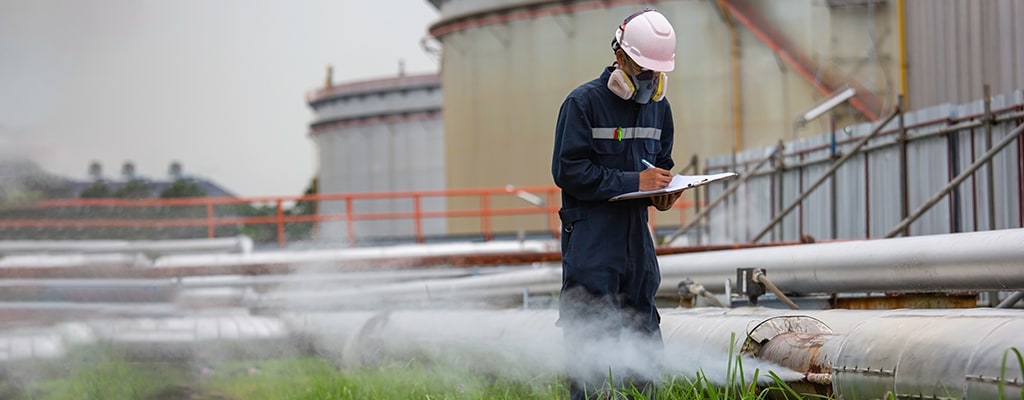
Industries
Detecting and Monitoring Corrosion Under Insulation in the Oil and Gas Industry
Corrosion Under Insulation (CUI) is a significant challenge across various sectors, particularly within the petrochemical and oil and gas industries. This pervasive issue, concealed beneath layers of insulation, often remains undetected until routine maintenance occurs. If overlooked, this issue can lead to compromised safety, environmental damage, operational disruptions, financial losses, regulatory non-compliance, shortened asset lifespan, and increased maintenance challenges, ultimately posing a grave risk of injuries or even loss of life. Reports suggest that CUI is responsible for 40% to 60% of pipeline repair costs (Dey, n.d.), amounting to hundreds of billions of dollars in annual industry expenses.
This whitepaper addresses the persistent issue of CUI. It explores advanced sensor technologies and monitoring techniques pivotal in the early detection and continuous monitoring of corrosion under insulation, which, in turn, enables the proactive mitigation of potential hazards, consequently preserving the integrity of assets and enabling continuous and safe operations in the oil and gas industry.

Overview of Corrosion Under Insulation
CUI is external corrosion that typically occurs in insulated equipment made from carbon or low-alloy steels, such as pipelines. For this type of corrosion to take place, two conditions are necessary:
- The presence of water
- The availability of oxygen
CUI is most prevalent in processing plants and refineries that operate under fluctuating temperatures, which contributes significantly to the corrosion process. Additionally, the system’s exposure to corrosive products in contact with the pipe surface also acts as a source of corrosion.
The pipe at the core of the insulation is typically made of steel and the insulation comprises of materials or combinations of materials wrapped around the pipe to significantly reduce heat energy transfer. This effective reduction in energy losses contributes to considerable cost savings.
Hot Insulation and Cold Insulation Piping
Hot insulation prevents energy transfer from the heated fluid. The primary function of this insulation is heat conservation. It also protects the operators from hot surfaces. Commonly used hot insulating materials include mineral wool, glass wool, and calcium silicate.
On the other hand, cold insulation reduces the heat transfer from the external environment to the piping it also limits condensation. Widely used cold insulating materials include polyurethane foam or rubber foam.
Understanding the composition and function of insulation materials, both hot and cold, provides foundational knowledge of their role in the complex issue of Corrosion Under Insulation. While the primary role of insulation is to control the transfer of energy, when combined with certain environmental and operational conditions, it inadvertently creates an environment conducive to corrosion.
