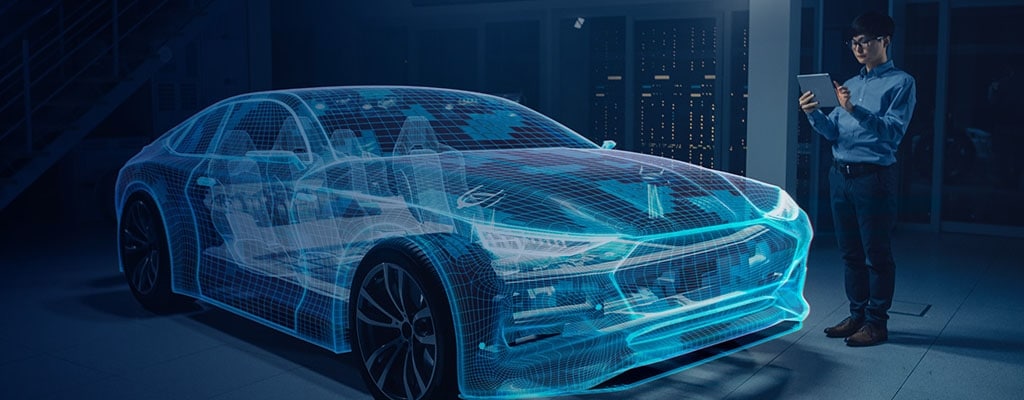
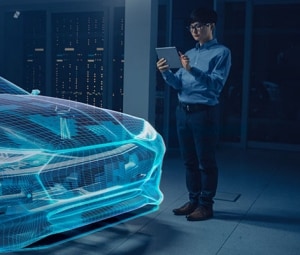
When transmitting the power from the grid to the battery in the vehicle, and converting either DC or AC grid power to the battery DC power, all components in the system need to be designed to maximize the power efficiency. This is the main challenge that engineers need to solve.
October 3, 2022
Environmental sustainability has been the main driving force for the automotive industry and policy makers across the world demanding the transition from the conventional internal combustion engine (ICE) to the battery powered vehicles. This shift also provides other crucial benefits for the electric vehicle (EV) owners – faster acceleration with instant torque, better vehicle maneuverability and handling, and less noise and vibration, which helps the EV adoption with superior (or greater) user experience. Both the environmental benefits and performance improvements are possibly achieved because of innovations in designing and developing EV technologies at scale in various areas. TE's Qiong Sun, global vice president for Automotive E-mobility, is deeply focused on engineering connectivity solutions to advance these EV innovations.
Since the battery is the heart of an EV, any innovations that can increase the energy density of the lithium-ion battery to extend the driving range and reduce the time to charge help increase consumer acceptance. Many of the battery innovations in the past two decades have focused on improving battery cell materials, optimizing battery connectivity, electronics, and software innovations that improve the overall battery performance, safety and cost.
The other major innovations for our industry are happening in areas like automation and design for manufacturing in order to ensure reliable, efficient and automated manufacturing processes. The manufacturability for the products and manufacturing efficiency are the keys for launching EV at scale so that EVS can be affordable, and help achieve the optimized performance, cost and quality to meet the requirements of consumers in every market segment.
Read – and listen to – an interview with Qiong Sun.
What factors are enabling advancements in EV architectures at scale?
As far as getting the broader advancements in launching EV architectures at scale, I believe that the manufacturability for the products and the manufacturing efficiency are the keys for the success.
You know, it is always much easier when you only need to produce a small quantity of the vehicles to achieve the performance and quality. As the production scale goes up, we need more of the innovations in areas like automation, design for manufacturing in order to ensure reliable, efficient and automated manufacturing processes. This will help facilitate improvements in both the cost and the quality of the products so that EVs can be affordable and meet the requirements of consumers in every market segment.
