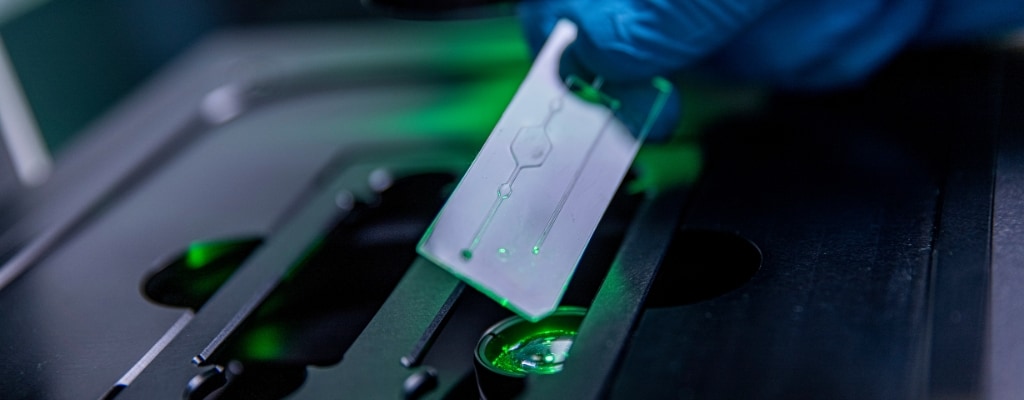
Selecting a Bonding Method for Microfluidic Chips
When an assay is migrated to a disposable cartridge format, one of the most overlooked considerations involves how to securely bond the layers of a microfluidic cartridge in a manner that does not adversely impact the performance of the device. The sealing of the open microchannels is necessary to produce the final enclosed fluid paths, and thus a critical step in the fabrication process invariably involves bonding a capping layer to the microchannel substrate. While bond strength and leakage prevention is certainly the baseline expectation, there are many other factors to consider including surface chemistry, optical properties, material compatibility, dimensional control and homogeneity of the channel sidewalls. Additional issues such as manufacturability and compatibility with off-chip interconnects can limit the selection of bonding methods.
Understanding Microfluidic Bonding Forces
Microfluidics bonding techniques can be indirect or direct. Indirect bonding involves the use of an adhesive layer to seal two substrates and encapsulate microchannels fabricated in one or both of the substrates. Direct bonding methods permanently bond the two substrates without any additional materials. Indirect bonding methods require an intermediate adhesive that results in channel sidewalls with different chemical, optical and mechanical properties than the bulk polymer. This may be a preferable requirement as a more hydrophobic surface may facilitate the fluidics of your sample and reagents.
In general, bonding forces between mating surfaces arise from either molecular entanglement or charge interactions. Entanglement can occur by mechanical interlocking of diffusion between surfaces, while bonding due to charge interactions can result from electrostatic or chemical (covalent) bonding, acid-base interactions, or van der Waals forces.
Thermoplastic bonding methods like thermal fusion bonding, ultrasonic bonding, chemical and solvent bonding, and laser welding are mainly achieved by molecular entanglement.
TE’s IVD Solutions team specializes in the design and manufacturing of microfluidic cartridges and can work with you to help create a design that meets your performance requirements.
Adhesive bonding is achieved from charge interactions. In most cases bonding at high temperatures can greatly enhance polymer entanglement and interaction at the bonding interface resulting in high bond strength.
However, bonding methods for microfluidic chips must be adapted and optimized for the task of enclosing micron-scale fluidic channels without excessive deformation of the channel cross sections.
15 Factors That Affect Selection of Bonding Technique
Your initial inclination may be to focus on the bonding method that offers the most consistent adhesion for your specific assay and substrate but there are many other factors to consider. Our suggestion is that you create a bonding method evaluation rating sheet like the one shown below. This will allow you to objectively rate each method you test. To take this to the next level, weight each specific characteristics that are most important to your assay rather than weighting each one equally.
