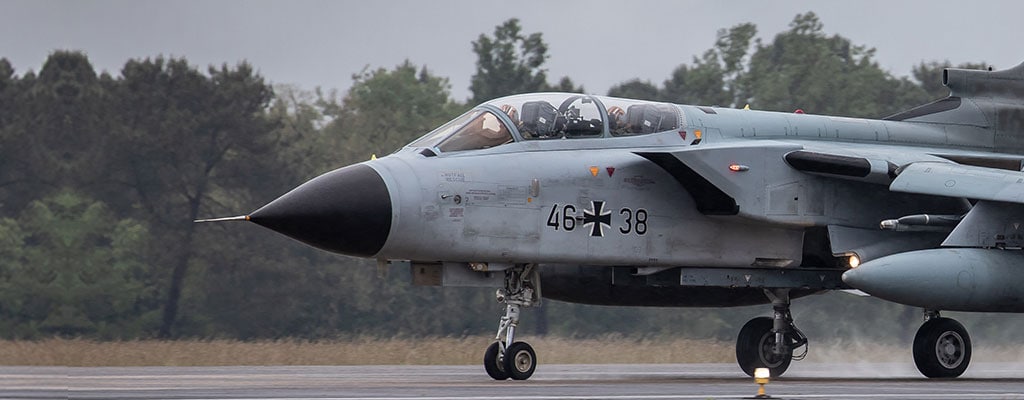
Top Tips For RFI/EMI Shielding In The Aerospace Industry
INTRODUCTION:
The Aerospace & Defense industries have always been the main drivers for RFI/EMI shielding design and products. Achieving EMC (electromagnetic compatibility) in this sector is safety critical, whereas in everyday life it can just be a frustrating nuisance. This article looks at some of the design challenges aerospace engineers face and talks about the best shielding options available.
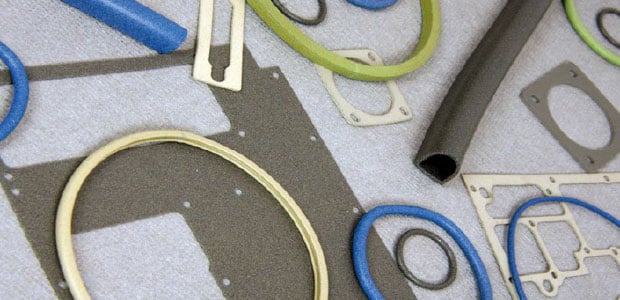
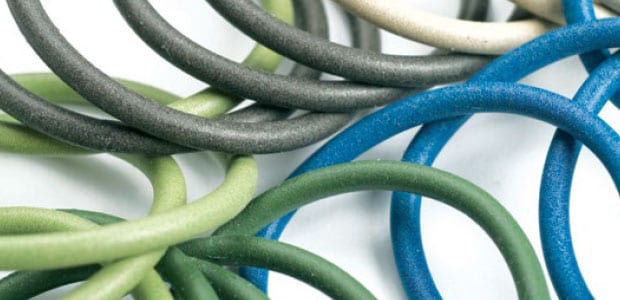
Aircraft can get struck by lightning with regular occurrence which will cause an electromagnetic pulse or EMP. EMP will have a devastating effect on electronic circuitry, so it is important that the aircraft has a path for the lightning to continue without causing damage. Space is another matter; satellites are in a very hostile electromagnetic environment with solar flares that can emit a coronal mass ejection. We are protected on earth by the magnetosphere, but satellites don’t have that advantage, so shielding is paramount to ensure the safety of the satellite and its systems.
Greater integration of electronics means electromagnetic compatibility between systems is of upmost importance to ensure they work in harmony and not interfere with each other. Aircrafts are more fly-by-wire than mechanical systems, with complex software operating computerised systems. Sensors measuring the aircraft environment, flight data etc. all need to communicate with each other, operate independently and provide back up for system failure or malfunction.
Electronics engineers are very familiar with this and will consider in their design good board layout, filtering, grounding, signal integrity etc. to try resolving EMI at its source. However, shielding of the enclosure is just as important and solves the problem of radiated emissions and susceptibility. Mating surfaces on an enclosure can look very flat and you think there is full metal to metal contact but, in a mass production process nothing can be that flat and gaps will exist. These gaps are slots and can become radiating antennas. This joint unevenness can be addressed by using an electrical gasket and adding more fixings to get good contact between the mating surfaces.
RFI/EMI shielding is a mechanical fix for an electrical problem and the enclosure design engineer should be aware of the types of gaskets available and their different attributes and ensure there is enough land area on the enclosure seams, doors etc. to fit the gasket. In Aerospace, weight and size of equipment and systems is important so miniaturisation where possible is used. This means that the shielding options available to the design engineers must also be small and offer good shielding. Electrically conductive elastomers are the best option for Aerospace as the material can be moulded, extruded or fabricated into very small components or deposited directly to hardware. Many electrically conductive fillers are available to suit shielding requirements and a fluorosilicone base meets the needs of resistance to fuel oils etc.
The aim is to always design for the worst-case scenario and consider shielding early in the design process as it is very difficult, if not impossible, to retrofit shielding to an enclosure that doesn’t have the space to incorporate a shielding gasket or component.