Also, as mentioned earlier, most of the OEMs are utilizing this EV inflection point as an opportunity to basically start over with a clean sheet of paper, and significantly reduce the complexity of their products. The clean sheet design method can be also applied to the manufacturing, supply chain, and human capital investment. I do think the ones that realize it and act fast upon it will become the true winners.
What challenges must EV OEMs must resolve to produce next-gen EVs?
The biggest challenges that I see are further improvements are still needed on how fast a driver can charge a vehicle. And as you make further breakthroughs in charging speed, and at the same time, the EV OEMs must consider how easy it is for drivers to access to the new improved charging infrastructure; how safely they can charge a vehicle; and how reliably they can charge a vehicle over time. Basically, it is all about addressing the concerns for the user experience by providing fast, safe, and reliable EV charging experience.
How are these challenges being addressed in the short term?
The industry is certainly doing a lot to address these challenges. For fast charging, as you know, we're talking about a lot of power going through the charging system, and we must figure out how to maximize the power efficiency. It is obvious that the less power lost during charging means more drive range you can gain. When transmitting the power from the grid to the battery in the vehicle, and converting either DC or AC grid power to the battery DC power, all components in the system need to be designed to maximize the power efficiency. This is the main challenge that engineers need to solve.
At the same time, extremely high heat is generated during high power charging. Therefore, every component - the charging inlet, connectors, wiring, and the battery components must be designed to manage the heat that comes with it. TE has provided solutions to help our EV customers address thermal management at the charging inlets with both passive and active cooling systems. The active system uses a water glycol based fluid from the main battery cooling system. Thermal management is very crucial to reduce the heat and prevent the battery from thermal runaway in order to ensure the safety of the EV battery.
The higher demand of fast charging also increases the wear and tear on the charging inlet terminal contact, the metal part that conducts and transmits the electricity from the charging grid to the battery. Besides being subjected to higher temperatures at each charge, the charging inlet contacts are potentially exposed to things like salt, dirt, and other abrasives, especially when using the public charging stations. The degradation of electrical terminals can lead to reduced energy transfer efficiency, which results in longer charging times.
So in a nutshell, I will summarize that the industry is addressing the power efficiency, thermal management, and key component durability those three areas right now to provide the EV customers with a fast, safe and reliable charging.
What must EV OEMs consider when developing longer term solutions?
As EV manufacturers race to develop more powerful, efficient vehicles, they must remain focused on another important consideration for EV owners. That's environmental sustainability.
Here, we're talking about a CO2 emission reduction not only from the operation of the electrical vehicles, but also from manufacturing the vehicles, transporting the vehicles, and even recycling the vehicles, and especially the batteries when they come to the end of their life. Concerns over water and energy consumption in the EV manufacturing process are putting pressure on us to think holistically about the sustainability of the EV industry. For example, how to use more clean energy, how to consume less water. So this is what I see as the longer goal for the industry to achieve.
What TE is doing to help customers address the short- and long-term challenges?
This is the part that I’m most excited about because I strongly believe that TE is well positioned to help the EV OEMs with what lies ahead. For example, our engineers have been focused on an often-overlooked piece of the EV charging equation: metallic plating technology.
As I mentioned previously, the durability of the inlet terminals is a key enabler for high efficiency and high power charging systems. TE developed a new TENDUR surface plating technology for EV charging inlets that uses an innovative surface material with the combination of silver and graphite. While silver delivers the best electrical conductivity performance, graphite particles act as a lubrication for superior abrasion resistance. TENDUR can withstand up to 50,000 charging cycles with almost no performance degradation. This is five times the 10,000-cycle lifespan for most standard charging inlets in the market today with the traditional coatings.
I also talked about the importance of environmental sustainability. This is another area of strength for TE. One example of this is GreenSilver contact surface technology for the high voltage EV connectors. By selectively applying silver to limited areas of the connection surface, GreenSilver uses less precious metal than traditional connectors while still delivering the same electrical performance with enhanced vibration and heat tolerance. This proprietary, non-galvanic dry plating process does not use any hazardous materials in the plating process. It can achieve a 35% reduction in CO2 emissions and 99% reduction in freshwater consumption during production. So I am extremely proud of what we can bring to the industry for both the short and long term goals.
