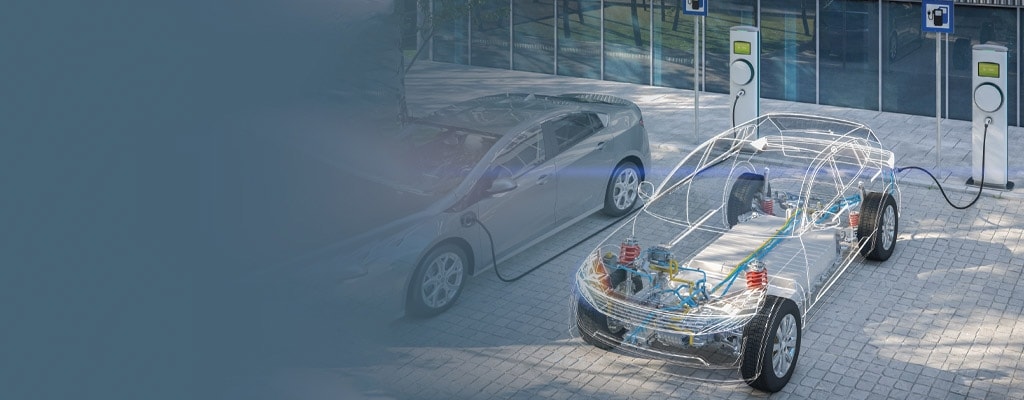
White Paper:
BCON+ High Voltage Connection System
Touch-safe bolt termination for traction batteries.
Authored By:
Alexander Ginsburg, TE Connectivity
Frank Kaehny, TE Connectivity
Uwe Hauck, TE Connectivity
Our new BCON+ high voltage connection system is a versatile, compact, robust, and touch-safe solution for interconnecting cell modules inside a traction battery and high voltage connection points outside the battery. The BCON+ connection system combines the advantages of solid steel-to-steel bolt termination with the extremely low contact resistance of copper contact elements. The system is touch-safe in unmated and mated condition. It flexibly interconnects with a large number of available conductors and cross-sections.
Touch-Safe High-Voltage Battery Connectivity Solutions (English)
On-Demand Webinar
TE Connectivity's Alexander Ginsburg discusses solutions for battery pack connectivity during this one-hour webinar with SAE. Watch the on-demand version now.
The Electrification Challenge
Increased pressure to reduce carbon emissions is driving the introduction of electrified propulsion systems within vehicles. The primary source of electric energy comes from the battery, while in a hydrogen fuel cell vehicle, the battery functions as a peak load buffer. The battery is therefore the core of powertrain electrification. Batteries used in these applications consist of many individual cells that are grouped into modules. During all vehicle operation modes, energy must flow safely in and out of the battery. Therefore, module connections must be able to carry currents up to 600 Amp for minutes during a high-power charge cycle but up to a factor higher during dynamic drive modes lasting only seconds.
Battery module connections also constitute the physical layer for battery protection (overtemperature shut-down), battery management (charge states, e.g. state-of-charge SoC) and cell-balancing (charge voltage equalization between cells with different SoC levels). To ensure these operations, every individual transmission battery module must feature failproof electrical connections. This requires highly integrated contact systems, which must not only be capable of supporting full functionality over the vehicle’s complete lifespan (usually 300,000 km/186,500 miles over ten years) but are also robust enough to prevent vibration and temperature stress from unduly affecting the contacts’ mechanical and electric properties. Contacts must also be fully touch-safe in order to eliminate potential high-voltage and high-power hazards in both private and commercial vehicles and to ensure safety towards customers and service personnel as well as regulatory compliance.
Full touch protection of the connection systems in mated and unmated state enables safe handling of battery modules during battery assembly. In particular, regular inspection or repair scenarios over the course of a vehicle’s life, battery modules can be easily and safely handled by trained electricians without the need for expensive special tools or complicated safety procedures.