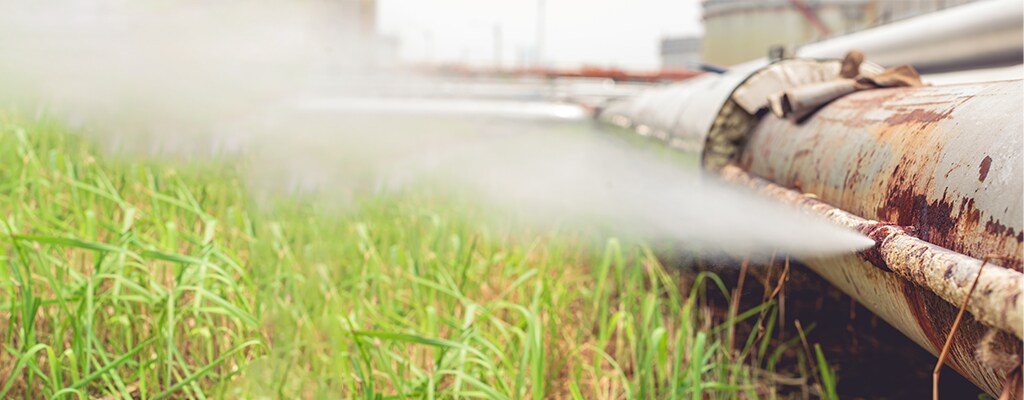
Corrosive environmental conditions affecting an insulated pipe.
Traditional CUI Detection
Various factors interplay to facilitate CUI. The interaction of these elements forms a complex network of causation that exacerbates the problem, making it challenging to detect and manage. Let’s dissect the interplay of these factors more intricately, illuminating how their complex interactions underpin the development of CUI.
Firstly, environmental conditions greatly influence the onset of CUI. Humidity, temperature fluctuations, and exposure to salt spray or industrial pollutants can increase the likelihood of water intrusion into the insulation, a prerequisite for CUI. These conditions, combined with the operating temperature of the equipment, often create the perfect conditions for corrosion.
Another critical factor is the quality and type of insulation. As previously noted, insulation materials vary greatly, and their effectiveness and susceptibility to water retention can contribute to CUI. For instance, porous insulations (hydrophilic) or closed cells (hydrophobic) will contribute to CUI creations in different ways.
Material properties of the insulated equipment, particularly its resistance to corrosion, play a pivotal role in CUI onset. Carbon and low-alloy steels are prone to rust when exposed to moisture, a process exacerbated by high temperatures.
Moreover, operational practices are a contributing factor. For instance, equipment that frequently cycles between high and low temperatures can lead to condensation within the insulation, creating an ideal environment for corrosion. Maintenance practices also significantly influence the occurrence of CUI. If insulation remains damaged or if moisture intrusion is not addressed promptly, the risk escalates.
Understanding these complex interactions is essential in formulating effective strategies to prevent and mitigate CUI. Before discussing these strategies and their efficacy, let’s dive deeper into the CUI phenomenon by examining a typical case: hot insulation pipe construction. To physically secure the insulation and protect it from external weather conditions, a metallic jacket, often referred to as “cladding”, is affixed around the insulation, held in place with metallic bands. This jacket is designed to wrap around the insulation, resulting in the creation of longitudinal or radial joints.
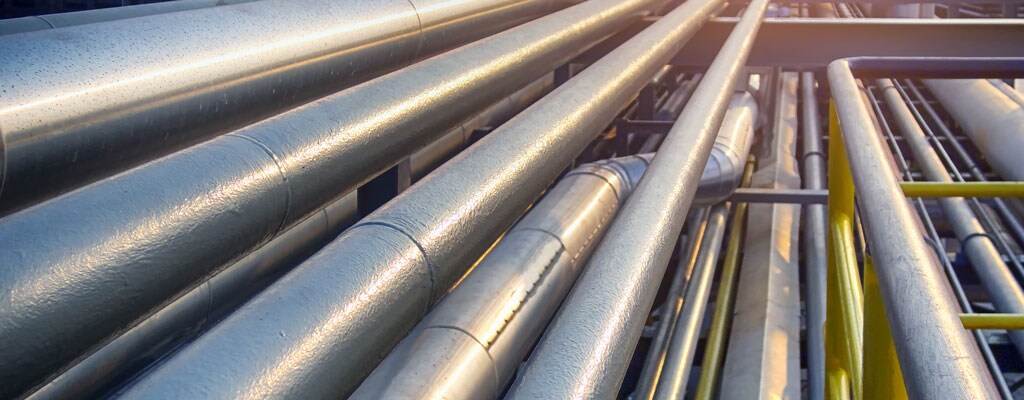
Insulated pipe with metallic cladding.