How might these solutions battery connectivity improve EV performance?
Let me show you some of the battery solutions that we have for OEMs to protect and prolong the battery life. As you know, the battery is switched on and off many, many times during charging events and the normal driving operations. Over its lifespan, it is really important to protect the battery, the surrounding electrical and electronics devices to guarantee the longevity and the safety levels that are required. The high voltage contactors from TE do exactly that! Not only functioning as the switching device, but they can also detect the overload or short circuit failure modes when something goes wrong, and instantaneously cut off the power in the vehicle. I'm sure that I don't have to tell you how important it is to shut off high voltage within the vehicle when bad things happen, especially when we're talking about lithium-ion batteries. Besides the contactors, TE also offers battery solutions to connect the battery cells and the modules safely and reliably to deliver the power, data and signals.
How might OEMs change their approach to EV innovation over the next 5 years?
The automotive industry is experiencing unprecedented changes and is at a unique inflection point in its history. Currently, the OEMs are very much focused on speed-to-market and make sure they can jump start their EV transition. We are going to see a paradigm change based on how much they need to do in such a short period of time. There are three areas that they will have to change from the traditional automotive business model.
First of all, the speed of innovation deployment will get even faster. Therefore, innovations to improve the efficiency of the design development process must happen. This will result in accelerating time-to-market.
Second, due to the number of new products and technologies needed for multiple new vehicle launches, the OEMs do not have the necessary resources required and need to work with the suppliers who can provide solutions with the speed and quality. We're going to see more platforming, more modular building features.
Third, we are seeing more OEMs are willing to partner with each other and share certain technologies and innovations to increase the economies of scale. Just yesterday, we all heard that Mercedes-Benz and Rivian plan a joint venture to make electrical vans in Europe. They will not only share the technologies, but also the capital investment, and etc.
So those three things are happening at OEMs and suppliers in all regions around the world.
What does the next phase of maturity in EV charging look like?
I think a few things will happen in EV charging. First, the charging infrastructure is going to further scale up, and the charging interface standardization across the industry will happen as EV charging gets into a more mature phase. Vehicles need to be able to charge at any charging station, whether it is 800-volt or a 400-volt system. Charging stations should be able to charge any EV, no matter who the EV manufacturer is. Just like today, we don't think about which gas station I need to go to fill up my car. Inter-operation has to be the case for the EV industry.
Second, we're going to see bi-directional charging capability, not only charging from the grid to the battery, but also charging from the battery back to the grid. It is well understood that a degradation of the battery performance will happen due to any additional charging cycles. However, I do see two potential user cases. One is when electrical blackout happens, in such an emergency case, the EV batteries can serve as the power source for the household to operate lights, refrigerators, and other electrical appliances. Second, as we see the EV volume grows, almost reaching 10 million this year, the integration of EVs with the grid system can offer various cost-wise and environment-wise benefits as part of the energy ecosystem. When there are too many loads on the grid, vehicle-to-grid can help load leveling and peak shaving for the utility companies. Certainly, vehicle-to-grid benefits can be recognized much, much more efficient when EV deployment is at scale.
And last but not least, we want more and more of the energy feeding into the battery that can come from renewable sources like solar, wind, hydropower, and geothermal, all different kinds of clean energy.
Our team is extremely excited about these further advancements that we can bring to our customers to help achieve their electric future.
What differentiates TE’s approach to partnering with EV OEMs?
Growing demands for EVs also means that OEMs really don't have time to waste on bringing new models to the market. Developing EVs across all vehicle segments will call for as minimal adjustments as possible within the same electrical architecture. That's why we design our E-mobility products with a platform solutions and modular features, which also allows us for customization when it is needed. It enables us to meet each application-specific requirements while significantly speeding up the development process.