This evaluation sheet could also become a part of your risk management and design control documentation.
Common Microfluidic Chip Bonding Techniques
Bonding two pieces of thermoplastic together is trickier than it may seem which is why you need to spend time understanding those limitations before you choose a specific method. Shown below are some of the most common bonding methods along with pros and cons of each.
UV Curable Resin Adhesive | Pressure Sensitive Adhesive (PSA) |
---|---|
A compatible resin is used to bond the two substrates to one another.
Advantages
Disadvantages
|
PSA films are a popular choice because there are numerous varieties to choose from and they offer many advantages.
Advantages
Disadvantages
|
Laser Welding | Thermal Fusion Bonding |
Polymer layers are melted together using a laser, forming a strong bond free from additives.
Advantages
Disadvantages
|
Application of heat and pressure at near glass transition temperature to fuse surfaces together, typically the same material.
Disadvantages
|
Ultrasonic Welding | Chemical Solvent Bonding |
Ultrasonic vibrations create a pure bond between substrates using energy directors.
Advantages
Disadvantages
|
Application of a chemical solvent to bond two surfaces together.
Advantages
Disadvantages
|
Material selection is a critical aspect of microfluidic chip design. Let the TE IVD Solutions team help you make the right choice.
Ways to Measure Microfluidic Thermoplastic Bonding Strength
Once you have narrowed down a few bonding methods you believe to be a good match with your particular assay, you'll need to conduct some performance tests. These tests can take many forms from simple to complex. Here are some common methods engineers use to test their bonding technology.
Delamination Tests - Just like it sounds this test relies on brute force to peel layers apart. This might be done with a scalpel or knife to wedge in between the two layers and pry them apart. While this is the cheapest and easiest test to conduct, there is no quantitative data output and it's difficult to reproduce consistently. This is the kind of test you might conduct when you're first doing initial “quick and dirty” comparative tests of different bonding techniques.
Peel Resistance Tests - This test requires one or more of pieces of the substrate to be flexible and be able to bend to 90 degree angle without breaking. Using a clamp, one piece of the substrate is bent to a 90 degree angle, slowly peeling it away from the other piece to which it is bonded. The peel force needed to separate the two pieces is then measured.
Tensile Strength Tests - Using a common tensile testing machine, grips or stronger adhesives are used to forcibly separate the two layers and in doing so measure the tensile strength of the bond. This method is commonly chosen because it is highly reproducible.
Shear Strength Tests - Although not as commonly used, this test uses a technique of sliding the substrate laterally along the bonding surface to measure the force needed to separate it from the lower piece which is held stationary. The challenge with this test is that the layers separate gradually and require a lot of monitoring.
Leakage Tests - This is definitely one of the more reliable ways to test the efficacy of the bond. Leakage tests are pretty simple to understand - you inject a liquid into the microchannels and see what happens over a set period of time. Often these tests are done using colored water/dye so leaks can easily be spotted. Other assays may necessitate using specific solutions that test durability and mechanical effects, e.g., mixing. Liquid injected can be static (pressurized or not) and/or have specific flow rates applied to also test component resilience.
Burst Pressure Tests - In this test, a specific PSI of pressure (example: 30-60 PSI) is applied in the form of gas or liquid and can be used to test the bond between substrates or between the blister and the substrate in the case of onboard reagent storage. For higher heat applications (e.g. PCR), it’s important to simulate the maximum reaction temperature with your test liquids since adhesives sometimes fail at higher temperatures.
Making Your Final Decision
Even after testing, the right bonding technology for your microfluidic cartridge may not be entirely obvious. In reality, there may be 2-3 bonding methods that seem to be a good fit for your application in bench tests. Which one to choose? This is why it is important that you work with someone who truly understands the specific manufacturing methods used to make your device at small, moderate and higher volumes. What may work at smaller volumes may not work well at larger volumes, or may hinder your ability to scale. Make that decision carefully. We can help.