Rainfall, while a common cause, is not the sole source of water that can instigate CUI. Water can also originate from cooling towers, steam, and different processes that can result in spilling liquids. Water intrusion can occur if the cladding is damaged, seals are broken, or due to external forces such as impacts, sharp or falling objects, or individuals walking on the pipe. Once a water entry point exists, it’s not always immediately noticeable, but under rainy conditions, water intrusion becomes inevitable.
The interaction between water and insulation material can differ depending on the material’s nature. As mentioned above, If the insulation material is hydrophobic (a closed cell that does not permit water absorption), the water will flow and remain sandwiched between the insulation and the pipe. This water will not always evaporate fully over time and some pockets of water may persist in certain locations.
Conversely, if the insulation material is hydrophilic (able to absorb humidity like a sponge), the water will create thermal conduction through the sponge, and the heat momentum will go from the pipe to the cladding, creating an evaporation-condensation cycle, leading to an increase in “salt” concentration on the pipe skin as water evaporates. This “salt”, along with other natural constituents of this insulation material type, can degrade pipe protection and lead to corrosion and cracks known as chloride stress corrosion cracking (CSCC) under insulation.
Contaminants, primarily chlorides, and sulphates, are common under insulation. These may leach from the insulation materials or come from external sources. Their aqueous solutions, possessing high electrical conductivity, can facilitate the corrosion process.
Temperature also plays a pivotal role. It is generally accepted (or different sources indicate) that carbon steel operating in the temperature range of -4°C (25°F) to 149°C (300°F) is at the highest risk of CUI. Equipment that operates continuously below -4°C (25°F) tends to remain corrosion-free. Equipment operating above 149°C (300°F), exceeding the boiling point of water, experiences reduced corrosion as the carbon steel surface essentially remains dry.
Grasping the interaction between insulation materials, water ingress, contaminants, and temperature variations is critical for understanding the onset of CUI. However, this understanding isn’t complete without appreciating the potential consequences of this problem unmitigated. The ramifications extend beyond the corrosion itself, impacting not only the financial aspect of the oil and gas industry but also the health, safety, and environmental aspects.
The implications of CUI echo those of corrosion more generally. Corrosion can precipitate cracks which may eventually lead to fractures and pipeline leaks of petroleum products. This not only poses a significant threat to the surrounding environment due to potential pollution but also creates health hazards for those living near the leaks. Additionally, the risk of fires and explosions adds a layer of danger to an already critical situation.
Such damage is not only hazardous but also costly. Repairing these defects can be both financially burdensome, in terms of capital and operational expenditures (CAPEX and OPEX), and perilous for technicians performing the repairs. In the following sections, we explore strategies to prevent and mitigate CUI to control these risks effectively.
Uncovering CUI is challenging due to its hidden nature beneath insulation, often only coming to light when it’s too late. Traditional methods for detecting CUI range from straightforward to advanced techniques, all aimed at uncovering corrosion before it causes significant damage.
The most prevalent and direct approach to inspecting for CUI involves cutting portions in the insulation to allow non-destructive testing or visual inspections.
The following methods, with their respective advantages and disadvantages, are commonly employed to detect CUI:
- Visual Inspection: The simplest and first method involves removing the insulation, checking the pipe’s surface condition, and reinstating the insulation. Studies indicate that most of the time CUI is not found after insulation removal. Other challenges can be the risk associated with handling insulation in the presence of asbestos or impacting the thermal insulation if piping is in service.
- Inspection without Insulation Removal: This technique considerably reduces the cost of inspections, as it avoids the need for insulation removal and reinstatement. Non-destructive evaluation (NDE) methods are typically used for this approach.
- Non-destructive Evaluation (NDE): NDE encompasses various non-invasive inspection techniques used to evaluate material properties, components, or entire process units. Various methods, such as pulsed eddy current (PEC) and digital radiography, are used to inspect for CUI. Typically, no one method is used in isolation—several methods are used in conjunction for optimal results.
- Pulsed Eddy Current (PEC): PEC equipment operates on electro-magnetism, effectively determining the average wall thickness of the pipe through their insulation. This allows the detection and localization of CUI. PEC’s main advantage is its ability to discern general wall thinning in insulated objects without removing the insulation or any object surface preparation.
- Guided Waves (GW): alternative technology for assessing CUI over long lengths of pipe. It uses low-frequency guided ultrasonic waves that propagate along the pipe. Both internal and external corrosion can be detected but the guided wave sensor needs to be in direct contact with the pipe, therefore some insulation needs to be removed to install the sensor.
