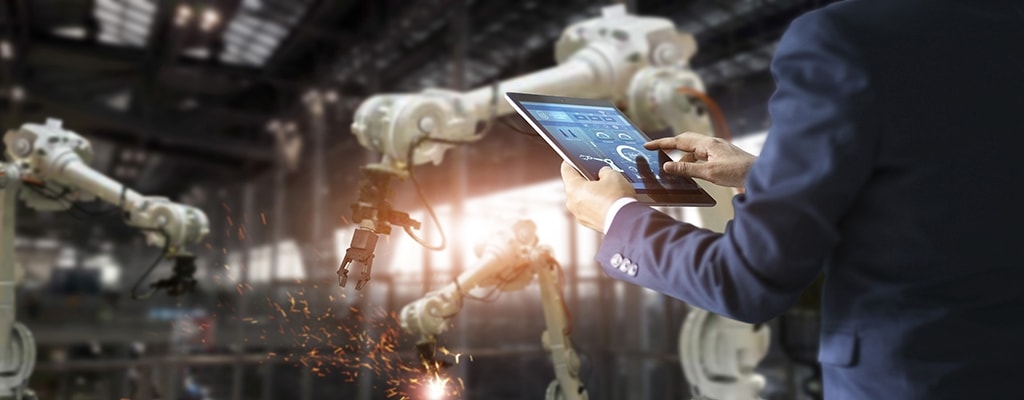
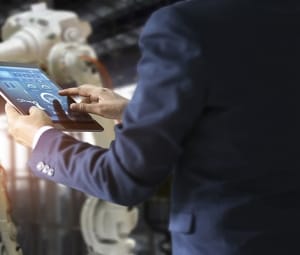
There are already cobots being used in surgeries...Everything is possible. I think the driving force will be the factories as there is a huge demand for automation.
Cobots are more compact than large-size manufacturing robots. “Think of them as a mechanical arm that can operate in very tight spaces,” says Alex Megej, vice president and chief technology officer for TE's Connected Living Solutions business unit (formerly, CTO for TE's Industrial business unit). “Typically, they can handle weights from several hundred grams up to several kilograms.” In this interview, Alex explains how cobots differ from traditional industrial manufacturing robots and how this technology is helping advance factory automation.
Cobots provide an excellent option for minor mass movement when operating near a person on a factory floor. Giant robots typically operate in isolation from factory workers for safety reasons. Cobots operate in more open or semi-protected environments. So, can these two mechanical wizards play together, or are they best kept apart? “In terms of collaboration between huge robots and small robots, this usually happens only in situations where smaller robots, or small cobots, in this case, pick and place material for further processing with larger robots,” notes Alex.
While any manufacturing operation can use cobots, Alex see cobots thriving in small and medium size business enterprises. The flexibility of cobots allows them to pick and place one day. Then, with the change of an arm tool, it can perform drilling functions on components the next day and perform assembly tasks on another. Its ability to be reprogrammed for various operations and functions makes its versatility invaluable. “Now we can use cobots to pick the finish goods, put them into a bag, as an example, close the bag, and transport it to the final destination,” explains Alex.
Read – and listen to – an interview with Alex Megej.
What are cobots? How are these different from robots typically used in industrial manufacturing?
Everybody is familiar with the large articulated robots, which you normally see in large manufacturing plants. They handle weights of hundreds and plus kilograms. Cobots on the other side, they are much more compact. Think of them as a mechanical arm which can operate in very tight spaces. And typically, they can handle the weights from several hundred grams up to several kilograms. I.e., wherever we have relatively small mass, which has to be moved next to a person working on a factory floor. This is the place where cobots thrive. So in terms of pictures, just imagine a cobot as an arm with typically with six joints working next to a human being.
What factors must be considered when designing cobots?
Generally, the large robots, they work in in a closed cage. This is done for safety reasons. The cobots typically operate in an open environment or a semi-protected environment, where sensors make sure that nobody is hurt. In terms of collaboration between huge robot and small robots, this usually happens only in the situations where smaller robots, or cobots in this case, just pick and place material for further processing with larger robots. Getting back to the introduction: where the cobots really thrive is by complementing or working alongside people. In this way, some repetitive tasks will be taken over by cobots. A typical example would be pick and place, just picking one part of equipment, moving this around to the next part. Another big advantage of a cobot is its flexibility. Ideally you would be able to program the cobot to change the tasks to be done within minutes, which is not really possible with the articulated robots.
