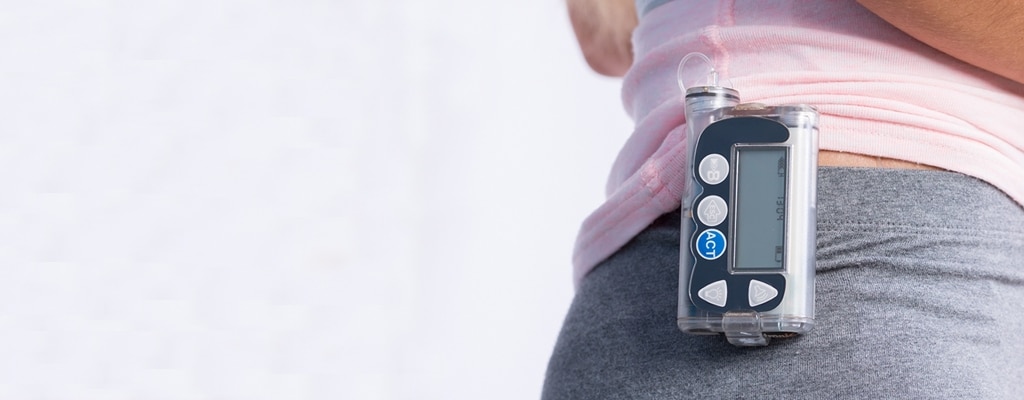
Application
Sensors for Insulin Pumps
Constantly monitoring medical conditions and controlling micro-doses of nutrients or medication has proven to benefit patients’ health. However, patients must have freedom to lead normal lives outside a medical facility.
A growing trend in healthcare to improve patients’ quality of life while reducing demand on medical facilities is through medical mobility. Accurate, reliable sensors drive lifesaving wearable pumps while technology is shrinking and advancing automation for medical wearables. Insulin pumps mimic a healthy pancreas, which is to regulate sugar in the bloodstream. Early insulin pumps were the size of a backpack. Today, technology and MEM sensors make it possible to provide effective glucose monitoring and insulin control in wearable devices smaller than a smartphone. These medical systems save patients from multiple pin pricks and self-injections every day. Mobile medical pumps require sensors that are reliable and accurate within a power efficient, small package. A safe pump collects and communicates accurate data. This requires a sensitive, robust design. For example, two types of strain gauges are used to detect blockages that affect the delivery of insulin; bonded foil and semiconductor.
Semiconductor gauges, such as TE’s FX29 compression load cells, are 75 times more sensitive. This MEMS technology delivers stiffer load bearing structure, smaller strain level, and produces 10 times the output. MEMS technology fits more sensors and value into medical wearables. Today's smart pumps can detect blockages (force sensors), air bubbles (ultrasonic sensors), volume and flow (position sensors), and more. Manufacturers must deliver precise, reliable sensors that combat fatigue, drift, and provide long-term stability in a highly regulated industry for customers that demand low cost. As the insulin pump market is expected to exceed $8 billion by 2027, we have the experience and experts necessary to continue producing medical sensors for the best value in healthcare.

