Guidance for properly handing PCB relays
Incorrect handling and mounting of printed circuit board relays can alter the relay’s operational characteristics and result in premature relay failure. Additionally, recommended conductor widths and PC board cleaning procedures play an important part in assuring that the assembly will yield long, reliable service.
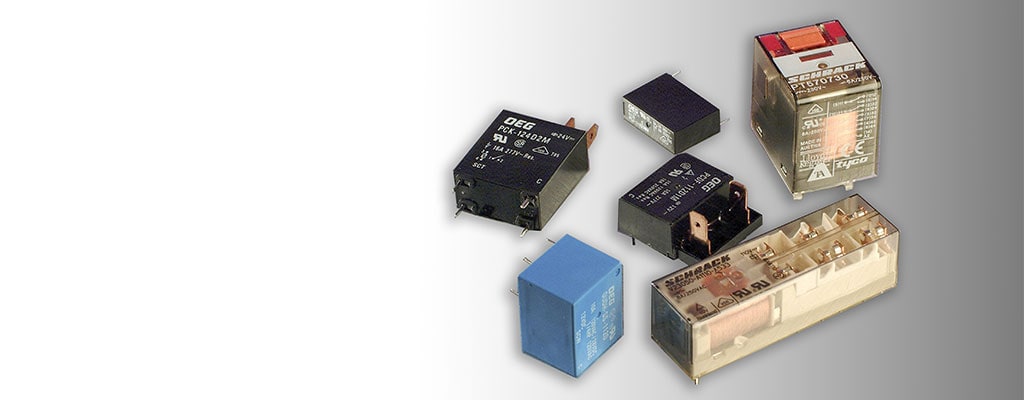
Figure 1. TE printed circuit board (PCB) relays. We manufacture miniature relays designed for switching signals as well as power relays capable of switching up to 30 amps.
PC Board Design and Relay Mounting:
- Avoid handling relay by the armature, contacts or terminals. This will prevent contamination and altering of contact-arm adjustments.
- Relays should be located away from semiconductors and other signal devices. This will reduce the effects of electromagnetic interference. Also, signal traces should be located away from relay traces.
- Relays controlled by solid state devices may require coil suppression. For more information refer to Application Note 13C3264, “Coil Suppression Can Reduce Relay Life.”
- Position relays as close as possible to the connectors. This keeps PC board heat rise to a minimum.
- UL/CSA spacings as required by the end-use application should be observed on PC board layout.
- Refer to data sheets for suggested PC board layout and recommended hole diameter.
Conductor Thickness:
The printed wiring must be at least as wide as that listed in Graph 1. Current through too small a trace will generate excessive heat, exceeding temperature ratings.
Graph 1. PC Board Temperature Rise Above Ambient (°C) as a Function of Conductor Width and Load Current
* For the width of 1 oz/ft2 (1.35 mils) copper, width = 2 X (width of 2 oz/ft2 ). If a double-sided PC board with plated-through holes is to be used, one-half of the required 1 oz/ft2 or 2 oz/ft2 copper width may be located on each side of the board.
Wave Smoldering:
- A non-corrosive flux is recommended.
- Preheat the PC board as recommended by flux vendor. This not only improves solderability but also allows the relay to stabilize.
- Do not allow solder flux to infiltrate relay components.
- Wave soldering exposure time should be kept to a minimum. Do not solder to flow on top of the PC board.
- Air cool the PC board before cleaning. This allows the relay temperature to stabilize.
Cleaning:
Open and Dust Cover Relays
- Use only clean distillate spray to remove flux; not to exceed two minutes. Never immersion clean open or dust covered relays.
- Avoid aqueous solvents. Water may be trapped between coil windings, resulting in wire corrosion.
- Use only those solvents listed in Table 1 (or equivalents) as cleaning agents. Many cleaning solvents will cause the coil tape adhesive to loosen. Relays without coil tape may be cleaned with any solvent listed, except aqueous.
- Any solvent used to clean the PC board should itself be continuously distilled. Otherwise, the spray may distribute flux, oil or dissolved acids throughout the relay. This leads to contact problems and corrosion.
Plastic Sealed Relays
- Spray cleaning or immersion cleaning may be used to remove flux. Cleaning time should be limited to two minutes.
- Avoid thermal shock during the cleaning process. Excessive thermal or mechanical shock may damage the seal integrity.
- Use only those solvents listed in Table 1 (or equivalents) as cleaning agents.
- After an aqueous cleaning, use a clean water rinse to remove all cleaning agents.
- To insure maximum relay life on tape and tab enclosures, vent the relay after board cleaning and before the relay is put into service.