What advantages can manufacturers gain from using cobots? How can cobots help small and medium sized businesses?
Think of it as SME, small and medium sized enterprises. This is where cobots are really spot on. And just to give you an example, TE is not really an SME, but we do have also midsize factories where initially we had either fixed lines to transport components from one working station to another, or even human beings. And this is the same as for smaller factories. The flexibility plays a huge role. It means one day a cobot can pick and place from one working space to another. Then you change what we call end of arm the tool, and the next day it can start drilling components. And on the third day it will have, let's say, a pneumatic gripper transporting subcomponents to an assembly station. An example from a TE factory where we have fully automated lines. And at one point of time you need to pick manufactured finished goods and place into a tray. In former days, it would be done either semi-automated or even manually. Now we can use cobots to pick the finished goods, put it into the bag, close the bag and transport it to the final destination. Again, flexibility, flexibility, flexibility, not only in terms of size but also processes. These cobots can [do] operations, these robots can process. And last but not least, it’s about the software flexibility. Reprogramming takes just a dozens of minutes.
How can cobots help keep workers safe, particularly in small manufacturing spaces?
This is probably one of the major issues or challenges cobot manufactures need to address. The first part, what do you do if there is shouldn't be any access to a cobot, there is no operating area. It is typically secured by mechanical means lie a cage. And then there are sensors. There are light curtains like what everybody knows from elevator doors. As soon as you put an object in hand, the robot stops immediately. Then there is a third level of security. Each joint typically has got a so-called torque sensor within the joints. As soon as the torque becomes too high, robots or cobots, stop. They stop so that nobody is injured. But this is the last level of defense. These three levels of defense: mechanical, light curtains, or external software.
How has TE integrated cobots into its manufacturing processes?
I can give you a couple of examples from different factors. In our factory in Mexico, we use it for packing. Where formerly we use humans making manufacturing step in terms of picking the finished goods, putting them into a bag, sealing the bag, and putting it into a box. This is now automated and automation doesn't mean that we remove the work from people. The automation means foremost the improvement of the quality so that we don't forget anything. Especially the repetitive work. There's nothing you would like to do for more than a couple of hours. In another factory, we move some semi-finished goods from one working station to another. We handle there pretty hot pieces from brazing to the next manufacturing step, cobots are used there to move these parts, avoiding injuries by burn. In this case, we protect the human being. Another example, in a factory in Germany, we use cobots to perform assembly of our connectors. It means there are a lot of different parts coming together and the cobot performs an automated assembly of our connectors where otherwise you would be using human beings to do this manually. So this gives you a range of flexibility where we already utilize cobots. And especially in the last example, this is where the space is extremely constrained. It literally is a fixed cage with some glass windows and different components moving around.
How is TE technology helping TE customers develop and run effective robust cobots?
In the case of cobots, TE plays two roles. On one side, we are customers utilizing cobots in our factories and optimizing the processes and making our work on the shop floor much safer. This is one piece of our work. Another piece is that we provide connectors, cables, and sensors into these cobots. The sensors are typically provided by our sister Business Unit, Sensors, TE Sensor Solutions. As an example, the torque sensor, which I mentioned before, is one of the components which is used directly in many robots. The Industrial BU provides solutions in the area of connectivity. Connectivity within a cobot arm, but also in the control box where many of our connectors are being used. As you see, every cobot manufacturer is on one side our customer, on the other side, it is also our supplier. It is sometimes very interesting to see to stay on a factory floor. The reaction is, hey, I know this cobot is using our connector, but that cobot is also manufacturing almost the same connector. So it is literally a circular economy, in the case or manufacturing at least.
What are the engineering challenges in designing cobots?
The one thing is the fact that the end of arm tools are getting more and more complex. The tools which handle components, but also the sensing elements. Especially the electrical driven grippers and the sensing elements needs different types of connectivity. It means different types of connectors providing data, power, and signals to the end of arm. This is one piece. Another piece which is very often overlooked is how do we pull cables outside of the arm? The place within the arm is very restricted. This is where I personally have seen a lot of requests from customers saying, “hey guys, I do have a wonderful sensor at the end of my arm and I've got customers interested, but all these cables break after, let’s say, a couple of weeks or at least a couple of months. So can you help us?” It is not only about the know-how in the connector area, but also the know-how in terms of how to connect them to a cable assembly, how to pull the cables along the arm.