TE Connectivity has drawn from extensive automotive contact physics expertise in copper and aluminum connection technology to develop an innovative interconnection solution for traction batteries. The new BCON+ bolt termination system meets all requirements for this demanding application. The BCON+ high voltage connection system is a bolted termination that can be easily unmated (for diagnosis or recycling), while also being fully touch-safe with IPxxB protection following ISO 20653. The mechanical path of the bolt termination and the electrical path (low-impedance copper-to-copper connection) are functionally separated from each other to ensure robustness and easy handling of contacts in manufacturing conditions.
The BCON+ bolt termination system is designed for maximum flexibility of module connections and other power terminations in a wide variety of interconnection applications in electrical performance architectures. Figure 1.
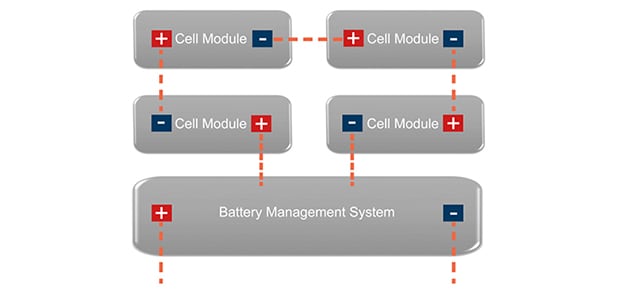
BCON+ Connection System
Development Objectives
Battery module contacts in an electrified vehicle have to meet very high requirements. Therefore, the objective was to design all conductors and connections to handle constant currents of 400 Amp (plus short peaks of up to 1,200 Amp) and voltages of up to 1,000 V, and to operate reliably at typical battery ambient temperatures from -40 °C to +80 °C. The finally selected connector materials will operate reliably even up to 140 °C. The main challenge was to achieve very low contact resistance at the individual contact points with minimal power losses, close to those of commercial battery cells. BCON+ contacts feature contact resistance of
<10 μΩ at each side over the complete interconnection system.
The module connector is designed to achieve vibration resistance for severity level 3 (LV214, SG 3), complying with environmental regulations for unsealed systems according to manufacturer test specification LV215.
A termination system of this type must offer easy and safe assembly. Depending on vehicle and battery configuration, it must also provide configuration flexibility. This applies to connections subject to geometric constraints as well as connecting different conductor types. In addition, module interconnections have to meet lifetime requirements of 300,000 km (186,500 miles) or ten years and withstand up to 25 mating and bolting cycles. In an electrified vehicle, the permanent charging stress further increases demands on battery component robustness and charging times must be added to the total operating time.
System Description
A BCON+ battery module termination consists of aluminum and copper profiles at the battery interface and of flexible conductor types on the steel-to-steel bonding side.
Actual cell interconnection is generally achieved by means of flat aluminum busbars, which serve as a contact to all cells interconnected within the module (as illustrated in figure 2). Each module is connected to the high voltage battery system via flat bolting connections made of solid copper (Cu-busbars). These integrate the bottom of the electroplated copper interface with a thread insert made of tempered steel. The interface with the plug-in socket is an inserted bolt integrated into the termination of a stranded copper wire (high voltage cable), which is converted to solid copper, or into a round massive conductor (figure 2).
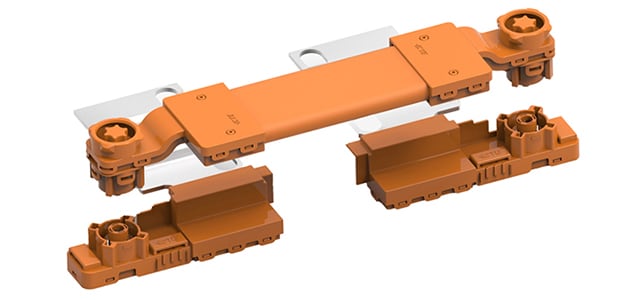
In BCON+ termination the high voltage cable contact is mated with the female copper interface (figure 3). Matching coding (= correct interconnection) releases a pre-latching process, which locks the cable to the busbar to enable easy two-handed assembly during the subsequent bolting process (also over-head assembly).