- Real-time Digital Radiography: X-rays are discharged on one side of the insulated pipe, they go through the pipe, cladding, and insulation, and a sensor will receive the X-ray on the opposite side. The rays received by the sensor are converted into real-time images and will highlight anomalies such as internal or external corrosion or defects on the pipe. This method can be applied without removing the cladding and gives real-time information.
- Thermography: used in the petrochemical industry. It gives a thermal imaging of an object and will detect wasted energy for example that can be caused by insulation defects, water ingress, gas, or liquid leaks that will impact the temperature of the insulated pipe.
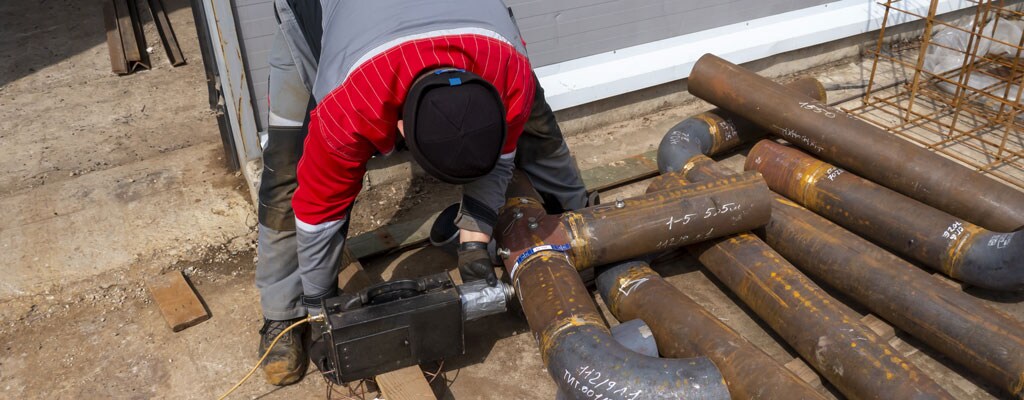
A specialist installing an X-ray device for non-destructive evaluation of welded joints.
While each of the described methods has unique strengths, they all share inherent limitations that may render them ineffective in revealing hidden CUI beneath insulation. Visual inspections, while straightforward, only expose surface conditions, potentially overlooking corrosion that lies deeper within. The removal and reinstatement of insulation during these inspections also add substantial costs and logistical challenges, such as managing asbestos. (Texas Nondestructive Testing Academy & Level III Services, n.d.)
Non-destructive evaluation (NDE) methods, which assess material properties without damaging the insulation, are limited by their respective nature. For instance, Pulsed Eddy Current (PEC) systems offer valuable insights about wall thinning but may not accurately detect localized corrosion or small pits. (Texas Nondestructive Testing Academy & Level III Services, n.d.)
Guided waves technology requires the removal of insulation at specific points, allowing the possibility of missing corrosion that occurs elsewhere. Additionally, factors like high-loss coatings or signal reflections from features such as welds and clamps can impact signal attenuation, limiting the length of pipe that can be inspected. (Chukwuemeka, et al., 2021)
Real-time digital radiography provides imaging of potential anomalies under the insulation but may lack the sensitivity to detect early-stage corrosion. Moreover, it’s only useful for material densities and may not effectively reveal corrosion in certain pipe materials. (Nanan, 2020)
Visual examinations and thermography, while effective for identifying potential CUI hazards due to damaged weatherproofing or cladding, it only offers surface level analysis and can miss corrosion hidden deeper beneath the insulation. (Fujifilm, 2022)
In essence, the primary challenge lies in these methods’ inability to provide a complete and comprehensive evaluation of hidden corrosion, especially when it’s localized or in its early stages. Each method’s limitations can leave significant areas unchecked, potentially leading to overlooked CUI that continues to evolve beneath the insulation.
Sensors for CUI Detection
Emerging from the digital transformation of the industry, the rapid proliferation of Internet of Things (IoT) devices and interconnected systems have set the stage for innovative technologies in CUI detection, particularly through wireless, battery-powered sensors. The acceleration of this technological revolution is largely due to the emergence of battery-powered wireless sensors that capitalize on advancements in low-power electronics, and the introduction of ‘battery-friendly’ wireless communication protocols such as LoRaWAN, NB-IoT, LTE M, and Bluetooth.