How might single pair Ethernet impact future cobot technologies?
In order to answer this, I would like to step back a bit and look at the overall architecture, or automation architecture in a factory and the trends which we are observed there. Generally, the trend goes from one large production line to multiple decentralized cells. Every cells will perform certain tasks, allowing for flexibility to either stop material transfer or transport. If one cell breaks down, there is a possibility to repair it or bring it back online without stopping the overall system or an entire factory. It means there is a trend to decentralization. And the other trend is sensing. I.E, a lot of sensors. And those sensors have to be very flexible. Some of the sensors will use mobile technology, but mobile technology currently or wireless technology currently on a factory floor suffers from one restriction. Once we get above, once we get the number of the sensors or communicating devices buffer, certain threshold will get what you experience in a busy airport. Just drop connections, which is an absolute no go in a factory. And this is where SPE would jump in. Because it uses simplified wiring. And having the flexibility getting from wireless to wired SPE and where you have standard connectors at the end, where can connect sensors as you need them. This is where I believe that SPE will play a big role.
How is miniaturization impacting cobot design?
There are two aspects to this. On one side, miniaturization in terms of that cobots have to handle smaller and smaller products. This is a trend that the end of arm tools or grippers, they have to be much more flexible and much smaller. So this is one piece. Another piece is the space within cobots or within the control units of cobots is very, very constrained. And this once again, where TE comes in with the miniaturized connectors. We have already series of connectors or connector product lines which we can utilize within controlled units. The so-called board-to-board connectors, but also within the cobots. And those miniaturized connectors are very important in the area where you need to transfer a lot of data, especially what we call real time data. So relatively quick data packages or basically create data packages where timing between the packages or timing between the signals is very, very important. And this way we do have a pretty dedicated product line, so-called high speed, but to both connectivity solutions, which we provide with shielding and without shielding just to improve EMI. So electromagnetic interference compatibility.
Where will we see innovation happening in factory technologies?
You probably know a saying, which says, paraphrasing, that whatever your prediction is, it's probably, even highly probably wrong. Let’s focus on the trends I personally see materializing with the probability higher than 50%. The one I already mentioned is the decentralization on the factory floor. And another is that cobots will become more and more ubiquitous, not only on the factory floor, but also in other areas. You probably saw an example in medical and the hospital environments cobots which help patients during rehabilitation to make the life of physicians a bit easier. Let's say the rehabilitation, where there is a need to repeat certain movements after a knee surgery. There are already cobots being used in surgeries, but then you are going to have a robot in your kitchen helping you to make your dishes. Everything is possible. I think the driving force will be the factories as there is a huge demand for automation. Especially if you look at the megatrends. The population on this planet is getting older. We don't have enough workers to work in factories or do repetitive work, nor is this work very attractive. And here, the cobots will jump in. And once again, the main advantage of cobots is the flexibility.
Did you enjoy this interview? Read the source article.
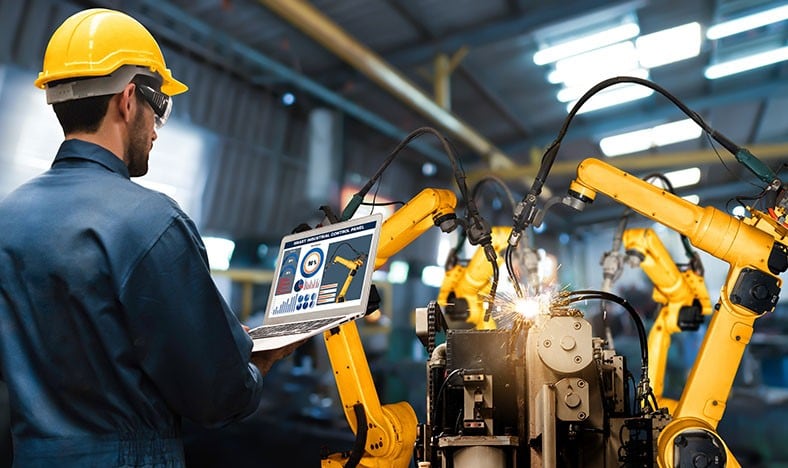
The emergence of collaborative robots, or cobots, is bringing new levels of efficiency and productivity to smaller businesses that can’t afford (and don’t need) the capabilities of industrial robots.