We also offer mechanical, electrical and thermal simulations to our customers. These simulation tools allow the customer to see potential failures and weak design areas for power and data connection and transmission so that preventive actions can be put in place, often before the first product is built.
For almost over two decades of being directly involved with almost all kinds of EVs and working with different customers, we understand our customer's pain points and what problems need to be addressed quickly. Through this process, we also have created a library of general market products that we can offer to the EV manufacturers, especially the emerging ones. Since these companies generally don't have the time and resources to focus on the components that TE has the most expertise on, they do rely on us to deliver them off-the-shelf products with minimal customization and improve their time-to-market.
How might EV OEM-Supplier partnerships evolve through EV innovation?
Partnerships have always been really important in the automotive industry. But for EVs, partnerships will become even more critical. The reasons I say that are, as I mentioned several times, reduced complexity and speed-to-market will be important themes as we move forward. This will drive the OEMs to select their supplier partners that they can trust to be able to manage the critical components that go across several different platforms and multiple regions around the globe. At the same time, the supplier will likely need to take on more responsibility to assure speed-to-market while maintaining best-in-class quality and flawless launch.
Therefore, the earlier that suppliers can engage with the OEMs during its development cycle, the more value that the suppliers can bring with optimized solutions that can give the best performance, cost, and quality tradeoffs.
You will also see more partnerships forming beyond the automotive industry. Automotive companies are partnering directly with the power companies, the infrastructure companies, the raw material mining and refining industry. The automotive OEMs are also offering their EV solutions to other transportation segments like marine, commercial vehicles, and two wheelers.
And at the end of the day, all suppliers and OEMs need to adapt to this new ecosystem and work together to find solutions. You can rest assured that TE is approaching this with the best technologies, products, global footprint, and most importantly, the best people needed to support our customers in this transformation, both in the short and the long term.
Is there anything else you'd like to share with our audience?
It is a very exciting time for our industry. Innovations have been playing a key role as a fuel to accelerate the EV industry, and it will continue to be the case. All players, small or large, any of us can contribute to it. And I am glad that TE Connectivity can be part of this to create a safer, sustainable, productive, and connected future.
I do want to mention to the audience of this podcast, TE is launching an open innovation initiative, partnering with Start-US. We want to invite you, whether you are a startup, small business, university research team, from anywhere around the world, to apply and scale your innovative ideas to the next generation of connectivity and sensor technologies. And together, we can further advance our mission to the electric future. I'm sure it's going to be a lot of fun.
Did you enjoy this interview? Read the source article.
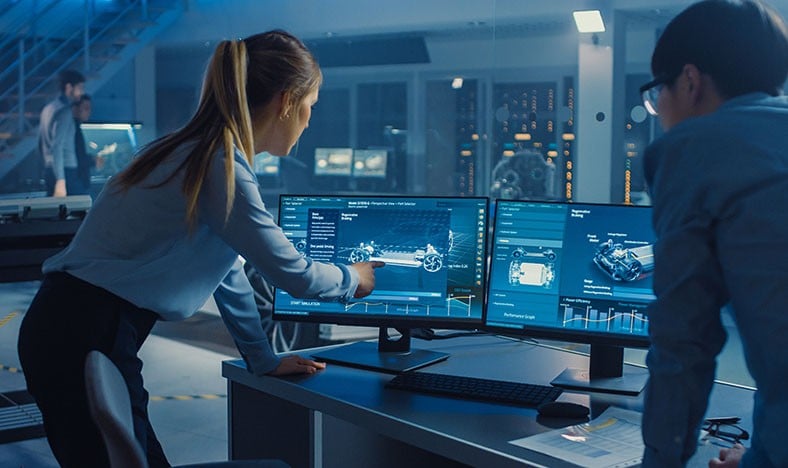
Basic EV technology has already proven itself. Now, the focus is on innovations providing more nuanced optimizations, such as reducing costs and increasing manufacturing efficiency while continuing to advance performance.