Various sensing principles are being evaluated, including sensors that detect moisture - both humidity and temperature - between the pipe and external cladding, or within or around insulation material, for example, optical fiber or EMGR. However, challenges exist, such as the difficulties associated with retrofitting existing infrastructures with optical fiber, or integrating “sacrificial” wires (cables) into the insulation.
These “sacrificial” wires are used in conjunction with Electro-Magnetic Guided Radar (EMGR), where the cable corrodes as a preindicator of CUI, while non-corrosive cable transmits signals to a wireless module placed outside the cladding. This incorporation allows for a seamless connection between innovative detection methods and the practical constraints of implementation, reflecting the complexities inherent in merging new technologies with established infrastructures.
TE Connectivity excels in overcoming these challenges through its unique sensor expertise, particularly its core RH capacitive sensing technology and wireless transmitters. These sensors, strategically placed on insulated pipes, allow for effective mapping of entire infrastructures. They can detect water ingress and, through smart analytics, simplify the task of pinpointing areas that require further CUI investigation using non-destructive evaluation (NDE) methods. More details on how this technology is applied in real-world settings are discussed in the case study section.
Collaborative efforts in the industry offer avenues for enhanced real-time monitoring. However, the efficacy of these solutions is substantially amplified when paired with TE Connectivity’s advanced sensor technologies.
The traditional approach often necessitates costly and resource-intensive inspections. However, TE Connectivity’s sensors aim to make this process more efficient and less resource-intensive, saving both time and costs. More than 90% of visual inspections, conducted after removing cladding, result in no corrosion found. Targeted inspections facilitated by our advanced sensor technology can thus lead to significant cost savings.
Different companies may have their own risk-based inspection strategies. Critical assets will likely continue to use scheduled maintenance and NDE methods, but less critical assets could reduce maintenance costs substantially if equipped with
TE Connectivity’s wireless remote sensors.
The goal remains to design and deploy a robust, precise, cost-effective, and long-lasting sensor capable of monitoring all insulated pipes and surfaces in refineries. TE Connectivity’s sensors, which already meet these criteria, are also fully ATEX FCE certified, providing safe operation in potentially hazardous environments.
Advancements in Sensor Technology and Their Benefits
Utilizing technologies such as LoRaWAN allows the retrieval of sensor data from distances ranging from a few meters to several kilometers. Working in tandem with gateways, advanced analytics, CUI-centric management strategies, and specialized corrosion expertise, operators and maintenance companies can detect corrosion proactively. This enables swift and targeted interventions to repair areas where corrosion occurs, saving time and reducing costs while enabling the safety and longevity of infrastructure.
The integration of such systems offers profound benefits in the proactive management of Corrosion Under Insulation. In recent years, numerous simulations and laboratory experiments involving humidity sensors have been conducted. These have yielded promising results, demonstrating that humidity and temperature measurements could indeed be effective in detecting CUI before it occurs. At TE Connectivity, we pride ourselves on our expertise in sensor technology, which has been key to these advancements. However, advancements like these don’t just stay in the lab; they find their way into practical applications through strong strategic partnerships, as we will now explore further.
KAEFER Case Study
Recognizing the Industry’s Grave Concerns
In recent years, KAEFER Group, a leader in integrated industrial services solutions, has interviewed a wide range of oil and gas companies worldwide. One commonality emerged: all cited Corrosion Under Insulation (CUI) as a top priority. The concern was not just technical but had far-reaching implications, such as the one’s addressed earlier in this paper. It was against this backdrop that our collaboration with KAEFER took shape, poised to address these urgent needs.
Comprehensive Solutions Through KIT®
Blu Empowered by KAEFER introduced KIT® (KAEFER Integrity Technology) as a holistic end-to-end service for CUI management. KIT showcases KAEFER’s expertise in effectively managing CUI projects of varying scales. From the intricate optimization of sensor placement and installation to system configuration, KIT stands as a complete package. But what amplifies its capability is TE Connectivity’s sensor technology.
The synergy between KAEFER’s integrated services and TE’s advanced sensing solutions forms the bedrock of this innovative partnership. TE’s wireless sensor technology, embedded with features such as long battery life and the ability to withstand harsh environments, represents a significant stride forward in CUI detection. Certified to meet the highest safety standards, these wireless sensors enable communication over vast distances using advanced protocols like LoRaWAN™ and are equipped with Bluetooth® Low Energy for versatile remote configuration.