Learn about the key trends shaping the future of factory automation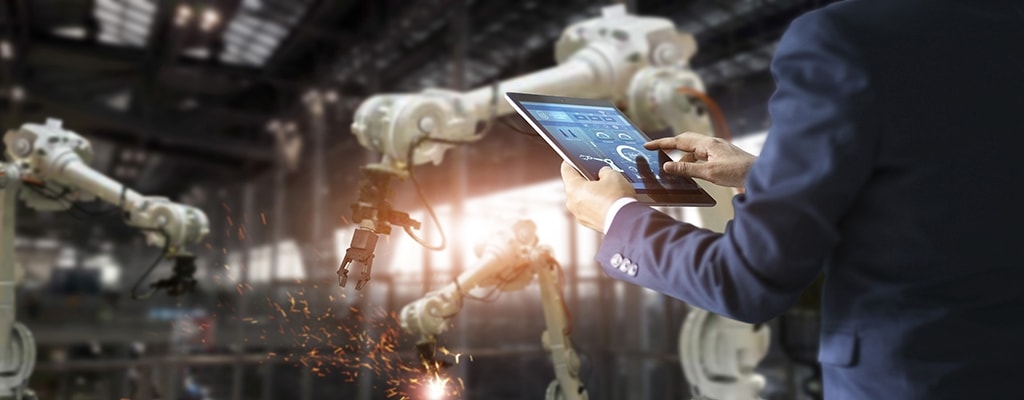
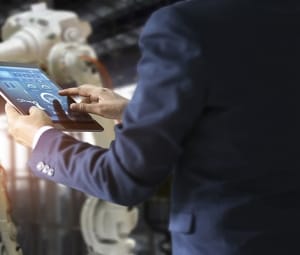
There are already cobots being used in surgeries...Everything is possible. I think the driving force will be the factories as there is a huge demand for automation.
Cobots are more compact than large-size manufacturing robots. “Think of them as a mechanical arm that can operate in very tight spaces,” says Alex Megej, vice president and chief technology officer for TE's Connected Living Solutions business unit (formerly, CTO for TE's Industrial business unit). “Typically, they can handle weights from several hundred grams up to several kilograms.” In this interview, Alex explains how cobots differ from traditional industrial manufacturing robots and how this technology is helping advance factory automation.
Cobots provide an excellent option for minor mass movement when operating near a person on a factory floor. Giant robots typically operate in isolation from factory workers for safety reasons. Cobots operate in more open or semi-protected environments. So, can these two mechanical wizards play together, or are they best kept apart? “In terms of collaboration between huge robots and small robots, this usually happens only in situations where smaller robots, or small cobots, in this case, pick and place material for further processing with larger robots,” notes Alex.
While any manufacturing operation can use cobots, Alex see cobots thriving in small and medium size business enterprises. The flexibility of cobots allows them to pick and place one day. Then, with the change of an arm tool, it can perform drilling functions on components the next day and perform assembly tasks on another. Its ability to be reprogrammed for various operations and functions makes its versatility invaluable. “Now we can use cobots to pick the finish goods, put them into a bag, as an example, close the bag, and transport it to the final destination,” explains Alex.
Read – and listen to – an interview with Alex Megej.
What are cobots? How are these different from robots typically used in industrial manufacturing?
Everybody is familiar with the large articulated robots, which you normally see in large manufacturing plants. They handle weights of hundreds and plus kilograms. Cobots on the other side, they are much more compact. Think of them as a mechanical arm which can operate in very tight spaces. And typically, they can handle the weights from several hundred grams up to several kilograms. I.e., wherever we have relatively small mass, which has to be moved next to a person working on a factory floor. This is the place where cobots thrive. So in terms of pictures, just imagine a cobot as an arm with typically with six joints working next to a human being.
What factors must be considered when designing cobots?
Generally, the large robots, they work in in a closed cage. This is done for safety reasons. The cobots typically operate in an open environment or a semi-protected environment, where sensors make sure that nobody is hurt. In terms of collaboration between huge robot and small robots, this usually happens only in the situations where smaller robots, or cobots in this case, just pick and place material for further processing with larger robots. Getting back to the introduction: where the cobots really thrive is by complementing or working alongside people. In this way, some repetitive tasks will be taken over by cobots. A typical example would be pick and place, just picking one part of equipment, moving this around to the next part. Another big advantage of a cobot is its flexibility. Ideally you would be able to program the cobot to change the tasks to be done within minutes, which is not really possible with the articulated robots.
