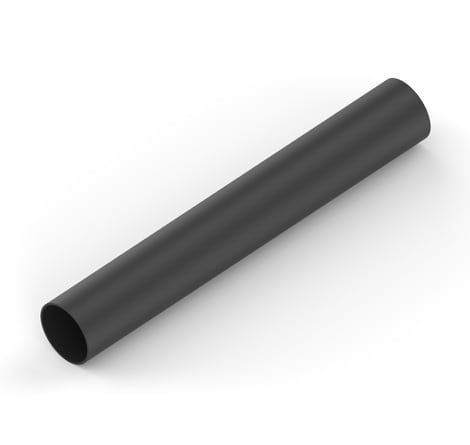
ATUM Heat Shrink Tubing : Moisture Proof Sleeving 3:1 and 4:1 Shrink Ratio
The ATUM range of heat shrink tubing has been specifically designed to provide environmental sealing and protection in a wide variety of electrical applications and is suitable for both commercial and military use. The tubing has an internal adhesive lining that when heated forms a moisture proof seal that bonds to a wide variety of materials. The high expansion ratio makes it possible to repair most damaged cables without the need to remove any connectors.
Overview
ATUM tubing is radiation-crosslinked, heat shrink, and adhesive-lined to provide environmental sealing in a wide variety of electrical applications. The product is typically used to seal connector backshells and cable breakouts and to repair damaged cable.
ATUM has an internal adhesive coating that, when heated, melts and flows to form a positive environmental seal. The coating adheres to the outer tubing and the surface below, creating an excellent barrier to moisture penetration. The adhesive bonds to a wide variety of plastics, rubbers, and metals, including PVC, polyethylene, rubber, and aluminum.
Because the tubing and adhesive are flexible, the moisture seal withstands bending of the substrate. This flexibility makes ATUM tubing ideal for cable repair. ATUM tubing is available with expansion ratios of both 3:1 and 4:1. These high expansion ratios make it possible to repair cables without removing connectors. Just a few sizes of ATUM tubing cover a wide range of substrates. ATUM is UL-recognized at 110°C, 600 V.
Features
- 3:1 and 4:1 shrink ratio.
- Operating temperature from –55°C up to +110°C.
- Minimum shrink temperature: +80°C.
- Minimum full recovery temperature: +110°C.
- Flammability Rating ASTM D2671.
- RoHS compliant.
Benefits
- Tubing environmentally seals and protects components and interconnections.
- Medium wall provides increased mechanical protection.
- The adhesive in ATUM tubing bonds to a wide variety of plastics, rubbers, and metals, including polyethylene, aluminum, steel, and copper.
- Easier, lower cost installation compared to dip-coat processes – simply slide over substrate and shrink using hot air, convection or infrared equipment.
- Reduced production times tubes can be bent or formed on the pipe.
Applications
- Sealing Halogenated and protection of connector backshells.
- Breakouts and connector-to-cable transitions.
- High shrink ratio allows for repair of damaged cable jackets without removing connectors.