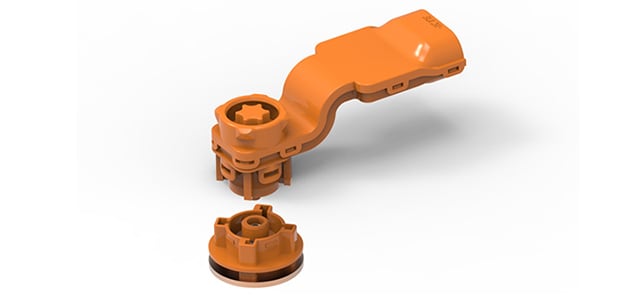
Both contact parts are enclosed in upper and lower casings made of glass fiber reinforced plastic to prevent inadvertent finger contact with live parts ((IPXXB = no contact with objects >12 mm diameter and max. 80 mm length). Flame resistance of plastic parts correspond to HB standard, V0 protection is available on request. The casing shape makes optimum use of available installation space (figure 4), ensuring maximum safety even in limited installation space. All live parts are enclosed in casings and covered either by silicon coating or high-temperature resistant glass fiber fabric jacket.
Interconnections between aluminum busbars and solid copper interfaces (i.e. the interconnection between stranded conductor on the cable side and copper interface) are created via various welding or bonding technologies.
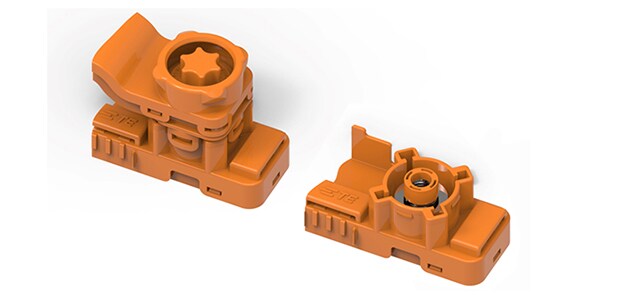
The captive M5 bolt used to tighten the round copper interfaces has been developed by TE Connectivity from tempered material. The bolt head is over molded with plastic and is tightened with a standard hexalobular internal. The steel bolt intersects both round interfaces with a flat mounting surface and then screws the threaded sleeve through the lower part of the BCON+ bolt termination connector (figure 5).
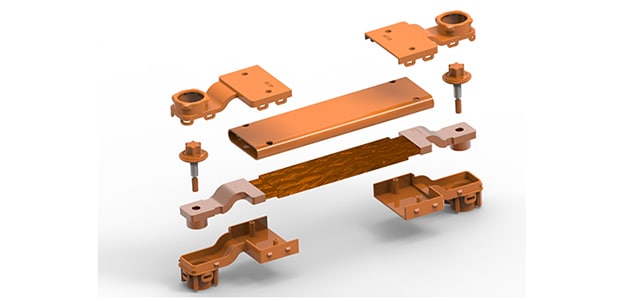
This construction applies mechanical tension only in the steel-to-steel system, fully separated from electrical interconnection function on the copper-to-copper current path established before by mechanical pre-tension (figure 6).
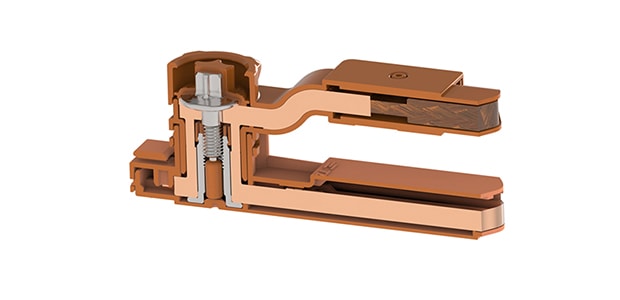
In order to address different contact challenges, solid copper busbars are available in a large variety of profiles including straight or angled versions and optional offsets (= varying offset heights).
Contacts on the interconnection’s bottom side can be differently coded and can be rotated in 90° increments to prevent inadvertent mating, i.e. incorrect coding of similar-looking interconnection cables onto the copper busbar.