Learn the technical demands evolving the EV market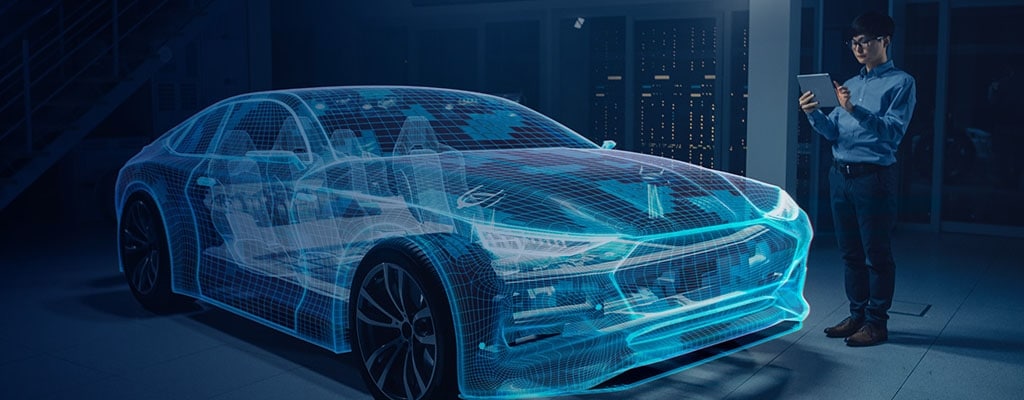
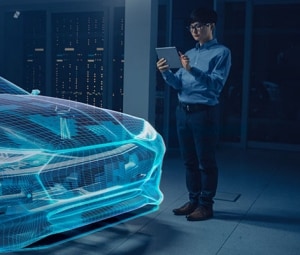
When transmitting the power from the grid to the battery in the vehicle, and converting either DC or AC grid power to the battery DC power, all components in the system need to be designed to maximize the power efficiency. This is the main challenge that engineers need to solve.
October 3, 2022
Environmental sustainability has been the main driving force for the automotive industry and policy makers across the world demanding the transition from the conventional internal combustion engine (ICE) to the battery powered vehicles. This shift also provides other crucial benefits for the electric vehicle (EV) owners – faster acceleration with instant torque, better vehicle maneuverability and handling, and less noise and vibration, which helps the EV adoption with superior (or greater) user experience. Both the environmental benefits and performance improvements are possibly achieved because of innovations in designing and developing EV technologies at scale in various areas. TE's Qiong Sun, global vice president for Automotive E-mobility, is deeply focused on engineering connectivity solutions to advance these EV innovations.
Since the battery is the heart of an EV, any innovations that can increase the energy density of the lithium-ion battery to extend the driving range and reduce the time to charge help increase consumer acceptance. Many of the battery innovations in the past two decades have focused on improving battery cell materials, optimizing battery connectivity, electronics, and software innovations that improve the overall battery performance, safety and cost.
The other major innovations for our industry are happening in areas like automation and design for manufacturing in order to ensure reliable, efficient and automated manufacturing processes. The manufacturability for the products and manufacturing efficiency are the keys for launching EV at scale so that EVS can be affordable, and help achieve the optimized performance, cost and quality to meet the requirements of consumers in every market segment.
Read – and listen to – an interview with Qiong Sun.
What factors are enabling advancements in EV architectures at scale?
As far as getting the broader advancements in launching EV architectures at scale, I believe that the manufacturability for the products and the manufacturing efficiency are the keys for the success.
You know, it is always much easier when you only need to produce a small quantity of the vehicles to achieve the performance and quality. As the production scale goes up, we need more of the innovations in areas like automation, design for manufacturing in order to ensure reliable, efficient and automated manufacturing processes. This will help facilitate improvements in both the cost and the quality of the products so that EVs can be affordable and meet the requirements of consumers in every market segment.