What advantages can manufacturers gain from using cobots? How can cobots help small and medium sized businesses?
Think of it as SME, small and medium sized enterprises. This is where cobots are really spot on. And just to give you an example, TE is not really an SME, but we do have also midsize factories where initially we had either fixed lines to transport components from one working station to another, or even human beings. And this is the same as for smaller factories. The flexibility plays a huge role. It means one day a cobot can pick and place from one working space to another. Then you change what we call end of arm the tool, and the next day it can start drilling components. And on the third day it will have, let's say, a pneumatic gripper transporting subcomponents to an assembly station. An example from a TE factory where we have fully automated lines. And at one point of time you need to pick manufactured finished goods and place into a tray. In former days, it would be done either semi-automated or even manually. Now we can use cobots to pick the finished goods, put it into the bag, close the bag and transport it to the final destination. Again, flexibility, flexibility, flexibility, not only in terms of size but also processes. These cobots can [do] operations, these robots can process. And last but not least, it’s about the software flexibility. Reprogramming takes just a dozens of minutes.
How can cobots help keep workers safe, particularly in small manufacturing spaces?
This is probably one of the major issues or challenges cobot manufactures need to address. The first part, what do you do if there is shouldn't be any access to a cobot, there is no operating area. It is typically secured by mechanical means lie a cage. And then there are sensors. There are light curtains like what everybody knows from elevator doors. As soon as you put an object in hand, the robot stops immediately. Then there is a third level of security. Each joint typically has got a so-called torque sensor within the joints. As soon as the torque becomes too high, robots or cobots, stop. They stop so that nobody is injured. But this is the last level of defense. These three levels of defense: mechanical, light curtains, or external software.
How has TE integrated cobots into its manufacturing processes?
I can give you a couple of examples from different factors. In our factory in Mexico, we use it for packing. Where formerly we use humans making manufacturing step in terms of picking the finished goods, putting them into a bag, sealing the bag, and putting it into a box. This is now automated and automation doesn't mean that we remove the work from people. The automation means foremost the improvement of the quality so that we don't forget anything. Especially the repetitive work. There's nothing you would like to do for more than a couple of hours. In another factory, we move some semi-finished goods from one working station to another. We handle there pretty hot pieces from brazing to the next manufacturing step, cobots are used there to move these parts, avoiding injuries by burn. In this case, we protect the human being. Another example, in a factory in Germany, we use cobots to perform assembly of our connectors. It means there are a lot of different parts coming together and the cobot performs an automated assembly of our connectors where otherwise you would be using human beings to do this manually. So this gives you a range of flexibility where we already utilize cobots. And especially in the last example, this is where the space is extremely constrained. It literally is a fixed cage with some glass windows and different components moving around.
How is TE technology helping TE customers develop and run effective robust cobots?
In the case of cobots, TE plays two roles. On one side, we are customers utilizing cobots in our factories and optimizing the processes and making our work on the shop floor much safer. This is one piece of our work. Another piece is that we provide connectors, cables, and sensors into these cobots. The sensors are typically provided by our sister Business Unit, Sensors, TE Sensor Solutions. As an example, the torque sensor, which I mentioned before, is one of the components which is used directly in many robots. The Industrial BU provides solutions in the area of connectivity. Connectivity within a cobot arm, but also in the control box where many of our connectors are being used. As you see, every cobot manufacturer is on one side our customer, on the other side, it is also our supplier. It is sometimes very interesting to see to stay on a factory floor. The reaction is, hey, I know this cobot is using our connector, but that cobot is also manufacturing almost the same connector. So it is literally a circular economy, in the case or manufacturing at least.
What are the engineering challenges in designing cobots?
The one thing is the fact that the end of arm tools are getting more and more complex. The tools which handle components, but also the sensing elements. Especially the electrical driven grippers and the sensing elements needs different types of connectivity. It means different types of connectors providing data, power, and signals to the end of arm. This is one piece. Another piece which is very often overlooked is how do we pull cables outside of the arm? The place within the arm is very restricted. This is where I personally have seen a lot of requests from customers saying, “hey guys, I do have a wonderful sensor at the end of my arm and I've got customers interested, but all these cables break after, let’s say, a couple of weeks or at least a couple of months. So can you help us?” It is not only about the know-how in the connector area, but also the know-how in terms of how to connect them to a cable assembly, how to pull the cables along the arm.