Furthermore, the incorporation of customizable measurement times and intelligent threshold event management exemplifies the forward-thinking approach of this partnership, enhancing the reliability and accuracy of data while optimizing battery life. With sensors capable of autonomous adaptation in their data measurement and transmission based on configured thresholds, and automatic notifications for battery management, the collaboration is set to deliver great efficiency.
The sensing elements in such technology are meticulously designed, often leveraging long-proven MEMS humidity die & ASIC technologies, which have been extensively utilized across various industries including automotive, off road, and truck sectors. Significantly, this cross-industrial application underscores the potential for high volume scaling into sectors such as oil & gas, enabling the delivery of quality levels that are requisite in industries like automotive, and serving as the backbone for effective data acquisition and real-time monitoring.
Technical Sophistication in KIT®
KIT offers a fully digitalized CUI monitoring scheme. While it’s true that identified problem areas still require traditional inspections, there is potential to autonomize field activities, reducing human intervention and thereby mitigating risks. Moreover, the system is in ongoing development to include various features such as an advisory service, and even robotic, autonomous installation possibilities—powered by TE’s battery-operated, wireless sensors.
In terms of data visualization, KIT offers options ranging from modern dashboards to digital twin representations. These are further enriched by sophisticated analytics that assist in predicting corrosion under insulation as well as recommending maintenance actions.
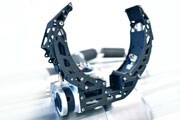
Monkeybot for robotic sensor installation
The integration of TE Connectivity’s sensor technology into KIT® doesn’t merely offer technological sophistication; it delivers tangible benefits. Case studies have demonstrated significant cost savings in maintenance and improvements in plant integrity. All these ultimately culminate in increased customer value, something both KAEFER and TE Connectivity strive to achieve.
Conclusion
In grappling with the pervasive challenge of corrosion under insulation, a dilemma that has significant ramifications on operational efficiency, environmental safety, and community well-being, the role of advanced technology cannot be overstated. This whitepaper has illustrated the vast impacts of corrosion on the oil and gas sector, affecting not just the financial bottom line—capital and operational expenditures (CAPEX and OPEX)—but also health, safety, and environmental factors (HSE).
Our collaboration with KAEFER serves as a backdrop, acknowledging the industry’s urgent needs for robust CUI management solutions. KIT® by KAEFER, which integrates TE Connectivity’s innovative sensor technology, offers a holistic End-to-End service for CUI management. This collaborative effort exemplifies an interdisciplinary approach to problem-solving, uniting diverse expertise in an ecosystem committed to tackling the complex challenges of CUI detection and management. The large-scale deployment of our wireless, battery-powered sensors goes beyond mere technological achievement; it signifies a transformative impact on the industry. The potential to reduce both scheduled maintenance and unnecessary visual inspections amplifies safety and offers substantial cost savings.
The digitalization of assets, including the development of ‘digital twins,’ allows us to take a leap forward in precision and predictability. Our sensors, backed by robust analytics tools, align well with existing systems and standards, signifying our commitment to leading advancements in CUI detection and prevention. It showcases our dedication to the continuous evolution of sensor technology and to the industry partnerships that make these advancements possible.
Looking ahead, TE Connectivity’s focus remains clear: to pioneer safer and more sustainable solutions by leveraging state-of-the-art technology. Visualization tools powered by our wireless intelligent sensors offer a comprehensive view into asset health, allowing for an insightful transition from generalized, risk based maintenance to a more focused, data-driven approach.

TE Connectivity’s wireless sensors have been deployed and are currently used in condition monitoring applications that enable predictive maintenance of rotating assets and oil & gas wellheads.
A comprehensive smart platform is available, featuring single and triaxial piezoelectric vibration sensors with a frequency range up to 15KHz (FFT and signal processing integrated), temperature sensors that can be clamped on pipes and are capable of withstanding up to 260°C external pipe temperature, and pressure sensors that can measure absolute or relative pressure.
These smart sensors are fully configurable via the TE Sensor Toolbox or using your smartphone and the TE SensorConnect app available on the Apple App Store or Google Play Store. As we navigate the future, we remain confident that our leadership in CUI monitoring solutions stands at the vanguard of industry transformation, driving both efficiency and safety to new heights.
By uniting advanced technology with deep-rooted expertise and collaborative partnerships, we are not just responding to the challenges of today but shaping the solutions of tomorrow.