Also, as mentioned earlier, most of the OEMs are utilizing this EV inflection point as an opportunity to basically start over with a clean sheet of paper, and significantly reduce the complexity of their products. The clean sheet design method can be also applied to the manufacturing, supply chain, and human capital investment. I do think the ones that realize it and act fast upon it will become the true winners.
What challenges must EV OEMs must resolve to produce next-gen EVs?
The biggest challenges that I see are further improvements are still needed on how fast a driver can charge a vehicle. And as you make further breakthroughs in charging speed, and at the same time, the EV OEMs must consider how easy it is for drivers to access to the new improved charging infrastructure; how safely they can charge a vehicle; and how reliably they can charge a vehicle over time. Basically, it is all about addressing the concerns for the user experience by providing fast, safe, and reliable EV charging experience.
How are these challenges being addressed in the short term?
The industry is certainly doing a lot to address these challenges. For fast charging, as you know, we're talking about a lot of power going through the charging system, and we must figure out how to maximize the power efficiency. It is obvious that the less power lost during charging means more drive range you can gain. When transmitting the power from the grid to the battery in the vehicle, and converting either DC or AC grid power to the battery DC power, all components in the system need to be designed to maximize the power efficiency. This is the main challenge that engineers need to solve.
At the same time, extremely high heat is generated during high power charging. Therefore, every component - the charging inlet, connectors, wiring, and the battery components must be designed to manage the heat that comes with it. TE has provided solutions to help our EV customers address thermal management at the charging inlets with both passive and active cooling systems. The active system uses a water glycol based fluid from the main battery cooling system. Thermal management is very crucial to reduce the heat and prevent the battery from thermal runaway in order to ensure the safety of the EV battery.
The higher demand of fast charging also increases the wear and tear on the charging inlet terminal contact, the metal part that conducts and transmits the electricity from the charging grid to the battery. Besides being subjected to higher temperatures at each charge, the charging inlet contacts are potentially exposed to things like salt, dirt, and other abrasives, especially when using the public charging stations. The degradation of electrical terminals can lead to reduced energy transfer efficiency, which results in longer charging times.
So in a nutshell, I will summarize that the industry is addressing the power efficiency, thermal management, and key component durability those three areas right now to provide the EV customers with a fast, safe and reliable charging.
What must EV OEMs consider when developing longer term solutions?
As EV manufacturers race to develop more powerful, efficient vehicles, they must remain focused on another important consideration for EV owners. That's environmental sustainability.
Here, we're talking about a CO2 emission reduction not only from the operation of the electrical vehicles, but also from manufacturing the vehicles, transporting the vehicles, and even recycling the vehicles, and especially the batteries when they come to the end of their life. Concerns over water and energy consumption in the EV manufacturing process are putting pressure on us to think holistically about the sustainability of the EV industry. For example, how to use more clean energy, how to consume less water. So this is what I see as the longer goal for the industry to achieve.
What TE is doing to help customers address the short- and long-term challenges?
This is the part that I’m most excited about because I strongly believe that TE is well positioned to help the EV OEMs with what lies ahead. For example, our engineers have been focused on an often-overlooked piece of the EV charging equation: metallic plating technology.
As I mentioned previously, the durability of the inlet terminals is a key enabler for high efficiency and high power charging systems. TE developed a new TENDUR surface plating technology for EV charging inlets that uses an innovative surface material with the combination of silver and graphite. While silver delivers the best electrical conductivity performance, graphite particles act as a lubrication for superior abrasion resistance. TENDUR can withstand up to 50,000 charging cycles with almost no performance degradation. This is five times the 10,000-cycle lifespan for most standard charging inlets in the market today with the traditional coatings.
I also talked about the importance of environmental sustainability. This is another area of strength for TE. One example of this is GreenSilver contact surface technology for the high voltage EV connectors. By selectively applying silver to limited areas of the connection surface, GreenSilver uses less precious metal than traditional connectors while still delivering the same electrical performance with enhanced vibration and heat tolerance. This proprietary, non-galvanic dry plating process does not use any hazardous materials in the plating process. It can achieve a 35% reduction in CO2 emissions and 99% reduction in freshwater consumption during production. So I am extremely proud of what we can bring to the industry for both the short and long term goals.