How might single pair Ethernet impact future cobot technologies?
In order to answer this, I would like to step back a bit and look at the overall architecture, or automation architecture in a factory and the trends which we are observed there. Generally, the trend goes from one large production line to multiple decentralized cells. Every cells will perform certain tasks, allowing for flexibility to either stop material transfer or transport. If one cell breaks down, there is a possibility to repair it or bring it back online without stopping the overall system or an entire factory. It means there is a trend to decentralization. And the other trend is sensing. I.E, a lot of sensors. And those sensors have to be very flexible. Some of the sensors will use mobile technology, but mobile technology currently or wireless technology currently on a factory floor suffers from one restriction. Once we get above, once we get the number of the sensors or communicating devices buffer, certain threshold will get what you experience in a busy airport. Just drop connections, which is an absolute no go in a factory. And this is where SPE would jump in. Because it uses simplified wiring. And having the flexibility getting from wireless to wired SPE and where you have standard connectors at the end, where can connect sensors as you need them. This is where I believe that SPE will play a big role.
How is miniaturization impacting cobot design?
There are two aspects to this. On one side, miniaturization in terms of that cobots have to handle smaller and smaller products. This is a trend that the end of arm tools or grippers, they have to be much more flexible and much smaller. So this is one piece. Another piece is the space within cobots or within the control units of cobots is very, very constrained. And this once again, where TE comes in with the miniaturized connectors. We have already series of connectors or connector product lines which we can utilize within controlled units. The so-called board-to-board connectors, but also within the cobots. And those miniaturized connectors are very important in the area where you need to transfer a lot of data, especially what we call real time data. So relatively quick data packages or basically create data packages where timing between the packages or timing between the signals is very, very important. And this way we do have a pretty dedicated product line, so-called high speed, but to both connectivity solutions, which we provide with shielding and without shielding just to improve EMI. So electromagnetic interference compatibility.
Where will we see innovation happening in factory technologies?
You probably know a saying, which says, paraphrasing, that whatever your prediction is, it's probably, even highly probably wrong. Let’s focus on the trends I personally see materializing with the probability higher than 50%. The one I already mentioned is the decentralization on the factory floor. And another is that cobots will become more and more ubiquitous, not only on the factory floor, but also in other areas. You probably saw an example in medical and the hospital environments cobots which help patients during rehabilitation to make the life of physicians a bit easier. Let's say the rehabilitation, where there is a need to repeat certain movements after a knee surgery. There are already cobots being used in surgeries, but then you are going to have a robot in your kitchen helping you to make your dishes. Everything is possible. I think the driving force will be the factories as there is a huge demand for automation. Especially if you look at the megatrends. The population on this planet is getting older. We don't have enough workers to work in factories or do repetitive work, nor is this work very attractive. And here, the cobots will jump in. And once again, the main advantage of cobots is the flexibility.
Did you enjoy this interview? Read the source article.
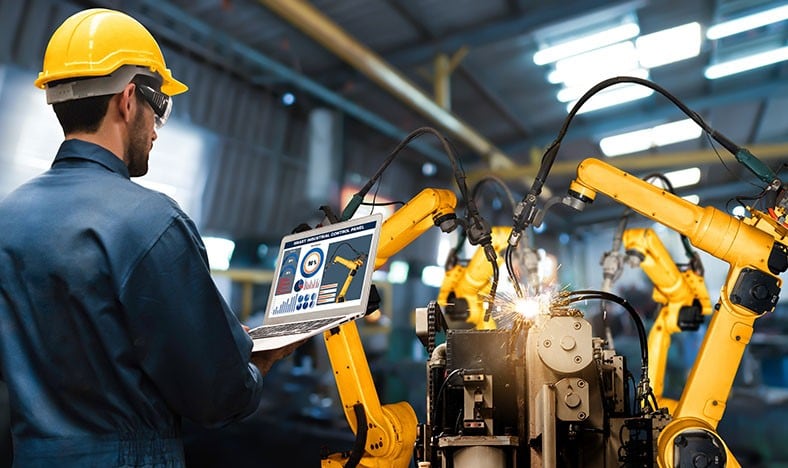
The emergence of collaborative robots, or cobots, is bringing new levels of efficiency and productivity to smaller businesses that can’t afford (and don’t need) the capabilities of industrial robots.
Learn about the key trends shaping the future of factory automation