Contact Details
Since no separable interface provided sufficiently low contact resistance, a bolt termination was selected. This delivered, at 400 Amp and required <10 μΩ, the necessary electrical connection performance in vibration scenarios. A bolt termination generates the required high contact normal force by means of an M5 bolt tightened with the required torque. The top and bottom of the electrical contact area consist of electroplated copper (Cu), ring-profiled with a flat surface. This geometry maximizes the electrical contact interface surface area. The bolt design considers the different coefficients of thermal expansion of both copper and steel, resulting into minimal torque loss after environmental exposure at low (-40°C) and high (+140°C) temperatures. In environmental testing, according to LV215, BCON+ bolt terminations maintained the specified re-tightening torque until the end of their life, thus demonstrating functional safety.
Connection Points & Possible Contacts
Space-saving butt joints between the solid copper busbars and individual electrical conductors can be created, for example, by means of hard solder resistance butt-welding. Thanks to the higher electrical resistance of hard-solder materials in between both connecting partners, the welding current generates local melting of the connecting elements in the solder area, with subsequent substance-to-substance low-resistance butt-jointing of the contact partners. In stranded wires the cable tail is usually compacted before welding. Alternatively, a connection is also possible by means of overlapping, using conventional welding procedures. To make optimum use of the available space, however, we opted for butt-jointing. Figure 7 shows several geometric options. The BCON+ bolt termination is designed for conductor cross-sections from 16 mm2 to 100 mm2.
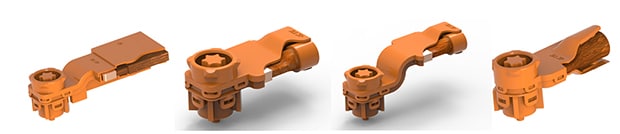
Connections are possible with round solid conductors, stranded wire conductors (round and flat), and (straight and offset) copper flat contacts. Fastening clips and protective covers against mechanical abrasion complete the portfolio.
Thanks to their extremely compact size, all system components are perfectly matched. This also applies to the two ring-profiled contacts of the electrical interconnection. Ideally, the ring-profiled contacts are integrated into the copper flat contact. However, they can also be welded to the copper flat contact as separate parts, or simply be dropped onto the copper flat contact. The required contact resistance determines which method may be used. As with the copper busbars, the contact rings are made of solid copper. The contact area is electroplated with silver (Ag) over nickel (Ni), with the Ni serving as diffusion barrier and the tarnish protected Ag lowering contact resistance and ensuring component shelf-life of up to one year following production. During production, the copper flat contacts are solidified at defined load. The offset copper flat contact versions function to leapfrog obstacles or compensate offsets.
Outlook
The actual contact resistance of <10 μΩ is an excellent achievement. It results mainly from the physically unavoidable losses caused by the copper’s electrical resistance (approx. 7 μΩ) and, to a smaller degree, from the contact resistance between the two ring-profiled contacts (approx.
3 μΩ). Additional requirements (e.g. splash water protection) can also be implemented in the same way. Furthermore, BCON+ bolt termination can be scaled for higher or lower current.
Summary
TE Connectivity’s BCON+ connection system is a highly functional low-resistance bolt termination system for reliable and fully touch-safe steel-to-steel bolting, even in limited space scenarios. Mechanical tension and electrical interface are completely separated from each other. At the same time, low contact resistance in combination with high durability and safety make the BCON+ bolt termination a reliable, safe high voltage connection for battery modules and additional high-power applications outside the battery.
The flexibility of interconnection options (various copper flat contacts shapes, various conductor options) enable different contact configurations and different geometrical contact formats (offset compensation, complex harness routing) with just one system. Different coding options and 90° increment rotation support safe assembly. Pre-latching of the bolt termination during mating simplifies handling during production. Touch-safety following IPXXB protects users during all relevant vehicle life stages (production, maintenance/repair – also in non-specialized garages –, recycling) from touching live parts.
The touch-safe, compact BCON+ bolt termination system is a flexible, scalable connection solution capable of being mass-produced for the battery. Touch-safe handling in unmated and mated condition and low-resistance electrical connectivity make the BCON+ connection system suitable for high volume applications, positioning the BCON+ module interconnection as a key component for enabling safe operation and safe handling of high voltage battery systems.