How might these solutions battery connectivity improve EV performance?
Let me show you some of the battery solutions that we have for OEMs to protect and prolong the battery life. As you know, the battery is switched on and off many, many times during charging events and the normal driving operations. Over its lifespan, it is really important to protect the battery, the surrounding electrical and electronics devices to guarantee the longevity and the safety levels that are required. The high voltage contactors from TE do exactly that! Not only functioning as the switching device, but they can also detect the overload or short circuit failure modes when something goes wrong, and instantaneously cut off the power in the vehicle. I'm sure that I don't have to tell you how important it is to shut off high voltage within the vehicle when bad things happen, especially when we're talking about lithium-ion batteries. Besides the contactors, TE also offers battery solutions to connect the battery cells and the modules safely and reliably to deliver the power, data and signals.
How might OEMs change their approach to EV innovation over the next 5 years?
The automotive industry is experiencing unprecedented changes and is at a unique inflection point in its history. Currently, the OEMs are very much focused on speed-to-market and make sure they can jump start their EV transition. We are going to see a paradigm change based on how much they need to do in such a short period of time. There are three areas that they will have to change from the traditional automotive business model.
First of all, the speed of innovation deployment will get even faster. Therefore, innovations to improve the efficiency of the design development process must happen. This will result in accelerating time-to-market.
Second, due to the number of new products and technologies needed for multiple new vehicle launches, the OEMs do not have the necessary resources required and need to work with the suppliers who can provide solutions with the speed and quality. We're going to see more platforming, more modular building features.
Third, we are seeing more OEMs are willing to partner with each other and share certain technologies and innovations to increase the economies of scale. Just yesterday, we all heard that Mercedes-Benz and Rivian plan a joint venture to make electrical vans in Europe. They will not only share the technologies, but also the capital investment, and etc.
So those three things are happening at OEMs and suppliers in all regions around the world.
What does the next phase of maturity in EV charging look like?
I think a few things will happen in EV charging. First, the charging infrastructure is going to further scale up, and the charging interface standardization across the industry will happen as EV charging gets into a more mature phase. Vehicles need to be able to charge at any charging station, whether it is 800-volt or a 400-volt system. Charging stations should be able to charge any EV, no matter who the EV manufacturer is. Just like today, we don't think about which gas station I need to go to fill up my car. Inter-operation has to be the case for the EV industry.
Second, we're going to see bi-directional charging capability, not only charging from the grid to the battery, but also charging from the battery back to the grid. It is well understood that a degradation of the battery performance will happen due to any additional charging cycles. However, I do see two potential user cases. One is when electrical blackout happens, in such an emergency case, the EV batteries can serve as the power source for the household to operate lights, refrigerators, and other electrical appliances. Second, as we see the EV volume grows, almost reaching 10 million this year, the integration of EVs with the grid system can offer various cost-wise and environment-wise benefits as part of the energy ecosystem. When there are too many loads on the grid, vehicle-to-grid can help load leveling and peak shaving for the utility companies. Certainly, vehicle-to-grid benefits can be recognized much, much more efficient when EV deployment is at scale.
And last but not least, we want more and more of the energy feeding into the battery that can come from renewable sources like solar, wind, hydropower, and geothermal, all different kinds of clean energy.
Our team is extremely excited about these further advancements that we can bring to our customers to help achieve their electric future.
What differentiates TE’s approach to partnering with EV OEMs?
Growing demands for EVs also means that OEMs really don't have time to waste on bringing new models to the market. Developing EVs across all vehicle segments will call for as minimal adjustments as possible within the same electrical architecture. That's why we design our E-mobility products with a platform solutions and modular features, which also allows us for customization when it is needed. It enables us to meet each application-specific requirements while significantly speeding up the development process.
