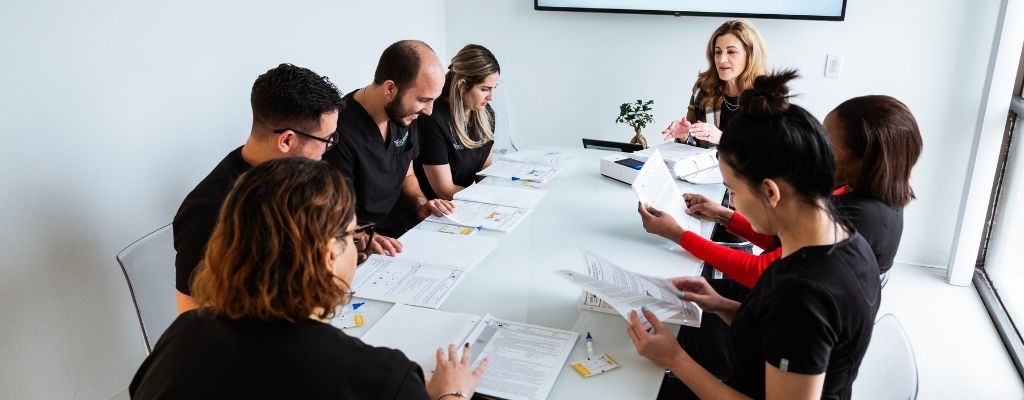
IVD Clinical Research (CRO) Services
TE Connectivity's full-service IVD clinical research organization (CRO) has the experience and clinical capabilities to help guide your IVD device to market quickly and successfully.
TE Connectivity (TE) is experienced in IVD clinical studies, regulatory submissions and clearances. Our team works in tandem with you during product development to fulfill clinical and regulatory needs, supporting you to get your device to market.
Established Clinical Experience
TE Connectivity’s IVD Solutions team has successfully led clinical development of 510(k)s, Dual Submissions, CE Mark/ IVDR, DeNovo and EUA submissions & clearances. TE has subject matter experts (SMEs) with extensive clinical and research expertise, and Clinical Research Associates (CRAs)
Extensive Clinical Footprint
TE has 300 well-established IVD clinical sites throughout the USA and is continuing to expand into Australia.
End-to-End Partnerships
From concept, and testing, to production, TE’s end-to-end services and diagnostic/biopharma partnerships offer our clients the opportunity to work with industry professionals and experienced CRAs at each stage of the IVD development process.

CRO SERVICE AREAS

SPEAK TO A SPECIALIST