Table 1: Solvent Compatibility
Guidance for properly handing PCB relays
Incorrect handling and mounting of printed circuit board relays can alter the relay’s operational characteristics and result in premature relay failure. Additionally, recommended conductor widths and PC board cleaning procedures play an important part in assuring that the assembly will yield long, reliable service.
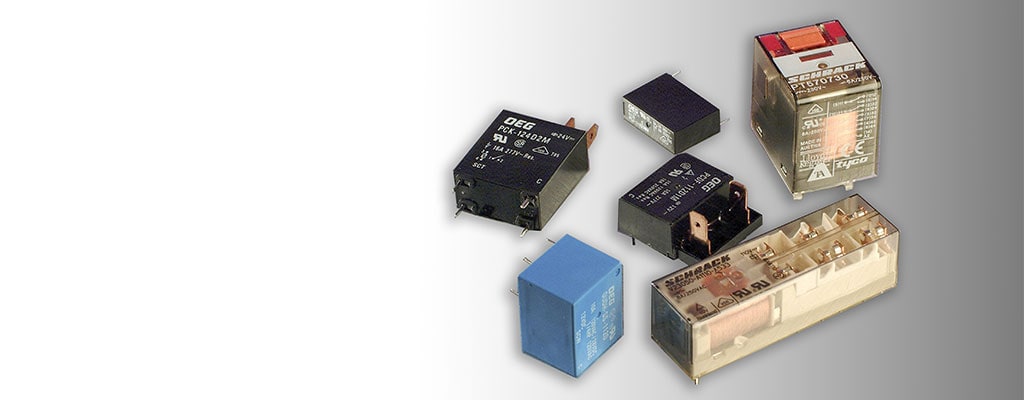
Figure 1. TE printed circuit board (PCB) relays. We manufacture miniature relays designed for switching signals as well as power relays capable of switching up to 30 amps.
PC Board Design and Relay Mounting:
- Avoid handling relay by the armature, contacts or terminals. This will prevent contamination and altering of contact-arm adjustments.
- Relays should be located away from semiconductors and other signal devices. This will reduce the effects of electromagnetic interference. Also, signal traces should be located away from relay traces.
- Relays controlled by solid state devices may require coil suppression. For more information refer to Application Note 13C3264, “Coil Suppression Can Reduce Relay Life.”
- Position relays as close as possible to the connectors. This keeps PC board heat rise to a minimum.
- UL/CSA spacings as required by the end-use application should be observed on PC board layout.
- Refer to data sheets for suggested PC board layout and recommended hole diameter.
Conductor Thickness:
The printed wiring must be at least as wide as that listed in Graph 1. Current through too small a trace will generate excessive heat, exceeding temperature ratings.
Graph 1. PC Board Temperature Rise Above Ambient (°C) as a Function of Conductor Width and Load Current
* For the width of 1 oz/ft2 (1.35 mils) copper, width = 2 X (width of 2 oz/ft2 ). If a double-sided PC board with plated-through holes is to be used, one-half of the required 1 oz/ft2 or 2 oz/ft2 copper width may be located on each side of the board.
Wave Smoldering:
- A non-corrosive flux is recommended.
- Preheat the PC board as recommended by flux vendor. This not only improves solderability but also allows the relay to stabilize.
- Do not allow solder flux to infiltrate relay components.
- Wave soldering exposure time should be kept to a minimum. Do not solder to flow on top of the PC board.
- Air cool the PC board before cleaning. This allows the relay temperature to stabilize.
Cleaning:
Open and Dust Cover Relays
- Use only clean distillate spray to remove flux; not to exceed two minutes. Never immersion clean open or dust covered relays.
- Avoid aqueous solvents. Water may be trapped between coil windings, resulting in wire corrosion.
- Use only those solvents listed in Table 1 (or equivalents) as cleaning agents. Many cleaning solvents will cause the coil tape adhesive to loosen. Relays without coil tape may be cleaned with any solvent listed, except aqueous.
- Any solvent used to clean the PC board should itself be continuously distilled. Otherwise, the spray may distribute flux, oil or dissolved acids throughout the relay. This leads to contact problems and corrosion.
Plastic Sealed Relays
- Spray cleaning or immersion cleaning may be used to remove flux. Cleaning time should be limited to two minutes.
- Avoid thermal shock during the cleaning process. Excessive thermal or mechanical shock may damage the seal integrity.
- Use only those solvents listed in Table 1 (or equivalents) as cleaning agents.
- After an aqueous cleaning, use a clean water rinse to remove all cleaning agents.
- To insure maximum relay life on tape and tab enclosures, vent the relay after board cleaning and before the relay is put into service.
Table 1: Solvent Compatibility