We also offer mechanical, electrical and thermal simulations to our customers. These simulation tools allow the customer to see potential failures and weak design areas for power and data connection and transmission so that preventive actions can be put in place, often before the first product is built.
For almost over two decades of being directly involved with almost all kinds of EVs and working with different customers, we understand our customer's pain points and what problems need to be addressed quickly. Through this process, we also have created a library of general market products that we can offer to the EV manufacturers, especially the emerging ones. Since these companies generally don't have the time and resources to focus on the components that TE has the most expertise on, they do rely on us to deliver them off-the-shelf products with minimal customization and improve their time-to-market.
How might EV OEM-Supplier partnerships evolve through EV innovation?
Partnerships have always been really important in the automotive industry. But for EVs, partnerships will become even more critical. The reasons I say that are, as I mentioned several times, reduced complexity and speed-to-market will be important themes as we move forward. This will drive the OEMs to select their supplier partners that they can trust to be able to manage the critical components that go across several different platforms and multiple regions around the globe. At the same time, the supplier will likely need to take on more responsibility to assure speed-to-market while maintaining best-in-class quality and flawless launch.
Therefore, the earlier that suppliers can engage with the OEMs during its development cycle, the more value that the suppliers can bring with optimized solutions that can give the best performance, cost, and quality tradeoffs.
You will also see more partnerships forming beyond the automotive industry. Automotive companies are partnering directly with the power companies, the infrastructure companies, the raw material mining and refining industry. The automotive OEMs are also offering their EV solutions to other transportation segments like marine, commercial vehicles, and two wheelers.
And at the end of the day, all suppliers and OEMs need to adapt to this new ecosystem and work together to find solutions. You can rest assured that TE is approaching this with the best technologies, products, global footprint, and most importantly, the best people needed to support our customers in this transformation, both in the short and the long term.
Is there anything else you'd like to share with our audience?
It is a very exciting time for our industry. Innovations have been playing a key role as a fuel to accelerate the EV industry, and it will continue to be the case. All players, small or large, any of us can contribute to it. And I am glad that TE Connectivity can be part of this to create a safer, sustainable, productive, and connected future.
I do want to mention to the audience of this podcast, TE is launching an open innovation initiative, partnering with Start-US. We want to invite you, whether you are a startup, small business, university research team, from anywhere around the world, to apply and scale your innovative ideas to the next generation of connectivity and sensor technologies. And together, we can further advance our mission to the electric future. I'm sure it's going to be a lot of fun.
Did you enjoy this interview? Read the source article.
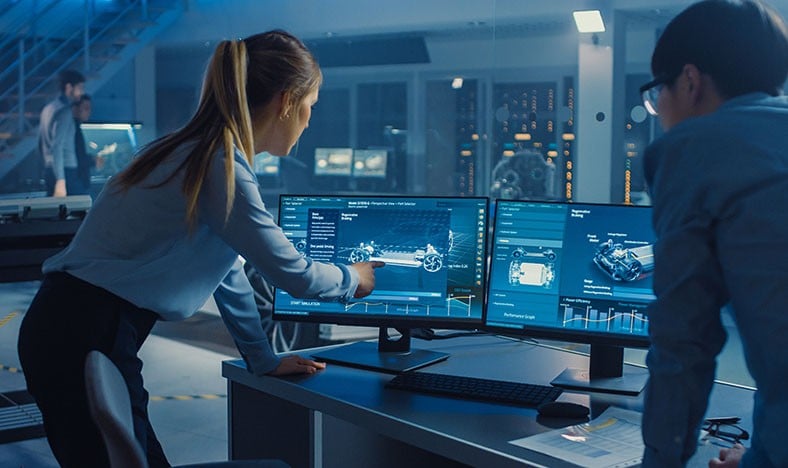
Basic EV technology has already proven itself. Now, the focus is on innovations providing more nuanced optimizations, such as reducing costs and increasing manufacturing efficiency while continuing to advance performance.
Learn the technical demands evolving the EV market